Top 29 Linotype Operator Interview Questions and Answers [Updated 2025]
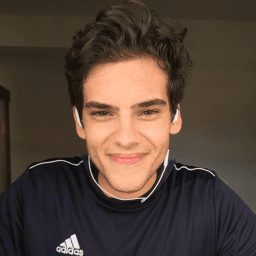
Andre Mendes
•
March 30, 2025
Preparing for a Linotype Operator interview can be daunting, but we're here to help you succeed. In this post, you'll find the most common interview questions for the role, along with insightful example answers and practical tips to respond confidently. Whether you're a seasoned professional or new to the field, this guide will equip you with the knowledge to impress your interviewers and land the job.
Download Linotype Operator Interview Questions in PDF
To make your preparation even more convenient, we've compiled all these top Linotype Operatorinterview questions and answers into a handy PDF.
Click the button below to download the PDF and have easy access to these essential questions anytime, anywhere:
List of Linotype Operator Interview Questions
Behavioral Interview Questions
Can you describe a time when you worked closely with a team to solve a significant printing issue?
How to Answer
- 1
Focus on a specific example with clear details
- 2
Highlight your role and contributions within the team
- 3
Mention the steps the team took to identify and resolve the issue
- 4
Incorporate the outcome or results of the team's efforts
- 5
Emphasize communication and collaboration among team members
Example Answers
In my previous job, our team faced a major issue with misalignment on the press. I organized a meeting with the operators and the maintenance crew, and we brainstormed potential causes. I suggested we run calibration tests on the equipment. After finding the root cause, we quickly adjusted the machinery, which improved our production quality significantly.
Tell me about a challenging project you completed and what steps you took to ensure quality.
How to Answer
- 1
Choose a project that had a specific challenge related to quality.
- 2
Describe the steps you took to address the challenge clearly.
- 3
Highlight how you communicated with your team to ensure quality.
- 4
Emphasize any tools or techniques you used to improve quality.
- 5
Conclude with the positive outcome of your efforts.
Example Answers
In my last job, I worked on a large layout that had strict deadlines but required high accuracy. I created a detailed checklist for each step, collaborated closely with my team to review proofs, and implemented a double-check system for quality before final output. As a result, we not only met the deadline but also received praise for the print quality.
Don't Just Read Linotype Operator Questions - Practice Answering Them!
Reading helps, but actual practice is what gets you hired. Our AI feedback system helps you improve your Linotype Operator interview answers in real-time.
Personalized feedback
Unlimited practice
Used by hundreds of successful candidates
Provide an example of a time when your attention to detail prevented a major error in your work.
How to Answer
- 1
Think of a specific instance that highlights your attention to detail.
- 2
Describe the context and what could have gone wrong.
- 3
Explain the actions you took to ensure accuracy.
- 4
Emphasize the outcome and how it benefited the project or team.
- 5
Keep it concise and relevant to the role of a Linotype Operator.
Example Answers
In my previous job as a typesetter, I noticed a recurring error in the font specifications for a publishing project. I double-checked each page and discovered that several pages were set to the wrong font size. I corrected the errors before printing, which saved us from a costly reprint.
Describe a situation where you had to manage your time efficiently under tight deadlines.
How to Answer
- 1
Select a specific instance from your experience.
- 2
Highlight the challenge and the time constraint.
- 3
Explain the steps you took to prioritize tasks.
- 4
Emphasize the outcome and what you learned from the experience.
- 5
Keep your response structured and concise.
Example Answers
In my previous role as a print technician, I faced a last-minute request to produce a large print run for a client. With only 24 hours to meet their deadline, I quickly assessed the workload and prioritized by first completing the most critical tasks, such as preparing the Linotype machine and sourcing materials. I communicated with my team to delegate lesser tasks and we finished ahead of schedule, which impressed the client and led to additional orders.
How have you adapted to changes in technology or processes in your previous roles?
How to Answer
- 1
Identify specific technologies or processes you have adapted to.
- 2
Explain the context of the change and its impact on your work.
- 3
Describe the steps you took to learn or adjust.
- 4
Highlight any positive outcomes or improvements from your adaptation.
- 5
Show enthusiasm for ongoing learning and adaptability.
Example Answers
In my previous role, we shifted from traditional typesetting to digital printing. I took the initiative to attend online training sessions and practiced on the new software. This not only improved my efficiency but also allowed us to take on more varied projects.
Can you provide an example of when you had to implement quality checks in your work? How did you approach it?
How to Answer
- 1
Identify a specific situation where you ensured quality.
- 2
Describe the steps you took for the quality checks.
- 3
Mention the tools or techniques used to verify quality.
- 4
Discuss the results and improvements made to the process.
- 5
Reflect on what you learned from that experience.
Example Answers
In my previous role, I noticed inconsistencies in print quality. I implemented a step where I checked each printing plate for alignment and made adjustments when needed. This reduced errors by 20%.
Describe a time when you took the lead on a project or initiative within the printing team. What was the outcome?
How to Answer
- 1
Choose a specific project where you had a significant role.
- 2
Focus on your leadership actions and decisions.
- 3
Highlight the impact of your leadership on the team and project outcome.
- 4
Use metrics or outcomes to demonstrate success.
- 5
Keep the response clear and structured, covering the situation, action, and result.
Example Answers
In a recent project, I noticed that our workflow was inefficient during peak print runs. I proposed and led a team meeting to reorganize our processes, implementing a new tracking system for jobs. As a result, we reduced turnaround times by 20%, and our error rate dropped significantly.
Tell me about a time when you received constructive feedback on your work. How did you respond to it?
How to Answer
- 1
Choose a specific example that shows your ability to accept feedback
- 2
Explain the feedback you received clearly
- 3
Describe the actions you took in response to the feedback
- 4
Highlight the positive outcome of the changes you made
- 5
Keep your tone positive and show willingness to learn
Example Answers
At my previous job, my supervisor pointed out that my typesetting speeds could be improved. I took this feedback seriously and practiced using different typesetting techniques daily. After a few weeks, I was able to increase my speed significantly, which improved our team's overall efficiency.
Describe a situation where you had to use creativity to solve a problem related to typesetting or printing.
How to Answer
- 1
Think of a specific project you worked on.
- 2
Identify a challenge you faced during typesetting or printing.
- 3
Explain the creative solution you implemented.
- 4
Highlight the positive outcome of your solution.
- 5
Be concise and focus on your role in the solution.
Example Answers
During a rush job, the client wanted a unique layout that wasn't standard. I brainstormed different formats and created a mockup with varied fonts and spacing that matched their vision. The client loved it and the job was completed ahead of schedule.
Technical Interview Questions
What is your experience with operating a Linotype machine? Please describe your familiarity with its parts and functions.
How to Answer
- 1
Start by stating the duration and context of your experience.
- 2
Mention specific parts of the Linotype machine you are familiar with.
- 3
Describe key functions you performed while operating the machine.
- 4
Highlight any specialized training or courses you've completed.
- 5
Conclude with how this experience makes you a good fit for the role.
Example Answers
I operated a Linotype machine for about three years at a local print shop. I am familiar with the keyboard, matrix, and casting mechanism. My main tasks included setting type and adjusting the machine for different fonts. I attended a workshop on Linotype operations, which deepened my understanding of its mechanics.
Can you explain what type of materials you typically use in typesetting and how you select them?
How to Answer
- 1
Mention common materials like type metal, paper, and ink.
- 2
Explain how you choose materials based on project requirements.
- 3
Discuss the importance of quality and consistency in materials.
- 4
Include any specific brands or types you prefer for reliability.
- 5
Talk about how you stay updated on new materials and technologies.
Example Answers
In typesetting, I typically use type metal for the printing plates, high-quality paper suited for the ink types, and various inks based on the desired finish. I select materials based on the project needs, like durability for outdoor prints or richness for artistic pieces. Consistency is key, so I often stick to known brands that have proven reliable.
Don't Just Read Linotype Operator Questions - Practice Answering Them!
Reading helps, but actual practice is what gets you hired. Our AI feedback system helps you improve your Linotype Operator interview answers in real-time.
Personalized feedback
Unlimited practice
Used by hundreds of successful candidates
What routine maintenance tasks do you perform on the Linotype machine to ensure it runs smoothly?
How to Answer
- 1
Highlight key daily maintenance tasks like cleaning and oiling.
- 2
Mention inspection of parts for wear or damage.
- 3
Discuss the importance of adjusting settings for optimal performance.
- 4
Include the significance of keeping the machine calibrated.
- 5
Emphasize recording maintenance activities for future reference.
Example Answers
Every day, I clean the machine's components and oil the moving parts. I also inspect the rollers and gears for any wear and make necessary adjustments to settings to ensure everything is calibrated correctly.
How do you ensure accuracy and quality in the typesetting process when producing printed material?
How to Answer
- 1
Double-check all text before starting the typesetting.
- 2
Use proofing tools to catch errors in spelling and alignment.
- 3
Implement a checklist for final review of typeset materials.
- 4
Consistently compare printed proof to digital files for discrepancies.
- 5
Engage in regular communication with the editorial team for clarity.
Example Answers
I ensure accuracy by carefully proofreading all texts before starting the typesetting process. I utilize proofing software to eliminate any spelling mistakes and follow a checklist to verify each aspect before final review.
Are you familiar with any software that assists in typesetting? If so, please elaborate on your experience.
How to Answer
- 1
Mention specific typesetting software you have used
- 2
Describe your level of proficiency with each software
- 3
Include examples of projects where you used the software
- 4
Highlight any relevant training or certifications
- 5
Emphasize how the software improved your workflow
Example Answers
I have experience using Adobe InDesign for typesetting, where I created layouts for magazines. I am proficient in using its tools for advanced typography and layout management. In my last project, I used InDesign to format a 100-page newsletter, which I completed ahead of schedule due to the software's efficiency.
What types of metal type and faces are you comfortable working with, and how do you select them for a job?
How to Answer
- 1
Identify specific types of metal type you have experience with, such as Helvetica or Times New Roman.
- 2
Discuss the characteristics of typefaces that influence your selection, like readability and aesthetic fit.
- 3
Explain how the purpose of the print job affects your typeface choice, whether for headlines or body text.
- 4
Mention any practical experience with different type sizes and styles, such as bold or italic.
- 5
Share how you evaluate the final output, considering factors like paper type and printing method.
Example Answers
I am comfortable working with typefaces like Garamond and Bodoni. For a job, I select type based on the project's needs; for instance, I use Garamond for elegant invitations and Bodoni for bold headlines.
What common problems can arise when operating a Linotype machine, and how would you troubleshoot them?
How to Answer
- 1
Identify key problems such as misalignment, jams, and type errors.
- 2
Explain how to diagnose each problem step by step.
- 3
Include preventative measures to avoid these issues.
- 4
Mention the importance of regular maintenance and checks.
- 5
Demonstrate your problem-solving skills with practical examples.
Example Answers
Common problems include misalignment, which can be fixed by adjusting the machine's settings. Jams often occur, and I troubleshoot them by carefully inspecting the feed mechanism. Regularly cleaning the machine helps prevent these issues.
How do you approach mixing inks for different types of printing jobs? Could you walk us through your process?
How to Answer
- 1
Identify the type of printing job and its requirements.
- 2
Choose the base colors needed for the job.
- 3
Test small batches before full-scale mixing.
- 4
Adjust the ink consistency based on the press type.
- 5
Document the mixture ratios for future reference.
Example Answers
For a new job, I first check the specifications to understand the required colors. Then, I select the base inks and mix them in small batches, testing their print quality. I adjust the thickness depending on whether it's offset or letterpress, and I always keep notes on the ratios I use.
What industry standards do you follow when performing typesetting and printing tasks?
How to Answer
- 1
Mention specific standards such as ISO 12647 for color management
- 2
Discuss adherence to the accessibility guidelines for text legibility
- 3
Reference the importance of DPI settings for print quality
- 4
Highlight the significance of using approved fonts and sizes according to design specifications
- 5
Explain the process of proofing and making revisions based on client feedback
Example Answers
In typesetting and printing, I follow ISO 12647 standards to ensure accurate color reproduction. I also make sure to use the correct DPI settings for print quality and adhere to accessibility guidelines so that the text remains legible for all readers.
Can you explain your workflow during a typical day as a Linotype operator?
How to Answer
- 1
Start with your preparation, mentioning equipment checks and material organization
- 2
Discuss the types of materials you work with throughout the day
- 3
Include the process from typesetting to casting and quality control
- 4
Highlight how you manage deadlines and prioritize tasks
- 5
Mention collaboration with other team members or departments, if applicable
Example Answers
A typical day begins with checking my Linotype machine for maintenance and ensuring the workspace is organized. I load the necessary type and prepare for the jobs scheduled that day. I spend time typesetting the text, then casting metal as needed, ensuring quality checks for each cast before moving on. I prioritize tasks based on deadlines, and if I'm collaborating with designers, I communicate regularly to ensure everything is on track.
Don't Just Read Linotype Operator Questions - Practice Answering Them!
Reading helps, but actual practice is what gets you hired. Our AI feedback system helps you improve your Linotype Operator interview answers in real-time.
Personalized feedback
Unlimited practice
Used by hundreds of successful candidates
Situational Interview Questions
If you notice a malfunction in the Linotype machine while in the middle of a printing job, what immediate steps would you take?
How to Answer
- 1
Stop the machine immediately to prevent further damage.
- 2
Identify the type of malfunction, whether it’s mechanical or electronic.
- 3
Check the manual or troubleshooting guide for common issues.
- 4
Communicate with your team about the issue and potential downtime.
- 5
Make necessary adjustments or repairs if qualified to do so, or escalate to a technician.
Example Answers
I would stop the machine immediately to prevent further damage. Then, I would assess whether the issue is mechanical or electronic. I would consult the troubleshooting guide for possible solutions and inform my team about the situation.
How would you handle a disagreement with a team member about the best approach to a typesetting project?
How to Answer
- 1
Listen actively to the team member's perspective and understand their reasoning.
- 2
Express your own viewpoint clearly and respectfully, using specific examples.
- 3
Seek common ground by finding aspects of both approaches that could be beneficial.
- 4
Consider the project's goals and how each approach aligns with them.
- 5
If necessary, involve a supervisor or seek further resources to reach a resolution.
Example Answers
I would first listen to my team member's point of view to fully understand their reasoning. After that, I would share my perspective, highlighting any key differences and the reasons behind my approach. Together, we would discuss the pros and cons of each method to reach a consensus that best meets the project's needs.
Don't Just Read Linotype Operator Questions - Practice Answering Them!
Reading helps, but actual practice is what gets you hired. Our AI feedback system helps you improve your Linotype Operator interview answers in real-time.
Personalized feedback
Unlimited practice
Used by hundreds of successful candidates
If you received a batch of printed material that did not meet quality standards, how would you address this issue?
How to Answer
- 1
Identify the specific quality issues present in the batch.
- 2
Consult the quality standards to understand the deviations.
- 3
Communicate the issue to your supervisor and the team.
- 4
Evaluate if the batch can be corrected or if reprinting is necessary.
- 5
Document the issue and the steps taken for future reference.
Example Answers
I would first inspect the batch to pinpoint the specific quality issues, such as misalignment or color inaccuracies. Then, I would compare these with our quality standards to establish how far off they are. I would inform my supervisor and discuss the best steps to address it, whether through correction or reprinting. Lastly, I would document the findings and actions taken.
Imagine you are overloaded with work and need to prioritize multiple jobs. How would you decide which job to tackle first?
How to Answer
- 1
Assess deadlines of each job
- 2
Evaluate the time required for each task
- 3
Consider the impact of each job on the operation
- 4
Settle priorities based on urgency and importance
- 5
Communicate with colleagues if needed to realign priorities
Example Answers
I would first check which jobs have the closest deadlines and prioritize those. Then I would assess how much time each job would take and see if there's a task that can be completed quickly to relieve some workload.
What steps would you take if you observed a colleague not following safety protocols while operating heavy equipment?
How to Answer
- 1
Approach the colleague privately and express your concerns.
- 2
Clearly explain the safety protocol they are overlooking.
- 3
Encourage them to correct their actions for their own safety.
- 4
If necessary, report the behavior to a supervisor for further action.
- 5
Always prioritize safety and teamwork in your response.
Example Answers
I would first talk to my colleague in private and explain the specific safety protocol they are not following. I would emphasize that following safety procedures is crucial for everyone's safety. If they refuse to follow the protocol, I would then inform a supervisor about the situation.
If the Linotype machine is down for maintenance before a big job, how would you decide on alternative resources to meet the deadline?
How to Answer
- 1
Assess the urgency of the job and the expected downtime of the Linotype machine.
- 2
Identify alternative typesetting methods or machines available in your facility.
- 3
Consult with your team to gather insights and suggestions.
- 4
Prioritize jobs based on their deadlines and resource availability.
- 5
Communicate clearly with stakeholders about potential impacts on the schedule.
Example Answers
I would first check how long the Linotype machine is expected to be down. If it's within a manageable timeframe, I might prioritize other work that can wait, but if it's going to take too long, I would look to other typesetting machines we have. I would gather the team’s input to see if any alternative solutions can be implemented quickly, ensuring we meet our deadline.
If a customer is unhappy with a print job you managed, how would you handle the situation to maintain their satisfaction?
How to Answer
- 1
Listen carefully to the customer's concerns without interrupting.
- 2
Acknowledge their feelings and express understanding of their dissatisfaction.
- 3
Apologize for any mistakes or issues with the print job.
- 4
Offer a solution, such as a reprint or discount, depending on the situation.
- 5
Follow up after the resolution to ensure the customer is satisfied.
Example Answers
I would start by listening to the customer's concerns without interrupting. I would acknowledge their feelings and apologize for the mistakes. Then, I would offer to reprint the job at no extra cost to them, ensuring we make it right. Finally, I would follow up to make sure they were satisfied with the resolution.
If you had to train a new team member on operating the Linotype machine, what key areas would you focus on?
How to Answer
- 1
Start with safety protocols and machine familiarization
- 2
Explain the types of materials and settings used for different jobs
- 3
Demonstrate the basic operation steps and troubleshooting methods
- 4
Teach maintenance routines for keeping the machine in good condition
- 5
Encourage regular practice under supervision to build confidence
Example Answers
I would begin by emphasizing safety protocols and ensuring the new team member understands the machine layout. Next, I'd cover the materials we use and how to set them up correctly for various projects. After that, I'd demonstrate the steps to operate the machine and common troubleshooting techniques. I'd also include maintenance practices to keep everything running smoothly, followed by supervised practice sessions to reinforce their learning.
How would you ensure quality and performance when facing an unexpected surge in printing demand?
How to Answer
- 1
Assess current workload and capacity to identify bottlenecks
- 2
Prioritize tasks to focus on high-impact jobs first
- 3
Utilize maintenance procedures to ensure equipment is functioning optimally
- 4
Communicate with the team about the surge and reallocate resources as necessary
- 5
Implement quality checks regularly to maintain standards even under pressure
Example Answers
To manage an unexpected surge, I would first assess our current workload to determine where we can maximize efficiency. I'd prioritize high-impact jobs and ensure the team communicates effectively while shifting resources where needed. Additionally, I'd conduct quick maintenance checks to guarantee that our equipment is performing at its best.
Imagine you need to collaborate with the graphic design team on a project. How would you manage the communication and workflow to ensure smooth completion?
How to Answer
- 1
Establish clear points of contact between teams.
- 2
Use project management tools for tracking tasks.
- 3
Schedule regular check-ins to address updates.
- 4
Encourage open feedback on designs and production issues.
- 5
Set deadlines that accommodate both teams' schedules.
Example Answers
I would start by designating a liaison from each team to ensure consistent communication. We can use a project management tool like Trello to keep track of tasks. Regular weekly check-ins would help us stay on track and address any concerns.
Don't Just Read Linotype Operator Questions - Practice Answering Them!
Reading helps, but actual practice is what gets you hired. Our AI feedback system helps you improve your Linotype Operator interview answers in real-time.
Personalized feedback
Unlimited practice
Used by hundreds of successful candidates
Linotype Operator Position Details
Related Positions
- Linotyper
- Linotypist
- Typographer
- Electronic Operator
- Phototypesetter
- Electrotyper
- Prepress Operator
- Keyboard Operator
- Lithographer
- Scanner Operator
Similar positions you might be interested in.
Ace Your Next Interview!
Practice with AI feedback & get hired faster
Personalized feedback
Used by hundreds of successful candidates
Ace Your Next Interview!
Practice with AI feedback & get hired faster
Personalized feedback
Used by hundreds of successful candidates