Top 30 Body Fitter Interview Questions and Answers [Updated 2025]
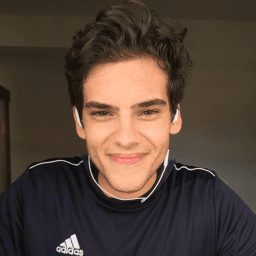
Andre Mendes
•
March 30, 2025
Preparing for a Body Fitter interview can be daunting, but we're here to help you succeed. In this post, you'll find the most common interview questions tailored for the Body Fitter role, complete with example answers and insightful tips to help you respond with confidence. Whether you're a seasoned professional or just starting out, this guide will equip you with the tools you need to impress your potential employer.
Download Body Fitter Interview Questions in PDF
To make your preparation even more convenient, we've compiled all these top Body Fitterinterview questions and answers into a handy PDF.
Click the button below to download the PDF and have easy access to these essential questions anytime, anywhere:
List of Body Fitter Interview Questions
Behavioral Interview Questions
Describe a time when you worked with a team to complete a complicated body fitting project. What role did you play, and what was the outcome?
How to Answer
- 1
Think about a specific project where teamwork was crucial.
- 2
Clearly define your role, highlighting your contributions.
- 3
Mention any challenges faced and how you overcame them as a team.
- 4
Include the final outcome and its impact on the project.
- 5
Use metrics or feedback if possible to demonstrate success.
Example Answers
In my last position, I was part of a team working on a custom fitting project for a sports apparel line. I was the lead fitter, and I coordinated with designers to ensure accurate measurements. We faced challenges with tight deadlines, but by working overtime and communicating effectively, we completed the project on time and received positive client feedback regarding the fit and comfort of the apparel.
Give an example of a situation where your attention to detail was crucial in a body fitting project. How did it impact the final result?
How to Answer
- 1
Choose a specific project you worked on.
- 2
Describe the details you focused on and why they were important.
- 3
Explain how your attention to detail improved the outcome.
- 4
Mention any feedback received from clients or colleagues.
- 5
Conclude with the positive result or success of the project.
Example Answers
In a recent project, I was tasked with fitting a client's custom workout gear. I noticed the initial measurements were slightly off, which could have affected the fit. I double-checked the measurements and adjusted the patterns accordingly. As a result, the final product was a perfect fit, and the client was thrilled, leading to a repeat order and positive referrals.
Don't Just Read Body Fitter Questions - Practice Answering Them!
Reading helps, but actual practice is what gets you hired. Our AI feedback system helps you improve your Body Fitter interview answers in real-time.
Personalized feedback
Unlimited practice
Used by hundreds of successful candidates
Tell me about a time when you had to troubleshoot an issue during a fitting task. How did you resolve it?
How to Answer
- 1
Identify a specific fitting issue you faced.
- 2
Briefly explain the context and what went wrong.
- 3
Describe the steps you took to troubleshoot the problem.
- 4
Highlight any tools or methods you used to resolve the issue.
- 5
Conclude with the positive outcome or what you learned from the experience.
Example Answers
During a fitting for a client, I noticed that the material was not sitting properly on their body. I quickly assessed the fit and realized it was due to an incorrect measurement. I retrieved the measuring tape and re-measured the key areas, then adjusted the design to enhance the fit, which ultimately satisfied the client.
Describe a situation where safety measures were important during a body fitting project. What steps did you take to ensure safety?
How to Answer
- 1
Identify specific safety measures relevant to body fitting.
- 2
Use a clear example from past experience.
- 3
Outline the steps taken to assess risks.
- 4
Explain how you communicated safety to the team.
- 5
Highlight any training or protocols followed.
Example Answers
In a recent body fitting project, we prioritized safety by conducting a risk assessment before starting. I led a team meeting to clarify the importance of using safety gear, ensuring everyone wore appropriate personal protective equipment.
Discuss a time when you improved the efficiency of a fitting process. What changes did you implement?
How to Answer
- 1
Identify a specific fitting process you improved
- 2
Explain the challenges or inefficiencies faced
- 3
Describe the changes you implemented and why
- 4
Highlight the outcome and benefits of your changes
- 5
Use metrics or feedback to quantify the improvement
Example Answers
In my previous role, the fitting process used to take over an hour due to manual measurements. I implemented a standardized measuring system and trained the team. This reduced fitting time by 30 minutes and improved accuracy by 20%.
Can you discuss a project where achieving high-quality standards in body fitting was challenging? How did you manage to maintain those standards?
How to Answer
- 1
Start with a specific project example that had quality challenges.
- 2
Explain the quality standards that were at risk.
- 3
Discuss the specific actions you took to address the challenges.
- 4
Highlight any tools or methods you used to ensure quality.
- 5
Conclude with the outcome and what you learned from the experience.
Example Answers
In my previous role, I worked on a custom apparel project where the fitting specifications were very strict. We initially faced challenges with sizing mismatches. To address this, I implemented a detailed fitting process, including multiple rounds of sample fittings and feedback sessions with clients. I used advanced fitting software to analyze measurements and make precise adjustments. As a result, we achieved a perfect fit for the final product, and the client was extremely satisfied.
Describe a time when you implemented a new technique or tool in your work. What was the result?
How to Answer
- 1
Choose a specific technique or tool that improved your work.
- 2
Explain why you decided to implement it and how you went about it.
- 3
Discuss the impact it had on your performance and the team.
- 4
Provide measurable outcomes if possible, like time saved or productivity increased.
- 5
Reflect on any challenges you faced and how you overcame them.
Example Answers
I started using a new exercise tracking app to monitor clients' progress better. I introduced it during sessions, and it improved communication with clients. Over three months, we saw a 30% increase in client adherence to workout plans.
Give an example of how you have kept your body fitting skills up to date with industry advancements.
How to Answer
- 1
Mention specific certifications or courses you have taken recently
- 2
Discuss any workshops or seminars you attended related to body fitness
- 3
Highlight any fitness trends or techniques you actively practice
- 4
Share how you follow fitness research or industry publications
- 5
Explain how you incorporate new knowledge into your training regimen
Example Answers
I recently completed a certification in Functional Training and attended a workshop on HIIT strategies. I regularly follow fitness journals to stay current and I incorporate what I've learned into my clients' training plans.
Have you ever led a body fitting project? What challenges did you face and how did you overcome them?
How to Answer
- 1
Briefly describe the project you led.
- 2
Identify specific challenges you encountered.
- 3
Explain how you addressed each challenge concretely.
- 4
Highlight key outcomes or learnings from the project.
- 5
Keep your answer focused and structured.
Example Answers
I led a body fitting project for a new clothing line where we faced sizing discrepancies. The challenge was that initial feedback indicated ill-fitting garments. We overcame this by implementing a round of user testing, gathering more precise measurements, and adjusting our patterns accordingly. The final product had a much better fit, leading to a 30% decrease in return rates.
Tell me about a time when you had to be resourceful to complete a project due to limited tools or materials.
How to Answer
- 1
Identify a specific project and describe the limitations you faced.
- 2
Explain how you analyzed the situation and brainstormed alternatives.
- 3
Detail the creative solutions you implemented.
- 4
Highlight the positive outcome of your resourcefulness.
- 5
Reflect on what you learned and how it can apply to future challenges.
Example Answers
In my previous job as a fitness instructor, I had to conduct a workshop with minimal equipment. I used bodyweight exercises and improvised with resistance bands, which I had on hand. The class was popular, and we got great feedback on the creativity and adaptability. I learned that you can achieve results with what you have if you think outside the box.
Don't Just Read Body Fitter Questions - Practice Answering Them!
Reading helps, but actual practice is what gets you hired. Our AI feedback system helps you improve your Body Fitter interview answers in real-time.
Personalized feedback
Unlimited practice
Used by hundreds of successful candidates
Technical Interview Questions
What tools and equipment do you commonly use when fitting vehicle bodies, and how do you ensure they are maintained properly?
How to Answer
- 1
List specific tools like welding equipment, body hammers, measuring tools.
- 2
Explain how you inspect tools regularly for wear and tear.
- 3
Mention cleaning processes and storage practices to prevent damage.
- 4
Discuss the importance of following manufacturer maintenance schedules.
- 5
Include your approach to training team members on tool usage and maintenance.
Example Answers
I frequently use tools such as MIG welders, body hammers, and tape measures. I check each tool for defects before use, clean them after jobs, and store them in designated areas to reduce wear.
What types of materials are most commonly used in car body panels, and how do their properties affect your fitting process?
How to Answer
- 1
Identify the main materials like steel, aluminum, and plastic.
- 2
Explain the properties of each material such as weight, strength, and durability.
- 3
Discuss how these properties influence the fitting techniques and tools used.
- 4
Mention any specific challenges that arise with different materials.
- 5
Highlight the importance of proper alignment and adjustment for each material type.
Example Answers
Car body panels are typically made from steel, aluminum, and plastic. Steel is strong yet heavy, which affects the handling during fitting. Aluminum is lighter and easier to work with but can be more prone to denting. Plastics are lightweight and corrosion-resistant, allowing for quicker fittings, but require specific techniques to ensure proper alignment.
Don't Just Read Body Fitter Questions - Practice Answering Them!
Reading helps, but actual practice is what gets you hired. Our AI feedback system helps you improve your Body Fitter interview answers in real-time.
Personalized feedback
Unlimited practice
Used by hundreds of successful candidates
Explain the process you use to ensure proper alignment when fitting body panels.
How to Answer
- 1
Start with visual inspection of the body panel and its mounting points.
- 2
Use gap measurements to ensure the consistent spacing between panels.
- 3
Adjust the panel position while securing it loosely to enable fine-tuning.
- 4
Check alignment using alignment tools or reference lines to verify precision.
- 5
Finalize adjustments and tighten all fasteners securely after achieving alignment.
Example Answers
I begin by visually inspecting the panel and checking its mounting points for any misalignment. Then, I measure the gaps between the panels to ensure they are uniform. I secure the panel loosely to allow for adjustments, then use alignment tools to confirm everything is aligned properly before tightening all the fasteners.
How do you take accurate measurements to ensure a perfect fit for body panels?
How to Answer
- 1
Use precise measuring tools like tape measures or calipers
- 2
Ensure the body is in the correct posture during measurements
- 3
Take measurements multiple times for accuracy and consistency
- 4
Record measurements systematically for reference
- 5
Consider the properties of the material being fitted to account for stretch or shrinkage
Example Answers
I take measurements using a high-quality tape measure, ensuring the person stands straight for accuracy. I repeat each measurement twice and write them down immediately to avoid mistakes.
What experience do you have with custom fabrication of body panels?
How to Answer
- 1
Mention specific projects where you fabricated body panels.
- 2
Explain the tools and techniques you used for custom fabrication.
- 3
Discuss any challenges faced during fabrication and how you overcame them.
- 4
Highlight collaboration with other team members in the fabrication process.
- 5
Include any relevant training or certifications related to body fabrication.
Example Answers
I fabricated custom body panels for a classic car restoration project. I used metalworking tools like a plasma cutter and sheet metal brake. One challenge was achieving a perfect fit for the rear quarter panels, but I navigated this by creating a template from the original panels.
Can you explain the welding techniques you use when fitting vehicle bodies?
How to Answer
- 1
Focus on specific techniques you are familiar with.
- 2
Mention safety protocols you follow when welding.
- 3
Include types of materials you work with.
- 4
Discuss the importance of precision in body fitting.
- 5
Be ready to explain why you prefer certain techniques.
Example Answers
I primarily use MIG welding for fitting vehicle bodies because it's efficient and provides strong welds. I also ensure to follow proper safety protocols like wearing protective gear and ensuring good ventilation.
What steps do you take in preparing surfaces for painting after fitting body panels?
How to Answer
- 1
Ensure the surface is clean and free of dirt or grease using a suitable cleaner.
- 2
Sand the surface to create a smooth and even texture.
- 3
Use a primer on bare metal areas to prevent rust and improve paint adhesion.
- 4
Mask off areas not to be painted to keep edges clean.
- 5
Inspect the surface for imperfections and repair them before applying paint.
Example Answers
First, I clean the surface with a degreaser to remove any contaminants. Then, I sand it down to ensure it's smooth. I always apply a primer on bare metal spots to enhance adhesion. Lastly, I mask off areas I don't want to paint to protect them.
What software tools or technologies have you used in the design or fitting of body panels?
How to Answer
- 1
Mention specific CAD software you have used, such as CATIA or SolidWorks.
- 2
Discuss any simulation tools for stress analysis or airflow analysis.
- 3
Include experience with body fitting technologies like 3D scanning.
- 4
Highlight any collaboration tools for teamwork in design projects.
- 5
Be prepared to describe how these tools improved your design process.
Example Answers
I have used SolidWorks for CAD design of body panels and ANSYS for stress analysis, which helped me ensure the panels could withstand various conditions.
What types of adhesives do you use in fitting, and how do you choose the right one for the job?
How to Answer
- 1
Identify common adhesives like contact cement, epoxy, and hot melt glue.
- 2
Explain the importance of surface compatibility for adhesion.
- 3
Discuss the strength and flexibility required for the fitting.
- 4
Mention environmental factors like temperature and humidity affecting adhesive choice.
- 5
Share any specific experience you have with adhesive applications.
Example Answers
I commonly use contact cement for fitting materials like laminate and wood, as it provides a strong bond and is easy to apply. I choose it based on the compatibility with the surface and the required drying time.
How do you ensure body panels are evenly adjusted for optimal vehicle performance during fitting?
How to Answer
- 1
Start with a thorough inspection of the body panels for any defects
- 2
Use precise measurement tools for alignment and fitment checks
- 3
Perform adjustments systematically, starting from structural points
- 4
Check for even gaps and flushness at all panel edges
- 5
Test drive the vehicle after adjustments to assess performance impact
Example Answers
I begin by inspecting the body panels for any surface defects, then use calipers and measuring tapes to ensure they are precisely aligned. I make adjustments from key structural points and consistently check the gaps and flushness of the panels. Finally, I take the vehicle for a test drive to evaluate its performance with the adjustments made.
Don't Just Read Body Fitter Questions - Practice Answering Them!
Reading helps, but actual practice is what gets you hired. Our AI feedback system helps you improve your Body Fitter interview answers in real-time.
Personalized feedback
Unlimited practice
Used by hundreds of successful candidates
Situational Interview Questions
If you notice a panel does not align correctly after fitting, what steps would you take to diagnose and fix the issue?
How to Answer
- 1
Inspect the panel for visible damage or misalignment.
- 2
Check the fastening points to ensure they are secure.
- 3
Measure the gap between the panel and adjacent surfaces.
- 4
Adjust the panel by loosening and repositioning it as necessary.
- 5
Re-test the panel alignment and repeat if needed.
Example Answers
First, I would inspect the panel for any visible damage or signs of misalignment. Next, I'd check all fastening points to ensure they are secure. If the panel is still misaligned, I would measure the gaps to identify any discrepancies. Then, I would carefully adjust the panel by loosening it and repositioning it. Finally, I'd recheck the alignment to ensure it's correct.
A customer is unhappy with the fit of their newly installed panels. How would you handle their complaint while ensuring high service standards?
How to Answer
- 1
Listen to the customer's concerns without interrupting
- 2
Apologize for the inconvenience and empathize with their situation
- 3
Assess the problem by asking clarifying questions
- 4
Offer a solution, such as a follow-up visit or adjustments
- 5
Ensure follow-up communication to confirm satisfaction after resolution
Example Answers
I would first listen carefully to the customer's concerns and validate their feelings. Then, I would apologize for the inconvenience and ask specific questions to understand the issue better. Based on their feedback, I would propose a solution, like reassessing the installation and making necessary adjustments. Finally, I would ensure to follow up with the customer to ensure they are happy with the resolution.
Don't Just Read Body Fitter Questions - Practice Answering Them!
Reading helps, but actual practice is what gets you hired. Our AI feedback system helps you improve your Body Fitter interview answers in real-time.
Personalized feedback
Unlimited practice
Used by hundreds of successful candidates
If you are running behind schedule on a fitting task, what strategies would you employ to catch up without compromising quality?
How to Answer
- 1
Identify the key tasks that are behind and prioritize them.
- 2
Communicate with team members about the delay and ask for support.
- 3
Use effective time management techniques like setting mini-deadlines.
- 4
Focus on high-impact adjustments that improve efficiency.
- 5
Stay organized to ensure you maintain quality while speeding up.
Example Answers
I would first list the tasks that are causing the delay and prioritize them. Then, I would communicate with my team to see if anyone can assist with those tasks, allowing me to maintain quality while catching up. I'd also set small deadlines to stay on track.
During the fitting process, you discover some hidden damage that complicates the task. What would you do?
How to Answer
- 1
Assess the extent of the damage and note the specifics
- 2
Communicate with the client about the findings and possible solutions
- 3
Determine if the damage can be repaired or if a replacement is necessary
- 4
Adjust your fitting plan based on the new information
- 5
Document the issue and any actions taken for future reference
Example Answers
I would first assess the damage to understand its severity. Then, I would inform the client about what I found and discuss possible solutions. If repairs can be made, I'd proceed, otherwise I would suggest alternatives and adjust my fitting plan accordingly.
If a fitting project you are working on is over the budget, how would you manage costs without sacrificing quality?
How to Answer
- 1
Identify areas of potential cost savings such as materials or processes
- 2
Communicate with suppliers for discounts or alternative options
- 3
Prioritize essential features that maintain quality over luxury options
- 4
Implement efficient project management to reduce wasted time and resources
- 5
Continuously monitor expenses to adjust the budget in real-time
Example Answers
I would first analyze the budget to identify where costs have exceeded expectations, then look for cheaper materials that meet our quality standards. Next, I'd discuss with suppliers for possible discounts. Instead of expensive additions, I’d focus on the core features that enhance the final product.
If a coworker is having difficulty with a fitting task, how would you assist and communicate effectively to ensure the project's success?
How to Answer
- 1
Identify the specific challenge your coworker is facing.
- 2
Offer your assistance by asking how you can help them directly.
- 3
Provide clear and constructive feedback to guide them.
- 4
Encourage collaboration and share techniques that have worked for you.
- 5
Follow up to see if they need more support after your initial help.
Example Answers
I would first ask my coworker what specific issue they are facing with the fitting task. Then I would offer to help them by sitting down together and discussing possible solutions. I'd share techniques that have worked for me and encourage them to ask questions throughout the process.
You made a small error while fitting a panel, but it was only noticed later. What would you do?
How to Answer
- 1
Acknowledge the error immediately.
- 2
Assess the impact of the error on the overall project.
- 3
Propose a solution to fix the error.
- 4
Communicate clearly with your supervisor or team.
- 5
Learn from the experience to avoid future mistakes.
Example Answers
I would first acknowledge the error to my supervisor and explain how it happened. Then I would assess if it affects functionality and propose a fix to replace or adjust the panel.
How would you handle a disagreement with a team member over the best method to fit a certain component?
How to Answer
- 1
Listen carefully to the team member's perspective without interrupting
- 2
Share your own view clearly and respectfully
- 3
Suggest finding common ground or a compromise solution
- 4
Propose testing both methods to see which works best
- 5
Encourage involving a third party for objective input if necessary
Example Answers
I would first listen to my team member's method and understand their reasoning. Then, I would explain my approach clearly and highlight the benefits. Together, we could perhaps test both methods to determine which is most effective.
A new team member is struggling with fitting panels. How would you go about training and supporting them?
How to Answer
- 1
Observe the team member's fitting process closely to identify issues.
- 2
Provide hands-on demonstrations of proper fitting techniques.
- 3
Encourage questions and create a supportive environment for learning.
- 4
Pair them with an experienced team member for mentoring.
- 5
Set clear, achievable goals and track their progress over time.
Example Answers
I would first observe them while they fit the panels to see where they are having difficulties. After identifying the issues, I would demonstrate the correct fitting technique and explain the key steps. I would encourage them to ask any questions to ensure they understand.
Imagine your team is consistently facing delays in body fitting tasks. How would you approach improving the process?
How to Answer
- 1
Identify the root causes of delays through team discussions.
- 2
Analyze the current workflow for bottlenecks or inefficiencies.
- 3
Implement time-tracking tools to monitor task completion.
- 4
Encourage open communication for quick issue resolution.
- 5
Provide training or resources to team members to enhance skills.
Example Answers
I would start by holding a team meeting to discuss specific delays and gather insights. Then, I would analyze our workflow to identify any bottlenecks and address them. Implementing a time-tracking system could help us monitor our progress and pinpoint areas for improvement.
Don't Just Read Body Fitter Questions - Practice Answering Them!
Reading helps, but actual practice is what gets you hired. Our AI feedback system helps you improve your Body Fitter interview answers in real-time.
Personalized feedback
Unlimited practice
Used by hundreds of successful candidates
Body Fitter Position Details
Recommended Job Boards
CareerBuilder
www.careerbuilder.com/jobs/body-fitterZipRecruiter
www.ziprecruiter.com/Jobs/Body-FitterThese job boards are ranked by relevance for this position.
Related Positions
- Body Maker
- Body Builder
- Upfitter
- Door Fitter
- Stove Fitter
- Cushion Filler
- Mattress Filler
- Bottom Liner
- Bed Maker
- Boat Outfitter
Similar positions you might be interested in.
Ace Your Next Interview!
Practice with AI feedback & get hired faster
Personalized feedback
Used by hundreds of successful candidates
Ace Your Next Interview!
Practice with AI feedback & get hired faster
Personalized feedback
Used by hundreds of successful candidates