Top 30 Manufacturing Operations Manager Interview Questions and Answers [Updated 2025]
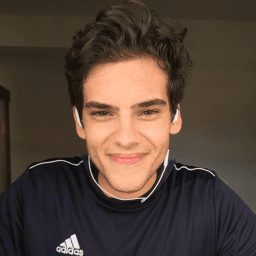
Andre Mendes
•
March 30, 2025
Navigating the competitive landscape of manufacturing operations management requires thorough preparation, especially when it comes to interviews. This blog post equips aspiring managers with the most common interview questions for the Manufacturing Operations Manager role, complete with example answers and strategic tips. Whether you're a seasoned professional or new to the field, these insights will help you articulate your experience and expertise effectively, setting you up for success.
Download Manufacturing Operations Manager Interview Questions in PDF
To make your preparation even more convenient, we've compiled all these top Manufacturing Operations Managerinterview questions and answers into a handy PDF.
Click the button below to download the PDF and have easy access to these essential questions anytime, anywhere:
List of Manufacturing Operations Manager Interview Questions
Behavioral Interview Questions
Can you describe a time when you successfully led a team through a challenging project or transition in manufacturing operations?
How to Answer
- 1
Choose a specific project or transition that had clear challenges.
- 2
Outline your role and responsibilities in the project.
- 3
Highlight key actions you took to lead the team effectively.
- 4
Discuss measurable outcomes or results of the project.
- 5
Reflect on what you learned and how it improved future operations.
Example Answers
In my last position, I led the transition to a new production line that improved efficiency. The team faced delays due to equipment failures. I organized daily huddles to address roadblocks, reallocated resources, and ensured clear communication. As a result, we launched the line two weeks early, increasing output by 15%.
Tell me about a time when you identified a significant operational issue on the manufacturing floor. How did you address it?
How to Answer
- 1
Start with a specific example highlighting the operational issue.
- 2
Describe how you identified the issue using data or observation.
- 3
Explain the steps you took to analyze the problem and develop a solution.
- 4
Share the outcome and what you learned from the experience.
- 5
Keep it concise and focused on your actions and results.
Example Answers
At my previous job, I noticed a consistent delay in our assembly line due to parts being misplaced. I used the production logs to pinpoint the most frequent error points and collaborated with the team to implement a better parts tracking system. This reduced our delays by 30% within a month, improving overall efficiency.
Don't Just Read Manufacturing Operations Manager Questions - Practice Answering Them!
Reading helps, but actual practice is what gets you hired. Our AI feedback system helps you improve your Manufacturing Operations Manager interview answers in real-time.
Personalized feedback
Unlimited practice
Used by hundreds of successful candidates
Describe an experience where you successfully reduced costs in manufacturing operations without compromising quality.
How to Answer
- 1
Identify a specific project or initiative where cost reduction was a goal.
- 2
Clearly explain the methods or strategies you implemented to reduce costs.
- 3
Emphasize how you ensured quality was maintained during the process.
- 4
Mention any measurable results or impact from your actions.
- 5
Be prepared to discuss challenges faced and how you overcame them.
Example Answers
At my previous job, I led a project to streamline our supply chain. By negotiating with suppliers for better rates and consolidating orders, we reduced material costs by 15%. I implemented regular quality checks, ensuring that overall quality remained high, which resulted in increased customer satisfaction.
Can you give an example of how you have motivated a team during a period of low morale?
How to Answer
- 1
Identify a specific instance of low morale in your team.
- 2
Describe the actions you took to address the situation.
- 3
Highlight the importance of communication with the team.
- 4
Share the positive outcomes that resulted from your actions.
- 5
Emphasize the lessons learned and how they shaped your management style.
Example Answers
In my previous role, our manufacturing team was facing low morale due to a tight project deadline. I organized daily stand-up meetings to discuss concerns and celebrate small wins. This open communication helped the team feel heard and appreciated, leading to an improvement in productivity by 20%.
Tell me about a time when you worked with other departments to improve manufacturing operations. What was the outcome?
How to Answer
- 1
Choose a specific project that involved cross-departmental collaboration.
- 2
Highlight your role and contributions in that project.
- 3
Focus on the challenge you faced and the solution you implemented.
- 4
Mention measurable outcomes or improvements achieved.
- 5
End with what you learned from the experience.
Example Answers
In my last role, I coordinated with the quality assurance and logistics departments to address a backlog in product shipments. We identified that quality checks were delaying dispatch. I implemented a streamlined quality assurance process that reduced inspection time by 30%. As a result, we cleared the backlog and improved customer satisfaction scores.
Provide an example of how you have fostered a culture of continuous improvement in a manufacturing setting.
How to Answer
- 1
Describe a specific initiative or program you led.
- 2
Explain how you involved team members in the process.
- 3
Share measurable results or improvements achieved.
- 4
Discuss training or tools you implemented to support the initiative.
- 5
Mention how you maintained momentum for continuous improvement.
Example Answers
In my last role, I implemented a Kaizen program where I encouraged all employees to submit improvement ideas. We held monthly meetings to discuss submissions and track progress. This led to a 15% reduction in waste over six months.
Describe a situation where your communication skills were crucial in managing manufacturing operations.
How to Answer
- 1
Think of a specific situation that illustrates your communication skills.
- 2
Highlight how you communicated with different teams or stakeholders.
- 3
Explain the impact of your communication on the outcome of the situation.
- 4
Use the STAR method: Situation, Task, Action, Result.
- 5
Keep it concise and focused on your role in the communication.
Example Answers
In a recent project, our production line was facing delays due to miscommunication between departments. I organized a cross-department meeting, clearly outlining the timeline and expectations. This led to improved cooperation and we met our production targets ahead of schedule.
Can you discuss a time when you managed change in a manufacturing environment? How did you ensure a smooth transition?
How to Answer
- 1
Identify a specific change initiative you led or were involved in.
- 2
Describe the challenges faced during the change and how you addressed them.
- 3
Highlight the communication strategies you used to engage your team.
- 4
Mention the tools or processes you implemented to support the transition.
- 5
Share the outcomes or improvements that resulted from the change.
Example Answers
In a previous role, we transitioned from manual to automated inventory management. I identified resistance among staff, so I held workshops to explain the benefits. We implemented new software in phases, allowing feedback, which helped us adjust the process. As a result, our inventory accuracy improved by 25%.
Tell me about a significant project you managed in manufacturing. What challenges did you face and how did you overcome them?
How to Answer
- 1
Choose a relevant project that showcases your skills in manufacturing management.
- 2
Clearly outline the project's goals and your specific role in it.
- 3
Identify key challenges faced during the project and their impact.
- 4
Discuss the strategies and actions you took to overcome these challenges.
- 5
Conclude with the successful outcome and any lessons learned.
Example Answers
In my last position, I managed a project to implement lean manufacturing processes in our assembly line. The main challenge was resistance to change from the team. I overcame this by organizing workshops that demonstrated the benefits of lean principles and involving team members in the process design, which led to a 15% increase in efficiency.
Describe a situation where you introduced an innovative solution to improve manufacturing efficiency.
How to Answer
- 1
Start with a specific challenge your team faced
- 2
Explain the innovative solution you proposed
- 3
Detail the steps you took to implement the solution
- 4
Share the measurable outcomes of the implementation
- 5
Emphasize teamwork and collaboration in your example
Example Answers
In my previous role, we faced high downtime due to machine failures. I proposed implementing a predictive maintenance system using IoT sensors. I led the team in selecting the right technology, training staff on the new system, and integrating it into our workflow. As a result, we reduced downtime by 30% over six months, significantly improving our production line efficiency.
Don't Just Read Manufacturing Operations Manager Questions - Practice Answering Them!
Reading helps, but actual practice is what gets you hired. Our AI feedback system helps you improve your Manufacturing Operations Manager interview answers in real-time.
Personalized feedback
Unlimited practice
Used by hundreds of successful candidates
Technical Interview Questions
What methodologies do you use for process improvement in manufacturing, and can you give an example of how you've applied them?
How to Answer
- 1
Identify key methodologies like Lean, Six Sigma, or Kaizen.
- 2
Choose a specific example that demonstrates your application of these methodologies.
- 3
Explain the problem you faced and the methodology used to solve it.
- 4
Highlight measurable outcomes or improvements resulting from your actions.
- 5
Keep your answer structured: situation, task, action, result (STAR).
Example Answers
In my role, I utilized Lean methodology to reduce waste in our assembly line. We identified excess movement as a major issue, applied 5S principles, and reorganized the workspace. This led to a 20% increase in throughput within three months.
What is lean manufacturing, and how have you implemented lean principles in previous roles?
How to Answer
- 1
Define lean manufacturing briefly and its goals like waste reduction.
- 2
Highlight specific lean tools or methodologies you've used, such as 5S or Kaizen.
- 3
Provide a clear example of a successful implementation from your past experience.
- 4
Mention the outcomes or improvements achieved through lean practices.
- 5
Be prepared to discuss challenges faced during implementation and how you addressed them.
Example Answers
Lean manufacturing focuses on minimizing waste while maximizing productivity. In my previous role, I implemented 5S in the assembly line, which organized our workspace and improved efficiency by 20%.
Don't Just Read Manufacturing Operations Manager Questions - Practice Answering Them!
Reading helps, but actual practice is what gets you hired. Our AI feedback system helps you improve your Manufacturing Operations Manager interview answers in real-time.
Personalized feedback
Unlimited practice
Used by hundreds of successful candidates
How do you ensure compliance with safety standards and regulations in a manufacturing environment?
How to Answer
- 1
Conduct regular safety training for all employees and ensure they understand protocols
- 2
Establish a system for reporting and addressing safety violations or concerns
- 3
Implement regular audits of safety practices and equipment to ensure compliance
- 4
Keep up-to-date with local and federal safety regulations and update policies accordingly
- 5
Encourage a culture of safety where employees can voice concerns and suggest improvements.
Example Answers
I ensure compliance by conducting regular safety training sessions that cover our protocols and regulations. Additionally, I maintain an open-door policy for employees to report any safety concerns.
What quality control techniques are you familiar with, and how do you implement them in your operations?
How to Answer
- 1
Identify specific quality control techniques like Six Sigma, SPC, or FMEA.
- 2
Discuss how you apply these techniques in daily operations.
- 3
Provide examples of measurable outcomes or improvements.
- 4
Mention any tools or software you use for quality control monitoring.
- 5
Highlight the importance of team training and communication.
Example Answers
I am familiar with Six Sigma and Statistical Process Control. I implement Six Sigma by training teams to identify defects and reduce variability in our processes. For instance, we improved our defect rate by 30% in the last year by applying these principles.
What factors do you consider essential when creating a production plan for a manufacturing facility?
How to Answer
- 1
Identify production capacity and constraints of the facility
- 2
Consider lead times for materials and resources
- 3
Account for workforce availability and skills
- 4
Incorporate quality control measures into the plan
- 5
Ensure flexibility to adapt to changes in demand
Example Answers
When creating a production plan, I first assess the facility's production capacity and identify any constraints. This helps in aligning the output with the available resources and equipment. Next, I factor in lead times for materials to ensure everything is available when needed. I also look into workforce availability and ensure that we have the right skills in place. Importantly, I incorporate quality checks to maintain our standards throughout the process. Finally, I aim to build flexibility into the plan to quickly adapt to shifting market demands.
How have you used ERP systems to enhance manufacturing operations, and which systems are you proficient with?
How to Answer
- 1
Identify specific ERP systems you have used, such as SAP, Oracle, or Microsoft Dynamics.
- 2
Explain how you implemented the ERP system to improve production efficiency or inventory management.
- 3
Provide examples of data analysis or reporting you conducted using the ERP.
- 4
Discuss any training you organized or provided for staff regarding the ERP use.
- 5
Mention quantifiable outcomes, such as reduced waste or increased production speed.
Example Answers
In my previous role, I used SAP to streamline our production scheduling. By implementing automated workflows, we reduced lead time by 15%.
What is capacity planning, and how do you ensure optimal capacity utilization in manufacturing?
How to Answer
- 1
Define capacity planning clearly in brief terms.
- 2
Discuss tools or methods you use for capacity planning.
- 3
Explain how you assess current utilization rates.
- 4
Mention the importance of forecasting demand.
- 5
Provide examples of adjustments made to meet capacity needs.
Example Answers
Capacity planning is the process of determining the production capacity needed to meet changing demands for products. I use tools like capacity requirement planning (CRP) to assess machine and labor availability. I also monitor utilization rates regularly and adjust shifts or schedules based on sales forecasts to ensure we meet demand without overproducing.
How do you approach production scheduling to balance efficiency and flexibility?
How to Answer
- 1
Assess current production capacity and demand forecasts.
- 2
Utilize scheduling software to optimize resource allocation.
- 3
Implement buffer times for unforeseen disruptions.
- 4
Engage with team members for input on scheduling challenges.
- 5
Continuously review and adjust schedules based on performance metrics.
Example Answers
I analyze demand forecasts against production capacity to create an initial schedule. I use scheduling software to allocate resources efficiently and include buffer time to address any disruptions. Regular check-ins with my team help to adapt our approach as needed.
What role do you believe automation plays in modern manufacturing, and how have you implemented it?
How to Answer
- 1
Highlight the benefits of automation such as efficiency, safety, and quality control.
- 2
Provide a specific example of automation you've implemented in past roles.
- 3
Discuss how automation has improved production processes in your experience.
- 4
Mention any relevant technologies or systems you've used in automation.
- 5
Emphasize your approach to integrating automation with existing workflows.
Example Answers
I believe automation is crucial for enhancing efficiency and reducing human error in manufacturing. At my previous job, I led a project to implement a robotic assembly line, which increased our production speed by 30% and improved product consistency. We used a combination of PLCs and robotics to streamline the assembly process, which also increased worker safety.
How do you manage workforce scheduling and labor efficiency in a manufacturing setting?
How to Answer
- 1
Utilize workforce management software for real-time scheduling.
- 2
Implement cross-training to enhance flexibility in staffing.
- 3
Analyze production data to optimize labor allocation.
- 4
Communicate clearly with staff about scheduling changes.
- 5
Gather feedback from workers to improve scheduling practices.
Example Answers
I use workforce management software to create schedules based on real-time production needs, allowing for adjustments as necessary. This approach helps optimize our staffing levels and ensures we maintain high labor efficiency.
Don't Just Read Manufacturing Operations Manager Questions - Practice Answering Them!
Reading helps, but actual practice is what gets you hired. Our AI feedback system helps you improve your Manufacturing Operations Manager interview answers in real-time.
Personalized feedback
Unlimited practice
Used by hundreds of successful candidates
Situational Interview Questions
Imagine you have two team members who disagree on the approach to a production process. How would you handle the situation?
How to Answer
- 1
Listen to both team members' perspectives without interruption.
- 2
Encourage them to explain their approaches and provide reasoning.
- 3
Facilitate a discussion to find common ground between the two ideas.
- 4
Consider the impact of each approach on productivity and quality.
- 5
Make a decision based on collective input, emphasizing teamwork.
Example Answers
I would first listen to both team members separately to understand their views. Then, I would bring them together to discuss their ideas openly and facilitate a conversation to find common ground. I would analyze both approaches based on our production goals and choose the best one, ensuring that they feel valued in the decision-making process.
Suppose a key supplier suddenly fails to deliver a critical component. What steps would you take to mitigate the impact on production?
How to Answer
- 1
Assess the situation immediately to understand the impact on production schedules
- 2
Contact alternative suppliers who can provide the critical component
- 3
Communicate with internal teams to update them on potential delays and adjust plans
- 4
Explore temporary in-house solutions to substitute the missing component
- 5
Implement a risk management strategy to establish better contingency plans for the future
Example Answers
I would first assess the immediate impact on production and identify which parts of the operation would be affected. Then, I'd reach out to approved alternative suppliers to source the critical component. Keeping all relevant departments informed is crucial, so I would communicate with the production team to adjust our schedules accordingly and minimize downtime. Additionally, I would explore any in-house alternatives we could use temporarily while we resolve the supply issue. Finally, I would initiate a review of our supplier risk management practices to ensure we're better prepared next time.
Don't Just Read Manufacturing Operations Manager Questions - Practice Answering Them!
Reading helps, but actual practice is what gets you hired. Our AI feedback system helps you improve your Manufacturing Operations Manager interview answers in real-time.
Personalized feedback
Unlimited practice
Used by hundreds of successful candidates
If a major piece of equipment breaks down unexpectedly, what would your immediate priorities be?
How to Answer
- 1
Ensure safety protocols are followed to protect staff and equipment
- 2
Assess the situation to determine the extent of the breakdown
- 3
Communicate with the team and relevant stakeholders promptly
- 4
Prioritize critical operations and allocate resources for quick repairs
- 5
Document the incident for future reference and analysis
Example Answers
My first priority would be to ensure everyone's safety and to follow safety protocols. Then, I would quickly assess the breakdown to understand its impact on operations. Communication with my team and management would be crucial to keep everyone informed. Next, I would focus on mobilizing resources for repairs while prioritizing essential production tasks. Lastly, I would document what happened to improve our response for future incidents.
You have limited resources and competing demands from different departments. How would you prioritize and allocate resources?
How to Answer
- 1
Assess the impact of each demand on overall business goals
- 2
Engage with department heads to understand their needs
- 3
Use data to evaluate performance and resource utilization
- 4
Prioritize based on urgency and strategic alignment
- 5
Communicate decisions clearly and transparently to all stakeholders
Example Answers
I would start by reviewing each department's request and assessing how they align with our strategic goals. Then, I'd consult with department heads to gather more insights and determine which projects are most critical. Finally, I'd allocate resources to the areas that will yield the highest impact while ensuring clear communication to manage expectations.
Imagine the company is considering adopting a new technology. How would you evaluate its potential impact on your operations?
How to Answer
- 1
Identify the goals of the new technology and how it aligns with current operations.
- 2
Analyze cost implications including initial investment and ongoing expenses.
- 3
Assess how it will affect productivity, quality, and employee roles.
- 4
Gather input from team members and stakeholders for broader perspective.
- 5
Consider a pilot implementation to test its effectiveness before full rollout.
Example Answers
First, I would clarify the objectives of the technology and see if they align with our operational goals. Then, I would conduct a cost-benefit analysis to evaluate the financial impact, followed by an assessment of how it might affect productivity and employee workflows. Finally, I would involve my team in discussions to gather their insights and possibly run a pilot test.
An employee's performance is not meeting expectations. How would you address this issue?
How to Answer
- 1
Identify specific performance issues with examples
- 2
Schedule a private meeting to discuss concerns
- 3
Use a constructive tone and express your willingness to help
- 4
Collaboratively set improvement goals and a timeline
- 5
Follow up regularly to track progress and provide support
Example Answers
I would meet with the employee to discuss the specific areas where their performance is lacking, providing clear examples. Together, we would identify goals and set a timeline for improvement, ensuring they know I am here to support them along the way.
A new regulation impacts your manufacturing process. How would you ensure compliance quickly and effectively?
How to Answer
- 1
Identify the key aspects of the new regulation and how they affect your operations.
- 2
Engage with your compliance team and key stakeholders for input and expertise.
- 3
Develop a clear action plan that outlines necessary changes and timelines.
- 4
Implement training sessions for staff to ensure everyone understands the new requirements.
- 5
Monitor compliance continuously and adjust processes as needed to stay aligned with the regulation.
Example Answers
I would first analyze the new regulation to understand its requirements and impacts on our processes. Next, I would consult with our compliance team to gather insights and develop a strategic action plan. After that, I would organize training sessions for our staff to ensure they are fully informed and prepared for the changes. Finally, I would set up a monitoring system to ensure ongoing compliance and make adjustments as necessary.
If a batch of products fails quality inspection, what corrective actions would you take?
How to Answer
- 1
Analyze the failure to identify root causes
- 2
Review quality control processes and inspection criteria
- 3
Engage the production team to gather insights
- 4
Implement corrective actions like rework or re-inspection
- 5
Document the issue and corrective measures for future reference
Example Answers
I would first analyze the reason for the failure by examining inspection reports and gathering feedback from the team. Then, I would assess the quality control processes and make necessary adjustments. If needed, I would implement rework procedures to meet quality standards before re-inspection, ensuring the process is documented for future improvements.
How would you adjust operations if there was a sudden change in customer demand?
How to Answer
- 1
Assess the current inventory levels to identify surplus or shortfall.
- 2
Analyze production capacity and determine if it can be scaled up or down swiftly.
- 3
Engage with the sales and marketing teams for insights on demand forecasts.
- 4
Implement flexible scheduling to adapt workforce shifts as needed.
- 5
Establish contingency plans to quickly respond to fluctuations in demand.
Example Answers
I would first evaluate our current inventory to see if we have enough stock or if we need to ramp up production. Then, I would work closely with the sales team to understand the demand spikes. Based on that, I would adjust production schedules and consider overtime or temporary staff to meet the new demand.
A natural disaster disrupts your supply chain. What steps would you take to ensure continued production?
How to Answer
- 1
Assess immediate impact on materials and resources
- 2
Communicate with suppliers for alternative arrangements
- 3
Implement a contingency plan for critical components
- 4
Re-evaluate inventory levels and adjust production schedules
- 5
Keep stakeholders informed about changes and updates
Example Answers
First, I would assess the extent of the disruption by communicating with our suppliers to understand what materials are affected. Next, I would activate our contingency plan to source critical components from alternative suppliers to maintain production. I would also adjust our production schedule based on current inventory levels and keep all stakeholders informed about our strategy.
Don't Just Read Manufacturing Operations Manager Questions - Practice Answering Them!
Reading helps, but actual practice is what gets you hired. Our AI feedback system helps you improve your Manufacturing Operations Manager interview answers in real-time.
Personalized feedback
Unlimited practice
Used by hundreds of successful candidates
Manufacturing Operations Manager Position Details
Recommended Job Boards
These job boards are ranked by relevance for this position.
Related Positions
Ace Your Next Interview!
Practice with AI feedback & get hired faster
Personalized feedback
Used by hundreds of successful candidates
Ace Your Next Interview!
Practice with AI feedback & get hired faster
Personalized feedback
Used by hundreds of successful candidates