Top 30 Logistics Analyst Interview Questions and Answers [Updated 2025]
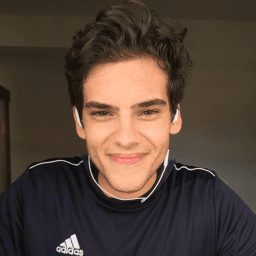
Andre Mendes
•
March 30, 2025
Navigating the interview process for a Logistics Analyst position can be daunting, but preparation is key to success. In this comprehensive guide, we delve into the most common interview questions for this role, providing you with example answers and insightful tips on how to respond effectively. Whether you're a seasoned professional or new to the field, this resource will equip you with the knowledge to impress potential employers and secure your next opportunity.
Download Logistics Analyst Interview Questions in PDF
To make your preparation even more convenient, we've compiled all these top Logistics Analystinterview questions and answers into a handy PDF.
Click the button below to download the PDF and have easy access to these essential questions anytime, anywhere:
List of Logistics Analyst Interview Questions
Behavioral Interview Questions
Tell us about a time when you identified a bottleneck in a logistics process. How did you address it?
How to Answer
- 1
Choose a specific example from your experience
- 2
Explain how you recognized the bottleneck clearly
- 3
Describe the steps you took to analyze the situation
- 4
Detail the solution you implemented and its impact
- 5
Be ready to discuss what you learned from the experience
Example Answers
In my previous job, we faced delays in order fulfillment. I tracked the workflow and noticed that manual data entry was causing errors and slowing us down. I proposed automating the data input process and implemented a new software solution. This reduced errors by 30% and improved order processing speed significantly.
Describe an instance where your analysis of data significantly improved a logistics operation.
How to Answer
- 1
Choose a specific project or task where your analysis had a clear outcome.
- 2
Use data metrics to quantify the improvement you achieved.
- 3
Explain the methods you used to analyze the data.
- 4
Discuss any challenges you faced and how you overcame them.
- 5
Conclude with the overall impact on the logistics operation.
Example Answers
In my previous role, I analyzed shipping data and discovered that our delivery routes had excessive overlaps. By reorganizing the routes based on my analysis, we reduced fuel costs by 15% and improved delivery times by 20%.
Don't Just Read Logistics Analyst Questions - Practice Answering Them!
Reading helps, but actual practice is what gets you hired. Our AI feedback system helps you improve your Logistics Analyst interview answers in real-time.
Personalized feedback
Unlimited practice
Used by hundreds of successful candidates
Give an example of how you successfully communicated a complex logistics concept to a non-technical team.
How to Answer
- 1
Identify the complex logistics concept clearly and concisely.
- 2
Tailor your explanation to the audience's level of understanding.
- 3
Use analogies or simple examples to illustrate key points.
- 4
Encourage questions to ensure understanding.
- 5
Summarize the main points to reinforce the message.
Example Answers
In my previous role, I explained supply chain optimization to the marketing team by comparing it to organizing a successful event. I highlighted how each part of the logistics process, like sourcing and distribution, is like planning venues and catering, ensuring everyone understood the importance of each step.
Can you describe a situation where you worked with other departments to improve a logistics process?
How to Answer
- 1
Identify a specific project or situation
- 2
Mention the departments you collaborated with
- 3
Describe the problem or inefficiency you addressed
- 4
Explain the steps you took to collaborate and their impact
- 5
Highlight measurable outcomes or improvements achieved
Example Answers
In my previous role, I worked with the purchasing and sales departments to reduce order processing delays. We identified that poor communication about inventory levels was causing late shipments. I organized weekly meetings to align our stock data, which resulted in a 20% reduction in delays over three months.
Describe a time when you had to quickly adapt to a change in a logistics plan. What was the outcome?
How to Answer
- 1
Choose a specific example from your experience.
- 2
Highlight the change in the logistics plan and its impact.
- 3
Explain the actions you took to adapt to this change.
- 4
Discuss the outcome and what you learned from it.
- 5
Keep the focus on your role and contributions.
Example Answers
In my previous role, the supplier we relied on for parts experienced a sudden delay. I quickly coordinated with alternative suppliers, analyzed their capabilities, and placed orders for critical components. As a result, we minimized downtime and met our project deadline.
Tell us about a time you led a logistics project from start to finish. What was the outcome?
How to Answer
- 1
Choose a specific project where you had a leadership role.
- 2
Describe the key steps you took from planning to execution.
- 3
Highlight any challenges you faced and how you overcame them.
- 4
Mention the outcome and any measurable results.
- 5
Reflect on what you learned from the experience.
Example Answers
In my last position, I led a project to streamline the inventory management process. I organized a team to assess our current systems, identified inefficiencies, and implemented a new software solution. We reduced order processing time by 30%, which improved customer satisfaction. This experience taught me the importance of teamwork and clear communication.
Describe how your attention to detail has helped prevent a logistics error in the past.
How to Answer
- 1
Choose a specific instance that highlights your attention to detail
- 2
Describe the error that was avoided and its impact
- 3
Explain the steps you took that demonstrate your attention to detail
- 4
Emphasize the result and what you learned from the experience
- 5
Relate it back to how it benefits the logistics process overall
Example Answers
In my previous role, I noticed a discrepancy in shipment weights just before dispatch. I double-checked the packing lists and the actual weights, leading to the discovery of a miscalculation. By correcting this, we avoided overcharging the client and ensured compliance with shipping regulations.
Give an example of a logistics improvement initiative that you started.
How to Answer
- 1
Choose a specific initiative you led or were part of
- 2
Explain the problem that the initiative addressed
- 3
Describe the actions you took to implement the initiative
- 4
Share the measurable results or improvements achieved
- 5
Highlight any skills or tools you used in the process
Example Answers
In my previous role, I noticed recurring delays in our shipping process. I implemented a new software tool that automated tracking notifications, which reduced shipping delays by 30%. This also improved customer satisfaction as they received real-time updates.
Describe a time when you successfully managed to cut costs in a logistics operation without sacrificing quality.
How to Answer
- 1
Identify a specific project where you reduced costs.
- 2
Explain the methods you used to analyze cost drivers.
- 3
Highlight any innovative solutions or technology you implemented.
- 4
Emphasize how you maintained or improved service quality.
- 5
Conclude with quantifiable results or savings achieved.
Example Answers
In my previous role, I analyzed our freight costs and discovered we were overpaying for shipping. I negotiated better rates with our carriers and switched to a more efficient routing strategy, which reduced our shipping costs by 15% while maintaining on-time delivery rates.
Explain how you have contributed to continuous improvement in your logistics role.
How to Answer
- 1
Identify a specific project or initiative you led or participated in.
- 2
Quantify the improvements achieved with measurable data, like percentage increases or cost reductions.
- 3
Describe how you collaborated with others to address challenges or implement changes.
- 4
Mention any tools or methodologies (like Lean or Six Sigma) you utilized.
- 5
Convey the impact of your contributions on overall operations or customer satisfaction.
Example Answers
In my previous role, I led a project to optimize our shipping routes. By analyzing our delivery data, we reduced delivery times by 15% and saved $20,000 in fuel costs annually. I worked closely with the transport team and applied Lean principles to streamline our processes.
Don't Just Read Logistics Analyst Questions - Practice Answering Them!
Reading helps, but actual practice is what gets you hired. Our AI feedback system helps you improve your Logistics Analyst interview answers in real-time.
Personalized feedback
Unlimited practice
Used by hundreds of successful candidates
Technical Interview Questions
What techniques do you use to model logistics processes and predict future trends?
How to Answer
- 1
Identify specific modeling techniques like simulation and optimization.
- 2
Mention data analysis methods such as regression or time-series analysis.
- 3
Discuss tools you are familiar with, like Excel, R, or MATLAB.
- 4
Provide examples of how you have used these methods in past roles.
- 5
Emphasize the importance of continuous improvement and feedback loops.
Example Answers
I use simulation models to map logistics processes, alongside regression analysis for trend prediction. In my last role, I utilized Excel for data analysis and presented predictions to management.
What logistics and supply chain software are you proficient in, and how have you used it in your work?
How to Answer
- 1
Identify specific software you've used in previous roles.
- 2
Explain your level of proficiency with the software.
- 3
Provide concrete examples of how you've utilized the software to solve problems.
- 4
Highlight any improvements or efficiencies you achieved with the software.
- 5
Mention any relevant certifications or training if applicable.
Example Answers
I am proficient in SAP and have used it extensively to manage inventory levels and streamline order processing. For instance, I implemented a reporting dashboard that reduced our order fulfillment time by 20%.
Don't Just Read Logistics Analyst Questions - Practice Answering Them!
Reading helps, but actual practice is what gets you hired. Our AI feedback system helps you improve your Logistics Analyst interview answers in real-time.
Personalized feedback
Unlimited practice
Used by hundreds of successful candidates
How would you use statistical analysis to predict inventory needs?
How to Answer
- 1
Identify historical sales data and trends for different products
- 2
Use time series analysis to forecast future demand
- 3
Consider seasonality and market trends in your analysis
- 4
Employ inventory models such as EOQ or safety stock calculations
- 5
Regularly update forecasts based on new data and performance metrics
Example Answers
I would start by analyzing historical sales data to identify patterns and trends for each product. From there, I would apply time series analysis to forecast future demand while accounting for seasonality. I would also leverage inventory models like EOQ to maintain optimal stock levels.
What methods do you use to optimize transportation and distribution routes?
How to Answer
- 1
Analyze historical data to identify patterns in transportation costs and times
- 2
Utilize optimization software or tools to simulate different route scenarios
- 3
Consider factors like traffic, delivery windows, and vehicle capacity when planning routes
- 4
Incorporate real-time data to adjust routes dynamically during transportation
- 5
Collaborate with drivers and logistics staff to gather insights on route performance
Example Answers
To optimize transportation routes, I analyze historical data to spot trends in costs and times. I also use route optimization tools to simulate different scenarios and find the most efficient paths considering traffic and delivery constraints.
Explain how you might conduct a cost-benefit analysis for a new logistics technology.
How to Answer
- 1
Identify the costs associated with the new technology, including acquisition and implementation.
- 2
Estimate the potential benefits, like cost savings and efficiency improvements.
- 3
Quantify the costs and benefits in monetary terms where possible.
- 4
Consider the time frame for realizing benefits and any ongoing costs.
- 5
Evaluate non-monetary factors such as customer satisfaction and operational flexibility.
Example Answers
To conduct a cost-benefit analysis for a new logistics technology, I would first list all costs, including purchase, installation, and training. Then, I'd estimate the benefits, focusing on cost savings from improved efficiency. I'd express both in monetary terms to see the ROI over a 5-year period, considering ongoing maintenance costs and potential impacts on customer satisfaction.
What key performance indicators (KPIs) do you track in logistics operations?
How to Answer
- 1
Identify the most relevant KPIs for logistics, such as order accuracy, inventory turnover, and transportation costs
- 2
Explain how each KPI impacts overall logistics efficiency and customer satisfaction
- 3
Mention specific tools or systems you use to track these KPIs
- 4
Provide examples of how you've used KPI data to make improvements
- 5
Be prepared to discuss how KPIs align with company goals
Example Answers
I track order accuracy, which measures how often orders are fulfilled correctly. This directly impacts customer satisfaction. I also monitor inventory turnover to ensure efficient stock management. I use ERP systems like SAP to pull these metrics.
Describe your experience with maintaining and querying logistics databases.
How to Answer
- 1
Discuss specific logistics databases you've used, such as SAP, Oracle, or custom systems.
- 2
Mention your role in maintaining data integrity and accuracy.
- 3
Highlight experience with SQL or other querying languages to extract insights from the data.
- 4
Provide examples of reports or analyses you've generated using the data.
- 5
Explain how your work with databases has improved logistics processes or decision-making.
Example Answers
In my previous job, I used SAP to maintain logistics databases, ensuring data accuracy by regularly auditing entries. I also utilized SQL to query the database for inventory reports, which allowed my team to optimize stock levels.
How do you approach demand forecasting in logistics? What models do you use?
How to Answer
- 1
Identify key data sources such as historical sales data and market trends
- 2
Discuss specific forecasting models like moving averages and exponential smoothing
- 3
Highlight the importance of collaboration with sales and marketing teams
- 4
Mention the use of software tools that assist in forecasting
- 5
Explain how you evaluate and adjust forecasts based on accuracy metrics
Example Answers
I approach demand forecasting by first gathering historical sales data and analyzing trends. I often use moving averages and exponential smoothing to create initial forecasts. Collaboration with sales teams helps refine these forecasts, and I regularly use software like SAP or Excel for analysis.
What Lean principles have you applied in logistics processes to improve efficiency?
How to Answer
- 1
Identify specific Lean principles like waste reduction, continuous improvement or value stream mapping
- 2
Explain a situation where you applied these principles in a logistics context
- 3
Quantify your results to demonstrate impact, such as time saved or cost reduced
- 4
Mention collaboration with teams or departments to implement changes
- 5
Focus on the outcomes and how they benefited the overall process
Example Answers
In my previous role, I applied the principle of waste reduction by conducting a value stream mapping exercise in our shipping process. By eliminating unnecessary steps, we reduced shipping time by 20%, which significantly cut costs.
How would you design a logistics network for a new product launch?
How to Answer
- 1
Identify target market and distribution channels
- 2
Analyze the supply chain components required
- 3
Determine warehousing and inventory needs
- 4
Plan for transportation methods and routes
- 5
Establish KPIs for logistics performance tracking
Example Answers
To design a logistics network for a new product launch, I would first identify the target market and distribution channels to understand where the product needs to go. Then, I would analyze the supply chain components, including suppliers and manufacturers, to ensure we have everything covered. Next, I'd determine the warehousing requirements and inventory levels needed to meet demand. I'd also plan the transportation methods and routes that optimize cost and efficiency. Finally, I'd set key performance indicators to monitor the logistics performance once the product is launched.
Don't Just Read Logistics Analyst Questions - Practice Answering Them!
Reading helps, but actual practice is what gets you hired. Our AI feedback system helps you improve your Logistics Analyst interview answers in real-time.
Personalized feedback
Unlimited practice
Used by hundreds of successful candidates
Can you explain the importance of end-to-end supply chain visibility and how it impacts logistics?
How to Answer
- 1
Define end-to-end supply chain visibility clearly
- 2
Explain how visibility improves decision-making
- 3
Mention the role of technology in achieving visibility
- 4
Discuss benefits such as cost reduction and improved customer service
- 5
Provide real-world examples or scenarios if possible
Example Answers
End-to-end supply chain visibility is crucial because it allows companies to track inventory and shipments in real-time. This visibility improves decision-making by enabling proactive management of potential disruptions. For example, if a delay is detected, we can quickly inform customers and make alternate arrangements, leading to better customer satisfaction.
Situational Interview Questions
If a supplier failed to deliver a critical component on time, what steps would you take to minimize disruption?
How to Answer
- 1
Immediately assess the impact on the supply chain and operations.
- 2
Communicate with the supplier to understand the reason for the delay.
- 3
Identify alternative suppliers or sources for the critical component.
- 4
Develop a contingency plan to mitigate any operational impact.
- 5
Keep stakeholders informed about the situation and expected outcomes.
Example Answers
First, I would evaluate how the delay affects our production schedule. Then, I would contact the supplier to get details on the delay and explore their estimated resolution time. Simultaneously, I would look for alternative suppliers to see if they can fulfill our needs quickly, and prepare a backup plan to minimize disruption in our operations.
Suppose you have two potential carriers: one is cheaper but less reliable, and the other is reliable but more expensive. How would you decide which to use?
How to Answer
- 1
Assess the criticality of the shipment's timeline.
- 2
Calculate the total cost of delays if using the unreliable carrier.
- 3
Consider the impact on customer satisfaction and service level.
- 4
Evaluate the potential consequences of a failed delivery.
- 5
Make a decision based on a balance of cost and reliability.
Example Answers
I would first assess the importance of the shipment deadline. If timely delivery is crucial, I would choose the reliable carrier despite the higher cost, as delays could lead to significant issues.
Don't Just Read Logistics Analyst Questions - Practice Answering Them!
Reading helps, but actual practice is what gets you hired. Our AI feedback system helps you improve your Logistics Analyst interview answers in real-time.
Personalized feedback
Unlimited practice
Used by hundreds of successful candidates
Imagine a situation where shipping costs have unexpectedly risen by 20%. What strategies would you consider to manage these increased costs?
How to Answer
- 1
Assess the current shipping methods and identify inefficiencies.
- 2
Negotiate with shipping providers for better rates or terms.
- 3
Consider consolidating shipments to reduce frequency and costs.
- 4
Analyze alternative transportation options that may be more cost-effective.
- 5
Review inventory management practices to minimize urgent shipping needs.
Example Answers
To manage a 20% increase in shipping costs, I would first assess our current shipping methods to identify any inefficiencies. Next, I would negotiate with our shipping providers to see if we can secure better rates or terms. Consolidating shipments where possible could also help reduce overall costs.
How would you handle a disagreement with a vendor over a delayed shipment?
How to Answer
- 1
Stay calm and professional during the discussion.
- 2
Gather all relevant information about the shipment delay.
- 3
Ask open-ended questions to understand the vendor's perspective.
- 4
Propose a solution that works for both parties.
- 5
Follow up in writing to confirm any agreements made.
Example Answers
I would first reach out to the vendor to discuss the delay calmly and professionally. I would ask for details about the situation, allowing them to explain their side. After understanding their perspective, I'd propose a solution such as partial shipment or a revised delivery date, ensuring we align our expectations. I'd follow up with an email summarizing our conversation and agreements.
You have multiple logistics projects with tight deadlines. How would you prioritize your tasks?
How to Answer
- 1
Identify urgent vs. important tasks to separate what needs immediate attention.
- 2
Evaluate project deadlines and stakeholder expectations to rank the tasks.
- 3
Consider resource availability and delegate if feasible to manage workload.
- 4
Break down larger tasks into smaller actions to tackle them systematically.
- 5
Use scheduling tools to visualize and manage your timeline effectively.
Example Answers
I would first list all tasks and categorize them based on urgency and importance. Then, I would assess which projects have the closest deadlines and communicate with stakeholders to understand their priorities. If resources allow, I'd delegate tasks appropriately.
If you were tasked with reducing delivery times by 20%, what innovative solutions might you propose?
How to Answer
- 1
Analyze current delivery processes and identify bottlenecks.
- 2
Research and suggest technology solutions like route optimization software.
- 3
Consider partnerships with local courier services for faster last-mile delivery.
- 4
Propose implementing a real-time tracking system to improve transparency and efficiency.
- 5
Encourage continuous feedback loops from delivery personnel to find practical improvements.
Example Answers
I would analyze the current logistics processes to pinpoint delays, then propose using route optimization software to find the fastest paths. Additionally, partnering with local couriers can help speed up last-mile delivery.
What steps would you take if you identified that a major logistics hub might be affected by an impending natural disaster?
How to Answer
- 1
Assess the threat level and gather all available data on the natural disaster.
- 2
Communicate with stakeholders, including team members and upper management, to inform them of the risks.
- 3
Develop alternative logistics plans, such as rerouting shipments or relocating goods.
- 4
Coordinate with emergency services and local authorities for updated information and support.
- 5
Monitor the situation continuously and adapt plans as necessary based on real-time developments.
Example Answers
First, I would assess the severity of the anticipated disaster and collect data on its projected impact. Then, I would notify all key stakeholders and outline potential threats to our logistics chain. Next, I would draft contingency plans, including alternative routes and storage options, to ensure minimal disruption in service. I would also stay in contact with local authorities for updates during the event and adjust our plans as needed.
How would you handle a situation where consistently high error rates were reported in order fulfillment?
How to Answer
- 1
Analyze the data to identify specific error types
- 2
Engage with the team to understand potential causes
- 3
Implement process improvements or technology solutions
- 4
Train staff on best practices and error prevention
- 5
Monitor the results to ensure improvements are effective
Example Answers
I would start by analyzing the data to pinpoint which errors are most common. Then, I'd collaborate with my team to discuss any challenges they face. From there, I would suggest implementing a double-check system and providing additional training. Finally, I would monitor the error rates post-implementation to gauge success.
How would you handle a customer complaint about delayed deliveries in a cost-effective manner?
How to Answer
- 1
Acknowledge the customer's issue promptly and empathetically.
- 2
Gather detailed information about the specific delay to understand the root cause.
- 3
Offer realistic solutions or alternatives, such as expedited shipping or discounts.
- 4
Keep the customer informed throughout the resolution process.
- 5
Follow up after resolution to ensure customer satisfaction.
Example Answers
I would start by acknowledging the customer's concern and apologizing for the delay. Then, I would gather all necessary details regarding their order to identify the cause. I would suggest a possible solution, like expedited shipping for their next order, and keep them updated until the issue is resolved. Finally, I would follow up to confirm they're satisfied with the outcome.
Logistics Analyst Position Details
Salary Information
Recommended Job Boards
CareerBuilder
www.careerbuilder.com/jobs-logistics-analystZipRecruiter
www.ziprecruiter.com/Jobs/Logistics-AnalystThese job boards are ranked by relevance for this position.
Related Positions
Ace Your Next Interview!
Practice with AI feedback & get hired faster
Personalized feedback
Used by hundreds of successful candidates
Ace Your Next Interview!
Practice with AI feedback & get hired faster
Personalized feedback
Used by hundreds of successful candidates