Top 31 Maintenance Planner Interview Questions and Answers [Updated 2025]
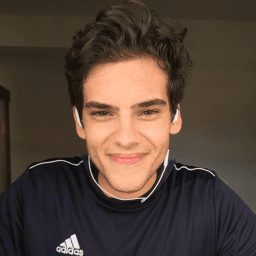
Andre Mendes
•
March 30, 2025
Are you preparing for a Maintenance Planner interview and want to stand out from the competition? Our latest blog post compiles the most common interview questions for this pivotal role, complete with example answers and expert tips to craft your responses effectively. Dive in to enhance your interview skills and boost your confidence as you navigate your career journey in maintenance planning.
Download Maintenance Planner Interview Questions in PDF
To make your preparation even more convenient, we've compiled all these top Maintenance Plannerinterview questions and answers into a handy PDF.
Click the button below to download the PDF and have easy access to these essential questions anytime, anywhere:
List of Maintenance Planner Interview Questions
Situational Interview Questions
How would you approach training new maintenance staff on existing systems and processes?
How to Answer
- 1
Start with a structured orientation to introduce the maintenance team and organization.
- 2
Utilize a hands-on training approach to familiarize new staff with tools and equipment.
- 3
Provide documented procedures and systems manuals for reference.
- 4
Encourage mentorship by pairing new staff with experienced employees.
- 5
Schedule regular check-ins to assess progress and address questions.
Example Answers
I would begin with an orientation session to introduce the new staff to our team and safety protocols. Then, I'd organize hands-on training sessions where they can learn by doing, alongside documented procedures that they can refer to. Pairing them with a mentor would also help them feel supported.
Imagine you receive a last-minute maintenance request that conflicts with your planned schedule. How would you handle it?
How to Answer
- 1
Assess the urgency of the maintenance request quickly
- 2
Communicate with your team about the conflict
- 3
Evaluate options to adjust the schedule
- 4
Prioritize tasks based on safety and operational impact
- 5
Document the changes made for future reference
Example Answers
I would first assess whether the last-minute request is urgent. If it is, I would communicate with my team to see if there are any non-essential tasks we can postpone. Then, I would adjust the schedule accordingly while ensuring that safety and operations are prioritized.
Don't Just Read Maintenance Planner Questions - Practice Answering Them!
Reading helps, but actual practice is what gets you hired. Our AI feedback system helps you improve your Maintenance Planner interview answers in real-time.
Personalized feedback
Unlimited practice
Used by hundreds of successful candidates
Suppose the maintenance team is short-staffed due to unexpected absences. What adjustments would you make?
How to Answer
- 1
Assess the current workload and prioritize maintenance tasks.
- 2
Communicate with the team to understand skill sets and availability.
- 3
Reallocate resources from less urgent projects to cover critical maintenance.
- 4
Implement a temporary on-call schedule to manage emergencies.
- 5
Document the adjustments for future reference and team learning.
Example Answers
First, I would review the maintenance schedule and prioritize urgent tasks. Next, I would talk to the team to see who is available and their skill sets. Then, I would reassign some of the less critical tasks to ensure that vital maintenance is completed on time.
If you notice a potential safety hazard during a routine inspection, what steps would you take?
How to Answer
- 1
Immediately report the hazard to your supervisor or safety officer.
- 2
Document the hazard with specific details including location and nature.
- 3
Ensure the area is secured to prevent accidents, if possible.
- 4
Follow up to verify that corrective actions are taken.
- 5
Review safety protocols and suggest improvements based on your findings.
Example Answers
If I notice a potential safety hazard, I would first report it to my supervisor to ensure they are aware. Then, I would document the hazard accurately so that we have a record. I'd secure the area to prevent any accidents while waiting for the issue to be addressed.
You need to inform your team about a change in maintenance policy. How would you communicate this?
How to Answer
- 1
Identify the key message of the policy change clearly.
- 2
Choose an appropriate communication method, like a team meeting or email.
- 3
Be transparent about the reasons behind the change.
- 4
Encourage questions and feedback from the team.
- 5
Follow up with written documentation of the change.
Example Answers
I would prepare a clear summary of the policy change and hold a team meeting to communicate it. During the meeting, I'd explain the reasons for the change and encourage my team to ask questions.
In the event of a critical equipment failure, how would you coordinate the emergency response?
How to Answer
- 1
Immediately assess the situation to understand the scope of the failure
- 2
Ensure safety protocols are followed to protect personnel
- 3
Communicate with the team and relevant stakeholders clearly and quickly
- 4
Mobilize necessary resources and personnel for the response
- 5
Document the incident and response actions for future review
Example Answers
In case of critical equipment failure, I would first assess the situation to understand the extent of the issue. Then, I'd ensure all safety protocols are in place to protect our team. I'd communicate promptly with relevant stakeholders to inform them of the failure and mobilize our maintenance team to respond quickly.
If you needed to collaborate with other departments for a large maintenance project, what steps would you take to ensure effective cooperation?
How to Answer
- 1
Identify key stakeholders from each department early on.
- 2
Schedule a kickoff meeting to align everyone on goals and timelines.
- 3
Establish clear communication channels and protocols for updates.
- 4
Define roles and responsibilities for each department's involvement.
- 5
Set regular check-ins to monitor progress and address any issues.
Example Answers
First, I would identify the key stakeholders involved in the maintenance project. Then, I would organize a kickoff meeting to ensure everyone understands the objectives and timelines. It's important to set up clear communication channels like email updates and a shared project management tool. I would also define specific roles for each department and hold regular check-ins to track progress.
How would you handle negative feedback from a team member regarding a maintenance plan you developed?
How to Answer
- 1
Listen actively to the team member's concerns without interrupting.
- 2
Acknowledge their feedback and express appreciation for their perspective.
- 3
Ask clarifying questions to understand the specifics of their criticism.
- 4
Discuss potential revisions to the maintenance plan collaboratively.
- 5
Follow up after implementation to see if improvements were effective.
Example Answers
I would first listen carefully to the team member's feedback, making sure to understand their concerns fully. I would thank them for bringing it up and then discuss how we can adjust the plan together to address their points.
If you discover that your maintenance processes are not as efficient as they could be, what steps would you take to improve them?
How to Answer
- 1
Conduct a thorough analysis of the current maintenance processes.
- 2
Identify key performance indicators that are not being met.
- 3
Involve the maintenance team in discussing inefficiencies.
- 4
Research and implement best practices or new technologies.
- 5
Monitor the improvements and adjust strategies as necessary.
Example Answers
First, I would analyze the current maintenance processes to pinpoint inefficiencies. Then, I would gather feedback from the maintenance team to understand their challenges. Based on this information, I would implement best practices from industry standards and track the results to ensure improvements.
How would you manage a situation where a facility's operations are disrupted due to a maintenance delay?
How to Answer
- 1
Assess the impact of the delay on operations immediately.
- 2
Communicate clearly with stakeholders about the situation.
- 3
Prioritize tasks to minimize downtime and plan quick fixes.
- 4
Coordinate with the maintenance team to expedite work where possible.
- 5
Implement preventive measures to avoid similar delays in the future.
Example Answers
First, I'd assess how the delay impacts operations and communicate that to relevant stakeholders. Then, I'd prioritize the most critical tasks and work with the maintenance team to expedite repairs.
Don't Just Read Maintenance Planner Questions - Practice Answering Them!
Reading helps, but actual practice is what gets you hired. Our AI feedback system helps you improve your Maintenance Planner interview answers in real-time.
Personalized feedback
Unlimited practice
Used by hundreds of successful candidates
Behavioral Interview Questions
Can you describe a time when you had to work closely with a maintenance team to complete a project?
How to Answer
- 1
Choose a specific project that required collaboration with the maintenance team.
- 2
Highlight your role and responsibilities during the project.
- 3
Mention any challenges faced and how they were overcome.
- 4
Discuss the outcome and the impact on operations or maintenance goals.
- 5
Keep it concise and focus on teamwork and communication.
Example Answers
In my previous role at XYZ Company, we had a project to upgrade our HVAC systems. I coordinated with the maintenance team to schedule downtime, ensuring minimal disruption. One challenge was syncing work schedules, but using a shared calendar helped us communicate better. The project was completed ahead of schedule, which improved our energy efficiency by 15%.
Tell me about a challenging maintenance issue you faced and how you resolved it.
How to Answer
- 1
Choose a specific maintenance issue that had significant impact
- 2
Explain the steps you took to identify the problem
- 3
Detail the solution you implemented and the reasoning behind it
- 4
Discuss the outcome and what you learned from the experience
- 5
Highlight any teamwork or communication involved in the resolution
Example Answers
In my previous role, we faced a recurring issue with a critical piece of machinery failing during production. I conducted a thorough analysis and discovered that the root cause was improper lubrication. I implemented a new lubrication schedule and trained the staff on proper maintenance procedures. As a result, machine downtime was reduced by 30%.
Don't Just Read Maintenance Planner Questions - Practice Answering Them!
Reading helps, but actual practice is what gets you hired. Our AI feedback system helps you improve your Maintenance Planner interview answers in real-time.
Personalized feedback
Unlimited practice
Used by hundreds of successful candidates
Describe an instance when you had to prioritize multiple maintenance tasks. What was your approach?
How to Answer
- 1
List the tasks you faced and their urgency.
- 2
Explain how you assessed the impact of each task.
- 3
Describe the criteria you used for prioritization.
- 4
Share the method you used to complete the tasks.
- 5
Briefly mention the outcome of your prioritization.
Example Answers
In my previous role, I had three tasks: an urgent repair for a conveyor belt, routine maintenance on a generator, and a planned inspection on HVAC. I prioritized the conveyor belt repair as it was critical for production, assessed that the generator maintenance could be safely delayed, and scheduled the inspection for after the urgent tasks. This ensured minimal downtime and all tasks were completed efficiently.
Give an example of how you communicated maintenance plans to non-technical stakeholders.
How to Answer
- 1
Use clear language to explain technical details
- 2
Focus on the benefits and impacts for stakeholders
- 3
Simplify the information without losing essential details
- 4
Use visuals or summaries if possible
- 5
Engage stakeholders by asking for their input or feedback
Example Answers
In my previous role, I created a simple presentation that outlined our maintenance plans for the upcoming quarter. I used charts to illustrate equipment downtime and how our plans would reduce it, which resonated with the sales team because they understood the impact on revenue.
Have you ever led a maintenance project? What were the challenges and outcomes?
How to Answer
- 1
Start with a brief overview of the project you led
- 2
Mention specific challenges faced during the project
- 3
Highlight how you overcame these challenges
- 4
Discuss the outcome and its impact on the team or organization
- 5
Keep your answer focused and relevant to the maintenance role
Example Answers
I led a project to upgrade our HVAC systems. A major challenge was coordinating with multiple vendors, which caused delays. I resolved this by setting up regular check-ins with all parties involved. The outcome was a timely upgrade that improved energy efficiency by 20%.
Describe a situation where there was a disagreement in your team regarding maintenance priorities. How did you handle it?
How to Answer
- 1
Identify the disagreement clearly.
- 2
Explain the factors that caused the differing priorities.
- 3
Describe how you facilitated communication within the team.
- 4
Highlight how you reached a resolution or compromise.
- 5
Share any positive outcomes resulting from the situation.
Example Answers
In my last role, our team disagreed on whether to prioritize a critical equipment breakdown or a scheduled maintenance task. I organized a meeting where team members could express their views and concerns. After discussing the potential impacts and costs, we decided to address the breakdown first, which minimized downtime and later completed the scheduled task seamlessly.
Have you ever introduced a new process or technology in maintenance planning? What was the outcome?
How to Answer
- 1
Choose a specific process or technology you implemented.
- 2
Clearly describe the situation before the change.
- 3
Explain how you implemented the new process or technology.
- 4
Share measurable outcomes or improvements.
- 5
Reflect on any challenges faced and how you overcame them.
Example Answers
In my previous role, I introduced a computerized maintenance management system (CMMS) that streamlined work orders. Before this, we used paper logs, which caused delays. After implementing the CMMS, we reduced response time by 30% and improved tracking of maintenance tasks.
Describe a time when you had to adapt your maintenance planning quickly due to unforeseen circumstances.
How to Answer
- 1
Briefly explain the situation and the unforeseen circumstance.
- 2
Describe the immediate steps you took to assess the impact.
- 3
Discuss how you communicated changes to the team and stakeholders.
- 4
Highlight the outcome and what you learned from the experience.
- 5
Keep the focus on your quick thinking and problem-solving skills.
Example Answers
In my previous role, a critical machine broke down unexpectedly during production. I quickly assessed the downtime impact and reshuffled the maintenance schedule to prioritize the repair. I communicated with my team and production management to adjust the workload accordingly. As a result, we minimized production loss and repaired the machine within a few hours. I learned the importance of flexibility and communication in maintenance planning.
What methods do you use to ensure your team stays updated on maintenance best practices?
How to Answer
- 1
Encourage regular training sessions on the latest maintenance techniques
- 2
Utilize a shared digital platform for maintenance resources and documentation
- 3
Implement a monthly team meeting to discuss recent developments and share insights
- 4
Encourage team members to attend workshops and conferences
- 5
Promote a culture of continuous improvement where team members share their learnings
Example Answers
I organize quarterly training sessions focused on the latest maintenance techniques and tools. We also have a shared digital platform where updates and best practices are documented for everyone to access.
Don't Just Read Maintenance Planner Questions - Practice Answering Them!
Reading helps, but actual practice is what gets you hired. Our AI feedback system helps you improve your Maintenance Planner interview answers in real-time.
Personalized feedback
Unlimited practice
Used by hundreds of successful candidates
Technical Interview Questions
What maintenance management software are you familiar with, and what specific features have you utilized?
How to Answer
- 1
Identify the maintenance software you have used.
- 2
Mention specific features you are comfortable with.
- 3
Connect your experience with the needs of the role.
- 4
Be honest about your level of proficiency.
- 5
Provide examples of how you've used the software to improve processes.
Example Answers
I have worked with SAP PM and I'm particularly familiar with the planning and scheduling features, which helped optimize our maintenance workflows. For instance, I used the preventive maintenance module to reduce downtime by scheduling regular checks.
Can you explain the importance of preventive maintenance in your planning processes?
How to Answer
- 1
Emphasize cost savings and efficiency improvements
- 2
Highlight the reduction of unplanned downtime
- 3
Discuss the extension of equipment lifespan
- 4
Mention the enhancement of safety and compliance
- 5
Provide examples of successful preventive maintenance implementations
Example Answers
Preventive maintenance is crucial because it significantly reduces the likelihood of unexpected breakdowns, which can be costly and disruptive. By planning regular maintenance, we can extend equipment lifespans and improve overall operational efficiency.
Don't Just Read Maintenance Planner Questions - Practice Answering Them!
Reading helps, but actual practice is what gets you hired. Our AI feedback system helps you improve your Maintenance Planner interview answers in real-time.
Personalized feedback
Unlimited practice
Used by hundreds of successful candidates
How do you use data analysis to improve maintenance scheduling and efficiency?
How to Answer
- 1
Identify key performance indicators related to maintenance.
- 2
Use historical data to forecast maintenance needs and downtime.
- 3
Analyze equipment reliability data to prioritize tasks.
- 4
Develop maintenance schedules based on data trends and patterns.
- 5
Continuously monitor and adjust schedules based on real-time data.
Example Answers
I analyze historical maintenance data to identify trends in equipment failures, which helps me prioritize tasks and create schedules that minimize downtime.
What strategies do you use to create and manage a maintenance budget?
How to Answer
- 1
Assess historical data to understand past maintenance costs and trends
- 2
Engage with maintenance teams to identify upcoming needs and priorities
- 3
Categorize expenses into fixed and variable costs for better clarity
- 4
Implement a tracking system to monitor actual spending against the budget
- 5
Adjust budget allocations based on performance and unexpected expenses
Example Answers
I start by examining historical expenditure records to identify trends and patterns in our maintenance costs. Then, I collaborate with team leaders to discuss anticipated maintenance needs, ensuring that the budget reflects our priorities. I categorize expenses into fixed and variable components to provide clearer insights into where funds are allocated. Throughout the year, I continually track our spending against the budget and make adjustments as necessary based on real-time needs.
Explain how you create a maintenance schedule. What factors do you consider?
How to Answer
- 1
Identify key equipment and their operational requirements
- 2
Analyze historical maintenance data for trends and insights
- 3
Consider manufacturer's recommendations for maintenance intervals
- 4
Incorporate production schedules to minimize downtime
- 5
Prioritize maintenance tasks based on criticality and safety
Example Answers
To create a maintenance schedule, I first identify all key equipment and gather their operational requirements. I analyze historical maintenance data to identify patterns, and consider the manufacturer's recommended maintenance intervals. Additionally, I align the schedule with production timelines to avoid disruptions, prioritizing tasks that affect safety and critical operations.
What role do regulations and compliance play in maintenance planning?
How to Answer
- 1
Identify relevant regulations for your industry
- 2
Discuss how compliance ensures safety and efficiency
- 3
Explain the impact of regulations on scheduling and resource allocation
- 4
Mention the importance of documentation and record-keeping for compliance
- 5
Highlight how compliance affects maintenance strategy and planning decisions
Example Answers
Regulations ensure that all maintenance work adheres to safety standards, which protects both employees and equipment. Compliance with these rules affects scheduling since certain tasks must be done at specific times to meet legal requirements.
What key performance indicators do you track to evaluate maintenance performance?
How to Answer
- 1
Focus on key KPIs relevant to maintenance, such as equipment uptime, mean time between failures, and maintenance cost.
- 2
Briefly explain why each KPI is important for overall performance.
- 3
Use specific examples from your experience where applicable.
- 4
Mention any industry standards or benchmarks you follow.
- 5
Be prepared to discuss how you use this data to improve maintenance processes.
Example Answers
I track key indicators such as equipment uptime, which measures the reliability of our machinery. For instance, maintaining over 95% uptime has allowed us to meet production targets consistently.
Can you discuss your experience with maintaining specific types of machinery relevant to this role?
How to Answer
- 1
Identify key machinery relevant to the role and focus on those.
- 2
Describe your hands-on experience with maintenance tasks and procedures.
- 3
Highlight specific tools and techniques you used for maintenance.
- 4
Mention any relevant achievements or improvements you made.
- 5
Tailor your response to align with the company's machinery and maintenance goals.
Example Answers
In my previous role, I was responsible for the maintenance of HVAC systems. I performed routine inspections and replaced filters, ensuring optimal performance. This resulted in a 20% reduction in energy consumption.
What is your experience with managing relationships with external vendors for maintenance services or parts?
How to Answer
- 1
Highlight your communication skills and how you build rapport with vendors.
- 2
Discuss specific strategies you've used to negotiate costs and services.
- 3
Mention any tools or software you use to track vendor performance.
- 4
Provide examples of resolving conflicts or issues with vendors.
- 5
Emphasize the importance of maintaining long-term relationships for reliability.
Example Answers
In my previous role, I regularly communicated with vendors to ensure timely delivery of parts, which helped establish a good rapport. I used a tracking software to monitor performance and addressed any delays proactively, which strengthened our relationship and improved service outcomes.
What project management methodologies do you apply in your maintenance planning?
How to Answer
- 1
Mention specific methodologies like Agile, Lean, or Six Sigma.
- 2
Explain how you adapt methodologies to maintenance scenarios.
- 3
Provide examples of projects where you applied these methodologies.
- 4
Discuss how these methods improve efficiency and reduce downtime.
- 5
Stay relevant to the role of a Maintenance Planner.
Example Answers
In my maintenance planning, I often use Lean methodologies to streamline processes and reduce waste. For instance, I improved our equipment maintenance schedule by implementing just-in-time practices, which minimized downtime.
Don't Just Read Maintenance Planner Questions - Practice Answering Them!
Reading helps, but actual practice is what gets you hired. Our AI feedback system helps you improve your Maintenance Planner interview answers in real-time.
Personalized feedback
Unlimited practice
Used by hundreds of successful candidates
Can you describe the safety procedures you incorporate into your maintenance planning?
How to Answer
- 1
Start by outlining the importance of safety in maintenance.
- 2
Mention specific safety procedures you follow, such as risk assessments.
- 3
Include how you ensure compliance with safety regulations.
- 4
Discuss training or safety programs that you implement.
- 5
Highlight your commitment to continuous improvement in safety practices.
Example Answers
I emphasize safety by conducting thorough risk assessments before any maintenance tasks. I ensure compliance with OSHA regulations and regularly update our safety protocols based on new best practices.
Maintenance Planner Position Details
Salary Information
Recommended Job Boards
CareerBuilder
www.careerbuilder.com/jobs/maintenance-plannerZipRecruiter
www.ziprecruiter.com/Jobs/Maintenance-PlannerThese job boards are ranked by relevance for this position.
Related Positions
Ace Your Next Interview!
Practice with AI feedback & get hired faster
Personalized feedback
Used by hundreds of successful candidates
Ace Your Next Interview!
Practice with AI feedback & get hired faster
Personalized feedback
Used by hundreds of successful candidates