Top 33 Packer Interview Questions and Answers [Updated 2025]
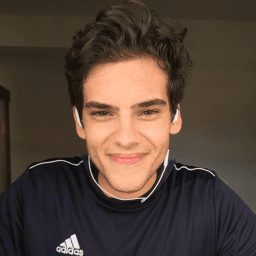
Andre Mendes
•
March 30, 2025
Preparing for a Packer interview can be daunting, but we're here to help you ace it with confidence. In this post, we've compiled the most common interview questions for the Packer role, complete with example answers and insightful tips on how to respond effectively. Whether you're a seasoned professional or a newcomer, this guide will equip you with the tools to impress your prospective employers.
Download Packer Interview Questions in PDF
To make your preparation even more convenient, we've compiled all these top Packerinterview questions and answers into a handy PDF.
Click the button below to download the PDF and have easy access to these essential questions anytime, anywhere:
List of Packer Interview Questions
Behavioral Interview Questions
Can you describe a time when you had to work as part of a team to complete a packing task? What was your role?
How to Answer
- 1
Identify a specific packing task you did with a team
- 2
Describe your specific responsibilities in that task
- 3
Highlight how you contributed to the team's success
- 4
Mention any challenges faced and how you overcame them
- 5
Conclude with a positive outcome for the team or project
Example Answers
In my previous job at a warehouse, our team had to pack a large order for a client. I was responsible for sorting the items based on size and type, which helped streamline the process. We faced a challenge when we ran out of packing materials, but I quickly contacted the supplier to get more. In the end, we completed the order on time and received positive feedback from the client.
Tell me about a time when you had to complete a packing job under a tight deadline. How did you manage your time?
How to Answer
- 1
Think of a specific example from your experience.
- 2
Describe the situation clearly and mention what the deadline was.
- 3
Explain the steps you took to prioritize your tasks.
- 4
Mention any tools or methods you used to stay organized.
- 5
Conclude with the outcome and any lessons learned.
Example Answers
In my previous job at a warehouse, we had a shipment that needed to go out within three hours. I quickly gathered the packing materials and created a list of items to pack. I prioritized the items by size and fragility, starting with the most fragile ones. Using a packing checklist helped me stay on track, and I completed the packing 30 minutes early, allowing time for a final quality check.
Don't Just Read Packer Questions - Practice Answering Them!
Reading helps, but actual practice is what gets you hired. Our AI feedback system helps you improve your Packer interview answers in real-time.
Personalized feedback
Unlimited practice
Used by hundreds of successful candidates
Describe a situation where you had to adapt your packing method due to changes in product size or shape. How did you handle it?
How to Answer
- 1
Identify a specific instance where product dimensions changed.
- 2
Explain the original packing method you used.
- 3
Describe how you assessed the new size or shape's impact on packing.
- 4
Detail the new packing method you implemented.
- 5
Conclude with the results or feedback received from the change.
Example Answers
In my last job, we received a shipment of larger boxes than usual for our electronic devices. Initially, I used standard packing materials, but to adapt, I switched to using custom-sized inserts that secured the items better. This new method prevented damage during transport, and my supervisor praised the improved safety.
Have you ever had a disagreement with a coworker about how to pack an item? How did you resolve it?
How to Answer
- 1
Stay calm and listen to the coworker's perspective.
- 2
Discuss the reasons behind each packing method.
- 3
Use data or company guidelines to support your approach.
- 4
Suggest a compromise if possible, like trying both methods.
- 5
Follow up after the disagreement to ensure smooth teamwork.
Example Answers
I had a disagreement with a coworker about how to pack fragile items. I listened to his concerns about his method. Together, we reviewed the packing guidelines, which supported my approach. We decided to try both methods to see which was more effective. In the end, we improved our packing techniques collaboratively.
Can you discuss a time when you noticed a safety concern while packing? What steps did you take?
How to Answer
- 1
Identify a specific safety issue you encountered
- 2
Explain how you assessed the situation
- 3
Describe the actions you took to address the concern
- 4
Mention how you communicated the issue to your team
- 5
Reflect on the outcome and any improvements made
Example Answers
While packing, I noticed that a carton had a sharp edge. I immediately stopped working and assessed the risk it posed to my hands and others. I reported it to my supervisor and we marked it as a safety concern while it was removed from the packing area. This led to a review of our packing materials to ensure safety.
Tell me about a challenging packing job you completed successfully. What made it challenging?
How to Answer
- 1
Identify a specific packing job and describe the context
- 2
Highlight the specific challenges faced during the packing process
- 3
Explain the steps you took to overcome these challenges
- 4
Emphasize the positive outcome and what you learned
- 5
Keep it concise, aiming for clarity and focus on your skills
Example Answers
I once had to pack a large shipment of fragile glass items for a last-minute order. The challenge was the tight deadline and the need to ensure that everything was packed securely to prevent breakage. I organized the items by size, used extra bubble wrap, and double-checked each box before sealing. The shipment arrived intact, and the client was very pleased with the fast turnaround.
Describe a situation where you had to multitask during packing. How did you ensure quality was not compromised?
How to Answer
- 1
Choose a specific example from your experience as a packer.
- 2
Explain the tasks you had to juggle during the multitasking situation.
- 3
Highlight techniques you used to maintain efficiency without sacrificing quality.
- 4
Mention any tools or systems that helped you stay organized.
- 5
Conclude with the positive outcome of your multitasking effort.
Example Answers
In my previous job, during a busy holiday season, I was responsible for packing multiple orders simultaneously. I prioritized my tasks, packing smaller items first to keep the workflow steady. I used checklists to ensure I didn't miss any items. By setting a timer for each order, I maintained a steady pace while double-checking each package. As a result, our team met shipping deadlines with zero complaints about incorrect orders.
Can you provide an example of how your work ethic contributed to a successful packing project?
How to Answer
- 1
Think of a specific project where your hard work made a difference.
- 2
Focus on the actions you took to ensure quality and efficiency.
- 3
Mention any challenges you overcame due to your dedication.
- 4
Highlight teamwork and communication if applicable.
- 5
Conclude with the positive outcome of your efforts.
Example Answers
In my last role at the warehouse, we had a tight deadline for a large order. I took the initiative to organize our packing station, ensuring everything was labeled and easily accessible. This improved our efficiency, and we completed the project ahead of schedule, which impressed the management.
Don't Just Read Packer Questions - Practice Answering Them!
Reading helps, but actual practice is what gets you hired. Our AI feedback system helps you improve your Packer interview answers in real-time.
Personalized feedback
Unlimited practice
Used by hundreds of successful candidates
Can you describe a time you received constructive feedback about your packing work? How did you respond?
How to Answer
- 1
Choose a specific example from your past packing work.
- 2
Explain the feedback you received clearly.
- 3
Describe your emotional response to the feedback.
- 4
Highlight the actions you took in response to the feedback.
- 5
Mention any positive results or improvements from your actions.
Example Answers
In my last job, my supervisor pointed out that I was not properly organizing the items on the packing line. Initially, I felt a bit defensive, but I took it seriously. I started sorting items into categories before packing. As a result, my packing became faster and more accurate.
Technical Interview Questions
What types of packing materials are you familiar with, and how do you choose the right one for different products?
How to Answer
- 1
Identify common packing materials like cardboard boxes, bubble wrap, and foam peanuts.
- 2
Discuss the importance of product protection during transport and storage.
- 3
Mention considerations like weight, fragility, and temperature sensitivity of the products.
- 4
Explain how sustainability and cost-effectiveness influence material choice.
- 5
Share examples of specific products and the materials best suited for them.
Example Answers
I am familiar with materials such as cardboard, bubble wrap, and shrink wrap. For fragile items, I would choose bubble wrap for cushioning, while for heavier items, strong cardboard boxes are ideal.
Describe your experience with packing machinery. How do you ensure they operate correctly?
How to Answer
- 1
Highlight specific types of packing machinery you've worked with
- 2
Discuss your training or certifications related to packing machinery
- 3
Mention any troubleshooting procedures you follow
- 4
Emphasize routine maintenance practices you implement
- 5
Provide examples of how you handle machine malfunctions
Example Answers
I have worked with various packing machines such as shrink wrap and vacuum sealers. I ensure they operate correctly by performing daily checks, following maintenance schedules, and quickly troubleshooting any issues that arise during operation.
Don't Just Read Packer Questions - Practice Answering Them!
Reading helps, but actual practice is what gets you hired. Our AI feedback system helps you improve your Packer interview answers in real-time.
Personalized feedback
Unlimited practice
Used by hundreds of successful candidates
What quality control measures do you implement during the packing process?
How to Answer
- 1
Start by mentioning the importance of standards and protocols.
- 2
Discuss checking for completed tasks and accuracy before sealing packages.
- 3
Include examples of using checklists to ensure all items are included.
- 4
Mention regular inspections and audits for consistency.
- 5
Explain the importance of training staff to understand quality standards.
Example Answers
I always follow the established packing protocols and ensure all items are picked accurately using checklists. Before sealing a package, I double-check that all items are present and fit the quality standards.
Explain the importance of proper packaging techniques in preventing damage to products.
How to Answer
- 1
Emphasize how packaging protects against physical damage during transit.
- 2
Discuss the role of packaging materials in cushioning and absorbing shocks.
- 3
Mention how proper sealing prevents contamination and moisture damage.
- 4
Highlight the importance of labeling for safe handling.
- 5
Bring up compliance with shipping regulations to avoid fines and damage.
Example Answers
Proper packaging techniques are essential because they protect products from physical damage while being transported. Using the right materials, like bubble wrap or foam, absorbs shocks and reduces the risk of breakage. Additionally, sealing packages correctly helps prevent moisture and contamination, which could ruin the products.
How do you keep track of inventory levels during the packing process?
How to Answer
- 1
Use a checklist for each packing order to ensure accuracy
- 2
Implement a digital inventory management system if available
- 3
Perform regular counts before and after packing to reconcile
- 4
Label and categorize items clearly to avoid confusion
- 5
Communicate with team members to stay updated on inventory changes
Example Answers
I use a checklist for each packing order to ensure I pack the correct items and quantities. I also perform regular counts before and after packing to track any discrepancies.
What are the key considerations you take into account while labeling packages?
How to Answer
- 1
Ensure clarity and legibility of the label for easy reading.
- 2
Include all required information such as destination, contents, and handling instructions.
- 3
Use durable materials that withstand transit conditions.
- 4
Verify correct barcodes and tracking information for accuracy.
- 5
Consider industry standards and regulations for labeling.
Example Answers
When labeling packages, I focus on clarity and ensure that all required information is visible. This includes the destination address, handling instructions, and a clear barcode for tracking.
Can you discuss the different shipping methods you have used? How does packing differ for each?
How to Answer
- 1
Identify at least three shipping methods you've used in your experience
- 2
Explain how packing differs for each method in terms of materials and techniques
- 3
Use specific examples from past jobs to illustrate your points
- 4
Focus on cost-effectiveness and how it impacts your packing choices
- 5
Be prepared to discuss any regulations or requirements you've followed
Example Answers
In my previous role, I worked with ground, air, and freight shipping. For ground shipping, I typically used corrugated boxes with foam inserts to secure fragile items. Air shipping required lighter materials to reduce weight, such as padded envelopes or custom-sized boxes with air pillows. Freight shipping often necessitated wooden crates for heavy machinery, ensuring everything was strapped down properly to avoid damage during transit.
What do you know about customs regulations and how they affect packing for international shipping?
How to Answer
- 1
Know the main customs regulations for your target countries.
- 2
Understand the importance of accurate customs documentation.
- 3
Be aware of restricted and prohibited items in international shipping.
- 4
Highlight the role of packing materials in customs compliance.
- 5
Mention any experience you have with customs processes.
Example Answers
I understand that customs regulations vary by country and can affect how goods are packed. Accurate documentation is essential to avoid delays and penalties. I've learned that certain materials are restricted, and we must know these to ensure compliance.
How do you verify that the correct items are included in a packing list?
How to Answer
- 1
Review the packing list before starting to pick items.
- 2
Cross-check each item with the corresponding orders or invoices.
- 3
Use a checklist to mark off items as you pack them.
- 4
Double-check quantities to ensure accuracy.
- 5
Verify with team members if there are any discrepancies.
Example Answers
I always start by carefully reviewing the packing list to understand what needs to be included. Then, I cross-check each item with the orders to make sure everything matches.
How do you consider environmental factors when selecting packing materials?
How to Answer
- 1
Research the sustainability of materials available for packaging
- 2
Prioritize biodegradable or recyclable materials when possible
- 3
Consider the carbon footprint of materials and their production process
- 4
Evaluate the recyclability of the packing after use
- 5
Stay updated on regulations and certifications related to environmental standards
Example Answers
I prioritize using biodegradable materials like plant-based fillers when packing. This not only reduces waste but aligns with eco-friendly practices.
Don't Just Read Packer Questions - Practice Answering Them!
Reading helps, but actual practice is what gets you hired. Our AI feedback system helps you improve your Packer interview answers in real-time.
Personalized feedback
Unlimited practice
Used by hundreds of successful candidates
What process do you follow when repacking returned items?
How to Answer
- 1
Inspect returned items for damage and ensure completeness.
- 2
Clean and sanitize items if necessary before repacking.
- 3
Carefully pack items securely to prevent damage during transport.
- 4
Label packages clearly with appropriate shipping information.
- 5
Follow any specific company procedures for repacking and documentation.
Example Answers
I start by inspecting the returned items for any damages and checking that all parts are included. Then, I clean the items if needed, and carefully repack them to ensure they are secure. Finally, I label the package with the correct shipping details.
Situational Interview Questions
If you are packing boxes and realize that a product is damaged, what steps would you take next?
How to Answer
- 1
Immediately assess the extent of the damage
- 2
Set aside the damaged item to avoid packing it
- 3
Notify a supervisor or team lead about the issue
- 4
Replace the damaged item with a suitable alternative if available
- 5
Document the incident as per the company's protocols
Example Answers
I would first check how damaged the product is, then I would set it aside to avoid including it in a shipment. Next, I would inform my supervisor about the damage and ask for instructions. If another similar item is available, I would replace the damaged one. Finally, I would fill out any necessary forms regarding the damaged item.
Imagine you are behind schedule on a packing assignment. What strategies would you employ to catch up?
How to Answer
- 1
Assess the current status and identify delays
- 2
Prioritize tasks based on urgency and importance
- 3
Increase efficiency by minimizing distractions and optimizing workflow
- 4
Communicate with the team for additional support if needed
- 5
Maintain a steady pace and focus on quality to avoid rework
Example Answers
I would first evaluate the packing process to see where delays are occurring. Then, I'd prioritize the most urgent tasks and focus on completing those first. Keeping distractions to a minimum would help me work faster while ensuring quality.
Don't Just Read Packer Questions - Practice Answering Them!
Reading helps, but actual practice is what gets you hired. Our AI feedback system helps you improve your Packer interview answers in real-time.
Personalized feedback
Unlimited practice
Used by hundreds of successful candidates
If a team member is not following packing procedures and it causes delays, how would you approach the situation?
How to Answer
- 1
Observe the team member discreetly to understand the issue.
- 2
Approach them privately to discuss the situation calmly.
- 3
Share specific examples of how the delays affect the team.
- 4
Offer help or resources to ensure they understand the procedures.
- 5
Encourage them to ask questions if they're unsure about the packing process.
Example Answers
I would first observe the team member to identify what exactly is causing the delays. Then, I would approach them privately and explain how following the packing procedures is important for the team's efficiency. I would also ask if they need any support or clarification on the procedures.
How would you handle a day when you have multiple orders with different packing requirements to fill?
How to Answer
- 1
Prioritize orders based on deadlines and complexities
- 2
Organize packing materials and tools based on order requirements
- 3
Create a checklist for each order to ensure accuracy
- 4
Communicate any issues or delays to the supervisor promptly
- 5
Stay focused and keep a steady pace to meet the daily targets.
Example Answers
I would start by reviewing all the orders and prioritizing them based on their deadlines and specific packing needs. I’d set up my workspace with the necessary materials for each order to streamline the process. Throughout the day, I would refer back to a checklist to ensure I don't miss anything and keep my supervisor informed about my progress.
If you identify a flaw in the current packing process, what steps would you take to suggest improvements?
How to Answer
- 1
Observe the packing process to identify specific flaws.
- 2
Document the issues with clear examples and data.
- 3
Propose actionable solutions that address the identified flaws.
- 4
Communicate your findings to the appropriate team or supervisor.
- 5
Be prepared to discuss the potential impact of your suggestions.
Example Answers
I would first observe the packing process to pinpoint exact flaws. After documenting these issues with clear data, I would propose solutions, such as rearranging packing stations or enhancing staff training to improve efficiency. Then, I would communicate these findings to my supervisor.
What would you do if you noticed a coworker ignoring safety procedures while packing?
How to Answer
- 1
Stay calm and approach the situation with a non-confrontational attitude
- 2
Politely remind your coworker about the safety procedures
- 3
If they don't respond, escalate the issue to a supervisor
- 4
Emphasize the importance of safety for everyone’s well-being
- 5
Document the situation if necessary for future reference
Example Answers
I would calmly approach my coworker and say, 'Hey, I noticed we aren't sticking to the safety procedures. It's important for all of us to follow them to stay safe.' If they continued to ignore it, I would inform our supervisor.
If you find that packages are frequently damaged in transit, what steps would you take to investigate and resolve the issue?
How to Answer
- 1
Assess the packaging materials used to ensure they meet safety standards.
- 2
Review handling procedures to identify any improper methods that might contribute to damage.
- 3
Gather data on the frequency and types of damage to identify patterns.
- 4
Communicate with shipping partners for insights into transit conditions.
- 5
Implement improvements in packaging or handling based on findings.
Example Answers
I would first check if the packaging materials are up to standard. Then, I'd observe the packing and handling procedures to spot any mistakes. Next, I would collect data on damage incidents to find trends, and finally, I'd collaborate with shipping partners to understand any challenges during transit.
What would you do if you receive an urgent request for a last-minute order that requires packing?
How to Answer
- 1
Stay calm and assess the urgency of the request.
- 2
Verify the details of the order such as items and quantities.
- 3
Prioritize tasks and communicate with your team if necessary.
- 4
Gather necessary packing materials and tools quickly.
- 5
Execute the packing efficiently, ensuring accuracy and quality.
Example Answers
I would first assess the details of the last-minute order to understand what needs to be packed. Then, I'd prioritize this task and communicate with my team to ensure everyone knows what we are working on. After preparing the packing materials, I would efficiently pack the items while maintaining quality.
If a customer reports that their package arrived incomplete, how would you handle the situation?
How to Answer
- 1
Listen carefully to the customer's concerns without interrupting.
- 2
Apologize sincerely for the inconvenience caused to the customer.
- 3
Gather all relevant information about the order and missing items.
- 4
Assure the customer that you will resolve the issue quickly.
- 5
Follow up with the customer once the resolution is implemented.
Example Answers
I would first listen to the customer's complaint and apologize for the inconvenience. Then, I would ask for details about the order and what items are missing. After gathering this information, I'd ensure to resolve the issue by sending the missing items as quickly as possible and follow up to confirm their satisfaction.
If you notice that a high volume of packing is required with a limited workforce, how would you prioritize tasks?
How to Answer
- 1
Assess the urgency of different packing tasks
- 2
Identify which orders are most time-sensitive
- 3
Delegate tasks based on team strengths
- 4
Use time management tools to track progress
- 5
Ensure communication is clear among team members
Example Answers
I would start by identifying the most urgent orders and prioritize those. Then, I would delegate tasks based on each team member's strengths to increase efficiency.
Don't Just Read Packer Questions - Practice Answering Them!
Reading helps, but actual practice is what gets you hired. Our AI feedback system helps you improve your Packer interview answers in real-time.
Personalized feedback
Unlimited practice
Used by hundreds of successful candidates
How would you communicate with other departments if a packing delay could impact shipping schedules?
How to Answer
- 1
Assess the situation quickly to understand the cause and impact of the delay
- 2
Notify key stakeholders in other departments as soon as possible
- 3
Provide clear and concise information about the delay and expected resolution time
- 4
Coordinate with the shipping department to explore possible adjustments
- 5
Follow up with updates as the situation evolves to maintain clear communication
Example Answers
I would first assess the delay's impact on shipping schedules. Then, I would promptly inform the shipping team and any other affected departments, sharing details about the cause and estimated time of resolution. I'd work with them to find solutions if necessary and keep everyone updated throughout the process.
Packer Position Details
Salary Information
Recommended Job Boards
CareerBuilder
www.careerbuilder.com/jobs/packerZipRecruiter
www.ziprecruiter.com/Jobs/PackerThese job boards are ranked by relevance for this position.
Related Positions
- Mule Packer
- Palletizer
- Machine Stacker
- Rack Carrier
- Package Pick Up
- Pack Master
- Pick Up
- Loader Helper
- Dumper
- Boat Loader
Similar positions you might be interested in.
Ace Your Next Interview!
Practice with AI feedback & get hired faster
Personalized feedback
Used by hundreds of successful candidates
Ace Your Next Interview!
Practice with AI feedback & get hired faster
Personalized feedback
Used by hundreds of successful candidates