Top 31 Maintenance Specialist Interview Questions and Answers [Updated 2025]
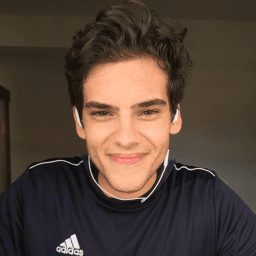
Andre Mendes
•
March 30, 2025
Navigating the competitive landscape of maintenance specialist roles requires preparation, especially when it comes to interviews. In this post, we delve into the most common interview questions tailored for maintenance specialists, providing insightful example answers and practical tips to help you respond with confidence and clarity. Whether you're a seasoned professional or new to the field, these strategies will equip you to shine in your next interview.
Download Maintenance Specialist Interview Questions in PDF
To make your preparation even more convenient, we've compiled all these top Maintenance Specialistinterview questions and answers into a handy PDF.
Click the button below to download the PDF and have easy access to these essential questions anytime, anywhere:
List of Maintenance Specialist Interview Questions
Technical Interview Questions
What experience do you have with HVAC systems, and can you explain how you ensure they operate efficiently?
How to Answer
- 1
Highlight specific HVAC projects you've worked on
- 2
Mention any relevant certifications or training in HVAC
- 3
Discuss key maintenance practices you implement
- 4
Explain how you troubleshoot efficiency issues
- 5
Share an example of improving HVAC system performance
Example Answers
In my previous role, I managed the HVAC systems for a large commercial building where I implemented a regular maintenance schedule that included filter changes and system checks. This proactive approach helped reduce energy costs by 15%.
Can you explain how pneumatic systems work and what common issues might arise?
How to Answer
- 1
Start with a brief definition of pneumatic systems using compressed air.
- 2
Mention how they operate mechanics like actuators and valves.
- 3
List common issues like leaks, pressure drops, and component failure.
- 4
Explain the impact of these issues on system performance.
- 5
Conclude with a preventive measure or maintenance tip.
Example Answers
Pneumatic systems use compressed air to power actuators and valves. They operate by controlling air flow and pressure to move machinery. Common issues include air leaks which cause pressure drops and can lead to slow operation. Regular inspections can help identify leaks early, ensuring smooth operation.
Don't Just Read Maintenance Specialist Questions - Practice Answering Them!
Reading helps, but actual practice is what gets you hired. Our AI feedback system helps you improve your Maintenance Specialist interview answers in real-time.
Personalized feedback
Unlimited practice
Used by hundreds of successful candidates
What types of machinery have you worked with in maintenance, and what are common issues associated with them?
How to Answer
- 1
List specific types of machinery you have experience with.
- 2
Mention common maintenance issues for each type.
- 3
Give examples of how you solved those issues.
- 4
Highlight safety protocols you follow during maintenance.
- 5
Tailor your answer to relate to the job you are applying for.
Example Answers
I have worked with hydraulic lifts, conveyor belts, and industrial compressors. Common issues with hydraulic lifts include fluid leaks and pressure drops, which I address by inspecting seals and performing regular fluid changes. I also ensure compliance with safety standards while working.
How proficient are you with electrical systems in maintenance, and can you explain a troubleshooting process?
How to Answer
- 1
Assess your experience with electrical systems in maintenance roles.
- 2
Highlight specific tools or technologies you are familiar with.
- 3
Describe a systematic approach to troubleshooting, such as identifying symptoms, testing components, and implementing solutions.
- 4
Provide a real-life example of a troubleshooting scenario you handled.
- 5
Mention any relevant certifications or training you have in electrical maintenance.
Example Answers
I have over five years of experience with electrical systems, specifically in industrial settings. I am proficient in using tools like multimeters and oscilloscopes. For troubleshooting, I start by identifying the symptoms, then isolate the problem by testing individual components, and finally apply the appropriate solution. Recently, I resolved a recurring circuit failure by replacing a faulty relay after monitoring voltage drops.
What is your process for developing and executing a preventive maintenance program?
How to Answer
- 1
Start with a thorough assessment of current equipment and maintenance history
- 2
Identify critical systems and prioritize them based on risk and impact
- 3
Develop a maintenance schedule using manufacturer guidelines and best practices
- 4
Implement a tracking system for maintenance tasks and performance metrics
- 5
Regularly review and adjust the program based on feedback and operational changes
Example Answers
I begin by assessing the current state of the equipment and reviewing past maintenance records. Then, I prioritize equipment based on their criticality to operations, ensuring we focus on high-risk areas first. I create a schedule aligned with manufacturer recommendations, and I track completed tasks using a software system to monitor performance. Finally, I review the program quarterly to make improvements.
How do you manage spare parts inventory and ensure you have the necessary tools available for maintenance tasks?
How to Answer
- 1
Maintain a digital inventory system for tracking spare parts usage and stock levels
- 2
Regularly audit inventory to identify low stock and reorder as necessary
- 3
Use predictive maintenance data to anticipate parts needs based on equipment usage
- 4
Establish relationships with suppliers for quick turnaround on urgent parts
- 5
Communicate with maintenance staff to gather feedback on tool and part requirements
Example Answers
I use a digital inventory system to track spare parts, conducting regular audits to reorder any low stock. By analyzing predictive maintenance data, I can anticipate the parts we need and ensure they're available.
What maintenance management software have you used, and how did it improve your workflow?
How to Answer
- 1
Identify specific software you have used in past roles.
- 2
Explain the features of the software that were most beneficial.
- 3
Share a concrete example of how it improved your efficiency or productivity.
- 4
Mention any metrics or results that demonstrate the improvement.
- 5
Keep your answer focused and relevant to the position.
Example Answers
I've used CMMS software like EAM, which streamlined our work order process. It allowed us to track maintenance requests in real time, reducing our response time by 30%.
What methods do you use for diagnosing mechanical failures in machinery?
How to Answer
- 1
Start with visual inspections to identify obvious issues.
- 2
Utilize diagnostic tools like vibration analysis or thermal imaging.
- 3
Analyze historical performance data for patterns indicating failures.
- 4
Engage with operators for their insights on machinery behavior.
- 5
Follow a systematic troubleshooting process to isolate the problem.
Example Answers
I begin with visual inspections to check for wear and tear. Then, I use tools like vibration analysis to detect abnormal sounds and thermal imaging to find overheating components. Historical data helps spot recurring issues, and I always ask operators for their observations before diving into a systematic troubleshooting process.
How do you ensure that your maintenance practices comply with regulatory standards?
How to Answer
- 1
Stay updated on local, state, and federal regulations affecting maintenance.
- 2
Implement regular training sessions for the maintenance team on compliance practices.
- 3
Develop a checklist for procedures that meet regulatory standards.
- 4
Conduct regular audits of maintenance practices to identify compliance gaps.
- 5
Keep thorough documentation of all maintenance activities and regulatory requirements.
Example Answers
I ensure compliance by staying updated on regulations and conducting regular training sessions for my team. We also use detailed checklists to follow all required procedures and perform audits to ensure we meet standards.
What types of welding techniques are you familiar with, and when would you apply them in maintenance?
How to Answer
- 1
Identify key welding techniques you know, such as MIG, TIG, or Stick welding.
- 2
Explain the advantages of each technique for maintenance tasks.
- 3
Provide specific examples of when you used these techniques in past jobs.
- 4
Mention safety precautions and considerations relevant to each technique.
- 5
Tailor your answer to relate to the company's maintenance needs.
Example Answers
I am familiar with MIG welding, which I often use for its speed in maintenance tasks like repairing metal frames. It's great for thicker materials and projects requiring a fast turnaround.
Don't Just Read Maintenance Specialist Questions - Practice Answering Them!
Reading helps, but actual practice is what gets you hired. Our AI feedback system helps you improve your Maintenance Specialist interview answers in real-time.
Personalized feedback
Unlimited practice
Used by hundreds of successful candidates
Can you discuss your knowledge of mechanical systems and how you approach their maintenance?
How to Answer
- 1
Start with your education or training related to mechanical systems
- 2
Mention specific mechanical systems you are familiar with
- 3
Explain your maintenance strategies and methodologies
- 4
Highlight your experience with preventive and corrective maintenance
- 5
Conclude with an example of a successful maintenance project or challenge you overcame
Example Answers
I have a degree in Mechanical Engineering and several years of experience with HVAC and hydraulic systems. My approach involves thorough inspections and regular preventive maintenance to avoid costly breakdowns. In my last job, I implemented a new schedule that reduced equipment downtime by 20%.
Behavioral Interview Questions
Can you describe a time when you successfully led a maintenance team through a challenging situation?
How to Answer
- 1
Select a specific situation that highlights your leadership and problem-solving skills.
- 2
Use the STAR method: Situation, Task, Action, Result to structure your response.
- 3
Emphasize communication and teamwork in overcoming the challenge.
- 4
Highlight any technical skills or knowledge that contributed to the success.
- 5
Mention both the outcome and what you learned from the experience.
Example Answers
In my previous role, our team faced a significant equipment failure during peak operation hours. I organized an immediate meeting, assigned roles based on each team member's strengths, and we diagnosed the issue quickly. We managed to repair the equipment within three hours, minimizing downtime. This experience strengthened my leadership skills and taught me the importance of teamwork under pressure.
Tell me about a specific instance when you identified a recurring maintenance issue and how you addressed it.
How to Answer
- 1
Identify a specific maintenance issue you encountered.
- 2
Explain how you discovered it was recurring.
- 3
Describe the steps you took to address the issue.
- 4
Mention the outcome and any improvements seen.
- 5
Use measurable results if possible.
Example Answers
At my previous job, we had a recurring issue with the conveyor belts frequently breaking down. I noticed this after tracking the maintenance logs for several months. I organized a root cause analysis with the team, which revealed that the tension was incorrectly calibrated. We adjusted the tension settings and implemented regular tension checks. As a result, downtime decreased by 40% over the next quarter.
Don't Just Read Maintenance Specialist Questions - Practice Answering Them!
Reading helps, but actual practice is what gets you hired. Our AI feedback system helps you improve your Maintenance Specialist interview answers in real-time.
Personalized feedback
Unlimited practice
Used by hundreds of successful candidates
Describe an experience where you had to work closely with another department to complete a maintenance project.
How to Answer
- 1
Identify the departments involved and the project scope.
- 2
Explain your role in facilitating communication and collaboration.
- 3
Highlight specific actions you took to overcome challenges.
- 4
Discuss the outcome of the project and its impact.
- 5
Use a structured approach: Situation, Task, Action, Result.
Example Answers
In my previous role, I worked with the production department to upgrade our manufacturing line. I liaised between teams to align schedules and requirements, ensured timely communication, and helped resolve logistical issues. The project was completed ahead of schedule, increasing productivity by 15%.
Give an example of a conflict that arose within your team and how you resolved it.
How to Answer
- 1
Identify the conflict clearly and concisely.
- 2
Describe your role in the situation as a leader.
- 3
Explain the steps you took to understand both sides.
- 4
Outline the solution you implemented and its impact.
- 5
Reflect on what you learned from resolving the conflict.
Example Answers
In my previous role, two team members disagreed on the best approach to a repair project, causing tension. I met with each individual to listen to their perspectives. I facilitated a team meeting where we discussed the pros and cons of both approaches together, leading to a compromise that satisfied everyone. The project was completed successfully and on time, and the team learned to communicate better.
What steps have you taken in the past to ensure a safe working environment for your team?
How to Answer
- 1
Conduct regular safety training for all team members
- 2
Implement and enforce safety protocols and procedures
- 3
Perform routine safety inspections to identify hazards
- 4
Encourage open communication about safety issues
- 5
Provide personal protective equipment (PPE) and ensure its use
Example Answers
I initiate monthly safety training sessions to cover protocols and refresh our knowledge, which has significantly reduced accidents.
How do you prioritize maintenance tasks when faced with multiple urgent issues?
How to Answer
- 1
Assess the impact of each issue on operations
- 2
Consult with your team to gauge urgency and resources
- 3
Categorize tasks by safety risk, production impact, and ease of completion
- 4
Communicate priorities clearly to the team and stakeholders
- 5
Document decisions and review them regularly for adjustments
Example Answers
I begin by evaluating which issue affects safety or critical operations the most. Then, I involve my team in discussing which tasks can be tackled quickly with available resources. Finally, I categorize them and communicate the plan to ensure everyone is aligned.
Describe a time when you had to train a new employee in maintenance protocols. What approach did you take?
How to Answer
- 1
Choose a specific training example from your experience.
- 2
Outline the training process you used, such as shadowing or hands-on practice.
- 3
Explain how you ensured the new employee understood the protocols.
- 4
Mention any challenges faced and how you addressed them.
- 5
Highlight the positive outcome or feedback from the new employee.
Example Answers
At my previous job, I trained a new maintenance technician by having him shadow me for the first week. I broke down the protocols into manageable steps and provided hands-on practice with the tools. When he struggled with safety procedures, I took extra time to demonstrate the correct methods. By the end of our training, he felt confident and received positive feedback from our team.
Describe a time you received constructive criticism and how you used it to improve your management style.
How to Answer
- 1
Identify a specific instance of criticism you received.
- 2
Explain the context and who gave you the feedback.
- 3
Describe your initial reaction to the feedback.
- 4
Share the steps you took to implement changes in your management style.
- 5
Highlight the positive outcome or improvement resulting from the change.
Example Answers
In my previous role, my supervisor pointed out that I wasn't delegating tasks effectively. At first, I felt defensive but then I recognized the truth in the feedback. I started to trust my team more by assigning responsibilities and empowering them. This led to increased team morale and productivity, as everyone felt more engaged and accountable.
Don't Just Read Maintenance Specialist Questions - Practice Answering Them!
Reading helps, but actual practice is what gets you hired. Our AI feedback system helps you improve your Maintenance Specialist interview answers in real-time.
Personalized feedback
Unlimited practice
Used by hundreds of successful candidates
Situational Interview Questions
If a key piece of equipment breaks down unexpectedly, how would you handle the situation?
How to Answer
- 1
Assess the situation quickly to understand the impact on operations
- 2
Communicate with the team to inform them of the breakdown
- 3
Identify potential solutions, such as repairs or replacements
- 4
Assign tasks to team members to address the issue efficiently
- 5
Document the incident for future reference and preventive measures
Example Answers
First, I would assess the extent of the breakdown and its impact on our operations. Then, I would notify the team and delegate tasks based on their expertise to start troubleshooting. It's important to communicate clearly throughout the process and to document everything for future improvements.
How would you identify and address skills gaps in your maintenance team?
How to Answer
- 1
Conduct regular assessments of team capabilities through performance reviews
- 2
Implement skills matrices to visualize strengths and weaknesses within the team
- 3
Encourage open communication for team members to express their self-identified skills gaps
- 4
Arrange training sessions or workshops based on the identified skills gaps
- 5
Monitor progress and adjust training programs as needed
Example Answers
I would start by assessing each team member's skills through performance reviews and create a skills matrix to identify gaps. Then, I’d facilitate training sessions tailored to those needs.
Don't Just Read Maintenance Specialist Questions - Practice Answering Them!
Reading helps, but actual practice is what gets you hired. Our AI feedback system helps you improve your Maintenance Specialist interview answers in real-time.
Personalized feedback
Unlimited practice
Used by hundreds of successful candidates
How would you respond if you received reports of a safety incident in the maintenance area?
How to Answer
- 1
Acknowledge the report immediately and express concern for safety.
- 2
Gather all relevant details about the incident from those involved.
- 3
Ensure that first aid or emergency services are provided if necessary.
- 4
Investigate the incident thoroughly to understand the cause.
- 5
Implement corrective actions to prevent future occurrences.
Example Answers
I would first acknowledge the report and express my concern for anyone involved. Then, I would gather more details from the team to understand what happened. If there were injuries, I would ensure that proper medical assistance is given. I would also conduct a thorough investigation and apply necessary safety measures to prevent similar incidents in the future.
Imagine you have limited resources for a maintenance project. How would you allocate your team's time and skills?
How to Answer
- 1
Identify the critical tasks that must be completed first
- 2
Assess the skills of each team member and assign roles accordingly
- 3
Create a realistic timeline that prioritizes urgent needs
- 4
Communicate clearly with the team about the plan and expectations
- 5
Monitor progress and adjust assignments as needed
Example Answers
I would first identify the most critical tasks for the project and prioritize them. Then I would evaluate my team's strengths and assign the right people to the key tasks. I would create a timeline focusing on the urgent needs and keep everyone updated with regular check-ins.
What would you do if you noticed a team member not collaborating well with others?
How to Answer
- 1
Observe the team dynamics to identify specific issues with collaboration
- 2
Speak to the team member privately to understand their perspective
- 3
Encourage open communication within the team to address issues together
- 4
Suggest team-building activities to strengthen relationships
- 5
Follow up after addressing the issue to ensure improvement
Example Answers
I would first observe the interactions to pinpoint the problem. Then, I would talk to the team member privately to understand what might be causing their reluctance to collaborate. Encouraging them to express their feelings can help clear misunderstandings.
How would you handle a situation where a production team is dissatisfied with the maintenance response time?
How to Answer
- 1
Acknowledge their concerns and listen actively
- 2
Investigate the root causes of the delays
- 3
Communicate openly about current response times
- 4
Implement a system for prioritizing urgent requests
- 5
Follow up with the production team to provide updates
Example Answers
I would first acknowledge the production team's concerns and listen to their feedback. Then, I would investigate the reasons behind the response delays, whether it's staffing, equipment issues, or communication gaps. Open communication about our current workload and response prioritization would be key, and I'd implement a system for handling urgent maintenance requests more swiftly. Finally, I'd ensure to follow up with the team regularly to keep them informed of our progress.
What strategy would you use to manage your team's workload during peak production periods?
How to Answer
- 1
Prioritize tasks based on urgency and overall impact on production.
- 2
Communicate clearly with the team about expectations and deadlines.
- 3
Allocate resources effectively by balancing workloads among team members.
- 4
Implement a flexible schedule to accommodate increased demands.
- 5
Monitor progress regularly and adjust plans as needed.
Example Answers
I would prioritize our tasks by assessing which ones are critical for meeting production goals. Then, I would hold a meeting to communicate these priorities to the team, ensuring everyone understands their roles. I'd allocate tasks based on each member's strengths to maintain high productivity.
How would you approach implementing a new maintenance protocol that is met with resistance from your team?
How to Answer
- 1
Engage with the team to understand their concerns
- 2
Communicate the benefits and importance of the new protocol
- 3
Provide training and support to ease the transition
- 4
Encourage feedback and suggestions for improvement
- 5
Lead by example to show commitment to the new protocol
Example Answers
I would listen to my team's concerns about the new protocol and address them directly. I would explain how it benefits our efficiency and safety, and then provide training to ensure everyone is comfortable with the changes.
How would you respond to a maintenance emergency during off-hours?
How to Answer
- 1
Assess the situation quickly and determine the severity of the emergency.
- 2
Contact the appropriate team members or external services if needed.
- 3
Implement immediate measures to contain or mitigate the issue.
- 4
Communicate clearly with management and relevant personnel about the situation.
- 5
Document the incident and the actions taken for future reference.
Example Answers
In an off-hours emergency, I would first assess the situation to understand how severe it is. If it’s critical, I would call in the necessary team members or external contractors. After securing the area, I would keep management updated on the status and any actions taken to resolve the issue.
If your maintenance budget was cut, how would you adjust your planning to ensure essential maintenance is still performed?
How to Answer
- 1
Prioritize critical maintenance tasks and focus on safety and compliance.
- 2
Review and analyze current spending to identify non-essential expenses.
- 3
Implement a preventive maintenance schedule to reduce reactive maintenance needs.
- 4
Engage your team for ideas on cost-saving measures and efficient practices.
- 5
Consider alternative solutions such as training staff to handle multiple roles.
Example Answers
I would start by assessing which maintenance tasks are absolutely critical to ensure safety and compliance with regulations. Then, I'd look at our current budget to see where we can trim non-essential expenses. Implementing a stronger preventive maintenance plan could also reduce the number of emergency repairs needed.
Don't Just Read Maintenance Specialist Questions - Practice Answering Them!
Reading helps, but actual practice is what gets you hired. Our AI feedback system helps you improve your Maintenance Specialist interview answers in real-time.
Personalized feedback
Unlimited practice
Used by hundreds of successful candidates
Maintenance Specialist Position Details
Recommended Job Boards
CareerBuilder
www.careerbuilder.com/jobs/maintenance-specialistThese job boards are ranked by relevance for this position.
Related Positions
- Maintenance Repairer
- Maintenance Man
- Multi-Skilled Maintenance Engineer
- Maintenance Machinist
- Maintainer
- Grease Worker
- Machinist
- Hot Worker
- Car Greaser
- Machine Oiler
Similar positions you might be interested in.
Ace Your Next Interview!
Practice with AI feedback & get hired faster
Personalized feedback
Used by hundreds of successful candidates
Ace Your Next Interview!
Practice with AI feedback & get hired faster
Personalized feedback
Used by hundreds of successful candidates