Top 31 Mixing Operator Interview Questions and Answers [Updated 2025]
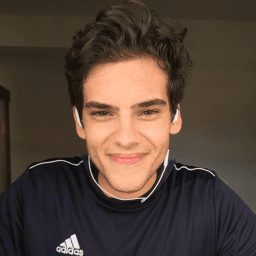
Andre Mendes
•
March 30, 2025
Preparing for a Mixing Operator interview? This blog post is your ultimate guide to acing it with confidence. Dive into a curated list of the most common interview questions for the role, complete with example answers and expert tips on crafting your responses effectively. Whether you're a seasoned professional or new to the field, this resource will help you impress your interviewers and secure the job.
Download Mixing Operator Interview Questions in PDF
To make your preparation even more convenient, we've compiled all these top Mixing Operatorinterview questions and answers into a handy PDF.
Click the button below to download the PDF and have easy access to these essential questions anytime, anywhere:
List of Mixing Operator Interview Questions
Behavioral Interview Questions
How have you communicated process changes to your team? Can you provide an example?
How to Answer
- 1
Explain the context of the process change briefly
- 2
Describe how you informed the team about the changes
- 3
Highlight any tools or methods you used for communication
- 4
Discuss how you encouraged feedback from the team
- 5
Share the outcome of the change and any improvements observed
Example Answers
In my last role, we needed to switch to a new mixing formula. I held a team meeting to explain the reason for the change and shared a detailed document outlining the new process. We used a shared online platform for updates, and I encouraged everyone to ask questions. After implementing the change, we noticed a 15% increase in product consistency.
Don't Just Read Mixing Operator Questions - Practice Answering Them!
Reading helps, but actual practice is what gets you hired. Our AI feedback system helps you improve your Mixing Operator interview answers in real-time.
Personalized feedback
Unlimited practice
Used by hundreds of successful candidates
Tell me about a time when you took initiative to improve a mixing process.
How to Answer
- 1
Think of a specific instance where you noticed a problem.
- 2
Describe the solution you proposed or implemented.
- 3
Include any positive outcomes from your initiative.
- 4
Keep your answer structured: Situation, Task, Action, Result.
- 5
Emphasize any teamwork or collaboration that occurred.
Example Answers
In my previous job, I noticed that our mixing times were inconsistent, affecting product quality. I proposed a new standardized procedure for mixing based on batch size, which we tested and found improved consistency. After implementation, our quality control complaints dropped by 30%.
Describe a time when you had to learn a new mixing technique or technology quickly.
How to Answer
- 1
Select a specific instance with clear learning objectives
- 2
Explain the resource you used to learn, like manuals or tutorials
- 3
Describe the challenge faced and how you overcame it
- 4
Highlight the outcome and any feedback received
- 5
Keep it focused on your adaptability and willingness to learn
Example Answers
In my previous job, I had to learn a new automated mixing control system within a week. I used the user manual and online video tutorials to get up to speed. Initially, I struggled with the interface, but I practiced during downtime and asked a colleague for tips. By the end of the week, I was able to operate it confidently and received positive feedback from my supervisor.
Can you provide an example of receiving feedback on your mixing work? How did you react?
How to Answer
- 1
Choose a specific instance where you received feedback.
- 2
Explain the feedback clearly and objectively.
- 3
Describe your initial reaction honestly.
- 4
Discuss how you applied the feedback to improve your work.
- 5
Mention any positive outcomes from applying the feedback.
Example Answers
In my previous role, I received feedback from my supervisor that my mix was too bass-heavy. Initially, I felt defensive because I thought I had done a good job. However, I took a step back, listened to the recording again, and adjusted the levels based on the feedback. After revising the mix, my supervisor praised the new version for its clarity and balance.
Discuss a time when you met or exceeded a mixing objective. What helped you achieve that?
How to Answer
- 1
Identify a specific mixing objective you achieved.
- 2
Describe the steps you took to meet that objective.
- 3
Highlight any challenges you encountered and how you overcame them.
- 4
Mention any teamwork or communication that contributed to your success.
- 5
Conclude with the results and what you learned from the experience.
Example Answers
In my last position as a Mixing Operator, we had a target to reduce mixing time by 10%. I collaborated with my team to streamline our process by adjusting mixer speeds and batch timings. We faced some initial resistance, but through effective communication, we reached our goal ahead of schedule, decreasing time by 15%. This taught me the importance of teamwork and flexible problem-solving.
Can you describe a situation where you worked closely with a team to achieve a mixing goal?
How to Answer
- 1
Choose a specific project where teamwork was essential.
- 2
Highlight your role and contributions to the team's efforts.
- 3
Explain the goal you were trying to achieve and the mixing process involved.
- 4
Discuss any challenges faced and how the team overcame them.
- 5
Conclude with the outcome and what you learned from the experience.
Example Answers
In my previous job at XYZ Company, we had a project where we needed to mix a new product formula. I collaborated with three coworkers, each responsible for different ingredients. My role was to measure the components accurately and ensure we followed the mixing protocol. We faced timing challenges, but by improving our communication and dividing tasks efficiently, we met our deadline. The project was successful, and I learned the importance of clear roles in teamwork.
Tell me about a time when you faced a significant challenge during the mixing process. How did you resolve it?
How to Answer
- 1
Identify a specific challenge you faced during mixing.
- 2
Explain the impact of the challenge on the process or outcome.
- 3
Describe the steps you took to resolve the issue.
- 4
Highlight any teamwork or collaboration that occurred.
- 5
Conclude with the positive outcome or lessons learned.
Example Answers
In my previous job, we encountered a problem when a key ingredient was miscalculated, affecting the mix ratio. This potentially risked the batch quality. I quickly assessed the situation and recalibrated the mixer to adjust the ratios. I communicated with my team to verify the ingredient totals and successfully salvaged the batch. In the end, we delivered a high-quality product and I learned the importance of double-checking measurements.
Give me an example of a time when your attention to detail prevented a potential mixing error.
How to Answer
- 1
Think of a specific instance from your past experience.
- 2
Describe the situation clearly with context.
- 3
State the potential mixing error and its consequences.
- 4
Explain the actions you took based on your attention to detail.
- 5
Close with the positive outcome that resulted from your actions.
Example Answers
In my previous job, I noticed the incorrect ratio of ingredients during a mixing operation. This could have led to a batch being off-spec and wasted. I double-checked the measurements and confirmed the ratios with my supervisor, preventing the error and ensuring product quality.
Don't Just Read Mixing Operator Questions - Practice Answering Them!
Reading helps, but actual practice is what gets you hired. Our AI feedback system helps you improve your Mixing Operator interview answers in real-time.
Personalized feedback
Unlimited practice
Used by hundreds of successful candidates
Describe a situation where you identified a safety risk in the mixing operation. What actions did you take?
How to Answer
- 1
Think of a specific incident where you noticed a safety hazard.
- 2
Explain how you recognized the risk and its potential impact on safety.
- 3
Detail the steps you took to address the risk, including reporting it.
- 4
Mention any follow-up actions or training you initiated to prevent recurrence.
- 5
Highlight any positive outcomes from your actions regarding team safety.
Example Answers
In my previous role, I noticed that a mixing tank had a faulty safety valve which could lead to overpressure. I immediately reported it to my supervisor and we shut down the operation to prevent any accidents. We replaced the valve and I initiated a team safety meeting to discuss the importance of regularly checking safety equipment.
Technical Interview Questions
What types of mixing equipment are you familiar with, and which do you prefer to use? Why?
How to Answer
- 1
List specific types of mixing equipment you have experience with.
- 2
Mention your preferred equipment and explain the reason for your choice.
- 3
Focus on how your experience aligns with the job requirements.
- 4
Use examples from past roles to illustrate your familiarity.
- 5
Keep your answer concise and relevant to the position.
Example Answers
I am familiar with ribbon blenders and paddle mixers. I prefer ribbon blenders because they provide excellent mixing efficiency for dry powders and are easier to clean.
Explain the key parameters that need to be monitored during the mixing process for optimal results.
How to Answer
- 1
Identify the key parameters such as mixing speed and time.
- 2
Emphasize the importance of temperature control.
- 3
Discuss the role of material properties like viscosity.
- 4
Mention the significance of the mixing ratio of components.
- 5
Highlight the need for regular monitoring and adjustments.
Example Answers
During the mixing process, it's crucial to monitor the mixing speed and the duration to ensure uniform consistency. Temperature control plays a significant role as it affects the viscosity of the materials. Additionally, maintaining the correct mixing ratio of components is essential for optimal results.
Don't Just Read Mixing Operator Questions - Practice Answering Them!
Reading helps, but actual practice is what gets you hired. Our AI feedback system helps you improve your Mixing Operator interview answers in real-time.
Personalized feedback
Unlimited practice
Used by hundreds of successful candidates
What quality control measures do you implement in the mixing process?
How to Answer
- 1
Describe specific quality checks you perform during mixing.
- 2
Explain how you monitor ingredient ratios and consistency.
- 3
Mention any equipment or tools you use for quality control.
- 4
Talk about your process for documenting quality checks.
- 5
Provide an example of a problem you solved related to quality.
Example Answers
I implement a series of checks including weighing each ingredient before mixing to ensure accurate ratios. I also visually inspect the blend for consistency and use a pH meter to verify that the mixture meets the desired specifications.
How would you approach adjusting a mixing formula when the initial results do not meet specifications?
How to Answer
- 1
Analyze the deviation from specifications to identify specific issues.
- 2
Consider the individual components and their ratios in the formula.
- 3
Make small adjustments one at a time rather than changing multiple components at once.
- 4
Document the adjustments and results for future reference.
- 5
Communicate with team members to gather insights on the issue.
Example Answers
I would start by carefully reviewing the discrepancies to understand where the formula fell short. Then, I’d focus on the key ingredients, adjusting their ratios one at a time to find the right balance. I would keep track of each change to see its impact.
What routine maintenance checks do you perform on mixing machinery?
How to Answer
- 1
Identify key components of the mixing machinery that require regular checks
- 2
Discuss checking and replacing worn out parts as part of routine maintenance
- 3
Mention the importance of cleaning machinery to prevent contamination
- 4
Include checking fluid levels and ensuring proper calibration of equipment
- 5
Highlight the necessity of logging maintenance activities for future reference
Example Answers
I perform routine checks on the agitator and seals to ensure there is no wear and tear. I also clean the machinery regularly to avoid contamination, check fluid levels daily, and keep a log of all maintenance activities.
How important is temperature control during the mixing process, and how do you manage it?
How to Answer
- 1
Explain the impact of temperature on mixing quality and consistency.
- 2
Mention equipment used for monitoring and controlling temperature.
- 3
Describe techniques for adjusting temperature during the process.
- 4
Provide examples from past experiences where temperature control was critical.
- 5
Highlight any relevant safety considerations related to temperature management.
Example Answers
Temperature control is critical because it affects the viscosity and flow of materials. I monitor the temperature using thermocouples and adjust it with cooling jackets on the mixer when necessary. In my last position, I kept track of temperature fluctuations and made real-time adjustments to ensure optimal mixing.
What material properties do you consider critical when selecting materials for mixing?
How to Answer
- 1
Identify specific material properties relevant to the mixing process like viscosity and density.
- 2
Discuss how these properties affect the mixing efficiency and product quality.
- 3
Consider the compatibility of materials and their impact on the final blend.
- 4
Mention any safety or regulatory considerations based on the material properties.
- 5
Be ready to provide examples from your experience where material selection affected mixing outcomes.
Example Answers
I consider viscosity and density as critical properties. Viscosity affects how easily materials mix, ensuring a homogenous blend, while density helps in understanding the flow characteristics during mixing. For instance, in my previous role, selecting materials with similar densities led to better mixing efficiency.
Are you familiar with any software tools for managing the mixing process? Which ones?
How to Answer
- 1
Identify relevant software tools you have experience with
- 2
Mention specific functionalities that aid the mixing process
- 3
Discuss how you've used these tools in past roles
- 4
Express willingness to learn new software if needed
- 5
Be confident and clear in your response
Example Answers
Yes, I have experience with the MixMetrix software. I used it to track batch recipes and monitor ingredient ratios during the mixing process, which helped improve consistency.
What hygiene practices do you follow to ensure a clean mixing environment?
How to Answer
- 1
Always wear appropriate PPE like gloves and masks.
- 2
Clean and sanitize mixing equipment before and after use.
- 3
Regularly check and maintain cleanliness of work surfaces.
- 4
Dispose of waste materials properly and timely.
- 5
Follow a strict handwashing protocol before and after handling materials.
Example Answers
I ensure a clean mixing environment by wearing gloves and masks at all times and sanitizing all equipment before and after use.
What methods do you use to optimize the mixing process for efficiency?
How to Answer
- 1
Analyze the mixing formulas to ensure accurate ingredient ratios.
- 2
Utilize efficient mixing techniques, such as vortexing or shearing.
- 3
Regularly maintain and calibrate mixing equipment for optimal performance.
- 4
Monitor the mixing time and adjust based on viscosity and batch size.
- 5
Implement a feedback loop to assess and improve the mixing process continually.
Example Answers
I analyze the ingredient ratios before mixing to ensure they are optimal for efficiency. I use techniques like vortexing to improve suspension and reduce air pockets, which speeds up the process.
Don't Just Read Mixing Operator Questions - Practice Answering Them!
Reading helps, but actual practice is what gets you hired. Our AI feedback system helps you improve your Mixing Operator interview answers in real-time.
Personalized feedback
Unlimited practice
Used by hundreds of successful candidates
How do you utilize data from previous mixing operations to inform future runs?
How to Answer
- 1
Review data logs from past operations for insights on efficiency and quality.
- 2
Identify trends in ingredient performance to optimize recipes.
- 3
Use statistical analysis to determine the best mixing times and speeds.
- 4
Document any issues encountered and adjust parameters to prevent recurrence.
- 5
Collaborate with the quality control team to align data insights with product standards.
Example Answers
I regularly analyze data logs from previous mixing operations to identify any patterns in efficiency and product quality. For instance, I found that increasing the mixing speed at a certain stage improved the final product consistency.
Situational Interview Questions
If a mixing batch fails to meet quality standards, what steps would you take to address the situation?
How to Answer
- 1
Identify the specific quality standard that was not met
- 2
Review the mixing process and ingredients used
- 3
Document all findings and gather data from the batch
- 4
Consult with team members for additional insights
- 5
Develop a corrective action plan and implement it
Example Answers
I would start by identifying the specific quality standard that was not achieved. Then, I would review the mixing process, including the ingredients and equipment used. After gathering data, I would consult with my team to get their insights and create a corrective action plan to prevent recurrence.
If there is a disagreement among team members regarding the mixing process, how would you handle it?
How to Answer
- 1
Acknowledge the differing opinions without taking sides.
- 2
Encourage a collaborative discussion to explore each viewpoint.
- 3
Seek data or evidence to support the different opinions.
- 4
Facilitate a compromise or agree on a trial to test the different methods.
- 5
Maintain a focus on safety and quality throughout the discussion.
Example Answers
I would first listen to each team member's concerns and opinions to understand the disagreement. Then, I would facilitate a discussion where we could examine the evidence each person brings. If needed, I would suggest a trial of both methods to see which works better in practice.
Don't Just Read Mixing Operator Questions - Practice Answering Them!
Reading helps, but actual practice is what gets you hired. Our AI feedback system helps you improve your Mixing Operator interview answers in real-time.
Personalized feedback
Unlimited practice
Used by hundreds of successful candidates
Imagine that a new mixing technology is implemented. How would you adapt to this change?
How to Answer
- 1
Be open-minded about the new technology and its benefits for efficiency.
- 2
Highlight your willingness to undergo training and learn quickly.
- 3
Mention the importance of collaborating with team members during the transition.
- 4
Discuss your past experiences with adapting to new equipment or procedures.
- 5
Express your focus on maintaining quality standards while adapting.
Example Answers
I would approach the new mixing technology with an open mind and focus on understanding its benefits. I would participate actively in any training sessions offered and collaborate closely with my team to ensure we all adapt effectively together.
You have a tight deadline for a large mixing order. Describe how you would prioritize your tasks.
How to Answer
- 1
Assess the entire order to understand the ingredients and their quantities.
- 2
Identify any tasks that can be done simultaneously to save time.
- 3
Communicate with the team about priorities to ensure everyone is aligned.
- 4
Allocate time for quality checks to avoid redoing work later.
- 5
Stay flexible and adjust priorities as needed based on progress and any issues.
Example Answers
First, I would review the mixing order and list all ingredients and quantities. Then, I would prioritize the mixing tasks based on the complexity and required time. I would also delegate simpler tasks to my team to work on while I handle critical mixing. Regular communication with my team would ensure we're on track and can adapt as needed.
If you notice that your mixing procedures are not fully aligned with safety standards, what would you do?
How to Answer
- 1
Identify specific safety standards that are not being met.
- 2
Communicate the issue promptly to your supervisor or safety officer.
- 3
Document the discrepancies in procedures and potential risks.
- 4
Suggest corrective actions based on safety protocols.
- 5
Follow up to ensure implemented changes are effective.
Example Answers
I would first identify which specific safety standards are not being met. Then, I'd report the issue to my supervisor immediately and document my findings. I'd suggest corrective actions based on the safety guidelines and ensure they are implemented.
If you were in the middle of a mixing run and the machine suddenly malfunctioned, what would be your immediate actions?
How to Answer
- 1
Immediately stop the machine to prevent further damage.
- 2
Assess the nature of the malfunction and any safety risks.
- 3
Safely clear the area and notify your supervisor or the appropriate personnel.
- 4
Document the malfunction details for maintenance records.
- 5
Follow standard operating procedures for machine troubleshooting.
Example Answers
I would first stop the machine to avoid any risk or further damage. Then, I would assess the situation for any safety hazards and ensure the area is clear. I would notify my supervisor and document the issue as per our protocols.
If you have an opportunity to evaluate the mixing processes of others, what criteria would you use?
How to Answer
- 1
Assess the consistency of the final product for quality standards.
- 2
Evaluate adherence to safety and operational protocols.
- 3
Check for efficiency in time and resource usage.
- 4
Look for proper equipment maintenance and calibration.
- 5
Gather feedback from team members on the process effectiveness.
Example Answers
I would evaluate the mixing processes by checking whether the final product meets our quality standards consistently. I'd also look at how well the team follows safety protocols during operation.
How would you handle a scenario where there are insufficient materials for the mixing schedule?
How to Answer
- 1
Assess the specific materials that are lacking and quantify the shortage.
- 2
Communicate with your supervisor or team to inform them of the issue as soon as possible.
- 3
Explore alternative materials that might be used without compromising quality.
- 4
Check inventory for any excess from previous batches that could be repurposed.
- 5
Prepare a revised schedule or workflow to minimize downtime until materials are replenished.
Example Answers
If I notice insufficient materials for the mixing schedule, I would quickly determine the exact shortage and inform my supervisor. I would then look for any alternative materials that may be adequate for the mix and check if we have leftover inventory that we could use to complete the task.
How would you ensure cooperation with other departments, such as quality assurance, during a mixing operation?
How to Answer
- 1
Establish clear communication channels with quality assurance.
- 2
Schedule regular meetings to discuss mixing goals and quality standards.
- 3
Encourage feedback from quality assurance during the mixing process.
- 4
Document procedures and outcomes to share with all departments.
- 5
Be proactive in resolving any issues that may arise between departments.
Example Answers
I would ensure clear communication by setting up weekly meetings with the quality assurance team to align on mixing standards and any adjustments needed.
Mixing Operator Position Details
Recommended Job Boards
ZipRecruiter
www.ziprecruiter.com/Jobs/Mixer-OperatorThese job boards are ranked by relevance for this position.
Related Positions
- Mixer
- Mixing Engineer
- Sound Mixer
- Rerecording Mixer
- Music Engineer
- Sound Engineer
- Mixer Operator
- Distribution Operator
- Spice Mixer
- Food Mixer
Similar positions you might be interested in.
Ace Your Next Interview!
Practice with AI feedback & get hired faster
Personalized feedback
Used by hundreds of successful candidates
Ace Your Next Interview!
Practice with AI feedback & get hired faster
Personalized feedback
Used by hundreds of successful candidates