Top 32 Maintenance Supervisor Interview Questions and Answers [Updated 2025]
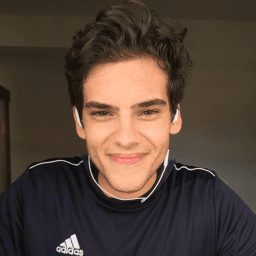
Andre Mendes
•
March 30, 2025
Are you preparing for a Maintenance Supervisor interview and unsure where to start? This blog post is your ultimate guide, featuring the most common interview questions tailored for this pivotal role. Dive into detailed example answers and insightful tips designed to help you respond with confidence and authority. Whether you're a seasoned professional or new to the field, enhance your interview readiness and stand out from the competition.
Download Maintenance Supervisor Interview Questions in PDF
To make your preparation even more convenient, we've compiled all these top Maintenance Supervisorinterview questions and answers into a handy PDF.
Click the button below to download the PDF and have easy access to these essential questions anytime, anywhere:
List of Maintenance Supervisor Interview Questions
Behavioral Interview Questions
Can you describe a time when you successfully led a maintenance team to complete a challenging project on time?
How to Answer
- 1
Identify a specific project with clear challenges
- 2
Outline your leadership role and contributions
- 3
Highlight team collaboration and problem-solving
- 4
Include measurable outcomes and results
- 5
Keep the focus on your actions and decisions
Example Answers
I led a team during an emergency generator installation project that was behind schedule. I coordinated daily meetings, assigning clear tasks based on team strengths. By implementing a strict timeline and adjusting workflows, we completed the project two days early, significantly improving operational readiness.
Tell me about a time when you encountered a serious mechanical failure. How did you approach the problem?
How to Answer
- 1
Start by briefly describing the mechanical failure and its impact.
- 2
Explain the immediate actions you took to assess the situation.
- 3
Discuss how you communicated with your team and stakeholders.
- 4
Outline the steps you took to resolve the issue and prevent recurrence.
- 5
Conclude with the results and what you learned from the experience.
Example Answers
In my previous role, our main conveyor belt failed during peak hours, halting production. I quickly gathered my team, assessed the damage, and communicated with management. We determined it was a worn-out motor, so I organized a temporary workaround while sourcing a replacement. The production resumed within three hours, and we later introduced regular maintenance checks to prevent future failures.
Don't Just Read Maintenance Supervisor Questions - Practice Answering Them!
Reading helps, but actual practice is what gets you hired. Our AI feedback system helps you improve your Maintenance Supervisor interview answers in real-time.
Personalized feedback
Unlimited practice
Used by hundreds of successful candidates
Describe an instance where you had to resolve a conflict between team members. What steps did you take?
How to Answer
- 1
Identify the specific conflict and the parties involved.
- 2
Explain your role in facilitating communication between team members.
- 3
Outline the steps you took to understand each person's perspective.
- 4
Describe how you helped them reach a resolution.
- 5
Mention the positive outcome that resulted from your intervention.
Example Answers
In my previous job, two technicians disagreed on the best method to complete a repair. I scheduled a meeting for them to air their views. I listened to both sides and encouraged them to collaborate. We reached a compromise that utilized both their ideas and improved our workflow.
Give an example of how you have communicated maintenance issues to non-technical staff or management.
How to Answer
- 1
Use simple language to explain technical issues
- 2
Focus on the impact of the issue on operations
- 3
Provide a clear solution or action plan
- 4
Offer to follow up for any questions
- 5
Use visuals or data if helpful to illustrate the problem
Example Answers
In my previous role, I noticed recurring HVAC issues affecting comfort levels in the office. I scheduled a brief meeting with the management team, explaining the problem in layman's terms, and discussed how it could impact employee productivity. I proposed a maintenance check and provided a timeline for resolution.
Describe a time when you had to adapt quickly to changes in maintenance procedures. How did you manage?
How to Answer
- 1
Identify a specific change that occurred in maintenance procedures.
- 2
Explain the impact of the change on operations or the team.
- 3
Describe the steps you took to adapt, including communication and training.
- 4
Highlight the positive outcomes resulting from your adaptation.
- 5
Reflect on what you learned and how it improved future processes.
Example Answers
In my previous role, our safety protocols were updated unexpectedly due to new regulations. I quickly organized a team meeting to inform everyone of the changes and initiated a training session to ensure compliance. This not only minimized disruptions but also enhanced our safety record, as all team members felt more confident in the new procedures.
Can you provide an example of how you evaluated your team's performance and provided feedback?
How to Answer
- 1
Use specific metrics or criteria for evaluation, such as project completion rates or quality of work.
- 2
Share a specific instance where you assessed performance, making it relatable.
- 3
Explain the feedback method, like one-on-one meetings or team reviews.
- 4
Emphasize the positive impact of your feedback on team motivation or performance.
- 5
Reflect on any adjustments made to improve team workflows based on evaluations.
Example Answers
In my previous role, I evaluated my team's performance by tracking equipment downtime and maintenance completion rates. During a weekly review, I noticed we had a delay in task execution, so I held one-on-one meetings to provide constructive feedback. This approach helped uncover issues and motivated team members to adopt better time management practices. As a result, our task completion rate improved by 20%.
Describe a time when you implemented a new process or technology that improved efficiency in maintenance.
How to Answer
- 1
Identify a specific process or technology you introduced.
- 2
Explain the problem it addressed in maintenance operations.
- 3
Share quantifiable results or improvements achieved.
- 4
Highlight teamwork or collaboration efforts if applicable.
- 5
Reflect on lessons learned and how it impacts future processes.
Example Answers
I introduced a computer maintenance management system to track work orders. This reduced response time by 30%. The team quickly adapted, leading to improved scheduling and less downtime on equipment.
Describe a time when you had to make a tough decision regarding maintenance operations. What was the process?
How to Answer
- 1
Use the STAR method: Situation, Task, Action, Result
- 2
Choose a specific incident that had significant impact
- 3
Explain your decision-making criteria and considerations
- 4
Highlight collaboration with team members and stakeholders
- 5
Emphasize the outcome and what you learned from the experience
Example Answers
In a situation where our main production line broke down, I had to decide whether to repair the existing equipment or invest in a new system. I assessed repair costs and downtime, consulted with my team, and determined that a new system would provide better long-term reliability. This decision resulted in a 30% increase in productivity and reduced maintenance costs over the next year.
Don't Just Read Maintenance Supervisor Questions - Practice Answering Them!
Reading helps, but actual practice is what gets you hired. Our AI feedback system helps you improve your Maintenance Supervisor interview answers in real-time.
Personalized feedback
Unlimited practice
Used by hundreds of successful candidates
Can you discuss an innovative solution you've implemented in maintenance that led to significant improvements?
How to Answer
- 1
Use the STAR method: Situation, Task, Action, Result.
- 2
Focus on a specific problem you identified.
- 3
Explain the innovative solution you introduced.
- 4
Quantify the improvements where possible.
- 5
Highlight any feedback from team members or management.
Example Answers
In my previous role, we faced frequent equipment downtime (Situation). I realized we lacked a predictive maintenance schedule (Task). I implemented a new system using IoT sensors to monitor equipment health in real-time (Action). As a result, we reduced downtime by 30% and saved the company over $50,000 annually (Result).
Technical Interview Questions
What are the standard maintenance procedures you follow for HVAC systems?
How to Answer
- 1
Begin with regular inspection and cleaning protocols.
- 2
Discuss preventative maintenance schedules and their importance.
- 3
Include specific tasks like changing filters and checking refrigerant levels.
- 4
Mention documentation practices for maintenance records.
- 5
Highlight safety checks and compliance with regulations.
Example Answers
I follow a strict schedule for inspecting and cleaning HVAC units quarterly, including changing filters and checking for refrigerant leaks to ensure efficiency.
What knowledge do you have of safety regulations pertaining to maintenance work?
How to Answer
- 1
Mention specific safety regulations like OSHA standards.
- 2
Highlight your experience with safety training programs.
- 3
Discuss your understanding of risk assessment protocols.
- 4
Provide examples of safety audits or inspections you've conducted.
- 5
Emphasize a proactive approach to maintaining a safe work environment.
Example Answers
I am well-versed in OSHA regulations, particularly related to equipment safety and personal protective equipment. In my previous role, I implemented a safety training program that reduced accidents by 30%.
Don't Just Read Maintenance Supervisor Questions - Practice Answering Them!
Reading helps, but actual practice is what gets you hired. Our AI feedback system helps you improve your Maintenance Supervisor interview answers in real-time.
Personalized feedback
Unlimited practice
Used by hundreds of successful candidates
How do you diagnose issues in heavy machinery? Can you describe your process?
How to Answer
- 1
Start with a visual inspection for obvious signs of wear or damage.
- 2
Use diagnostic tools like multimeters or pressure gauges for precision.
- 3
Follow a systematic approach, checking key systems in a logical order.
- 4
Document findings to track recurring issues and solutions.
- 5
Communicate clearly with your team about potential causes and fixes.
Example Answers
I begin with a thorough visual inspection of the machinery to identify any obvious signs of wear. Then, I use diagnostic tools to check the electrical and hydraulic systems while following a logical order to ensure nothing is missed. I document everything for future reference and share the insights with my team.
What maintenance management software are you familiar with, and how have you used it in your previous roles?
How to Answer
- 1
Identify specific software you have experience with, like CMMS or EAM.
- 2
Describe your role and responsibilities involving the software.
- 3
Highlight key functionalities you utilized, such as work order management or asset tracking.
- 4
Include any improvements or efficiencies you achieved using the software.
- 5
Be prepared to discuss any training you provided or received on the software.
Example Answers
I have extensive experience with CMMS software like Maintenance Connection. In my last role, I used it to track work orders and schedule preventive maintenance, which reduced downtime by 15%.
How do you conduct preventive maintenance planning, and what factors do you consider?
How to Answer
- 1
Identify critical equipment and their maintenance needs
- 2
Review historical maintenance data to prioritize actions
- 3
Develop a maintenance schedule that considers usage patterns
- 4
Engage with team members for insights and suggestions
- 5
Monitor compliance and adjust plans based on performance metrics
Example Answers
I start by identifying our critical equipment and reviewing their specific maintenance needs. I analyze historical maintenance records to prioritize tasks that often lead to issues, and then I create a schedule that aligns with equipment usage. I also involve team members to gather their insights and ensure all tasks are manageable. Finally, I regularly check our compliance with the plan and refine it based on our performance metrics.
Can you explain how you maintain electrical systems in industrial settings?
How to Answer
- 1
Detail your routine inspections and preventive maintenance schedule.
- 2
Highlight your experience with troubleshooting and diagnosing issues.
- 3
Mention compliance with safety and regulatory standards.
- 4
Discuss the tools you use for testing and monitoring systems.
- 5
Share examples of successful system upgrades or repairs you've implemented.
Example Answers
I maintain electrical systems by conducting weekly inspections and following a preventive maintenance schedule. I focus on identifying wear and tear before it became an issue, ensuring compliance with safety regulations, and using tools like multimeters for testing. For instance, I successfully upgraded our lighting system, which improved energy efficiency by 20%.
What is your experience with maintaining accurate maintenance records? Why is this important?
How to Answer
- 1
Highlight specific software or tools used for record-keeping
- 2
Mention how accurate records improve team efficiency and tracking
- 3
Explain how they assist in regulatory compliance and audits
- 4
Provide an example of a process improvement due to record accuracy
- 5
Emphasize ongoing training for team members on record management
Example Answers
In my previous role, I used CMMS software to maintain maintenance records, which improved our efficiency by 25%. Accurate records helped us track recurring issues and plan preventive maintenance effectively.
What steps do you take when troubleshooting a malfunctioning piece of equipment?
How to Answer
- 1
Identify the symptoms and gather information about the malfunction.
- 2
Check for simple issues like power supply or user errors first.
- 3
Refer to the equipment manual for troubleshooting tips specific to the model.
- 4
Isolate the problem area by systematically testing components.
- 5
Document findings and solutions for future reference.
Example Answers
First, I identify the symptoms and ask the operator about the issue. I then check basic problems like power supply or settings before consulting the manual. If needed, I isolate components to find the fault, and I document the process for our records.
What emerging technologies in maintenance do you think will impact the industry in the next few years?
How to Answer
- 1
Identify key technologies such as IoT and AI that are gaining traction.
- 2
Discuss the implications of predictive maintenance on operational costs.
- 3
Mention the role of automation in reducing manual tasks.
- 4
Consider the impact of mobile tools for on-site technicians.
- 5
Highlight the importance of data analytics in decision-making.
Example Answers
I believe IoT and AI will revolutionize maintenance by enabling predictive maintenance, which can significantly reduce downtime and costs.
How do you manage inventory for maintenance supplies to ensure you have the necessary materials?
How to Answer
- 1
Implement a digital inventory management system for real-time tracking
- 2
Conduct regular audits to identify usage trends and stock levels
- 3
Establish minimum stock levels for critical supplies
- 4
Work closely with suppliers for timely reordering and bulk discounts
- 5
Train staff on efficient materials usage to reduce waste
Example Answers
I utilize a digital inventory management system to track supplies in real time, ensuring we're updated on stock levels. Regular audits help us identify trends and adjust our orders accordingly. I also set minimum stock levels to prevent shortages.
Don't Just Read Maintenance Supervisor Questions - Practice Answering Them!
Reading helps, but actual practice is what gets you hired. Our AI feedback system helps you improve your Maintenance Supervisor interview answers in real-time.
Personalized feedback
Unlimited practice
Used by hundreds of successful candidates
Situational Interview Questions
If an unexpected equipment failure occurs during peak operation hours, how would you handle the situation?
How to Answer
- 1
Stay calm and assess the situation quickly
- 2
Communicate with your team and inform them of the issue
- 3
Implement a temporary solution if possible to minimize downtime
- 4
Notify relevant stakeholders about the situation
- 5
Document the incident for future reference and improvement
Example Answers
I would first assess the extent of the equipment failure, ensuring safety is prioritized. Then, I would communicate with my team to explain the situation and delegate immediate tasks to minimize downtime. After that, I'd implement a temporary fix while keeping stakeholders updated on our progress.
Imagine you have a limited budget for maintenance supplies. How would you prioritize your purchases?
How to Answer
- 1
Assess the critical needs for safety and compliance first
- 2
Evaluate the highest frequency of use items that impact operations
- 3
Consider the shelf life and availability of supplies to avoid shortages
- 4
Prioritize items that can prevent costly downtime or repairs
- 5
Maintain an inventory list to avoid unnecessary purchases and track usage
Example Answers
I would first prioritize items that are essential for safety, such as personal protective equipment. Next, I would focus on high-use supplies that keep equipment operational, like lubricants and cleaning agents. I would also ensure I have backups of critical components to prevent downtime.
Don't Just Read Maintenance Supervisor Questions - Practice Answering Them!
Reading helps, but actual practice is what gets you hired. Our AI feedback system helps you improve your Maintenance Supervisor interview answers in real-time.
Personalized feedback
Unlimited practice
Used by hundreds of successful candidates
If a team member is not performing well, what steps would you take to address this issue?
How to Answer
- 1
Identify specific performance issues through observation and feedback.
- 2
Schedule a one-on-one meeting to discuss the concerns privately.
- 3
Listen to the team member's perspective to understand any underlying issues.
- 4
Set clear expectations and provide necessary resources or training.
- 5
Monitor progress regularly and provide constructive feedback.
Example Answers
I would first observe the team member's work to identify specific issues and then hold a private meeting to discuss my observations. I would listen to their side and understand any challenges they might be facing, before setting clear expectations and providing any support they need.
How would you approach planning a major overhaul of an aging facility’s maintenance systems?
How to Answer
- 1
Conduct a comprehensive assessment of the current maintenance systems.
- 2
Identify the key areas that require upgrades and prioritize them based on criticality.
- 3
Engage with staff to gather input and insights on current issues and suggestions.
- 4
Develop a phased implementation plan with timelines and budget considerations.
- 5
Establish metrics to evaluate the success of the overhaul after completion.
Example Answers
First, I would assess the current maintenance systems to pinpoint weaknesses. Then, I'd prioritize upgrades based on the most critical areas. Collaborating with staff would be essential to understand their needs fully. I'd set up a phased plan to manage the overhaul effectively, ensuring we stay within budget. Finally, I would implement metrics to measure the success of the new systems.
What actions would you take if you discovered safety violations during a routine inspection?
How to Answer
- 1
Identify and document the specific safety violations immediately
- 2
Assess the severity of each violation and prioritize them based on risk
- 3
Communicate the findings to relevant stakeholders, including management and affected staff
- 4
Implement corrective actions or temporary measures to mitigate immediate risks
- 5
Follow up to ensure compliance and consider additional training if necessary
Example Answers
If I found safety violations, I'd document them thoroughly, evaluate their risk level, inform my supervisor promptly, take immediate steps to fix critical issues, and plan a follow-up inspection to ensure compliance.
If you need to cut costs in maintenance, what strategies would you implement to maintain service quality?
How to Answer
- 1
Assess current maintenance practices to identify inefficiencies
- 2
Implement a preventive maintenance schedule to reduce emergency repairs
- 3
Utilize data analytics for better resource allocation and decision-making
- 4
Train staff to enhance skills and improve productivity
- 5
Foster vendor relationships for better pricing on supplies and services
Example Answers
I would start by reviewing our existing maintenance schedules to find areas where we can be more efficient. Implementing preventive maintenance would reduce downtime and emergency costs, allowing us to maintain service quality while cutting expenses.
How would you handle a situation where your team disagrees on the best method to complete a maintenance task?
How to Answer
- 1
Encourage open dialogue among team members to express their opinions.
- 2
Assess each proposed method based on safety, efficiency, and costs.
- 3
Facilitate a group discussion to weigh the pros and cons of each approach.
- 4
Seek input from relevant stakeholders or experts if necessary.
- 5
Make a decision based on the consensus or lead with a clear rationale.
Example Answers
I would first bring the team together to discuss their different ideas openly. Then, I would evaluate the methods against our safety standards and efficiency needs to determine the best approach.
If you have to select a vendor for maintenance supplies, what criteria would you use to make your decision?
How to Answer
- 1
Evaluate the vendor's reliability and track record in delivery times.
- 2
Compare pricing to ensure it fits within the budget without compromising quality.
- 3
Assess the range of products offered to ensure they meet all maintenance needs.
- 4
Check for customer service responsiveness and support availability.
- 5
Review supplier certifications and compliance with industry standards.
Example Answers
I would select a vendor based on their reliability, product range, and pricing. I look for firms with a proven track record of timely deliveries and quality products that fit our maintenance needs.
If you were tasked with training new hires in maintenance, what key areas would you focus on?
How to Answer
- 1
Emphasize safety protocols and standards to prevent accidents.
- 2
Teach basic troubleshooting techniques for common equipment issues.
- 3
Include hands-on training with tools and machinery they will use.
- 4
Stress the importance of preventive maintenance practices.
- 5
Incorporate an overview of documentation and reporting processes.
Example Answers
I would start with safety protocols, ensuring that new hires understand the risks and proper procedures. Next, I'd teach troubleshooting methods for everyday equipment issues, followed by hands-on practice with tools. Preventive maintenance practices would be emphasized, alongside how to document their work effectively.
How would you manage your time and resources if multiple urgent maintenance requests come in at once?
How to Answer
- 1
Prioritize requests based on severity and impact on operations
- 2
Communicate with your team to delegate tasks efficiently
- 3
Use a tracking system to monitor progress of all requests
- 4
Stay calm and focused to manage stress during busy times
- 5
Follow up after resolution to ensure satisfaction and prevent recurrence
Example Answers
I would first assess each request and prioritize them based on their urgency and impact on operations. Then, I would delegate tasks to my team based on their strengths, while keeping a tracking system updated to monitor progress.
Don't Just Read Maintenance Supervisor Questions - Practice Answering Them!
Reading helps, but actual practice is what gets you hired. Our AI feedback system helps you improve your Maintenance Supervisor interview answers in real-time.
Personalized feedback
Unlimited practice
Used by hundreds of successful candidates
If you received negative feedback from your supervisors, how would you respond and address the issues?
How to Answer
- 1
Stay calm and listen to the feedback without becoming defensive
- 2
Acknowledge the feedback and express gratitude for the opportunity to improve
- 3
Ask for specific examples of the issues to understand them better
- 4
Develop an action plan to address the feedback and discuss it with your supervisor
- 5
Follow up on your progress and seek additional feedback regularly
Example Answers
I would take the feedback seriously, thank my supervisor for their thoughts, and ask for specific instances to understand how I can improve. Then, I would create a plan to address those issues and check in regularly to ensure I'm on the right track.
Maintenance Supervisor Position Details
Salary Information
Recommended Job Boards
Cushman & Wakefield Careers
careers.cushmanwakefield.com/en/jobs/r239785/maintenance-supervisor-multifamilyCareerBuilder
www.careerbuilder.com/jobs-maintenance-supervisorZipRecruiter
www.ziprecruiter.com/Jobs/Maintenance-SupervisorThese job boards are ranked by relevance for this position.
Related Positions
Ace Your Next Interview!
Practice with AI feedback & get hired faster
Personalized feedback
Used by hundreds of successful candidates
Ace Your Next Interview!
Practice with AI feedback & get hired faster
Personalized feedback
Used by hundreds of successful candidates