Top 30 Supply Technician Interview Questions and Answers [Updated 2025]
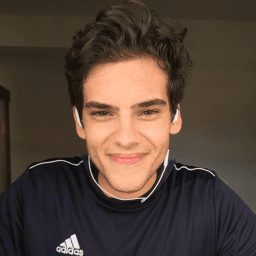
Andre Mendes
•
March 30, 2025
Preparing for a supply technician interview can be daunting, but our comprehensive guide has you covered. Dive into this post to discover the most common interview questions for the supply technician role, complete with example answers and practical tips on how to respond effectively. Whether you're a seasoned professional or new to the field, this resource will help you confidently tackle your next interview.
Download Supply Technician Interview Questions in PDF
To make your preparation even more convenient, we've compiled all these top Supply Technicianinterview questions and answers into a handy PDF.
Click the button below to download the PDF and have easy access to these essential questions anytime, anywhere:
List of Supply Technician Interview Questions
Technical Interview Questions
How do you ensure accurate record-keeping of supply transactions?
How to Answer
- 1
Use software tools for tracking inventory and transactions
- 2
Regularly audit records to catch discrepancies early
- 3
Maintain a consistent process for entering and updating data
- 4
Implement a double-check system for important entries
- 5
Train team members on record-keeping best practices
Example Answers
I utilize inventory management software to log all supply transactions immediately, ensuring accurate and timely updates, while conducting monthly audits to verify the data against physical inventory.
What experience do you have with inventory management software, and how have you used it effectively in your previous roles?
How to Answer
- 1
Identify specific inventory management software you have used.
- 2
Explain your role and how you implemented or managed the software.
- 3
Share an example of a challenge you faced and how the software helped you solve it.
- 4
Discuss measurable outcomes you achieved using the software.
- 5
Show familiarity with data analysis or reporting features of the software.
Example Answers
In my last position, I used Oracle NetSuite for inventory management. I was responsible for tracking stock levels, which helped reduce excess inventory by 15%. One challenge was syncing data across multiple locations, but using NetSuite's automated reporting features, I was able to identify discrepancies promptly.
Don't Just Read Supply Technician Questions - Practice Answering Them!
Reading helps, but actual practice is what gets you hired. Our AI feedback system helps you improve your Supply Technician interview answers in real-time.
Personalized feedback
Unlimited practice
Used by hundreds of successful candidates
What are the key considerations when planning the logistics for a large order of supplies?
How to Answer
- 1
Assess the demand to determine quantities needed
- 2
Evaluate the supplier reliability and lead times
- 3
Plan transportation methods based on cost and timing
- 4
Organize warehouse space to handle incoming supplies
- 5
Coordinate with the receiving team for effective delivery
Example Answers
When planning logistics for a large order, I assess the total demand to ensure we order the right quantities, evaluate suppliers for their reliability and lead times, and choose the best transportation methods to meet our timeframe while controlling costs.
How do you analyze inventory data to forecast future supply needs?
How to Answer
- 1
Gather historical inventory data and usage rates.
- 2
Identify trends and seasonal fluctuations in the data.
- 3
Utilize inventory management software for data analysis.
- 4
Collaborate with sales and operations teams for insights.
- 5
Regularly update forecasts based on recent data and changes.
Example Answers
I analyze inventory data by first gathering historical usage trends. I look for seasonal patterns in the data and adjust our forecasts accordingly. I also use inventory software that helps visualize trends and collaborate with the sales team to refine projections.
What criteria do you use to evaluate and select vendors?
How to Answer
- 1
Identify key factors like price, quality, reliability and service.
- 2
Evaluate vendor track record and customer reviews.
- 3
Consider the vendor's financial stability and capacity.
- 4
Assess compliance with industry standards and regulations.
- 5
Build relationships for better communication and negotiation.
Example Answers
I evaluate vendors based on their pricing, product quality, and delivery timelines. Additionally, I look at their past performance and customer feedback to ensure reliability.
Explain the process you follow for ordering and receiving supplies in bulk.
How to Answer
- 1
Start with identifying supply needs based on inventory levels.
- 2
Use a standardized order form or system to place bulk orders.
- 3
Establish relationships with vendors for timely delivery and best pricing.
- 4
Confirm receipt of supplies against the order to ensure accuracy.
- 5
Document any discrepancies and follow up with the vendor immediately.
Example Answers
I first check our inventory levels to identify what supplies we need. Then, I use an electronic ordering system to submit bulk orders to our approved vendors. After placing the order, I follow up with them to confirm the delivery date. Once the supplies arrive, I check them against the order to ensure everything is correct and document any issues.
How do you ensure that all supplies comply with relevant regulations and standards?
How to Answer
- 1
Familiarize yourself with industry regulations and standards relevant to the supplies you handle.
- 2
Implement a checklist to verify compliance at each stage of supply management.
- 3
Conduct regular audits to assess the compliance status of supplies.
- 4
Maintain clear documentation of all compliance checks and supplier certifications.
- 5
Engage with suppliers to ensure they understand and meet all relevant regulations.
Example Answers
I regularly review the latest regulations affecting our supplies and create a compliance checklist that I use during audits to ensure every item meets standards.
What strategies do you employ to keep supply costs under control?
How to Answer
- 1
Regularly review inventory levels to avoid overstocking.
- 2
Negotiate with suppliers for bulk purchase discounts.
- 3
Implement a just-in-time inventory system to reduce holding costs.
- 4
Track and analyze supply usage patterns to forecast needs accurately.
- 5
Educate the team on cost-saving practices and efficient usage.
Example Answers
I regularly review our inventory to prevent overstocking, and I negotiate with suppliers to secure discounts on bulk purchases.
Can you describe the safety standards you follow when handling hazardous materials?
How to Answer
- 1
Identify the specific standards you are familiar with, like OSHA or local regulations.
- 2
Mention personal protective equipment (PPE) you use, such as gloves and masks.
- 3
Discuss safe storage and labeling practices for hazardous materials.
- 4
Explain emergency procedures you are trained in, like spill response.
- 5
Share experience with regular safety training and compliance checks.
Example Answers
I follow OSHA standards for handling hazardous materials, ensuring I always wear appropriate PPE such as gloves and safety goggles. I also make sure to label all chemicals clearly and store them in designated areas to prevent accidents.
Describe the inspection procedures you use to verify the quality of incoming supplies.
How to Answer
- 1
Start with a clear description of initial checks like visual inspections.
- 2
Mention specific tools or systems you use for quality control.
- 3
Talk about adherence to standards and regulations.
- 4
Include examples of documentation or records maintained.
- 5
Share how you handle discrepancies or issues found during inspection.
Example Answers
I begin by performing a visual inspection of the incoming supplies to check for any obvious damages or irregularities. Then, I use a calibrated scale and measuring tools to ensure dimensions and weights match specifications. I document everything in our inventory management system, noting any discrepancies, and report them to my supervisor for further action.
Don't Just Read Supply Technician Questions - Practice Answering Them!
Reading helps, but actual practice is what gets you hired. Our AI feedback system helps you improve your Supply Technician interview answers in real-time.
Personalized feedback
Unlimited practice
Used by hundreds of successful candidates
What techniques do you use to optimize supply chain efficiency?
How to Answer
- 1
Identify key metrics to measure efficiency such as lead time and inventory turnover.
- 2
Leverage technology for real-time data tracking and inventory management.
- 3
Collaborate closely with suppliers to enhance communication and reduce bottlenecks.
- 4
Implement lean principles to eliminate waste in the supply chain.
- 5
Regularly analyze performance data and adjust strategies accordingly.
Example Answers
I use metrics such as lead time and inventory turnover to identify areas for improvement. By analyzing these metrics, I can implement lean principles to reduce waste effectively.
Behavioral Interview Questions
Can you describe a time when you successfully managed inventory levels for multiple items?
How to Answer
- 1
Identify a specific project or task where you managed inventory.
- 2
Include the methods or tools you used for tracking inventory levels.
- 3
Explain how you balanced stock levels for different items.
- 4
Discuss any challenges you faced and how you overcame them.
- 5
Mention the outcome and its positive impact on the operations.
Example Answers
In my previous role, I managed inventory for a warehouse with over 500 SKUs. I implemented a software system that tracked stock levels in real-time. I balanced inventory by analyzing sales trends and adjusting reorder points. When a supply chain delay occurred, I negotiated with suppliers to expedite shipments, ensuring we maintained optimal stock levels. This reduced stockouts by 20%.
Tell me about a time when you encountered a significant supply chain disruption. How did you handle it?
How to Answer
- 1
Clearly describe the disruption and its impact.
- 2
Focus on your specific role and actions taken.
- 3
Highlight problem-solving and communication skills.
- 4
Discuss the outcome and lessons learned.
- 5
Keep the answer concise and structured.
Example Answers
In my previous role, we faced a sudden supplier failure. I quickly researched alternative suppliers and reached out for quotes. Within a week, we secured a temporary contract that minimized delays and kept production on track. This experience taught me the importance of having backup suppliers.
Don't Just Read Supply Technician Questions - Practice Answering Them!
Reading helps, but actual practice is what gets you hired. Our AI feedback system helps you improve your Supply Technician interview answers in real-time.
Personalized feedback
Unlimited practice
Used by hundreds of successful candidates
Describe a situation where you had to work closely with a team to achieve a supply-related goal. What was your role, and what was the outcome?
How to Answer
- 1
Identify a specific team project related to supply management.
- 2
Clearly state your role and responsibilities in that project.
- 3
Highlight how teamwork contributed to achieving the goal.
- 4
Discuss the outcome and any measurable results.
- 5
Mention any skills or strategies you used to facilitate teamwork.
Example Answers
In my previous role at XYZ Company, I worked on a team tasked with improving inventory accuracy. As the primary data analyst, I coordinated with team members to track discrepancies and implement solutions. We successfully reduced inventory errors by 30%, which enhanced our overall supply chain efficiency.
Give an example of how you effectively communicated with a vendor or supplier to resolve a misunderstanding.
How to Answer
- 1
Clearly describe the misunderstanding in simple terms.
- 2
Explain how you initiated communication with the vendor.
- 3
Highlight the steps you took to clarify the issue.
- 4
Mention the outcome and how you ensured it was resolved.
- 5
Reflect on what you learned from the experience.
Example Answers
In my previous job, there was a mix-up about the delivery schedule with a supplier. I contacted them directly and explained the situation clearly. We reviewed the order together and identified the sources of confusion. I confirmed the new delivery date, and it arrived on time. This reinforced my communication skills and the importance of confirming details.
Describe a time when your attention to detail helped prevent a supply issue.
How to Answer
- 1
Think of a specific situation where you caught an error or identified a risk.
- 2
Explain the steps you took to address the issue before it escalated.
- 3
Emphasize the outcome and how it benefited the team or organization.
- 4
Use the STAR method: Situation, Task, Action, Result.
- 5
Keep your answer concise and focused on your role in the success.
Example Answers
In my previous role, I noticed a discrepancy in the inventory count of a popular supply item. I conducted a thorough check and found that a recent shipment had been miscounted. By correcting the order before it was processed, we avoided a stockout situation, ensuring our team could meet production demands without delay.
Tell me about a time when you had to adapt to a sudden change in inventory requirements. How did you handle it?
How to Answer
- 1
Focus on a specific situation where inventory needs changed suddenly
- 2
Explain the steps you took to address the change
- 3
Highlight your problem-solving skills and adaptability
- 4
Mention any teamwork or communication involved
- 5
Reflect on the outcome and what you learned
Example Answers
In my previous role, we received a last-minute order that required more stock than we had available. I quickly assessed what was in our inventory, communicated with suppliers to obtain more products, and coordinated with my team to reorganize existing stock for the new needs. We managed to fulfill the order on time and maintained a strong relationship with the client.
Have you ever led a project or initiative to improve supply processes? What did you do and what were the results?
How to Answer
- 1
Identify a specific project where you improved supply processes.
- 2
Outline your role in leading the initiative clearly.
- 3
Include specific actions you took during the project.
- 4
Mention the results quantitatively if possible.
- 5
Reflect on what you learned from the experience.
Example Answers
In my previous role, I led a project to streamline our inventory management system. I implemented a new software solution that reduced processing time by 30% and improved accuracy by 20%. This cut excess inventory by 15% and saved the company costs.
Describe a time when you developed a strategic plan for supply logistics. What was your approach and the result?
How to Answer
- 1
Choose a specific project or situation.
- 2
Explain the objectives of the strategic plan.
- 3
Detail the steps you took to create and implement the plan.
- 4
Discuss the tools or metrics you used to track success.
- 5
Share the outcomes and any lessons learned.
Example Answers
In my previous role, I was tasked with reducing our excess inventory by 20%. I conducted an analysis of our supply chain, identified slow-moving items, and developed a plan to optimize our stock levels. By implementing a just-in-time delivery system, we were able to reduce excess inventory and improve cash flow by 25%.
Situational Interview Questions
Imagine you receive news that a critical supply item will be delayed by two weeks. How would you handle the situation to minimize impact?
How to Answer
- 1
Assess the criticality of the item and its role in operations
- 2
Communicate promptly with relevant stakeholders about the delay
- 3
Explore alternative suppliers or substitute items that can fill the gap
- 4
Prioritize and adjust operations or schedules to mitigate disruption
- 5
Document the situation and develop a contingency plan for future occurrences
Example Answers
I would first notify the team about the delay to ensure everyone is aware. Then, I would look for alternative suppliers who might deliver a similar item more quickly. In the meantime, I would adjust our schedules to minimize impact on operations while we wait for the delayed item.
Suppose a department urgently requests a specialized item not in inventory. How would you handle their request?
How to Answer
- 1
Assess the urgency of the request and its impact on operations
- 2
Check if the item can be sourced from suppliers quickly
- 3
Communicate estimated delivery times to the requesting department
- 4
Explore alternatives or substitutes if the item can't be sourced
- 5
Document the request for future inventory planning
Example Answers
I would first clarify the urgency and importance of the item for the department. Then, I'd check with our suppliers to see if we could obtain it quickly, and I'd communicate back the estimated delivery time. If sourcing is not feasible, I'd look for alternative items that could serve a similar purpose and inform the department accordingly.
Don't Just Read Supply Technician Questions - Practice Answering Them!
Reading helps, but actual practice is what gets you hired. Our AI feedback system helps you improve your Supply Technician interview answers in real-time.
Personalized feedback
Unlimited practice
Used by hundreds of successful candidates
You discover an error in the inventory records showing a surplus of certain items when there is actually a shortage. What steps do you take?
How to Answer
- 1
Verify the physical stock against the records to confirm the shortage
- 2
Document your findings clearly and take pictures if necessary
- 3
Report the discrepancy to your supervisor immediately
- 4
Recommend corrective actions to update the inventory system
- 5
Implement a review process to prevent future discrepancies
Example Answers
First, I would check the physical inventory to confirm that there is indeed a shortage. Then, I would document my findings and report them to my supervisor. I would suggest updating the inventory records and propose a regular review process to avoid similar issues in the future.
How would you prioritize multiple urgent supply requests from different departments?
How to Answer
- 1
Assess the urgency and impact of each request on operations
- 2
Communicate with department heads to clarify needs and timelines
- 3
Consider the availability of supplies and stock levels
- 4
Prioritize requests based on overall business priorities
- 5
Keep all stakeholders updated throughout the process
Example Answers
I would first evaluate the urgency of each request by discussing with the departments involved. I'd ask which supplies are critical to their operations and then prioritize based on business impact and available stock.
You need to negotiate better terms with a supplier who has recently increased prices. How would you approach this?
How to Answer
- 1
Research the supplier's market position and alternatives available.
- 2
Prepare to present data showing how the price increase affects your business.
- 3
Offer a longer contract in exchange for better pricing.
- 4
Be ready to demonstrate loyalty and the benefits of a sustainable partnership.
- 5
Propose a meeting to discuss the escalation and collaborate on a solution.
Example Answers
I would start by researching the market to understand if the price hike aligns with industry trends. Then, I would gather data on how this increase impacts my budget and use that to start a conversation with the supplier about negotiating more favorable terms.
If you identified a bottleneck in the supply process, what steps would you take to improve it?
How to Answer
- 1
Analyze the data to identify the root cause of the bottleneck
- 2
Engage with team members involved to gather insights and feedback
- 3
Develop a collaborative action plan to address the issue
- 4
Implement changes on a small scale first to test effectiveness
- 5
Monitor the results and adjust the plan as necessary
Example Answers
First, I would analyze the supply chain data to pinpoint where the bottleneck occurs. Then, I would talk to the team members involved to understand their perspectives. Based on this information, I would create a targeted action plan to address the bottleneck and try a small-scale implementation to see if it resolves the issue. Finally, I would monitor the results and make adjustments as needed.
A major supplier suddenly goes out of business, affecting your supply line. What do you do next?
How to Answer
- 1
Assess the immediate impact on current operations
- 2
Identify alternative suppliers quickly
- 3
Communicate with stakeholders about the situation
- 4
Review existing inventory and demand forecasts
- 5
Implement a temporary solution while securing long-term alternatives
Example Answers
I would start by evaluating how this affects our inventory and production schedules. Then, I would reach out to our existing network of suppliers to find alternatives that can meet our needs. I would also inform my team and management about the situation so we can collaboratively find solutions.
How would you ensure the availability of essential supplies in a short-term emergency situation?
How to Answer
- 1
Identify critical supplies needed for emergencies.
- 2
Establish a reliable inventory system to track stock levels.
- 3
Maintain strong relationships with suppliers for quick reordering.
- 4
Create a contingency plan for alternative supply sources.
- 5
Regularly review and update emergency supply lists.
Example Answers
In a short-term emergency, I would first identify critical supplies required, then ensure our inventory is closely monitored to avoid shortages. I would also maintain communication with suppliers for prompt restocking and have a list of alternative suppliers ready in case of delays.
If you receive a shipment with significant damage to the contents, what actions do you take?
How to Answer
- 1
Inspect the shipment immediately for damage.
- 2
Document all findings with photos and notes.
- 3
Notify the supplier or shipping company right away.
- 4
Separate damaged items from intact ones to prevent confusion.
- 5
Follow company protocols for reporting and returns.
Example Answers
First, I would inspect the shipment thoroughly for any visible damage on the contents and their packaging. Then, I would document everything with photos and detailed notes before notifying the supplier to report the damages. Finally, I would follow our internal procedure for handling such incidents.
An end user reports dissatisfaction with the delivery time of supplies. How do you address their concern?
How to Answer
- 1
Acknowledge the user's concern and express empathy.
- 2
Gather specific details about their issue to understand the context.
- 3
Explain the reasons behind the delivery delays clearly.
- 4
Provide them with a realistic timeline for when they can expect their supplies.
- 5
Follow up with the user to ensure their satisfaction after addressing their concerns.
Example Answers
I understand that timely deliveries are crucial and I’m sorry for the frustration. Can you tell me more about your order? I’ll look into the delay and provide you an estimated delivery time as soon as possible.
Don't Just Read Supply Technician Questions - Practice Answering Them!
Reading helps, but actual practice is what gets you hired. Our AI feedback system helps you improve your Supply Technician interview answers in real-time.
Personalized feedback
Unlimited practice
Used by hundreds of successful candidates
Supply Technician Position Details
Salary Information
Average Salary
$41,802
Source: Indeed
Recommended Job Boards
These job boards are ranked by relevance for this position.
Related Positions
Ace Your Next Interview!
Practice with AI feedback & get hired faster
Personalized feedback
Used by hundreds of successful candidates
Ace Your Next Interview!
Practice with AI feedback & get hired faster
Personalized feedback
Used by hundreds of successful candidates