Top 31 Lithographer Interview Questions and Answers [Updated 2025]
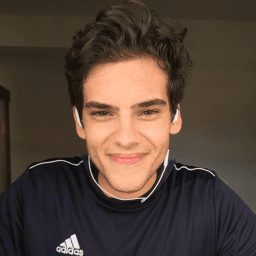
Andre Mendes
•
March 30, 2025
Preparing for a lithographer interview can be daunting, but our updated guide for 2025 has you covered with the most common interview questions in the field. This post not only provides example answers but also offers valuable tips on how to respond effectively, ensuring you're ready to impress. Dive in to gain the insights and confidence needed to excel in your lithographer interview.
Download Lithographer Interview Questions in PDF
To make your preparation even more convenient, we've compiled all these top Lithographerinterview questions and answers into a handy PDF.
Click the button below to download the PDF and have easy access to these essential questions anytime, anywhere:
List of Lithographer Interview Questions
Behavioral Interview Questions
Can you describe a time when you had to collaborate with others on a lithography project? What was your role?
How to Answer
- 1
Think of a specific project involving team collaboration
- 2
Highlight your specific role and contributions clearly
- 3
Mention the outcome of the project and its impact
- 4
Include any tools or processes you used to facilitate collaboration
- 5
Discuss any challenges faced and how you overcame them
Example Answers
In a recent project, I worked with a group of lithographers to produce a series of art prints. My role was to coordinate the color matching processes and ensure that everyone was aligned on the project deadlines. We used shared digital boards to track our progress, and the project was completed two weeks early, receiving positive feedback from the client.
Tell me about a challenging lithography job you completed. What difficulties did you encounter and how did you overcome them?
How to Answer
- 1
Choose a specific lithography job that presented real challenges.
- 2
Clearly explain the difficulties you faced during the project.
- 3
Describe the steps you took to resolve the challenges.
- 4
Highlight any skills or techniques you used to tackle the issues.
- 5
Conclude with the positive outcome and what you learned from the experience.
Example Answers
In a recent project, we had trouble with ink consistency affecting print quality. I identified the problem by running test prints and adjusted the ink formulation after consulting with my supplier. After implementing the changes, the print quality improved significantly and we met our deadline.
Don't Just Read Lithographer Questions - Practice Answering Them!
Reading helps, but actual practice is what gets you hired. Our AI feedback system helps you improve your Lithographer interview answers in real-time.
Personalized feedback
Unlimited practice
Used by hundreds of successful candidates
Describe a situation where your attention to detail directly impacted the quality of a lithographed product.
How to Answer
- 1
Think of a specific project where you noticed a detail others missed.
- 2
Explain the problem that detail caused and how you addressed it.
- 3
Quantify the impact if possible, such as improved customer satisfaction.
- 4
Use the STAR method: Situation, Task, Action, Result.
- 5
Keep it concise and focus on your direct contributions.
Example Answers
In a recent project for a client, I noticed a misalignment in color layers during the proofing stage. I halted the production to adjust the settings, which ensured that the colors matched the client's expectations perfectly. As a result, we received a commendation for our quality control.
Have you ever had to adapt to a significant change in technique or technology in lithography? How did you handle it?
How to Answer
- 1
Identify a specific change you experienced in lithography.
- 2
Explain how you learned about the new technique or technology.
- 3
Describe the steps you took to adapt, including any training or practice.
- 4
Mention the impact of this change on your work and results.
- 5
Highlight any positive outcomes from this adaptation.
Example Answers
In my previous job, we switched to digital lithography technology. I attended training sessions to learn the new software. I practiced extensively and quickly adapted my workflow to enhance efficiency. As a result, our production speed increased by 30%.
How do you prioritize your tasks when working on multiple lithographic projects?
How to Answer
- 1
List all current projects and their deadlines to get an overview.
- 2
Identify tasks that are critical for project completion first.
- 3
Communicate with team members to understand their priorities.
- 4
Use a project management tool or checklist to track progress.
- 5
Adjust priorities based on feedback and changing project requirements.
Example Answers
I start by listing all my current lithographic projects and their respective deadlines. Then, I identify the tasks that are critical for each project's success and focus on those. I also make sure to communicate with my team to align on priorities, and I use a project management tool to track my progress efficiently.
Describe an instance where you had to lead a team in a lithography project. What approach did you take?
How to Answer
- 1
Start with a specific project to set the context.
- 2
Highlight your leadership role and responsibilities.
- 3
Explain your approach in terms of communication and delegation.
- 4
Mention any challenges faced and how you overcame them.
- 5
Conclude with the successful outcome and what you learned.
Example Answers
In a recent project, I led a team to produce high-quality lithographic prints for a marketing campaign. I organized weekly meetings to ensure effective communication, and delegated tasks based on each member's strengths. We faced issues with color consistency, which we resolved by adjusting our printing parameters and conducting tests. The project was successful, and we delivered on time, boosting client satisfaction by 30%.
Describe a time when you implemented a new process or technology in lithography. What was the outcome?
How to Answer
- 1
Choose a specific instance from your experience in lithography.
- 2
Explain the problem you faced before implementing the new process.
- 3
Describe the steps you took to implement the new process or technology.
- 4
Highlight the positive outcome or improvements that resulted from your implementation.
- 5
Be prepared to discuss any challenges you faced during implementation and how you overcame them.
Example Answers
At my previous job, I identified that our ink drying process was causing issues with image quality. I researched and implemented a new drying technology, which involved upgrading our UV curing system. This not only sped up production by 20% but also improved overall print quality, leading to fewer customer complaints.
Tell me about a time you learned something new in lithography that significantly improved your work.
How to Answer
- 1
Describe a specific skill or technique you learned.
- 2
Explain the impact it had on your work quality or efficiency.
- 3
Mention any relevant challenges you faced while learning.
- 4
Highlight how you applied this knowledge in a practical situation.
- 5
Be concise and focus on the positive outcomes.
Example Answers
I recently learned a new technique for adjusting ink viscosity during the lithography process. This significantly improved the color consistency in my prints. Initially, I struggled to find the right balance, but I practiced by experimenting with small batches until I achieved the desired results. Now, my team produces much higher-quality prints with fewer adjustments needed.
What motivates you the most in your work as a lithographer?
How to Answer
- 1
Focus on aspects of lithography you enjoy, such as creativity or precision
- 2
Mention specific tasks that bring you satisfaction, like color matching or print quality
- 3
Explain how seeing the finished product motivates you and the impact it has
- 4
Consider discussing teamwork and collaboration with your peers
- 5
Share a personal story or experience that highlights your passion for lithography
Example Answers
I am most motivated by the precision required in lithography. I love the challenge of color matching and ensuring that every print is perfect. Seeing the final product come to life is incredibly satisfying and fuels my passion for this work.
Don't Just Read Lithographer Questions - Practice Answering Them!
Reading helps, but actual practice is what gets you hired. Our AI feedback system helps you improve your Lithographer interview answers in real-time.
Personalized feedback
Unlimited practice
Used by hundreds of successful candidates
Technical Interview Questions
What types of lithographic printing presses have you operated, and what are their differences?
How to Answer
- 1
Identify specific lithographic presses you've operated.
- 2
Briefly explain the type of work each press is suited for.
- 3
Mention any unique features or differences between the presses.
- 4
Highlight your comfort level and proficiency with each type.
- 5
Connect your experience with the needs of the role you're applying for.
Example Answers
I have operated offset lithographic presses like the Heidelberg Speedmaster and the KBA Rapida. The Speedmaster is great for high-volume work, while the KBA has faster setup times for shorter runs.
Explain the lithographic process. What are the key steps involved from start to finish?
How to Answer
- 1
Start with a brief definition of lithography.
- 2
Identify each key step clearly in chronological order.
- 3
Use simple language to explain technical terms.
- 4
Include the materials involved in each step.
- 5
Be prepared to explain why each step is important.
Example Answers
Lithography is a printing process that uses a flat surface. The key steps are: preparing the lithographic plate, applying an oil-based image, treating the plate with chemicals, and then using water to keep non-image areas free from ink. Finally, the inked plate is pressed onto paper to produce the final print.
Don't Just Read Lithographer Questions - Practice Answering Them!
Reading helps, but actual practice is what gets you hired. Our AI feedback system helps you improve your Lithographer interview answers in real-time.
Personalized feedback
Unlimited practice
Used by hundreds of successful candidates
What types of inks and substrates do you prefer to work with in lithography, and why?
How to Answer
- 1
Identify specific ink types you are familiar with, such as oil-based or water-based.
- 2
Mention preferred substrates like paper, cardboard, or plastic materials.
- 3
Explain why you prefer these inks and substrates, focusing on quality and print results.
- 4
Discuss any personal experience that highlights your preferences effectively.
- 5
Be ready to connect your preferences to the needs of the potential employer.},
Example Answers
I prefer working with oil-based inks because they provide rich colors and excellent durability. I often use coated paper substrates for their smooth finish, which enhances print quality and detail. In my last project, this combination allowed for vibrant marketing materials that met client expectations.
How do you maintain lithography equipment to ensure optimal performance?
How to Answer
- 1
Conduct regular inspections of all lithography machinery to detect any wear or damage.
- 2
Clean the equipment frequently to prevent dust and debris from affecting performance.
- 3
Check and calibrate exposure settings to ensure accurate reproduction of designs.
- 4
Keep a maintenance log to track issues and service history for the equipment.
- 5
Follow manufacturer guidelines for lubrication and parts replacement schedules.
Example Answers
I maintain lithography equipment by performing weekly inspections to spot any potential issues, cleaning the machines daily to avoid contamination, and ensuring that all settings are calibrated according to the specifications.
What common issues do you encounter in lithography, and how do you troubleshoot them?
How to Answer
- 1
Identify specific lithography issues like registration problems, poor ink adhesion, or contamination.
- 2
Explain your troubleshooting process step-by-step.
- 3
Mention tools or techniques used to diagnose and fix issues.
- 4
Provide examples from past experiences to demonstrate your problem-solving skills.
- 5
Emphasize the importance of preventive measures to avoid issues.
Example Answers
One common issue is registration misalignment. I check the registration marks and adjust the press if needed. I also ensure the plates are aligned properly before starting. In my last job, I resolved a recurring misalignment by recalibrating the setup.
Which design software do you use for preparing lithographic plates, and how proficient are you in it?
How to Answer
- 1
Identify the design software you use specifically for lithography
- 2
Mention your proficiency level clearly and confidently
- 3
Include any relevant certifications or training
- 4
Mention any projects where you successfully used the software
- 5
Conclude with your willingness to learn new software if required
Example Answers
I primarily use Adobe Illustrator for preparing lithographic plates and I am proficient in it, having created numerous projects that required precise layout and design over the last 5 years. I also completed a certification in Adobe Creative Suite.
What are the environmental regulations you need to consider while performing lithography?
How to Answer
- 1
Research local and national environmental regulations regarding hazardous waste disposal and emissions
- 2
Understand the use of eco-friendly inks and chemicals that comply with regulations
- 3
Ensure proper ventilation systems are in place to mitigate the release of volatile organic compounds (VOCs)
- 4
Stay updated on any changes in environmental laws that affect lithography processes
- 5
Implement best practices for recycling materials and reducing waste during production.
Example Answers
As a lithographer, I need to be aware of EPA regulations regarding hazardous waste, especially concerning ink and chemical disposal. This includes using compliant disposal methods and ensuring our materials are eco-friendly. Additionally, maintaining proper ventilation to control VOC emissions is crucial.
What are the differences between offset lithography and digital lithography?
How to Answer
- 1
Highlight that offset lithography uses printing plates while digital lithography uses digital files.
- 2
Mention that offset is generally more cost-effective for large runs compared to digital.
- 3
Explain that digital lithography allows for variable data printing and faster turnaround times.
- 4
Discuss the quality aspect, noting how offset provides high-quality prints for large formats.
- 5
Conclude by emphasizing the flexibility of digital lithography for small orders and customization.
Example Answers
Offset lithography relies on plates to transfer ink, which makes it cost-effective for large volumes. In contrast, digital lithography uses digital files directly to print, allowing quick changes and smaller runs. Offset excels in quality for mass prints, while digital is great for customization and swift jobs.
What do you consider when selecting inks for different jobs? How does this affect the final print?
How to Answer
- 1
Consider the substrate material and how the ink adheres to it.
- 2
Evaluate the intended use of the print, such as durability and color fidelity.
- 3
Account for drying times and curing processes relevant to the inks.
- 4
Think about environmental factors like temperature and humidity during printing.
- 5
Select inks that enhance the final appearance, like gloss or matte finishes.
Example Answers
When selecting inks, I first consider the substrate, ensuring the ink adheres well. For instance, when printing on plastic, I choose inks designed for plastics to avoid smudging. This directly impacts the durability and vibrancy of the print.
What are the steps involved in making a lithographic plate?
How to Answer
- 1
Start with surface preparation of the plate.
- 2
Apply a light-sensitive coating to the plate.
- 3
Expose the plate to an image using UV light.
- 4
Develop the plate by washing away the unexposed areas.
- 5
Finish with a baking process to harden the coating.
Example Answers
The process begins with preparing the plate's surface, then applying a light-sensitive coating. After that, we expose the plate to a UV image, develop it to remove unexposed parts, and finally bake it to set the coating.
Don't Just Read Lithographer Questions - Practice Answering Them!
Reading helps, but actual practice is what gets you hired. Our AI feedback system helps you improve your Lithographer interview answers in real-time.
Personalized feedback
Unlimited practice
Used by hundreds of successful candidates
How do you optimize workflow in a lithographic environment to enhance productivity?
How to Answer
- 1
Assess the current workflow to identify bottlenecks
- 2
Implement lean manufacturing principles to reduce waste
- 3
Regularly maintain and calibrate equipment to ensure efficiency
- 4
Train staff continuously on best practices and new technologies
- 5
Utilize software tools for job scheduling and progress tracking
Example Answers
I start by analyzing our existing processes to pinpoint where delays occur, then I apply lean principles to streamline those areas. This reduces waste and enhances throughput.
What safety protocols do you follow in the lithography process?
How to Answer
- 1
Emphasize personal protective equipment usage like gloves and goggles.
- 2
Mention regular maintenance of lithographic equipment to prevent hazards.
- 3
Discuss proper chemical handling and waste disposal practices.
- 4
Highlight the importance of ventilation in the workspace.
- 5
State adherence to established safety guidelines and training programs.
Example Answers
I always wear gloves and goggles when handling chemicals to protect myself from any harmful substances. Additionally, I ensure that all equipment is well-maintained to minimize risks during printing operations.
Situational Interview Questions
If there was a last-minute change request from a client on a lithography job, how would you handle it?
How to Answer
- 1
Stay calm and assess the situation promptly
- 2
Communicate with the client to clarify the changes needed
- 3
Evaluate the impact on the timeline and resources
- 4
Propose solutions that accommodate the request as much as possible
- 5
Document the changes and confirm with the client before proceeding
Example Answers
I would first listen carefully to the client's change request and make sure I understand it fully. Then, I would assess how this change affects our current schedule and resources. If possible, I would suggest alternatives that could meet their needs while also keeping us on track.
How would you approach a situation where the printed lithographs do not meet the quality standards?
How to Answer
- 1
Identify the specific quality issue immediately.
- 2
Analyze the printing process to locate the root cause.
- 3
Consult with team members to gather insights.
- 4
Implement corrective actions and monitor results.
- 5
Document the findings and adjust standard operating procedures.
Example Answers
If the lithographs do not meet quality standards, I would first determine the specific issue—whether it's color accuracy, registration, or paper quality. Then, I'd review the production process to find out where it went wrong. I'd involve my team for ideas and fix the problem before reprinting, ensuring we document everything for future reference.
Don't Just Read Lithographer Questions - Practice Answering Them!
Reading helps, but actual practice is what gets you hired. Our AI feedback system helps you improve your Lithographer interview answers in real-time.
Personalized feedback
Unlimited practice
Used by hundreds of successful candidates
Imagine you are close to a deadline and realize that your press is malfunctioning. What steps would you take?
How to Answer
- 1
Stay calm and assess the situation quickly
- 2
Identify the specific issue with the press
- 3
Communicate with your team about the problem
- 4
Implement a temporary solution if possible
- 5
Seek assistance or escalate if the problem cannot be resolved quickly
Example Answers
I would first take a moment to calm myself and then assess what exactly is malfunctioning on the press. Once I have identified the issue, I would inform my team and look for a temporary workaround. If it’s something I can't fix quickly, I would reach out for technical support immediately to avoid missing the deadline.
If you had to work with a difficult client who is unhappy with your lithographic proofs, how would you manage the situation?
How to Answer
- 1
Listen actively to the client's concerns
- 2
Acknowledge their feelings and validate their frustration
- 3
Ask questions to clarify their expectations
- 4
Propose solutions to rectify the issue
- 5
Follow up to ensure the client is satisfied with the outcome
Example Answers
I would first listen to the client’s concerns to understand their perspective. I would acknowledge their frustration and ask clarifying questions about what they specifically dislike. Then, I would suggest possible adjustments and involve them in the decision-making process. Finally, I would ensure to follow up to reassure them we are committed to meeting their needs.
What would you do if you were asked to use a new lithography technique that you're unfamiliar with?
How to Answer
- 1
Stay calm and express willingness to learn.
- 2
Research the technique through available resources.
- 3
Ask colleagues or experts for insights and tips.
- 4
Consider taking a quick training or workshop if time permits.
- 5
Document the new process for future reference.
Example Answers
If I was asked to use a new lithography technique, I would first stay calm and show my willingness to learn. I'd research the technique online and find relevant articles or videos. Additionally, I would consult with my colleagues who may have experience with it, and if needed, I would look into quick training sessions.
If you have limited resources for a lithography project, how would you prioritize your tasks?
How to Answer
- 1
Identify the critical tasks that must be completed for the project to succeed
- 2
Assess the impact of each task on the overall project outcome
- 3
Allocate resources to high-priority tasks first, ensuring they are completed efficiently
- 4
Communicate with the team about priorities and resource constraints
- 5
Be flexible and ready to adjust priorities as new information arises
Example Answers
I would first identify the essential tasks that are crucial for the lithography project’s success. For example, ensuring that the setup of the press is correct would be a top priority. Then, I would allocate resources to these tasks and keep the team informed about our focus areas. This strategy allows us to maximize our limited resources effectively.
How would you handle a situation where a client is requesting a turnaround that is impossible due to technical limitations?
How to Answer
- 1
Acknowledge the client's request and express understanding of their urgency
- 2
Clearly explain the technical limitations that prevent meeting their request
- 3
Offer alternative solutions or timelines that can work within the limitations
- 4
Communicate transparently and keep the client informed throughout the process
- 5
Follow up with the client to ensure satisfaction with the final outcome
Example Answers
I would first acknowledge the client's urgency and let them know I understand their needs. Then I would explain the specific technical limitations we are facing, ensuring they understand why the original request isn’t feasible. Next, I would propose alternative options or realistic timelines to meet their requirements. Throughout the process, I would keep open lines of communication to update them on progress.
How would you manage a team that's struggling with a particular lithography task?
How to Answer
- 1
Identify the specific issues the team is facing.
- 2
Encourage open communication to discuss challenges and ideas.
- 3
Provide additional training or resources if necessary.
- 4
Set clear goals and break the task into manageable parts.
- 5
Regularly check in with the team to monitor progress and offer support.
Example Answers
I would start by having a meeting to understand the specific challenges the team is facing. Once identified, I would encourage them to share their insights and suggestions openly. I believe providing targeted training could help, and breaking the task down into smaller goals would also make the task less daunting.
If you were to present lithographic proofs to a client, how would you prepare for that meeting?
How to Answer
- 1
Review the proofs thoroughly for quality and precision.
- 2
Understand the client's preferences and project requirements.
- 3
Prepare a clear presentation layout highlighting each proof.
- 4
Anticipate potential client questions and prepare responses.
- 5
Bring necessary materials, such as samples and tools for adjustments.
Example Answers
I would start by reviewing the proofs to ensure there are no errors. Then, I'd tailor my presentation to highlight how each proof meets the client's needs based on their feedback.
Lithographer Position Details
Recommended Job Boards
ZipRecruiter
www.ziprecruiter.com/Jobs/LithographerThese job boards are ranked by relevance for this position.
Related Positions
- Job Lithographer
- Photolithographer
- Photoengraver
- Linotyper
- Linotypist
- Typographer
- Printing Technician
- Prepress Operator
- Printing Plate Maker
- Linotype Operator
Similar positions you might be interested in.
Ace Your Next Interview!
Practice with AI feedback & get hired faster
Personalized feedback
Used by hundreds of successful candidates
Ace Your Next Interview!
Practice with AI feedback & get hired faster
Personalized feedback
Used by hundreds of successful candidates