Top 31 Machine Folder Interview Questions and Answers [Updated 2025]
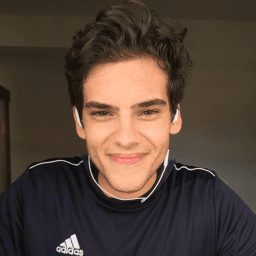
Andre Mendes
•
March 30, 2025
Preparing for a 'Machine Folder' interview can be daunting, but having the right insights makes all the difference. In this blog post, we've compiled the most common interview questions for this role, complete with example answers and expert tips to help you respond effectively. Dive in to boost your confidence and ensure you're well-equipped to impress your potential employers.
Download Machine Folder Interview Questions in PDF
To make your preparation even more convenient, we've compiled all these top Machine Folderinterview questions and answers into a handy PDF.
Click the button below to download the PDF and have easy access to these essential questions anytime, anywhere:
List of Machine Folder Interview Questions
Behavioral Interview Questions
Can you describe a time when you worked as part of a team to improve the efficiency of a machine folder?
How to Answer
- 1
Select a specific project or initiative where teamwork was key.
- 2
Explain your role and contributions clearly.
- 3
Highlight the steps you took to identify inefficiencies.
- 4
Describe the methods or solutions implemented.
- 5
Quantify the improvement achieved, if possible.
Example Answers
In my previous job, our team noticed that the machine folder was frequently misfeeding paper. I suggested we analyze the feeding mechanism, and we discovered a calibration issue. I worked with a technician to recalibrate the machine, which reduced misfeeds by 30%.
Don't Just Read Machine Folder Questions - Practice Answering Them!
Reading helps, but actual practice is what gets you hired. Our AI feedback system helps you improve your Machine Folder interview answers in real-time.
Personalized feedback
Unlimited practice
Used by hundreds of successful candidates
Tell me about a time you had to manage multiple tasks in a fast-paced environment while operating a machine folder.
How to Answer
- 1
Describe a specific situation where you operated a machine folder.
- 2
Explain the multiple tasks you had to manage and the pace of the environment.
- 3
Highlight your prioritization skills and how you ensured efficiency.
- 4
Mention any teamwork or communication aspects involved.
- 5
Conclude with the outcome and what you learned from the experience.
Example Answers
In my previous role at PrintCo, I operated a machine folder while handling several orders simultaneously. I had to prioritize the high-volume jobs and communicate with my team about deadlines. By staying organized and using a checklist, I ensured all tasks were completed on time, leading to a 20% increase in production efficiency.
Describe a situation where you had to adapt to a significant change in machine operation or folding processes.
How to Answer
- 1
Identify a specific instance of change in machine operation.
- 2
Explain your initial reaction to the change and why it was significant.
- 3
Describe the steps you took to adapt to the new processes.
- 4
Highlight the outcome of your adaptation and any improvements made.
- 5
Mention any skills you utilized or developed during this process.
Example Answers
At my previous job, we upgraded to a new folding machine that required different settings. Initially, I was overwhelmed, but I took the time to study the new machine manual. I then collaborated with the technical team to understand the new features. As a result, I improved my setup time by 20% and reduced paper jams significantly in the following weeks.
Have you ever had to train new employees on using a machine folder? How did you approach this task?
How to Answer
- 1
Identify the key features of the machine folder that need to be explained.
- 2
Demonstrate the operation of the machine folder step-by-step.
- 3
Encourage hands-on practice with supervision.
- 4
Provide written materials or guides for reference.
- 5
Ask questions to assess understanding and clarify doubts.
Example Answers
Yes, I trained new employees on the machine folder. I first highlighted key features and functions. Then, I demonstrated the machine in action before having them try it under my supervision. I provided a manual for reference and made sure to check their understanding by asking questions.
Can you provide an example of a time your attention to detail made a significant impact on the production process?
How to Answer
- 1
Think of a specific situation where your attention to detail was crucial
- 2
Mention the problem that was avoided or solved due to your attention
- 3
Quantify the impact if possible, such as increased efficiency or reduced errors
- 4
Use the STAR method: Situation, Task, Action, Result
- 5
Be concise but clear in explaining your role and the outcome
Example Answers
In my previous role, I noticed a discrepancy in the quality control checklist for machine setup. I flagged it before production started, which prevented a batch of defective products. This attention helped us maintain our quality standards and saved the company about $5,000 in rework costs.
Describe a time when you took the initiative to implement a new process related to machine folding.
How to Answer
- 1
Identify a specific problem with the current machine folding process.
- 2
Explain the new process you proposed and implemented.
- 3
Highlight the benefits or improvements achieved from the new process.
- 4
Mention how you involved your team or got buy-in from management.
- 5
Use metrics or clear outcomes to demonstrate success.
Example Answers
In my last role, I noticed that our machine folding process was causing frequent jams. I proposed a new workflow that included regular maintenance checks and staff training. As a result, we reduced machine downtime by 30% and improved our output efficiency.
Have you ever identified a training need within your team related to machine folding? How did you address it?
How to Answer
- 1
Think of a specific instance where you noticed a skill gap.
- 2
Describe how you assessed the need for training among team members.
- 3
Explain the steps you took to develop or implement the training.
- 4
Include how you measured the effectiveness of the training.
- 5
Mention any feedback received from team members after the training.
Example Answers
In my previous role, I noticed that new team members struggled with the machine folding techniques, leading to increased errors. I conducted a skills assessment and organized a hands-on workshop about proper machine settings and techniques. After the session, I gathered feedback and saw a 30% reduction in errors over the next month.
What do you consider your greatest success in your previous work as a machine folder operator?
How to Answer
- 1
Identify a specific success that demonstrates your skills
- 2
Quantify your success with metrics or outcomes
- 3
Explain the challenges you faced and how you overcame them
- 4
Link your success to the needs of the potential employer
- 5
Keep the response concise and focused on results
Example Answers
My greatest success was reducing the folder setup time by 30%, which improved our production efficiency. I identified bottlenecks in the process and implemented a new checklist system that streamlined our workflow.
Don't Just Read Machine Folder Questions - Practice Answering Them!
Reading helps, but actual practice is what gets you hired. Our AI feedback system helps you improve your Machine Folder interview answers in real-time.
Personalized feedback
Unlimited practice
Used by hundreds of successful candidates
Technical Interview Questions
What are the key components of a machine folder that you are familiar with?
How to Answer
- 1
Identify the main parts of a machine folder, such as rollers, fold plates, and feeder mechanisms.
- 2
Discuss the function of each component briefly.
- 3
Mention how these components interact to achieve efficient paper folding.
- 4
If applicable, refer to specific types of machine folders you have used or know about.
- 5
Relate your knowledge to practical applications in a folding operation.
Example Answers
A machine folder typically consists of rollers, which help control the paper feed, fold plates that dictate the type of folds produced, and the feeder mechanism that ensures the paper is fed accurately into the machine.
How do you perform routine maintenance on a machine folder to ensure it operates efficiently?
How to Answer
- 1
Regularly check and tighten all mechanical components to prevent vibrations and misalignments
- 2
Lubricate moving parts based on the manufacturer's recommendations to reduce wear
- 3
Inspect the folder for signs of wear, such as torn belts or damaged rollers, and replace as needed
- 4
Clean the machine thoroughly to prevent dust and debris from affecting performance
- 5
Document maintenance activities to track issues and ensure nothing is overlooked
Example Answers
I perform routine maintenance by checking and tightening all mechanical components regularly. I also lubricate the moving parts as per the manufacturer's instructions and inspect for any signs of wear.
Don't Just Read Machine Folder Questions - Practice Answering Them!
Reading helps, but actual practice is what gets you hired. Our AI feedback system helps you improve your Machine Folder interview answers in real-time.
Personalized feedback
Unlimited practice
Used by hundreds of successful candidates
What steps would you take to troubleshoot a machine folder that is not folding correctly?
How to Answer
- 1
Check for any visible jams or obstructions in the feed area.
- 2
Verify the folder settings and ensure they are correctly configured.
- 3
Inspect the folding plates for wear or misalignment.
- 4
Test the machine with different paper weights to see if issues persist.
- 5
Consult the machine's manual or troubleshooting guide for specific error codes.
Example Answers
First, I would look for paper jams or any foreign objects that might be blocking the feed. Then, I'd check the machine settings to ensure they match the type of paper being used.
Can you explain how to adjust the settings on a machine folder for different paper types?
How to Answer
- 1
Identify the type of paper and its thickness.
- 2
Locate the adjustable settings on the machine folder.
- 3
Change the folding guides according to paper size.
- 4
Adjust tension and speed settings for different paper types.
- 5
Perform a test fold to ensure settings are correct.
Example Answers
To adjust the settings for different paper types, first identify the paper's thickness. Then, I locate the adjustable folding guides and set them based on the paper size. I also make sure to adjust the tension and speed on the machine, and finally, I run a test folder to check the results.
What safety protocols do you follow when operating a machine folder?
How to Answer
- 1
Always wear appropriate personal protective equipment such as gloves and safety goggles.
- 2
Ensure all safety guards and emergency stop buttons are functional before use.
- 3
Never bypass safety mechanisms during operation.
- 4
Keep hands and other body parts clear of moving parts and folding mechanisms.
- 5
Regularly attend safety training and refreshers to stay updated on best practices.
Example Answers
I always wear safety goggles and gloves when operating the machine folder, and I check that all emergency stops are working before starting.
What machine folder software or controls have you previously worked with?
How to Answer
- 1
List specific software or controls you have experience with
- 2
Mention any relevant certifications or training
- 3
Discuss the context in which you used the software, like projects or tasks
- 4
Highlight any notable achievements with the software
- 5
Be prepared to explain technical aspects if asked
Example Answers
I have worked with the M-Folder Control System for the past three years in my previous job at ABC Corp. I led a project that increased efficiency by 20% using its advanced features.
How do you test the output of a machine folder to ensure it meets specifications?
How to Answer
- 1
Define the specifications for the folded output before testing.
- 2
Use measurement tools to check dimensions and consistency.
- 3
Conduct visual inspections for quality and alignment.
- 4
Perform output tests by running sample batches.
- 5
Document findings and compare them to specifications.
Example Answers
To test the output of a machine folder, I first check the specifications and measure the folds using calipers to ensure the proper dimensions. Then, I visually inspect the output for alignment and quality, and I run a few sample batches to see if they consistently meet the criteria.
What recent advancements in folding technology are you aware of that could benefit our operations?
How to Answer
- 1
Research current trends in folding technology before the interview
- 2
Mention specific advancements like robotics, AI, or smart folding equipment
- 3
Relate the advancements to operational efficiency and cost savings
- 4
Consider how these technologies improve speed and reduce errors
- 5
Be prepared to discuss practical examples or case studies of these technologies in use
Example Answers
One recent advancement in folding technology is the use of AI-powered folding machines that can adapt to different fabric types. This allows for greater efficiency and reduces the need for manual adjustments, potentially saving labor costs and time in our operations.
What different types of paper or materials have you worked with on a machine folder?
How to Answer
- 1
Think of various paper weights and types you've handled.
- 2
Include specific examples like glossy, matte, or cardstock.
- 3
Mention any specialty materials like recycled paper or textured stock.
- 4
Share experiences of adjusting folding techniques for different materials.
- 5
Highlight familiarity with handling different thicknesses and finishes.
Example Answers
I have worked with various paper types including lightweight text paper, cardstock for brochures, and glossy paper for promotional materials. Each required different folding settings.
What quality standards do you follow to ensure the output from the machine folder meets customer expectations?
How to Answer
- 1
Identify specific quality standards relevant to machine folding.
- 2
Explain your daily checks and procedures for maintaining quality.
- 3
Discuss how you gather and incorporate customer feedback.
- 4
Mention the importance of training and teamwork in quality assurance.
- 5
Highlight your commitment to continuous improvement based on performance metrics.
Example Answers
I ensure that my outputs meet quality standards by using a combination of regular machine calibrations, strict adherence to production guidelines, and performing detailed quality checks after each run to identify any issues early.
Don't Just Read Machine Folder Questions - Practice Answering Them!
Reading helps, but actual practice is what gets you hired. Our AI feedback system helps you improve your Machine Folder interview answers in real-time.
Personalized feedback
Unlimited practice
Used by hundreds of successful candidates
How do you interpret technical specifications for the folding processes?
How to Answer
- 1
Review the folding process step-by-step.
- 2
Identify key terms and their meanings.
- 3
Cross-reference specifications with folding machine capabilities.
- 4
Visualize the end product to ensure accuracy.
- 5
Consult with team members for clarifications if needed.
Example Answers
I break down the specifications into distinct steps, focusing on key terms like crease lines and fold types. Then, I match these to the machine settings to ensure everything aligns with our capabilities.
Situational Interview Questions
If a colleague disagrees with your method of operating a machine folder, how would you handle that situation?
How to Answer
- 1
Listen to their concerns without interrupting.
- 2
Ask for specific examples of what they disagree with.
- 3
Explain your reasoning clearly and provide supporting evidence.
- 4
Look for common ground or compromise if possible.
- 5
Maintain professionalism and focus on the best outcome for the team.
Example Answers
I would listen carefully to my colleague's concerns and ask them to clarify their points. Then, I would explain my approach and share why I think it's effective. If we find a compromise that satisfies both of us, that would be ideal.
Imagine the machine folder has a jam during peak hours. How would you prioritize your actions?
How to Answer
- 1
Assess the situation quickly to understand the severity of the jam.
- 2
Communicate with team members to inform them of the issue and the potential impact on production.
- 3
Stop the machine safely following the standard operating procedures.
- 4
Clear the jam efficiently while ensuring no damage to the machine.
- 5
Restart the machine and monitor its operation for any further issues.
Example Answers
First, I would quickly check the machine to assess the type and severity of the jam. Then, I would notify my supervisor and the team to let them know about the delay. After ensuring it's safe, I'd stop the machine, clear the jam carefully, and then restart it, monitoring it closely for any additional problems.
Don't Just Read Machine Folder Questions - Practice Answering Them!
Reading helps, but actual practice is what gets you hired. Our AI feedback system helps you improve your Machine Folder interview answers in real-time.
Personalized feedback
Unlimited practice
Used by hundreds of successful candidates
If a customer is unhappy with the finished product folded by the machine folder, how would you address their concerns?
How to Answer
- 1
Listen carefully to the customer's complaint without interrupting
- 2
Apologize for their inconvenience to show empathy
- 3
Ask specific questions to understand their issue better
- 4
Explain how you will address the problem and seek a resolution
- 5
Follow up to ensure their satisfaction after the resolution
Example Answers
I would first listen to the customer's concerns fully. Then, I would apologize for the trouble they've experienced. Next, I'd ask them specific questions to get details about what went wrong and how we can fix it. Finally, I would explain the steps I would take to correct the issue and follow up with them afterwards to make sure they're satisfied.
If you notice one of your team members struggling to operate their machine folder, how would you assist them?
How to Answer
- 1
Observe the team member's operation to identify specific issues
- 2
Ask them questions to understand their struggles
- 3
Offer clear, step-by-step assistance
- 4
Demonstrate the correct operation if necessary
- 5
Encourage them and provide positive feedback
Example Answers
I would first observe how they are using the machine folder and identify the specific problem. Then, I would ask them what part they find challenging and offer to show them how to do it step by step. If they’re still unsure, I would demonstrate again and encourage them to practice with my support until they feel more confident.
What would you do if you noticed that the quality of folding has decreased significantly during a production run?
How to Answer
- 1
Assess the current situation immediately and identify specific issues causing the decline.
- 2
Check machine settings and ensure they are properly calibrated and functioning.
- 3
Review material quality and stock to determine if any changes have occurred.
- 4
Conduct a quick inspection of the work area to see if any disruptions are affecting performance.
- 5
Communicate with team members about the issue and consider collaborative troubleshooting.
Example Answers
I would first stop the machine to prevent further misfolds and check the settings to ensure everything is correct. Then, I would inspect the materials being used for any inconsistencies.
If you were tasked with improving the folding speed of a machine folder, what steps would you take?
How to Answer
- 1
Analyze the current folding process to identify bottlenecks
- 2
Evaluate the machine’s components for wear and efficiency
- 3
Experiment with different folding patterns and speeds
- 4
Implement automation where feasible to reduce manual adjustments
- 5
Train operators on optimal settings and techniques for faster folds
Example Answers
First, I would assess the entire folding process for any bottlenecks that slow down production. This could involve observing the machine in action and analyzing its cycle times. Then, I'd check for any worn-out parts and replace them to improve efficiency.
If a critical error occurs during a machine folding task that affects productivity, how would you manage it?
How to Answer
- 1
Assess the error immediately and identify its cause
- 2
Communicate the issue to your team and supervisors promptly
- 3
Implement corrective measures to rectify the error swiftly
- 4
Document the incident and the resolution process for future reference
- 5
Review and adjust workflow processes to prevent similar issues
Example Answers
First, I would quickly assess the situation to identify the root cause of the critical error. Then, I would inform my team and supervisors to ensure everyone is aware. After that, I would implement a solution to fix the issue and minimize downtime. I would also document the incident for future training and review processes to avoid it happening again.
If there is a malfunction with the machine folder that poses a safety risk, what would be your immediate response?
How to Answer
- 1
Assess the situation quickly but carefully to understand the risk level
- 2
Immediately stop the machine to prevent any accidents or injuries
- 3
Alert co-workers in the area about the malfunction and potential danger
- 4
Notify the supervisor or maintenance team about the issue
- 5
Document the incident as per the safety protocols for future reference
Example Answers
I would quickly assess the situation and if the machine is still running, I would stop it immediately to ensure safety.
During a busy season, how would you ensure your machine folder team meets production goals?
How to Answer
- 1
Prioritize tasks based on deadlines and importance
- 2
Communicate clear expectations to the team
- 3
Monitor progress regularly and adjust plans if needed
- 4
Encourage teamwork and support among members
- 5
Provide training or resources to tackle increased workload
Example Answers
I would start by prioritizing tasks based on our deadlines and the importance of each order. Then, I would hold a team meeting to clearly communicate our goals and expectations during the busy season.
If you have to collaborate with the maintenance team to fix a machine folder issue, how would you communicate your needs?
How to Answer
- 1
Be clear and specific about the issue including what you observe.
- 2
Use technical terms appropriately while avoiding jargon where possible.
- 3
Check if the maintenance team has all the necessary information to troubleshoot effectively.
- 4
Suggest possible causes you have identified based on your experience.
- 5
Establish a cooperative tone and be open to their suggestions.
Example Answers
I would explain the specific problem I've noticed with the machine folder, detailing the symptoms and any error codes. I would also share any relevant data or logs to help them understand the issue better.
Don't Just Read Machine Folder Questions - Practice Answering Them!
Reading helps, but actual practice is what gets you hired. Our AI feedback system helps you improve your Machine Folder interview answers in real-time.
Personalized feedback
Unlimited practice
Used by hundreds of successful candidates
Machine Folder Position Details
Recommended Job Boards
CareerBuilder
www.careerbuilder.com/jobs/folder-operatorZipRecruiter
www.ziprecruiter.com/Jobs/Folder-OperatorThese job boards are ranked by relevance for this position.
Related Positions
- Hand Folder
- Garment Folder
- Machine Hand
- Machine Puller
- Bag Machine Operator
- Machine Sorter
- Screen Maker
- Machine Printer
- Frame Hand
- Table Worker
Similar positions you might be interested in.
Ace Your Next Interview!
Practice with AI feedback & get hired faster
Personalized feedback
Used by hundreds of successful candidates
Ace Your Next Interview!
Practice with AI feedback & get hired faster
Personalized feedback
Used by hundreds of successful candidates