Top 31 Pack Master Interview Questions and Answers [Updated 2025]
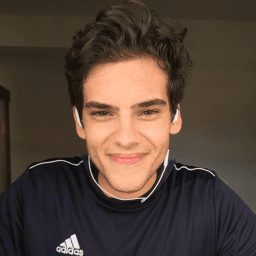
Andre Mendes
•
March 30, 2025
Preparing for a Pack Master interview can be daunting, but we're here to help you succeed. In this post, we cover the most common interview questions for the Pack Master role, providing you with example answers and effective response strategies. Whether you're aiming to refine your skills or boost your confidence, our insights will guide you in crafting compelling answers that make a lasting impression.
Download Pack Master Interview Questions in PDF
To make your preparation even more convenient, we've compiled all these top Pack Masterinterview questions and answers into a handy PDF.
Click the button below to download the PDF and have easy access to these essential questions anytime, anywhere:
List of Pack Master Interview Questions
Situational Interview Questions
How would you manage your time and resources if you had a tight deadline for packing a large order?
How to Answer
- 1
Prioritize tasks based on urgency and importance.
- 2
Delegate tasks to team members to maximize efficiency.
- 3
Utilize packing technology or tools to speed up the process.
- 4
Create a timeline with checkpoints to monitor progress.
- 5
Stay flexible and adjust plans as needed to meet the deadline.
Example Answers
To manage a tight deadline, I would start by prioritizing the packing tasks, focusing on items that need to go out first. I'd delegate specific items to team members based on their strengths. Using packing tools like tape dispensers and labeling machines, I would speed up the process. I'd set a clear timeline with milestones to ensure we stay on track and adapt the plan if unexpected delays arise.
If two team members are not getting along and it affects packing output, what would you do?
How to Answer
- 1
Address the issue promptly to prevent further decline in performance.
- 2
Have a private conversation with each team member to understand their perspective.
- 3
Encourage open communication between the team members to resolve tensions.
- 4
Mediate a group meeting to facilitate a constructive dialogue.
- 5
Follow up to ensure the conflict is resolved and productivity improves.
Example Answers
I would first speak to each team member individually to get their side of the story. Then, I'd facilitate a meeting where they can discuss their issues openly and work towards a solution together.
Don't Just Read Pack Master Questions - Practice Answering Them!
Reading helps, but actual practice is what gets you hired. Our AI feedback system helps you improve your Pack Master interview answers in real-time.
Personalized feedback
Unlimited practice
Used by hundreds of successful candidates
How would you adjust your packing strategies if you suddenly experienced a surge in orders?
How to Answer
- 1
Assess current packing processes and identify bottlenecks
- 2
Implement temporary overtime or additional shifts for packers
- 3
Utilize packing automation where possible to increase speed
- 4
Organize packing area for optimal workflow and efficiency
- 5
Train team members on flexible packing techniques to speed up processes
Example Answers
In the event of a surge in orders, I would first analyze our current packing workflow to pinpoint any inefficiencies. I would then assign extra shifts or seek temporary staff to handle the increase. Additionally, I would ensure our packing stations have all necessary materials readily available to avoid delays.
If a customer complained about damaged goods due to packing, how would you respond to resolve the issue?
How to Answer
- 1
Acknowledge the customer's concern promptly
- 2
Apologize sincerely for the inconvenience caused
- 3
Gather relevant details about the issue clearly
- 4
Offer a solution, such as a replacement or refund
- 5
Ensure follow-up to confirm customer satisfaction
Example Answers
I would start by acknowledging the customer's complaint and sincerely apologize for the inconvenience. Then, I would ask them for details about the order and what specifically was damaged. After gathering the information, I would offer a replacement at no additional charge and follow up to ensure they received it and were satisfied.
If you had to pack a fragile item, what considerations would you take to ensure its safety?
How to Answer
- 1
Choose a sturdy box that is slightly larger than the item
- 2
Use bubble wrap or foam to cushion the item from all sides
- 3
Fill any empty spaces with packing peanuts or crumpled paper
- 4
Seal the box securely with strong tape and label it as fragile
- 5
Consider the orientation of the item during transportation
Example Answers
I would select a sturdy box that fits the item, then wrap the item in bubble wrap to protect it from shock. I'd fill any gaps in the box with packing peanuts and seal it with strong tape, clearly labeling it as fragile.
What would you do if you received last-minute changes to a packing instruction?
How to Answer
- 1
Stay calm and assess the changes to understand their impact
- 2
Communicate with your team to relay the new instructions clearly
- 3
Prioritize the tasks involved based on urgency and importance
- 4
Adjust the packing process quickly while double-checking accuracy
- 5
Document the changes for future reference and improvement
Example Answers
If I received last-minute changes, I would first stay calm and review the new instructions carefully. Then, I would gather my team and communicate the changes, ensuring everyone understands the new priorities. I would reallocate tasks as needed and focus on maintaining accuracy while packing.
How would you motivate your team during a particularly monotonous packing task?
How to Answer
- 1
Incorporate short breaks to refresh the team.
- 2
Introduce a friendly competition with rewards for productivity.
- 3
Play upbeat music to create a positive atmosphere.
- 4
Set clear and achievable goals to give a sense of accomplishment.
- 5
Recognize and celebrate small wins to boost morale.
Example Answers
I would schedule short breaks to help the team recharge and keep spirits high. Additionally, I would set up a friendly competition where the fastest packers could earn small rewards, which would make the task engaging.
Describe how you would collaborate with the shipping department to ensure timely dispatch of packed goods.
How to Answer
- 1
Establish clear communication channels with the shipping department.
- 2
Schedule regular meetings to coordinate dispatch schedules.
- 3
Use a tracking system to monitor the status of packed goods.
- 4
Identify potential bottlenecks and address them proactively.
- 5
Align packing timelines with shipping deadlines to ensure synchronization.
Example Answers
I would set up weekly meetings with the shipping department to discuss our dispatch schedule and any changes that may arise, ensuring we are aligned on timelines.
If a packing machine broke down unexpectedly during a busy shift, how would you handle the situation?
How to Answer
- 1
Stay calm and assess the situation quickly
- 2
Notify the maintenance team immediately and provide details of the issue
- 3
Communicate with your team to manage workflow and expectations
- 4
Implement a contingency plan, such as redirecting work to other machines if available
- 5
Document the incident for future reference and improvement
Example Answers
I would first stay calm and assess the nature of the breakdown. Then, I would notify the maintenance team so they can address it promptly. Meanwhile, I would communicate with my team, letting them know to adjust our workflow as necessary.
If you notice that a batch of products is not being packed to quality standards, what steps would you take?
How to Answer
- 1
Assess the situation to confirm the quality issue.
- 2
Communicate with the packing team to understand the cause.
- 3
Isolate the affected batch to prevent further issues.
- 4
Document the quality concerns and any actions taken.
- 5
Implement corrective actions and monitor for improvements.
Example Answers
I would first assess the batch to verify the quality issue. Once confirmed, I would talk to the packing team to find out what went wrong. Then, I'd isolate the affected products and document everything, ensuring we implement corrective measures to resolve the issue.
Don't Just Read Pack Master Questions - Practice Answering Them!
Reading helps, but actual practice is what gets you hired. Our AI feedback system helps you improve your Pack Master interview answers in real-time.
Personalized feedback
Unlimited practice
Used by hundreds of successful candidates
Behavioral Interview Questions
Can you describe your experience in training new employees in packing procedures?
How to Answer
- 1
Start with how many employees you trained and in what capacity.
- 2
Mention specific packing procedures you focused on during training.
- 3
Explain any training materials or methods you used.
- 4
Share metrics or outcomes that demonstrate the success of your training.
- 5
Highlight any feedback you received from trainees or supervisors.
Example Answers
In my previous role, I trained 5 new employees on our packing procedures over a month. I focused on proper packing techniques and safety protocols. I used a hands-on approach along with a training manual. As a result, we achieved a 20% reduction in packing errors within that period.
Tell me about a time you received constructive criticism about your packing methods. How did you respond?
How to Answer
- 1
Choose a specific example from your experience
- 2
Describe the criticism clearly and objectively
- 3
Explain how you adapted your methods based on the feedback
- 4
Highlight the positive outcome of your change
- 5
Reflect on what you learned from the experience
Example Answers
In my previous job, my supervisor pointed out that my packing technique was inefficient and led to damaged items. I listened carefully to her suggestions, practiced a new method she recommended, and within weeks, our damage rate decreased significantly. This experience taught me the importance of being open to feedback.
Don't Just Read Pack Master Questions - Practice Answering Them!
Reading helps, but actual practice is what gets you hired. Our AI feedback system helps you improve your Pack Master interview answers in real-time.
Personalized feedback
Unlimited practice
Used by hundreds of successful candidates
Can you give an example of when your attention to detail made a significant impact in a packing operation?
How to Answer
- 1
Choose a specific scenario where details were crucial.
- 2
Explain the task and the potential for errors.
- 3
Describe how your attention prevented a problem.
- 4
Quantify the impact if possible, such as saved time or reduced errors.
- 5
Conclude with the positive outcome or feedback received.
Example Answers
In my previous job, we had a deadline to ship 500 packages. While checking the packing list, I noticed a product was incorrectly labeled. I caught it before shipping, which saved us from potential returns and customer dissatisfaction.
Describe a time when you suggested an innovative packing solution. What was the outcome?
How to Answer
- 1
Identify a specific situation where you proposed a new packing method.
- 2
Explain the problem that required innovation in packing.
- 3
Detail the solution you suggested and how it improved the process.
- 4
Discuss the outcome and any measurable results, such as cost savings or efficiency improvements.
- 5
Reflect on what you learned from the experience and how it can apply to the Pack Master role.
Example Answers
In a previous role, I noticed that our products were often damaged during shipping due to inadequate packing materials. I proposed using biodegradable packing peanuts instead of foam. This change reduced damage claims by 20% and also aligned with our sustainability goals.
Can you describe a time when you successfully worked as part of a team to improve the packing efficiency?
How to Answer
- 1
Identify a specific project or situation where team collaboration was key
- 2
Highlight your role and contributions within the team
- 3
Discuss the strategies or methods used to improve efficiency
- 4
Share the measurable results or outcomes of the team's efforts
- 5
Reflect on what you learned from the experience and how it can apply to future challenges
Example Answers
In my previous role as a packer, we faced delays during peak seasons. I suggested a team meeting where we brainstormed ideas. We implemented a rotation system that distributed tasks evenly, resulting in a 20% increase in our packing speed. This experience taught me the importance of teamwork and open communication.
Tell me about a challenge you faced in a packing operation and how you overcame it.
How to Answer
- 1
Select a specific challenge you encountered in packing operations.
- 2
Describe the context clearly and what made it challenging.
- 3
Explain the steps you took to address the challenge.
- 4
Highlight the results of your actions and what you learned.
- 5
Conclude with how this experience has prepared you for future challenges.
Example Answers
In a previous role, we faced a shortage of packing materials that delayed shipments. I organized an emergency meeting with suppliers to expedite orders and implemented a temporary system to manage inventory better. This solution minimized delays by 50% and built stronger supplier relationships.
Describe a situation where you led a team of packers. What was the outcome?
How to Answer
- 1
Choose a specific project or task where you were in charge.
- 2
Explain your leadership approach and how you motivated your team.
- 3
Discuss strategies you used to improve efficiency or resolve issues.
- 4
Highlight the positive outcomes, such as meeting deadlines or improving quality.
- 5
Summarize what you learned from the experience and how it can apply to future situations.
Example Answers
In my previous role, I led a team of 5 packers during our holiday rush. I set daily targets and held team meetings to encourage open communication. We implemented a new packing technique that reduced errors by 20%. As a result, we met our shipment goals for the season and received positive feedback from management.
Can you provide an example of how you prioritized tasks during a busy packing period?
How to Answer
- 1
Identify the most urgent tasks based on deadlines
- 2
Group similar tasks for efficiency
- 3
Communicate with team members to delegate responsibilities
- 4
Use tools like checklists to track progress
- 5
Be flexible and ready to adjust priorities as needed
Example Answers
During a peak packing week, I assessed all incoming orders and prioritized those due first by creating a list. I grouped similar tasks and delegated smaller pack jobs to my team, which helped us finish faster. This approach allowed us to meet deadlines without compromising quality.
Give an example of a time you had to adapt your packing methods to meet new requirements.
How to Answer
- 1
Identify the specific requirements that changed
- 2
Explain your original packing methods
- 3
Describe the adjustments you made
- 4
Highlight the impact of those changes
- 5
Conclude with what you learned from the experience
Example Answers
In my previous role at a logistics company, we received a sudden request to pack hazardous materials safely due to new regulations. I adapted by researching proper materials and methods for hazardous packing, transitioned from standard cardboard to specialized containers, and implemented labels for compliance. This change ensured safety and met legal standards, which enhanced our reputation with clients.
Describe a situation where you had to communicate a complex packing process to your team. How did you ensure understanding?
How to Answer
- 1
Identify the key elements of the packing process that were complex.
- 2
Use visual aids like diagrams or charts to illustrate the process.
- 3
Break down the process into simple, manageable steps.
- 4
Encourage questions and discussions to clarify doubts.
- 5
Follow up with a summary or guide document for reference.
Example Answers
In a previous role, I explained a new packing method by first creating a flowchart that highlighted each step of the process. I then walked the team through it and made sure to pause for any questions at each stage.
Don't Just Read Pack Master Questions - Practice Answering Them!
Reading helps, but actual practice is what gets you hired. Our AI feedback system helps you improve your Pack Master interview answers in real-time.
Personalized feedback
Unlimited practice
Used by hundreds of successful candidates
Can you tell me about a disagreement you had with a co-worker regarding packing procedures? How was it resolved?
How to Answer
- 1
Choose a specific disagreement that highlights packing procedures.
- 2
Explain the differing perspectives and why they mattered.
- 3
Describe the steps taken to resolve the disagreement.
- 4
Emphasize teamwork and collaboration in finding a solution.
- 5
Conclude with the outcome and what was learned from the situation.
Example Answers
In my previous role, a co-worker and I disagreed on the best way to package fragile items. I thought bubble wrap was sufficient, but they believed double-boxing was necessary. We discussed our reasons and agreed to do a test run. After trying both methods, we found double-boxing reduced damage in transit. This experience taught me the value of testing different approaches collaboratively.
Technical Interview Questions
What experience do you have with designing packaging layouts to maximize efficiency?
How to Answer
- 1
Focus on specific projects where you designed packaging.
- 2
Highlight your design process and any tools used.
- 3
Mention how you considered factors like material cost and space optimization.
- 4
Include results or feedback from your designs to show effectiveness.
- 5
Discuss any collaboration with other teams, such as marketing or production.
Example Answers
In my previous role, I designed packaging for a new product line. I used Adobe Illustrator to create layouts that minimized material waste, which reduced costs by 20%. The feedback from production was positive as it streamlined their packing process.
How do you track and analyze packing data to improve productivity?
How to Answer
- 1
Implement a data tracking system to log packing times and errors.
- 2
Utilize software to analyze trends in packing efficiency over time.
- 3
Regularly conduct team meetings to discuss data insights and suggestions.
- 4
Establish key performance indicators (KPIs) to measure packing performance.
- 5
Incorporate feedback loops for continuous improvement based on data findings.
Example Answers
I track packing data using a digital logging system that records packing times and error rates. By analyzing this data weekly, I identify trends and areas for improvement, which I share with the team during our meetings to refine our packing strategies.
Don't Just Read Pack Master Questions - Practice Answering Them!
Reading helps, but actual practice is what gets you hired. Our AI feedback system helps you improve your Pack Master interview answers in real-time.
Personalized feedback
Unlimited practice
Used by hundreds of successful candidates
What packing software or tools have you used, and how have they helped you in your role?
How to Answer
- 1
Identify specific software or tools you have used.
- 2
Explain the purpose and functionalities of these tools.
- 3
Share how these tools improved your efficiency or accuracy.
- 4
Mention any specific outcomes or results from using them.
- 5
Be prepared to discuss how you adapt to new tools.
Example Answers
In my last role, I used a software called ShipStation which helped streamline order management. It allowed me to batch print labels and track shipments in real time, reducing errors by 30%.
How familiar are you with RFID or barcode technology in the packing process?
How to Answer
- 1
Discuss any hands-on experience with RFID or barcode scanners.
- 2
Mention specific applications in packing, such as tracking inventory or improving accuracy.
- 3
Highlight any relevant training or certifications you've completed.
- 4
Explain the benefits of using RFID or barcodes in packing processes.
- 5
Be prepared to answer follow-up questions about your experience.
Example Answers
I have used barcode scanners in my previous job to track inventory during the packing process. This helped reduce errors by ensuring accurate item counts.
What types of packing machinery are you experienced with, and how have you operated them?
How to Answer
- 1
List specific types of packing machinery you have used.
- 2
Describe the types of products you packed with each machine.
- 3
Mention any maintenance or troubleshooting you did.
- 4
Highlight any improvements or efficiencies you achieved.
- 5
Provide context about teamwork or leading roles if applicable.
Example Answers
I have experience with vertical form-fill-seal machines and horizontal case packers. I used the vertical machines to package granola bars and the case packers for shipping boxes of snacks. I performed routine maintenance and resolved minor technical issues to ensure smooth operation.
How do you ensure compliance with industry packing standards in your work?
How to Answer
- 1
Familiarize yourself with the specific packing standards relevant to your industry
- 2
Regularly review packing protocols and guidelines to stay updated
- 3
Implement checklists for packing processes to ensure all standards are met
- 4
Conduct training sessions for team members on compliance standards
- 5
Document any compliance checks and results for accountability
Example Answers
I ensure compliance by thoroughly understanding the packing standards and regularly reviewing our protocols. I also use checklists during the packing process to verify every step is compliant.
What factors do you consider when selecting packing materials for a product?
How to Answer
- 1
Evaluate the product's fragility and requirements for protection
- 2
Consider the cost of materials versus budget constraints
- 3
Assess environmental impact and sustainability options
- 4
Ensure compliance with shipping regulations and standards
- 5
Think about branding and customer experience in packaging design
Example Answers
I focus on the fragility of the product, ensuring that the selected materials provide adequate protection. I also consider cost-effectiveness and try to choose sustainable options whenever possible.
How do you manage packing inventory to ensure you have the right materials on hand?
How to Answer
- 1
Regularly audit inventory levels to identify discrepancies
- 2
Implement a just-in-time inventory system to reduce excess
- 3
Utilize inventory management software for real-time tracking
- 4
Forecast demand based on historical data and upcoming orders
- 5
Establish strong relationships with suppliers for quick replenishment
Example Answers
I conduct routine audits of our inventory to keep our materials aligned with demand, and I use inventory software to track our stock levels in real-time.
Can you describe a packing process you optimized? What were the results?
How to Answer
- 1
Identify a specific instance where you improved packing efficiency.
- 2
Use metrics to quantify the improvements you made.
- 3
Explain the steps you took to analyze and implement changes.
- 4
Mention the impact on time saved or costs reduced.
- 5
Highlight any feedback you received from team members or management.
Example Answers
In my previous role, I analyzed our packing line workflow and noticed that we spent too much time sorting items before packing. I implemented a new sorting system that reduced sorting time by 30%. As a result, we increased our packing output by 15% per hour, which pleased both our management and customers.
What safety protocols do you follow when operating packaging equipment?
How to Answer
- 1
Always wear appropriate personal protective equipment (PPE) such as gloves and safety glasses.
- 2
Perform regular equipment inspections before use to identify any hazards.
- 3
Follow lockout/tagout procedures to ensure machines are properly shut down during maintenance.
- 4
Be aware of emergency stop buttons and safety switches on all equipment.
- 5
Adhere to manufacturer guidelines for operation and maintenance of packaging machinery.
Example Answers
I follow strict safety protocols by wearing PPE like gloves and glasses. Before operating any packaging equipment, I inspect it to ensure there are no hazards. I also always utilize lockout/tagout procedures for maintenance.
Don't Just Read Pack Master Questions - Practice Answering Them!
Reading helps, but actual practice is what gets you hired. Our AI feedback system helps you improve your Pack Master interview answers in real-time.
Personalized feedback
Unlimited practice
Used by hundreds of successful candidates
Pack Master Position Details
Related Positions
- Packer
- Headman
- Top Carrier
- Bucket Operator
- Hack Driver
- Machine Stacker
- Coal Handler
- Dragman
- Ship Loader
- Moveman
Similar positions you might be interested in.
Ace Your Next Interview!
Practice with AI feedback & get hired faster
Personalized feedback
Used by hundreds of successful candidates
Ace Your Next Interview!
Practice with AI feedback & get hired faster
Personalized feedback
Used by hundreds of successful candidates