Top 30 Machine Sorter Interview Questions and Answers [Updated 2025]
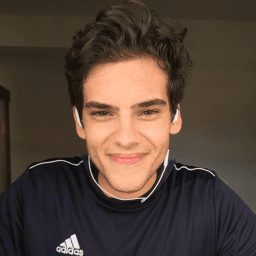
Andre Mendes
•
March 30, 2025
Navigating the job market can be challenging, especially when preparing for a 'Machine Sorter' position. Our latest blog post provides a comprehensive guide to the most common interview questions for this role, complete with example answers and effective answering tips. Whether you're a seasoned professional or new to the field, this resource will help you confidently tackle your next interview and make a lasting impression.
Download Machine Sorter Interview Questions in PDF
To make your preparation even more convenient, we've compiled all these top Machine Sorterinterview questions and answers into a handy PDF.
Click the button below to download the PDF and have easy access to these essential questions anytime, anywhere:
List of Machine Sorter Interview Questions
Behavioral Interview Questions
Have you ever trained new employees on sorting techniques? How did you approach this?
How to Answer
- 1
Focus on specific techniques you taught.
- 2
Mention the training resources or materials you used.
- 3
Discuss how you adapted your approach for different learning styles.
- 4
Highlight any positive outcomes from your training.
- 5
Share feedback you received from the new employees.
Example Answers
Yes, I trained new employees on our sorting techniques by using a combination of hands-on demonstrations and written guides. I found that many learned best by seeing the process in action and then practicing it themselves.
Describe a time when you had to work as part of a team to sort a large volume of materials quickly. What was your role?
How to Answer
- 1
Think of a specific instance where you worked in a team environment.
- 2
Highlight your specific role and responsibilities during that task.
- 3
Emphasize how you contributed to efficient sorting and teamwork.
- 4
Mention any tools or methods used to improve efficiency.
- 5
Conclude with the outcome of the team's efforts.
Example Answers
In my previous role at the warehouse, we had a sudden influx of packages to sort during peak season. I took the initiative to organize our team into smaller groups, assigning each group a specific type of item to sort. I also suggested we use color-coded tags for quick identification which sped up our workflow significantly. As a result, we managed to sort 30% more items that day compared to our usual output.
Don't Just Read Machine Sorter Questions - Practice Answering Them!
Reading helps, but actual practice is what gets you hired. Our AI feedback system helps you improve your Machine Sorter interview answers in real-time.
Personalized feedback
Unlimited practice
Used by hundreds of successful candidates
Tell me about a situation where you encountered a malfunction in the sorting machine. How did you handle it?
How to Answer
- 1
Identify a specific malfunction incident you faced.
- 2
Explain what steps you took to diagnose the problem.
- 3
Describe the solution you implemented and its effectiveness.
- 4
Highlight any collaboration with team members or supervisors.
- 5
Mention any lessons learned or improvements made to prevent future issues.
Example Answers
In my previous job, the sorting machine jammed due to a misalignment. I quickly stopped the machine and inspected the area. I found that a small component was out of place, so I realigned it and tested the machine. After the fix, I documented the issue and shared with my team how to prevent it from happening again.
Can you give me an example of a mistake you made in sorting and how you corrected it?
How to Answer
- 1
Think of a specific mistake related to sorting items.
- 2
Describe what went wrong or what you misjudged.
- 3
Explain the steps you took to correct the mistake promptly.
- 4
Highlight what you learned from the experience and any changes you made to avoid it in the future.
- 5
Keep it concise and focus on problem-solving and learning.
Example Answers
Once, I misclassified a batch of fragile items, mixing them with heavier boxes. I realized the error during a routine check. I quickly isolated the mixed items and sorted them correctly, ensuring the fragile items were placed in a designated area. From that, I created a checklist to double-check item categories before sorting.
Discuss a time you identified a safety risk while operating sorting machinery. What actions did you take?
How to Answer
- 1
Think of a specific instance where you noticed a potential hazard.
- 2
Describe the risk clearly and why it was a concern.
- 3
Explain the steps you took to mitigate the risk immediately.
- 4
Mention any follow-up actions to prevent future risks.
- 5
Highlight the importance of safety in your work ethic.
Example Answers
During my time at the warehouse, I noticed that a safety guard on the sorting machine was loose. I immediately stopped the machine, reported the issue to my supervisor, and secured the guard before resuming operations. I also suggested a weekly inspection of all machinery to prevent similar risks.
Describe a situation where you had to communicate a sorting issue to your supervisor or team. How did you approach it?
How to Answer
- 1
Identify the issue clearly and concisely.
- 2
Explain the impact of the sorting problem on operations.
- 3
Detail steps you took to communicate the issue effectively.
- 4
Discuss how you proposed a solution or improvement.
- 5
Highlight the outcome and any lessons learned.
Example Answers
I noticed that certain packages were being mis-sorted, causing delays in delivery. I immediately reported this to my supervisor, explaining that it was affecting our timeliness. I suggested we conduct a quick team meeting to review the sorting process, which led to implementing a new training session for everyone.
Can you describe an instance where you took responsibility for a successful sorting operation? What were the outcomes?
How to Answer
- 1
Identify a specific sorting operation you managed
- 2
Explain your role and responsibilities clearly
- 3
Describe challenges you faced and how you overcame them
- 4
Highlight the positive outcomes and any metrics of success
- 5
Reflect on what you learned from the experience
Example Answers
In my previous role at a logistics company, I was responsible for overseeing a busy sorting operation during peak season. I organized the workflow by implementing a new system that reduced sorting time by 20%, despite the higher volume. We managed to meet all deadlines, and the accuracy of our sorting improved by 15%.
Tell me about a time when you took the initiative to improve the sorting process. What was the result?
How to Answer
- 1
Identify a specific instance where you recognized a problem in the sorting process.
- 2
Explain the steps you took to address the issue, detailing your initiative.
- 3
Share how your actions positively impacted efficiency or accuracy in sorting.
- 4
Quantify the results if possible, such as time saved or errors reduced.
- 5
Conclude with what you learned from the experience or how it contributed to your skills.
Example Answers
At my previous job, I noticed we were frequently mis-sorting packages due to unclear labeling. I created a color-coding system for different types of packages, which made it much easier for the team to sort quickly and accurately. As a result, we reduced sorting errors by 30% and speeded up delivery times by nearly an hour each day.
Describe how you manage your time effectively during a busy sorting shift.
How to Answer
- 1
Prioritize tasks based on urgency and importance.
- 2
Use a timer to stay focused on sorting sections within set intervals.
- 3
Communicate with team members to adjust workload as needed.
- 4
Regularly check your progress against goals to stay on track.
- 5
Take brief breaks to recharge and maintain efficiency.
Example Answers
During a busy sorting shift, I prioritize my tasks by starting with the items that have the closest deadlines. I set a timer for 30 minutes to focus on a specific area of sorting. If I notice I'm falling behind, I communicate with my team to help balance the workload.
Don't Just Read Machine Sorter Questions - Practice Answering Them!
Reading helps, but actual practice is what gets you hired. Our AI feedback system helps you improve your Machine Sorter interview answers in real-time.
Personalized feedback
Unlimited practice
Used by hundreds of successful candidates
Can you discuss an experience that demonstrates your reliability in performing your sorting duties?
How to Answer
- 1
Select a specific instance where you sorted items under strict conditions.
- 2
Emphasize punctuality and accuracy in your sorting process.
- 3
Mention any challenges you overcame to fulfill your sorting duties.
- 4
Include any positive outcomes from your reliable performance.
- 5
Keep the answer concise and focused on your role in the situation.
Example Answers
In my previous job, I was responsible for sorting packages for delivery. There was a time when a sudden storm caused delays, but I stayed late to ensure all packages were sorted accurately and left on time.
Technical Interview Questions
What types of sorting machines have you operated, and what specific skills did you develop while using them?
How to Answer
- 1
List specific names of sorting machines you have used.
- 2
Explain the operational process you followed for each machine.
- 3
Highlight any troubleshooting skills you gained.
- 4
Mention safety protocols you followed while operating.
- 5
Include teamwork experience if you worked with others.
Example Answers
I have operated optical sorting machines and conveyor belt sorters. While using these machines, I developed skills in calibrating the settings for different materials, troubleshooting issues like jams, and understanding safety measures, such as proper shutdown procedures.
How do you perform routine maintenance on sorting machines? Can you describe any specific procedures?
How to Answer
- 1
Start by mentioning a daily checklist for inspection.
- 2
Include specific tasks like cleaning and lubricating parts.
- 3
Discuss checking for wear and tear on belts and rollers.
- 4
Mention the importance of following manufacturer's guidelines.
- 5
Emphasize documenting maintenance activities for records.
Example Answers
I perform routine maintenance by following a daily checklist that includes inspecting all critical components. I clean and lubricate moving parts, check the belts and rollers for any signs of wear, and ensure all sensors are functioning correctly. I always refer to the manufacturer's guidelines to maintain the machine effectively and document all maintenance activities.
Don't Just Read Machine Sorter Questions - Practice Answering Them!
Reading helps, but actual practice is what gets you hired. Our AI feedback system helps you improve your Machine Sorter interview answers in real-time.
Personalized feedback
Unlimited practice
Used by hundreds of successful candidates
What steps would you take to troubleshoot a sorting machine that is not identifying items correctly?
How to Answer
- 1
Check the calibration settings of the sorting machine.
- 2
Inspect the sensors for dirt or damage that might hinder performance.
- 3
Review the software logs for error messages or anomalies.
- 4
Test the machine with different items to see if the issue persists.
- 5
Consult the machine manual for specific troubleshooting guidelines.
Example Answers
First, I would check the calibration settings of the machine to ensure it's properly set for the items being sorted. Then, I would inspect the sensors for any dirt or damage that could affect accuracy. It's also important to review the software logs for any error messages.
Are you familiar with any sorting software? How have you used technology to improve the sorting process?
How to Answer
- 1
List specific sorting software you know, like Sortly or Pick and Pack.
- 2
Describe a situation where you utilized this software to enhance efficiency.
- 3
Mention measurable outcomes, such as reduced sorting time or errors.
- 4
Highlight your adaptability to new technologies.
- 5
Express a willingness to learn more about sorting technologies.
Example Answers
I have experience using Sortly for inventory management. By integrating it into our sorting process, we reduced sorting time by 30%, allowing for faster order fulfillment.
What methods do you use to ensure that sorted items meet quality standards?
How to Answer
- 1
Understand the specific quality standards related to the sorting process
- 2
Explain how you conduct visual inspections for defects or damages
- 3
Mention the use of sorting technology or machinery for accuracy
- 4
Describe how you document and report quality issues
- 5
Discuss the importance of frequent training and team communication on quality practices
Example Answers
I ensure sorted items meet quality standards by performing visual inspections to check for any defects during the sorting process. I also leverage technology, such as optical scanners, to enhance accuracy and reduce human error.
How do you measure the efficiency of a sorting process? Can you describe any specific metrics you use?
How to Answer
- 1
Identify key metrics such as sorting speed and accuracy.
- 2
Discuss the use of throughput as a measure of items sorted per hour.
- 3
Mention error rates as an important factor for efficiency.
- 4
Consider factors like downtime and maintenance impact on efficiency.
- 5
Use real-world examples if possible to illustrate your points.
Example Answers
I measure sorting efficiency by tracking throughput, which is the number of items sorted per hour. Additionally, I monitor error rates to ensure accuracy and minimize mistakes, as high error rates can significantly decrease overall efficiency.
What experience do you have with data entry related to sorting operations?
How to Answer
- 1
Highlight specific data entry systems you've used.
- 2
Mention your attention to detail and accuracy in data handling.
- 3
Discuss any experience with sorting technologies or software.
- 4
Provide an example where you improved the data entry process.
- 5
Emphasize your ability to work under pressure and meet deadlines.
Example Answers
In my previous role, I used a data entry system called SortPro to input sorting metrics. I consistently achieved over 99% accuracy in my entries and noticed that automating some parts of the process reduced errors significantly.
Can you explain how to adjust the settings on a sorting machine to handle different materials?
How to Answer
- 1
Identify the type of material being sorted to understand its properties.
- 2
Adjust the speed and feed rate based on the material's weight and size.
- 3
Calibrate sensors for detecting different material properties, like density or color.
- 4
Set the sorting thresholds accordingly to ensure accurate separation.
- 5
Run a test cycle and monitor the results, adjusting settings as needed.
Example Answers
To adjust the settings for different materials, I first determine the material type, whether it's heavy or lightweight, and then I adjust the speed and feed rate to match. Next, I calibrate the sensors for specific properties like density, set the sorting thresholds for accuracy, and conduct a test run to fine-tune settings as necessary.
What types of sorting problems have you encountered, and how did you resolve them?
How to Answer
- 1
Identify specific sorting scenarios you've faced at work or in projects
- 2
Highlight the techniques or tools you used to tackle these problems
- 3
Emphasize your thought process and decision-making steps
- 4
Mention any collaboration with teammates for solutions
- 5
Reflect on the outcomes and what you learned from the experience
Example Answers
In my previous role, I encountered a problem sorting parcels by size. I implemented a systematic approach using automated measurements, which reduced sorting time by 20%.
What safety and quality standards do you consider critical in the sorting process?
How to Answer
- 1
Identify key safety protocols relevant to sorting environment
- 2
Mention quality standards that ensure accuracy and efficiency
- 3
Highlight the importance of training and compliance with standards
- 4
Discuss how you monitor and report issues in the sorting process
- 5
Emphasize teamwork in maintaining safety and quality
Example Answers
Safety protocols like using protective gear are critical to prevent injuries during sorting operations. For quality, I focus on consistent checks to ensure items meet specifications before they proceed further in the process.
Don't Just Read Machine Sorter Questions - Practice Answering Them!
Reading helps, but actual practice is what gets you hired. Our AI feedback system helps you improve your Machine Sorter interview answers in real-time.
Personalized feedback
Unlimited practice
Used by hundreds of successful candidates
Situational Interview Questions
If you were faced with multiple sorting tasks having tight deadlines, how would you prioritize your work?
How to Answer
- 1
Assess the deadlines of each task and identify the most urgent ones.
- 2
Evaluate the complexity and volume of each sorting task.
- 3
Communicate with your team if needed to understand priorities.
- 4
Implement a time management technique, like the Pomodoro technique, to stay focused.
- 5
Start with the task that has the highest impact or is critical for operations.
Example Answers
I would first look at the deadlines for each task and sort them based on urgency. Then, I'd evaluate the complexity, focusing on tasks that require less time and have higher impact to get them done quickly.
Imagine you and a co-worker disagree on how best to sort a specific item. How would you resolve this situation?
How to Answer
- 1
Listen carefully to your co-worker's perspective without interrupting.
- 2
Express your viewpoint clearly and respectfully.
- 3
Discuss the pros and cons of each method together.
- 4
Suggest a trial run of both sorting methods to see which is more effective.
- 5
Focus on teamwork and finding a solution that benefits the overall process.
Example Answers
I would first listen to my co-worker's approach and understand their reasoning. Then, I would share my thoughts and suggest we weigh the pros and cons together. If we still disagree, we could run a trial of both methods to see which one works best.
Don't Just Read Machine Sorter Questions - Practice Answering Them!
Reading helps, but actual practice is what gets you hired. Our AI feedback system helps you improve your Machine Sorter interview answers in real-time.
Personalized feedback
Unlimited practice
Used by hundreds of successful candidates
If you notice that a sorting machine is running slower than normal, what steps would you take to resolve it?
How to Answer
- 1
Check the machine's display for error messages or alerts.
- 2
Inspect the machine for any visible obstructions or jams.
- 3
Verify that all parts are properly lubricated and maintained.
- 4
Evaluate the input material for inconsistencies that may affect performance.
- 5
Report persistent issues to a technician or supervisor for further assistance.
Example Answers
First, I would check the machine's display for any error messages. Then, I would visually inspect the machine for obstructions or jams. If nothing is found, I would ensure that the machine's parts are properly lubricated.
You're running the sorting machine and your team is falling behind. What would you do to get everyone back on track?
How to Answer
- 1
Evaluate the current workflow and identify bottlenecks.
- 2
Communicate with the team to understand challenges they're facing.
- 3
Redistribute tasks based on team members' strengths.
- 4
Implement short breaks to maintain focus and energy.
- 5
Set clear, achievable goals to track improvement.
Example Answers
I would first analyze the workflow to find where delays are happening. Then, I would talk to my team to see what problems they are encountering and help them overcome those hurdles. I might also adjust roles to ensure everyone is working in areas where they can be most efficient. Finally, I would set a short-term goal for the team to boost morale and focus efforts.
You see a colleague not following safety protocols while operating the sorter. How would you approach the situation?
How to Answer
- 1
Observe the situation to ensure you understand what is happening.
- 2
Approach your colleague in a calm and non-confrontational manner.
- 3
Express concern for their safety and the importance of protocols.
- 4
Encourage them to follow the safety procedures.
- 5
If the behavior continues, report it to a supervisor.
Example Answers
I would first make sure to observe the situation clearly, then calmly approach my colleague and say, 'I noticed you're not following the safety protocols, and I’m concerned for your safety. Can we talk about the right procedures together?'
What would you do if there was an emergency while sorting materials and evacuation was necessary?
How to Answer
- 1
Stay calm and quickly assess the situation.
- 2
Follow the established emergency protocols immediately.
- 3
Communicate clearly with team members about the situation.
- 4
Ensure everyone knows the exit routes and safe places to gather.
- 5
Report to a supervisor after evacuation for accountability.
Example Answers
In an emergency, I would remain calm and quickly evaluate what happened. I would follow the evacuation plan we have in place and make sure to communicate to my co-workers that it's time to leave and point them to the nearest exits.
If a client reports a problem with sorted items, how would you handle the situation?
How to Answer
- 1
Listen carefully to the client's concerns without interrupting.
- 2
Ask for specific details about the problem to understand the issue.
- 3
Apologize for the inconvenience and reassure them you will find a solution.
- 4
Take notes and communicate any immediate actions you will take.
- 5
Follow up with the client after resolving the issue to ensure satisfaction.
Example Answers
I would listen to the client’s issue thoroughly and ask them to clarify the specific details about the sorted items that are problematic. Then, I would apologize for the trouble caused and assure them that I will investigate the issue. I would take notes on what they said and follow up with them once I have resolved the problem.
If you received negative feedback on your sorting performance, how would you respond and improve?
How to Answer
- 1
Stay calm and listen to the feedback carefully.
- 2
Ask for specific examples of where you fell short.
- 3
Develop an action plan to address the issues mentioned.
- 4
Seek assistance or training if needed to improve skills.
- 5
Follow up after implementing changes to demonstrate improvement.
Example Answers
I would first listen to the feedback without getting defensive. Then, I would ask for specific instances of my sorting errors. Based on that, I would create a plan to improve my speed and accuracy, perhaps by practicing with a focus on those areas. I would also check in with my supervisor after a few weeks to show the progress I've made.
If tasked with organizing a sorting project for a new product line, what steps would you take to plan?
How to Answer
- 1
Identify the product characteristics and sorting requirements
- 2
Determine the sorting capacity and resources available
- 3
Create a layout plan for the sorting process
- 4
Develop a timeline for implementation and training
- 5
Review and adjust the plan based on feedback from stakeholders
Example Answers
First, I would gather all the details about the new product line, including size, weight, and materials. Next, I'd assess our sorting capacity and determine the resources we need. Then, I'd design an efficient layout for the sorting area and establish a timeline for training staff before starting the project.
Machine Sorter Position Details
Recommended Job Boards
CareerBuilder
www.careerbuilder.com/jobs-sorter-machine-operatorThese job boards are ranked by relevance for this position.
Related Positions
- Ball Sorter
- Paper Sorter
- Machine Folder
- Bag Machine Operator
- Machine Printer
- Machine Puller
- Machine Hand
- Machine Presser
- Sifter
- Turning Machine Operator
Similar positions you might be interested in.
Ace Your Next Interview!
Practice with AI feedback & get hired faster
Personalized feedback
Used by hundreds of successful candidates
Ace Your Next Interview!
Practice with AI feedback & get hired faster
Personalized feedback
Used by hundreds of successful candidates