Top 30 Mattress Filler Interview Questions and Answers [Updated 2025]
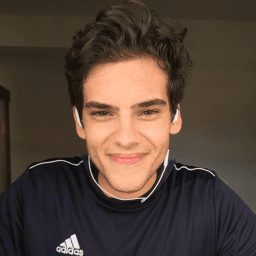
Andre Mendes
•
March 30, 2025
Are you preparing for a mattress filler job interview and want to make a great impression? Our updated guide offers a comprehensive collection of the most common interview questions for this specialized role. Discover example answers and practical tips on how to respond effectively, helping you to confidently showcase your skills and expertise. Dive in and equip yourself for success in your upcoming interview!
Download Mattress Filler Interview Questions in PDF
To make your preparation even more convenient, we've compiled all these top Mattress Fillerinterview questions and answers into a handy PDF.
Click the button below to download the PDF and have easy access to these essential questions anytime, anywhere:
List of Mattress Filler Interview Questions
Behavioral Interview Questions
Can you give an example of a time you caught a mistake in your work and how you addressed it?
How to Answer
- 1
Think of a specific instance where you identified an error.
- 2
Describe the mistake clearly without placing blame.
- 3
Explain the steps you took to correct it and prevent it from happening again.
- 4
Emphasize your attention to detail and problem-solving skills.
- 5
Keep your example relevant to the Mattress Filler position.
Example Answers
In a previous role, I noticed that I had input the wrong measurements for a batch of foam. Upon realizing this, I quickly double-checked my work and informed my supervisor. We were able to recalibrate the foam dimensions before production began. As a preventive measure, I started using a checklist to verify data entry accuracy.
Describe a time you worked as part of a team to complete a time-sensitive project. What was your role?
How to Answer
- 1
Identify a specific project and your contribution to it.
- 2
Explain the timeframe and why it was time-sensitive.
- 3
Highlight your role and responsibilities clearly.
- 4
Describe any challenges faced and how the team overcame them.
- 5
Conclude with the outcome and what you learned from the experience.
Example Answers
In my previous job, we had a project to launch a new product within a month. I was the project coordinator, organizing meetings and timelines. We faced issues with suppliers, but I communicated effectively with them to expedite delivery. We launched on time and it was successful.
Good Candidates Answer Questions. Great Ones Win Offers.
Reading sample answers isn't enough. Top candidates practice speaking with confidence and clarity. Get real feedback, improve faster, and walk into your next interview ready to stand out.
Master your interview answers under pressure
Boost your confidence with real-time practice
Speak clearly and impress hiring managers
Get hired faster with focused preparation
Used by hundreds of successful candidates
Give an example of a time you had to work under pressure. How did you manage to maintain quality and efficiency?
How to Answer
- 1
Identify a specific situation where you faced pressure
- 2
Describe the actions you took to remain effective
- 3
Focus on how you prioritized tasks to maintain quality
- 4
Mention any tools or techniques you used to manage your time
- 5
Conclude with the positive outcome of your efforts
Example Answers
During a recent project, our team faced a tight deadline to deliver a mattress product. I created a detailed checklist prioritizing tasks and delegated effectively to ensure every aspect was covered. By using time blocks for focused work, we completed the project on time with zero defects.
Tell me about a time when you had to learn a new process or use new equipment quickly. How did you adapt?
How to Answer
- 1
Use the STAR method: Situation, Task, Action, Result.
- 2
Focus on a specific example relevant to manufacturing or production.
- 3
Emphasize your quick learning and adaptability.
- 4
Mention any resources or tools you used to facilitate your learning.
- 5
Conclude with the positive outcome of your adaptation.
Example Answers
In my previous role at a factory, we had new machinery installed that I had never used before. The situation required me to get up to speed quickly to meet production goals. I observed a trainer and took detailed notes on the operation. Within a week, I was able to operate the machine independently, increasing productivity by 15%.
Describe an instance when you identified an area for improvement in your work environment. What did you do about it?
How to Answer
- 1
Think of a specific time when you saw a problem at work.
- 2
Explain what the problem was and how you recognized it.
- 3
Describe the steps you took to address the issue.
- 4
Focus on the positive outcome or benefits that resulted.
- 5
Keep your answer structured with clear beginning, middle, and end.
Example Answers
In my previous job at a furniture company, I noticed our filling material for mattresses was often inconsistent. I initiated a feedback session with the production team to discuss this. We then tweaked our supplier selection criteria and trained staff on quality checks. As a result, our defect rate dropped significantly, improving overall customer satisfaction.
Can you tell us about a time you had a conflict with a coworker? How was it resolved?
How to Answer
- 1
Choose a specific conflict and describe the situation briefly.
- 2
Focus on your role and actions taken to address the conflict.
- 3
Emphasize clear communication and collaboration.
- 4
Highlight the positive outcome or what you learned.
- 5
Keep it professional and avoid personal details.
Example Answers
In a previous job, I disagreed with a coworker about the best way to organize inventory. I initiated a meeting where we both voiced our concerns, and we decided to combine our ideas to create a more efficient system. This resolution improved our workflow and strengthened our working relationship.
Describe a process improvement you implemented that increased efficiency in your past work.
How to Answer
- 1
Identify a specific process you improved.
- 2
Explain the challenges with the original process.
- 3
Detail the changes you made to improve efficiency.
- 4
Quantify the results of the improvement if possible.
- 5
Highlight how this experience prepares you for the position.
Example Answers
In my previous job, I noticed that our inventory management was slow and error-prone. I implemented a digital tracking system that automated many manual tasks. As a result, we reduced processing time by 30% and errors decreased by 50%. This experience taught me the value of technology in improving workflow, which I can apply to the Mattress Filler role.
Tell me about a time when attention to detail paid off in your work.
How to Answer
- 1
Choose a specific example that had a positive outcome.
- 2
Explain the situation briefly without jargon.
- 3
Highlight the details you focused on and why they mattered.
- 4
Describe the results of your attention to detail clearly.
- 5
Connect the experience to skills required for the Mattress Filler position.
Example Answers
In my previous job, I was tasked with overseeing the quality of mattress production. I noticed a slight variation in the stitching pattern on a batch of covers. By addressing it early, we avoided several customer complaints and returned products, saving us time and money.
Describe a mistake you made in your past job and what you learned from it.
How to Answer
- 1
Choose a specific mistake that had a clear impact.
- 2
Explain the situation and what led to the mistake.
- 3
Focus on what you learned and how you improved.
- 4
Keep it positive and show your growth.
- 5
Be honest but don't dwell on negativity.
Example Answers
In my previous job, I mismanaged a project deadline because I underestimated the time needed for certain tasks. I learned the importance of setting realistic deadlines and improving my time management skills, which helped me complete future projects more efficiently.
How do you manage stress when there are multiple deadlines to meet?
How to Answer
- 1
Prioritize tasks by urgency and importance
- 2
Break larger tasks into smaller, manageable steps
- 3
Utilize a planner or digital tools to track deadlines
- 4
Practice time management techniques like the Pomodoro Technique
- 5
Take short breaks to recharge and maintain focus
Example Answers
I prioritize my tasks by determining which are most urgent and important. I then break those into smaller steps and use a planner to keep track of deadlines.
Good Candidates Answer Questions. Great Ones Win Offers.
Reading sample answers isn't enough. Top candidates practice speaking with confidence and clarity. Get real feedback, improve faster, and walk into your next interview ready to stand out.
Master your interview answers under pressure
Boost your confidence with real-time practice
Speak clearly and impress hiring managers
Get hired faster with focused preparation
Used by hundreds of successful candidates
Technical Interview Questions
What types of materials are commonly used in mattress filling, and how do they affect comfort and durability?
How to Answer
- 1
Identify key materials like memory foam, latex, and innerspring.
- 2
Explain how each material contributes to comfort levels.
- 3
Discuss durability factors related to different fillings.
- 4
Mention any recent trends in materials or innovative fillings.
- 5
Wrap up by summarizing how these materials perform for different sleepers.
Example Answers
Common materials for mattress filling include memory foam, latex, and innerspring coils. Memory foam provides excellent contouring and pressure relief, making it comfortable for side sleepers. Latex offers a bouncier feel and greater durability, while innerspring provides a traditional feel with good support. Overall, the choice of filling affects the comfort and longevity of the mattress.
What machinery are you familiar with for filling mattresses, and how do you ensure it is used safely and effectively?
How to Answer
- 1
List specific types of machinery you have used, such as blowers or filling machines.
- 2
Explain any safety protocols you follow, like wearing protective gear.
- 3
Mention any training or certifications related to the machinery.
- 4
Provide an example of a safety issue you encountered and how you resolved it.
- 5
Emphasize the importance of regular maintenance checks on machinery.
Example Answers
I am familiar with using foam filling machines and blowers for mattress filling. I always wear protective gear and ensure the machinery is regularly inspected for safety. For example, I once noticed a broken safety guard on a machine and reported it immediately to prevent any accidents.
Good Candidates Answer Questions. Great Ones Win Offers.
Reading sample answers isn't enough. Top candidates practice speaking with confidence and clarity. Get real feedback, improve faster, and walk into your next interview ready to stand out.
Master your interview answers under pressure
Boost your confidence with real-time practice
Speak clearly and impress hiring managers
Get hired faster with focused preparation
Used by hundreds of successful candidates
Can you describe the step-by-step process of filling a mattress, from beginning to end?
How to Answer
- 1
Start with selecting the appropriate filling material based on mattress type.
- 2
Prepare the mattress cover by ensuring it is clean and intact.
- 3
Add the filling material evenly inside the mattress shell.
- 4
Adjust the filling to ensure there are no lumps and it is evenly distributed.
- 5
Close the mattress cover securely and perform a quality check.
Example Answers
First, I select the right filling, like memory foam or innerspring. Then, I check the mattress cover for cleanliness. After that, I evenly distribute the filling inside. I make sure to smooth it out to avoid lumps. Finally, I seal the cover and check for overall quality.
What safety measures do you follow when handling mattress filling materials?
How to Answer
- 1
Always wear protective gloves and a mask to avoid skin irritation and inhalation of dust.
- 2
Ensure proper ventilation in the workspace to minimize exposure to fumes and particles.
- 3
Follow proper lifting techniques to avoid injuries when handling heavy materials.
- 4
Be aware of the material safety data sheets (MSDS) for specific filling materials used.
- 5
Regularly inspect equipment for any damage that could lead to accidents.
Example Answers
I always wear gloves and a mask when handling filling materials to protect myself from irritation and dust inhalation.
What quality control measures are essential in the mattress filling process?
How to Answer
- 1
Identify key materials used in filling and their quality.
- 2
Discuss techniques for measuring fill density and consistency.
- 3
Mention the importance of inspections during production.
- 4
Highlight testing for durability and comfort after assembly.
- 5
Explain the role of feedback in continuous improvement.
Example Answers
In mattress filling, ensuring the quality of raw materials like foam and fibers is crucial. We need to measure the fill density to ensure consistency and perform inspections during various production stages to catch any issues early.
How does the distribution of filling material affect the comfort and support of a mattress?
How to Answer
- 1
Discuss different types of filling materials like memory foam, latex, and innerspring.
- 2
Explain how the distribution affects pressure relief and body alignment.
- 3
Mention the importance of even distribution for overall support.
- 4
Include how firmness levels can vary based on filling distribution.
- 5
Relate the concept to personal comfort preferences and sleep positions.
Example Answers
The distribution of filling materials like memory foam and latex impacts mattress comfort by providing pressure relief and proper body alignment. For example, even distribution helps distribute weight across the surface, reducing pressure points, which is crucial for side sleepers.
What common issues can arise during the mattress filling process, and how do you troubleshoot them?
How to Answer
- 1
Identify common filling materials and their specific issues.
- 2
Discuss how to recognize these problems early.
- 3
Provide step-by-step troubleshooting methods for each issue.
- 4
Mention preventive measures to avoid these issues in the future.
- 5
Be clear and concise in your explanation.
Example Answers
One common issue is uneven filling. I troubleshoot it by inspecting the filling process to ensure consistent distribution, and I can manually redistribute the filling if necessary. Preventatively, I make sure the filling machinery is calibrated correctly before starting.
How does humidity and temperature affect the materials used in mattress filling, and how do you compensate for these factors?
How to Answer
- 1
Explain how high humidity can lead to mold growth in natural materials.
- 2
Mention that temperature changes can affect the firmness and feel of foam.
- 3
Discuss the use of moisture-wicking fabrics to manage humidity.
- 4
Talk about the importance of product testing in different conditions.
- 5
Highlight how adjusting the blend of materials can enhance durability.
Example Answers
Humidity can cause natural fillings like wool and cotton to retain moisture, leading to mold. We use moisture-wicking covers to minimize this effect. I also ensure that we test our mattresses under various humidity levels to assess their performance.
What tools do you typically use in the mattress filling process, and how do you ensure they are maintained?
How to Answer
- 1
List specific tools you use in mattress filling, like pneumatic fillers and measuring devices.
- 2
Explain the maintenance routine for each tool, such as cleaning and regular inspections.
- 3
Mention any safety equipment used during the process to protect yourself and others.
- 4
Discuss how proper maintenance contributes to quality control and efficiency.
- 5
Provide examples of how you've addressed tool malfunctions or maintenance issues in the past.
Example Answers
In my experience, I typically use pneumatic fillers, measuring devices, and hand tools like scissors and seam rippers. I ensure they are maintained by conducting regular cleaning after each shift and performing inspections daily to check for wear and tear.
Have you ever suggested an improvement to the filling process that was implemented by your team?
How to Answer
- 1
Think of a specific improvement you suggested.
- 2
Explain the problem that the improvement addressed.
- 3
Describe how you communicated your suggestion to the team.
- 4
Mention the outcome or results after implementation.
- 5
Be honest and keep it relevant to the filling process.
Example Answers
In my previous role, I noticed that the filling process often left air pockets in the mattresses. I suggested using a vacuum system to compress the filling material more efficiently. I presented this idea during a team meeting, and after testing it, we found it improved our quality and reduced filling time by 15%.
Good Candidates Answer Questions. Great Ones Win Offers.
Reading sample answers isn't enough. Top candidates practice speaking with confidence and clarity. Get real feedback, improve faster, and walk into your next interview ready to stand out.
Master your interview answers under pressure
Boost your confidence with real-time practice
Speak clearly and impress hiring managers
Get hired faster with focused preparation
Used by hundreds of successful candidates
Situational Interview Questions
If you notice that a batch of mattress filling material is defective, what steps would you take?
How to Answer
- 1
Identify the type and extent of the defect in the filling material
- 2
Segregate the defective batch to prevent it from being used
- 3
Report the issue to the supervisor and document the findings
- 4
Follow protocol for investigating the cause of the defect
- 5
Implement corrective measures to prevent future defects
Example Answers
I would first assess the specific defects in the filling material and check how serious they are. Then, I would isolate the affected batch to ensure it doesn't get used in production and inform my supervisor about the situation right away.
Imagine a scenario where the mattress filling machine jams during production. What would you do to resolve it?
How to Answer
- 1
Stop the machine immediately to prevent further issues.
- 2
Inspect the machine for visible obstructions or damage.
- 3
Clear any blockages or debris carefully and safely.
- 4
Follow the machine’s troubleshooting manual for guidance.
- 5
Report the incident to your supervisor and document the resolution.
Example Answers
I would stop the machine immediately and inspect it for any visible blockages. After clearing any debris, I would consult the troubleshooting manual to ensure I correctly address the issue. Once resolved, I'd inform my supervisor of the incident.
Good Candidates Answer Questions. Great Ones Win Offers.
Reading sample answers isn't enough. Top candidates practice speaking with confidence and clarity. Get real feedback, improve faster, and walk into your next interview ready to stand out.
Master your interview answers under pressure
Boost your confidence with real-time practice
Speak clearly and impress hiring managers
Get hired faster with focused preparation
Used by hundreds of successful candidates
If you realize mid-way through your shift that you will run out of a key filling material, how would you handle the situation?
How to Answer
- 1
Stay calm and assess how much material is left.
- 2
Notify your supervisor immediately about the shortage.
- 3
Check if there's a backup supply or alternative material available.
- 4
Prioritize tasks that can be done with the remaining materials.
- 5
Communicate with the team to ensure everyone is aware of the situation.
Example Answers
I would first check how much filling material we have left and then notify my supervisor right away about the potential shortage. I would also look for any backup supplies or alternative materials we could use while we wait for the new stock.
You are informed of an urgent order that needs to be prioritized. How would you ensure timely completion without compromising quality?
How to Answer
- 1
Assess the urgency and requirements of the order first
- 2
Communicate clearly with your team about priorities
- 3
Allocate resources effectively to meet deadlines
- 4
Monitor progress closely to catch any delays early
- 5
Maintain quality checks throughout the process
Example Answers
I would start by assessing the details of the urgent order and communicate with my team to prioritize it. I would allocate extra resources if needed to ensure we meet the deadline while checking in regularly to maintain quality.
If you and a coworker disagreed on the best way to handle a task, how would you resolve the situation?
How to Answer
- 1
Listen to your coworker's viewpoint and understand their reasoning.
- 2
Explain your perspective clearly and provide supporting reasons.
- 3
Find common ground or agreed objectives that benefit both parties.
- 4
Suggest a compromise or a trial of both methods if feasible.
- 5
Focus on maintaining a positive working relationship throughout the discussion.
Example Answers
I would first listen to my coworker's perspective to understand their reasoning. Then, I would share my own view, highlighting the benefits of my approach. If we still disagree, I would suggest trying both methods on a small scale to see which works better.
If a customer returns a mattress due to poor filling, how would you investigate and address the complaint?
How to Answer
- 1
Listen carefully to the customer's issue and gather specific details about the problem
- 2
Ask open-ended questions to understand the customer's experience with the mattress
- 3
Examine the returned mattress to identify any visible defects or issues with the filling
- 4
Offer a resolution such as a replacement, repair, or refund based on company policy
- 5
Follow up with the customer after the resolution to ensure satisfaction and gather feedback
Example Answers
I would start by listening to the customer to understand their concerns. I'd ask questions about when they noticed the issue and what specific problems they experienced. After that, I would inspect the mattress to see if there are any visible defects. Depending on what I find, I would offer a replacement or a refund and make sure to follow up to see if they are satisfied with the solution.
You've witnessed a safety incident in the workplace. How do you handle it?
How to Answer
- 1
Stay calm and assess the situation quickly.
- 2
Ensure the safety of yourself and others first.
- 3
Report the incident to a supervisor or safety officer immediately.
- 4
Document what you witnessed in detail.
- 5
Follow up to ensure proper procedures were taken.
Example Answers
I would first check if anyone was injured and call for medical help if needed. Then, I would report the incident to my supervisor and make sure it was documented properly.
How would you train a new team member on the mattress filling process?
How to Answer
- 1
Start with a basic overview of the materials and tools needed.
- 2
Demonstrate the entire filling process step by step.
- 3
Encourage hands-on practice with supervision.
- 4
Use checklists to ensure no steps are missed.
- 5
Provide feedback and allow questions throughout the training.
Example Answers
I would begin by explaining the materials like foam and latex we use. Then, I would demonstrate how to fill a mattress from start to finish. After that, I would have the new member try it while I supervise, using a checklist to keep track of each step. This ensures they understand the process and can ask questions as needed.
The specifications for a mattress filling have changed unexpectedly. How would you adapt to this change?
How to Answer
- 1
Assess the new specifications quickly and understand the requirements.
- 2
Communicate with your team to discuss the changes and gather insights.
- 3
Evaluate current materials and processes to see what adjustments are needed.
- 4
Implement changes systematically to ensure quality control is maintained.
- 5
Monitor the results and be prepared to make further adjustments if necessary.
Example Answers
I would start by reviewing the new specifications carefully to understand what is required. Then, I would hold a meeting with my team to discuss how these changes affect our current materials and processes and get their input on the best way to adapt.
During a high volume production day, how do you ensure that all safety and quality standards are upheld?
How to Answer
- 1
Prioritize safety training before production begins to ensure all team members are aware of protocols.
- 2
Implement regular checks during production to monitor both safety and quality standards.
- 3
Encourage open communication among team members to report any safety hazards or quality issues immediately.
- 4
Utilize personal protective equipment (PPE) and ensure it is worn correctly by everyone.
- 5
Document any incidents or near misses to improve processes and reinforce safety training.
Example Answers
I ensure all employees receive safety training and refreshers before a high volume day. We conduct routine checks during production to uphold quality, and I encourage team members to communicate any concerns right away.
Good Candidates Answer Questions. Great Ones Win Offers.
Reading sample answers isn't enough. Top candidates practice speaking with confidence and clarity. Get real feedback, improve faster, and walk into your next interview ready to stand out.
Master your interview answers under pressure
Boost your confidence with real-time practice
Speak clearly and impress hiring managers
Get hired faster with focused preparation
Used by hundreds of successful candidates
Mattress Filler Position Details
Related Positions
- Cushion Filler
- Mattress Maker
- Cushion Maker
- Mold Filler
- Bed Maker
- Bottom Liner
- Door Liner
- Coverer
- Body Fitter
- Liner Installer
Similar positions you might be interested in.
Good Candidates Answer Questions. Great Ones Win Offers.
Master your interview answers under pressure
Boost your confidence with real-time practice
Speak clearly and impress hiring managers
Get hired faster with focused preparation
Used by hundreds of successful candidates
Good Candidates Answer Questions. Great Ones Win Offers.
Master your interview answers under pressure
Boost your confidence with real-time practice
Speak clearly and impress hiring managers
Get hired faster with focused preparation
Used by hundreds of successful candidates