Top 31 Manufacturing Supervisor Interview Questions and Answers [Updated 2025]
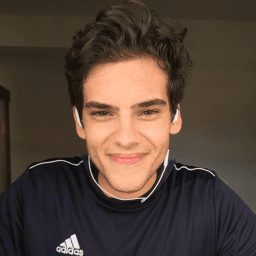
Andre Mendes
•
March 30, 2025
Navigating the path to becoming a successful Manufacturing Supervisor begins with acing the interview, and we're here to help you do just that. In this post, we've compiled the most common interview questions for the Manufacturing Supervisor role, complete with example answers and tips to respond effectively. Whether you're a seasoned professional or new to the field, this guide will equip you with the insights needed to impress your interviewers and secure the position.
Download Manufacturing Supervisor Interview Questions in PDF
To make your preparation even more convenient, we've compiled all these top Manufacturing Supervisorinterview questions and answers into a handy PDF.
Click the button below to download the PDF and have easy access to these essential questions anytime, anywhere: