Top 31 Maintenance Repairer Interview Questions and Answers [Updated 2025]
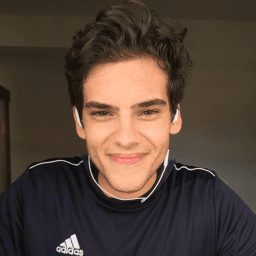
Andre Mendes
•
March 30, 2025
Preparing for a Maintenance Repairer interview? This blog post is your ultimate guide, featuring the most common interview questions you'll encounter in this role. Dive in to find example answers and insightful tips on how to respond effectively, boosting your confidence and readiness. Whether you're a seasoned professional or new to the field, this resource will help you stand out and succeed in your interview.
Download Maintenance Repairer Interview Questions in PDF
To make your preparation even more convenient, we've compiled all these top Maintenance Repairerinterview questions and answers into a handy PDF.
Click the button below to download the PDF and have easy access to these essential questions anytime, anywhere:
List of Maintenance Repairer Interview Questions
Behavioral Interview Questions
Can you describe a time when you identified a major maintenance issue before it became a problem?
How to Answer
- 1
Start with a brief context of your workplace and responsibilities.
- 2
Describe the specific issue you identified and how you discovered it.
- 3
Explain the steps you took to address and resolve the issue.
- 4
Highlight the results of your actions and any feedback received.
- 5
Keep your answer focused and concise, aiming for a narrative structure.
Example Answers
In my previous role as a maintenance technician at a large facility, I noticed that the heating system was making unusual noises during routine checks. I investigated further and discovered that one of the ducts was partially blocked. I quickly cleaned the duct and scheduled a more in-depth review of the system. As a result, we avoided a potential heating failure during the winter, and my supervisor praised my proactive approach.
Tell me about a situation where you had to work closely with a team to complete a maintenance project.
How to Answer
- 1
Clearly define the project and your role in the team.
- 2
Highlight communication and collaboration with team members.
- 3
Discuss any challenges faced and how they were overcome as a team.
- 4
Mention the outcome and any positive feedback received.
- 5
Keep your answer focused and relevant to the position.
Example Answers
In my last job, our team was tasked with overhauling the HVAC system in a commercial building. I was responsible for coordinating with the plumbing and electrical teams. We held daily briefings to ensure everyone was on the same page. We faced a challenge when we discovered outdated wiring, but I suggested we split into smaller groups to tackle each issue simultaneously. The project was completed on schedule, and the client praised our teamwork.
Don't Just Read Maintenance Repairer Questions - Practice Answering Them!
Reading helps, but actual practice is what gets you hired. Our AI feedback system helps you improve your Maintenance Repairer interview answers in real-time.
Personalized feedback
Unlimited practice
Used by hundreds of successful candidates
Describe a conflict you had with a coworker regarding maintenance priorities. How did you resolve it?
How to Answer
- 1
Focus on a specific conflict and its context
- 2
Explain your viewpoint and your coworker's viewpoint
- 3
Describe the steps you took to resolve the conflict
- 4
Highlight any compromise or solution reached
- 5
Reflect on what you learned from the experience
Example Answers
In a previous job, my coworker and I disagreed on whether the HVAC system or plumbing issue should be prioritized. I believed the HVAC system needed urgent attention due to extreme temperatures. I scheduled a meeting to discuss our priorities, presenting data on work orders and crew availability. We agreed to address both issues simultaneously by splitting our team. This compromise ensured both issues were handled promptly, and I learned the importance of communication in resolving conflicts.
Have you ever had to manage multiple maintenance tasks at once? How did you prioritize?
How to Answer
- 1
Identify urgent tasks that affect safety or operations first.
- 2
Assess the impact of each task on overall maintenance efficiency.
- 3
Communicate with team members to understand their input on priorities.
- 4
Use a checklist to organize tasks by importance and deadlines.
- 5
Be flexible and adjust priorities as new issues arise.
Example Answers
In my previous role, I faced multiple urgent repairs at once. I prioritized tasks based on urgency, starting with a power outage that affected entire equipment. I communicated with my team to delegate smaller tasks and later resolved less critical issues.
Give an example of a time when you took initiative to improve a maintenance process or procedure.
How to Answer
- 1
Identify a specific situation where you saw an issue.
- 2
Explain the action you took to address that issue.
- 3
Highlight the positive outcome or improvement made.
- 4
Use metrics or specific results if possible.
- 5
Keep the answer focused on your role and impact.
Example Answers
In my previous job, I noticed that our equipment maintenance logs were often incomplete, which led to missed service dates. I created a digital template that simplified logging maintenance and trained the team to use it. As a result, our on-time maintenance rate improved by 30%.
Can you talk about a time you had to learn a new maintenance technique or technology quickly?
How to Answer
- 1
Choose a specific example from your experience.
- 2
Describe the context and why you needed to learn quickly.
- 3
Explain the steps you took to learn the technique or technology.
- 4
Share the outcome and how it benefited the team or project.
- 5
Keep it concise, focusing on your adaptability and results.
Example Answers
At my previous job, we had to switch to a new HVAC system for which I had no prior experience. I dedicated a day to read the manual and watched tutorial videos. By the end of the week, I was able to successfully complete the installation and training my team on it, which improved our service response time by 20%.
Have you ever received feedback from a supervisor that helped you improve your maintenance skills? What was it?
How to Answer
- 1
Think of specific feedback you received from a supervisor.
- 2
Explain how that feedback helped you grow as a maintenance worker.
- 3
Provide a concrete example of what you changed based on the feedback.
- 4
Mention any specific results or improvements from implementing the feedback.
- 5
Keep your answer focused and concise.
Example Answers
Yes, my supervisor once pointed out that I was not as thorough in my inspections as I could be. I started following a detailed checklist for each inspection, which helped me identify issues earlier. As a result, our downtime decreased by 15%.
Describe a time when you had to learn a new skill for a maintenance job. What steps did you take?
How to Answer
- 1
Identify the specific skill you learned and why it was necessary.
- 2
Explain the resources you used to learn (e.g., online courses, manuals, mentorship).
- 3
Describe how you applied the new skill in a practical situation.
- 4
Highlight any challenges you faced and how you overcame them.
- 5
Conclude with the positive outcome or results from learning the skill.
Example Answers
In my last position, I needed to learn how to troubleshoot electrical systems. I enrolled in an online course focusing on electrical repair techniques, spent evenings studying the material, and practiced with old equipment at work. When the time came to troubleshoot a recurring issue, I applied what I learned, resolved the problem efficiently, and improved the team's workflow.
Tell me about a time when you had to ensure reliability in maintenance execution.
How to Answer
- 1
Use the STAR method: Situation, Task, Action, Result.
- 2
Focus on a specific maintenance task or project.
- 3
Highlight the steps you took to ensure reliability and quality.
- 4
Emphasize teamwork or communication if applicable.
- 5
Conclude with the positive impact of your actions on the operation.
Example Answers
At my previous job, we faced recurring issues with the HVAC system. I led a task force to perform a thorough inspection. We found that regular maintenance logs were not being followed. I initiated a revised schedule and implemented weekly checks. This improved system reliability by 30% over three months.
Have you ever had to explain technical information to someone without a technical background? How did you do it?
How to Answer
- 1
Identify a specific example where you explained something technical.
- 2
Use simple terminology and avoid jargon.
- 3
Relate the explanation to real-world examples the person can understand.
- 4
Check for understanding by asking questions.
- 5
Be patient and willing to elaborate if needed.
Example Answers
In my previous job, I had to explain how a heating system works to a client. I used simple terms, describing it like a car engine, explaining how energy flows and keeps the house warm. I made sure to ask if they needed clarification at any point, and related it to their specific heating concerns.
Don't Just Read Maintenance Repairer Questions - Practice Answering Them!
Reading helps, but actual practice is what gets you hired. Our AI feedback system helps you improve your Maintenance Repairer interview answers in real-time.
Personalized feedback
Unlimited practice
Used by hundreds of successful candidates
Technical Interview Questions
What safety procedures do you follow when performing repairs or maintenance?
How to Answer
- 1
Always wear appropriate personal protective equipment (PPE) based on the job type.
- 2
Ensure the workspace is clear of hazards and well-lit before starting repairs.
- 3
Lockout/tagout (LOTO) procedures must be followed to prevent accidental equipment start-up.
- 4
Use tools and equipment properly and ensure they are in good working condition.
- 5
Follow safety data sheets (SDS) for any chemicals or materials used.
Example Answers
I always wear safety goggles and gloves to protect myself. Before I begin any maintenance, I ensure the area is free of debris and follow LOTO procedures to ensure equipment is not accidentally energized.
What types of tools and equipment are you most comfortable using for maintenance tasks?
How to Answer
- 1
List specific tools you have experience with like hand tools, power tools, and specialized equipment.
- 2
Mention how long you have been using these tools to show your familiarity.
- 3
Include examples of tasks you have completed using these tools.
- 4
Highlight any certifications or training related to tools if applicable.
- 5
Be confident and express willingness to learn new tools if needed.
Example Answers
I am most comfortable using hand tools like wrenches, screwdrivers, and pliers. I've used power tools like drills and saws for over 5 years, completing various tasks such as repairs and installations.
Don't Just Read Maintenance Repairer Questions - Practice Answering Them!
Reading helps, but actual practice is what gets you hired. Our AI feedback system helps you improve your Maintenance Repairer interview answers in real-time.
Personalized feedback
Unlimited practice
Used by hundreds of successful candidates
Can you explain the difference between preventive maintenance and reactive maintenance?
How to Answer
- 1
Define preventive maintenance as scheduled maintenance to prevent issues.
- 2
Define reactive maintenance as fixing problems after they occur.
- 3
Provide examples of each type to illustrate your point.
- 4
Explain the benefits of preventive maintenance in cost savings and efficiency.
- 5
Mention situations where reactive maintenance might be necessary.
Example Answers
Preventive maintenance is when we schedule regular checks and maintenance tasks to avoid breakdowns, like changing filters and lubricating parts. In contrast, reactive maintenance comes into play when something breaks down unexpectedly, and we need to repair it on the spot.
How do you approach diagnosing mechanical issues in machinery?
How to Answer
- 1
Start with visual inspection of the machinery for any obvious signs of wear or damage.
- 2
Listen for unusual noises while the machinery is operating to pinpoint possible issues.
- 3
Use diagnostic tools and software if available to read any error codes.
- 4
Check the operating parameters against manufacturer specifications.
- 5
Engage in a methodical troubleshooting process, isolating each system component.
Example Answers
I begin by conducting a visual inspection to identify any signs of wear or loose connections. After that, I listen for any unusual noises and use diagnostic tools to check for error codes.
Can you describe your experience with troubleshooting electrical systems?
How to Answer
- 1
Start with your relevant educational background or certifications in electrical systems.
- 2
Mention specific tools and techniques you use for troubleshooting.
- 3
Provide examples of problems you have diagnosed and resolved.
- 4
Highlight your approach to safety when working with electrical systems.
- 5
Conclude with any relevant results or improvements from your troubleshooting efforts.
Example Answers
I have an electrical technician certification and over three years of experience troubleshooting wiring issues. I typically use a multimeter to check voltages and test circuits. For example, I once identified a faulty relay in a control panel that was causing system failures and replaced it, which improved the system's reliability. Safety is always my priority, and I ensure the power is off before starting any work.
What experience do you have with plumbing repairs and maintenance?
How to Answer
- 1
Briefly describe specific plumbing tasks you have performed.
- 2
Mention any formal training or certifications related to plumbing.
- 3
Include examples of troubleshooting plumbing issues.
- 4
Highlight teamwork or collaboration with other maintenance staff in plumbing projects.
- 5
State the impact of your plumbing work on overall facility maintenance.
Example Answers
I have over three years of experience in plumbing repairs, including fixing leaks, unclogging drains, and replacing fixtures in residential buildings. I completed a plumbing certification course which provided hands-on training.
Can you detail your experience with HVAC system maintenance?
How to Answer
- 1
Mention specific HVAC systems you have worked on
- 2
Describe key maintenance tasks you performed regularly
- 3
Share any certifications or training relevant to HVAC maintenance
- 4
Highlight your problem-solving skills and any challenges faced
- 5
Emphasize your attention to safety and compliance with regulations
Example Answers
I have over three years of experience maintaining residential HVAC systems, including central air conditioning units and furnaces. My tasks included regular filter changes, cleaning condenser coils, and performing annual inspections to ensure efficiency. I hold an EPA certification, which has equipped me to handle refrigerants safely.
What steps do you take when conducting preventive maintenance on equipment?
How to Answer
- 1
Identify the equipment and review its maintenance schedule
- 2
Gather necessary tools and equipment before starting the maintenance
- 3
Conduct a thorough inspection of the equipment for wear and tear
- 4
Perform maintenance tasks according to the checklist provided
- 5
Document any issues and maintenance performed for future reference
Example Answers
I start by reviewing the maintenance schedule and then gather all necessary tools. I inspect the equipment carefully for any signs of wear, perform the required tasks from the checklist, and finally, I document everything I did during the maintenance.
How do you maintain accurate records of maintenance work done?
How to Answer
- 1
Utilize a digital maintenance management system for records.
- 2
Document every task immediately after completion.
- 3
Include details such as date, time, and description of work.
- 4
Regularly review and update records for accuracy.
- 5
Ensure all team members follow the same recording procedure.
Example Answers
I use a digital maintenance management system where I enter each task right after completing it, making sure to include the date, time, and a detailed description. This helps keep records accurate and up-to-date.
What experience do you have with welding and metal repairs?
How to Answer
- 1
Outline specific welding techniques you have used
- 2
Mention types of projects or repairs you've completed
- 3
Include any relevant certifications or training
- 4
Discuss the tools and equipment you're familiar with
- 5
Highlight any problem-solving experiences related to welding
Example Answers
I have over three years of experience in MIG welding, primarily working on repair projects for machinery and equipment in a manufacturing setting. I've completed several metal fabrication tasks that required precise weld quality to ensure equipment safety.
Don't Just Read Maintenance Repairer Questions - Practice Answering Them!
Reading helps, but actual practice is what gets you hired. Our AI feedback system helps you improve your Maintenance Repairer interview answers in real-time.
Personalized feedback
Unlimited practice
Used by hundreds of successful candidates
What types of machinery do you have the most experience maintaining?
How to Answer
- 1
Identify key machinery types relevant to the job description.
- 2
Mention specific maintenance tasks you performed on those machines.
- 3
Highlight any relevant experience in troubleshooting issues.
- 4
Include any certifications or training related to machinery maintenance.
- 5
Tailor your answer to show how your experience aligns with the company's needs.
Example Answers
I have extensive experience maintaining HVAC units, including routine servicing, filter changes, and troubleshooting system failures.
Situational Interview Questions
You are given a tight deadline to complete maintenance on several machines. How do you ensure all tasks are completed?
How to Answer
- 1
Assess the maintenance needs of each machine quickly
- 2
Prioritize tasks based on urgency and impact on operations
- 3
Communicate with your team to delegate responsibilities
- 4
Utilize checklists to keep track of completed tasks
- 5
Remain flexible to adjust plans as needed to meet the deadline
Example Answers
First, I would quickly assess the maintenance needs of each machine and prioritize the tasks that are most critical. Then, I’d communicate with my team to delegate specific tasks based on their strengths, ensuring we work efficiently towards the deadline.
If you discovered that a critical piece of machinery had a malfunction, what steps would you take immediately?
How to Answer
- 1
Assess the situation to determine the severity of the malfunction.
- 2
Isolate or shut down the machinery to prevent further damage or accidents.
- 3
Notify your supervisor and relevant team members about the issue.
- 4
Document the malfunction details including time and circumstances.
- 5
Review maintenance logs and previous issues related to the machinery.
Example Answers
First, I would quickly assess the machine to understand what went wrong. If it's serious, I would shut it down immediately to avoid any safety hazards. Next, I would inform my supervisor about the situation and follow that up with a detailed report.
Don't Just Read Maintenance Repairer Questions - Practice Answering Them!
Reading helps, but actual practice is what gets you hired. Our AI feedback system helps you improve your Maintenance Repairer interview answers in real-time.
Personalized feedback
Unlimited practice
Used by hundreds of successful candidates
Imagine a situation where you are short on staff but have urgent maintenance tasks. How would you handle it?
How to Answer
- 1
Prioritize the most urgent tasks based on safety and operational impact
- 2
Communicate clearly with your team about expectations and roles
- 3
Consider reassigning tasks to fit staff strengths and expertise
- 4
Utilize tools and resources efficiently to speed up processes
- 5
Stay adaptable and ready to adjust plans as situations change
Example Answers
In a situation with reduced staff, I would first assess which maintenance tasks are critical and prioritize those. I would then assign responsibilities based on each team member's strengths and ensure everyone is clear on their roles. I would also leverage any available tools to maximize our efficiency.
How would you respond if a client reports a maintenance issue and is dissatisfied with previous repairs?
How to Answer
- 1
Listen actively to the client's concerns without interrupting.
- 2
Acknowledge the dissatisfaction and express understanding of their frustration.
- 3
Apologize for the inconvenience caused by the previous repairs.
- 4
Explain the steps you will take to investigate and resolve the issue.
- 5
Follow up with the client after the repairs to ensure their satisfaction.
Example Answers
I would first listen carefully to the client's concerns and allow them to express their dissatisfaction. I would then apologize for the inconvenience and assure them I understand their frustration. I would explain that I will thoroughly investigate the issue and get it resolved promptly. Finally, I would follow up after completing the repairs to check if they are satisfied.
What would your plan be if a machine fails during peak operation hours?
How to Answer
- 1
Remain calm and quickly assess the situation
- 2
Notify the team and management immediately
- 3
Identify the machine and gather necessary information
- 4
Implement a temporary workaround if possible
- 5
Perform repairs as soon as it’s safe and feasible
Example Answers
First, I would stay calm and assess the failure to understand its impact. Then, I would notify my supervisor and team immediately to address the issue collectively. I would document the incident and try to implement a temporary solution to minimize downtime.
If you notice a repair has not held up as expected after a short period, how would you handle it?
How to Answer
- 1
Assess the situation to understand why the repair failed.
- 2
Communicate with the relevant parties about the issue.
- 3
Determine if the initial repair method was appropriate.
- 4
Implement corrective measures promptly.
- 5
Document the incident for future reference and improvement.
Example Answers
I would first inspect the repair to identify the cause of the failure. Next, I would inform my supervisor about the issue and discuss possible reasons for the problem. I would then take corrective action, such as redoing the repair or using a different method if needed.
You realize that some necessary parts for a repair are on backorder. How would you approach this situation?
How to Answer
- 1
Assess the urgency of the repair and determine if it can wait.
- 2
Communicate with your supervisor about the situation and potential solutions.
- 3
Explore alternative suppliers or substitute parts if possible.
- 4
Schedule the repair for a later date once the parts arrive if it can wait.
- 5
Document the issue and keep a record of the communication regarding the backorder.
Example Answers
First, I would evaluate how critical the repair is. If it can wait, I would inform my supervisor of the backorder and discuss scheduling it for a later date. I would also look into other suppliers to see if I can find the parts sooner.
If you're working on a maintenance task and a team member suggests a different approach, how would you respond?
How to Answer
- 1
Listen actively to the team member's suggestion.
- 2
Evaluate the suggestion based on safety, efficiency, and effectiveness.
- 3
Express appreciation for their input, fostering collaboration.
- 4
If the suggestion is valid, discuss implementing the changes together.
- 5
If not suitable, politely explain your reasoning.
Example Answers
I would listen carefully to my team member’s suggestion and consider it. If it improves safety or efficiency, I would be open to trying it. I believe collaboration leads to better solutions.
If asked to perform maintenance on an unfamiliar system, how would you approach the task?
How to Answer
- 1
Start by gathering all available documentation for the system.
- 2
Identify and locate any tools or resources you might need.
- 3
Consult with team members or experts who have experience with the system.
- 4
Break down the maintenance task into smaller, manageable steps.
- 5
Test and validate your work once the maintenance is completed.
Example Answers
I would begin by collecting manuals or any documentation related to the system. Then, I'd make sure I have the necessary tools on hand. If needed, I would ask colleagues for insights. I would approach the maintenance step-by-step to ensure nothing is overlooked, and finally, I would test the system to confirm everything is working correctly.
How would you manage your stress levels during a high-pressure maintenance situation?
How to Answer
- 1
Stay calm and take a deep breath to clear your mind.
- 2
Prioritize tasks based on urgency and impact.
- 3
Communicate clearly with your team to delegate responsibilities.
- 4
Focus on solutions rather than problems.
- 5
Reflect on past experiences to draw on effective strategies.
Example Answers
In a high-pressure situation, I would first take a deep breath to help focus my mind. Then, I would assess the tasks at hand and prioritize them to tackle the most urgent issues first. Clear communication with my team would be key to ensure we all knew our roles.
Don't Just Read Maintenance Repairer Questions - Practice Answering Them!
Reading helps, but actual practice is what gets you hired. Our AI feedback system helps you improve your Maintenance Repairer interview answers in real-time.
Personalized feedback
Unlimited practice
Used by hundreds of successful candidates
Maintenance Repairer Position Details
Related Positions
- Maintenance Specialist
- Maintenance Man
- Maintenance Machinist
- Multi-Skilled Maintenance Engineer
- Maintainer
- Machinist
- Grease Worker
- Car Greaser
- Hot Worker
- Machine Oiler
Similar positions you might be interested in.
Ace Your Next Interview!
Practice with AI feedback & get hired faster
Personalized feedback
Used by hundreds of successful candidates
Ace Your Next Interview!
Practice with AI feedback & get hired faster
Personalized feedback
Used by hundreds of successful candidates