Top 31 Maintenance Manager Interview Questions and Answers [Updated 2025]
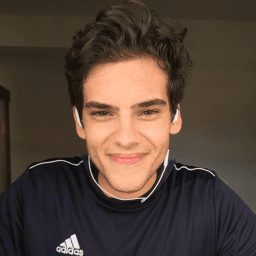
Andre Mendes
•
March 30, 2025
Navigating a Maintenance Manager interview can be daunting, but preparation is key to success. In this post, we delve into the most common interview questions for this critical role, offering insightful example answers and practical tips to help you respond confidently and effectively. Whether you're a seasoned professional or stepping into the position for the first time, this guide is designed to enhance your interview readiness.
Get Maintenance Manager Interview Questions PDF
Get instant access to all these Maintenance Manager interview questions and expert answers in a convenient PDF format. Perfect for offline study and interview preparation.
Enter your email below to receive the PDF instantly: