Top 31 Rack Carrier Interview Questions and Answers [Updated 2025]
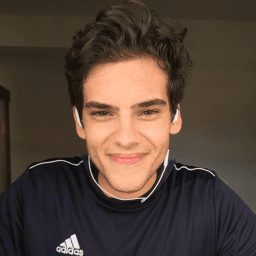
Andre Mendes
•
March 30, 2025
Preparing for a 'Rack Carrier' interview? This blog post is your ultimate guide to navigating the most common questions asked in interviews for this role. Dive into expertly crafted example answers and invaluable tips on how to respond with confidence and clarity. Whether you're a seasoned professional or new to the field, this resource equips you to impress potential employers and secure your desired position.
Download Rack Carrier Interview Questions in PDF
To make your preparation even more convenient, we've compiled all these top Rack Carrierinterview questions and answers into a handy PDF.
Click the button below to download the PDF and have easy access to these essential questions anytime, anywhere:
List of Rack Carrier Interview Questions
Behavioral Interview Questions
Can you describe a time when you worked as part of a team to achieve a goal related to rack management?
How to Answer
- 1
Use the STAR method: Situation, Task, Action, Result.
- 2
Pick a specific project related to rack management.
- 3
Explain your role clearly in the team.
- 4
Describe how collaboration led to success.
- 5
Quantify results if possible (e.g., reduced time, increased efficiency).
Example Answers
In my previous role at XYZ Warehouse, our team was tasked with reorganizing the rack layout to optimize space. I suggested a new layout based on our inventory needs. My role was to lead the team in mapping out the changes and communicating with staff. By working together, we reduced excess space by 20% and improved access to high-demand items.
Tell me about a situation where you identified a safety hazard while working with rack carriers. What did you do?
How to Answer
- 1
Think of a specific incident you experienced or observed.
- 2
Explain how you recognized the safety hazard.
- 3
Describe the actions you took to address the hazard.
- 4
Mention the outcome of your actions, if possible.
- 5
Highlight your commitment to safety and teamwork.
Example Answers
In my previous job, I noticed that some rack carriers were overloaded, which made them unstable. I immediately reported this to my supervisor and organized a team to redistribute the load safely. This not only corrected the issue but also prevented potential accidents.
Don't Just Read Rack Carrier Questions - Practice Answering Them!
Reading helps, but actual practice is what gets you hired. Our AI feedback system helps you improve your Rack Carrier interview answers in real-time.
Personalized feedback
Unlimited practice
Used by hundreds of successful candidates
Describe a challenging problem you encountered while transporting racks and how you overcame it.
How to Answer
- 1
Define the problem clearly and briefly.
- 2
Explain the steps you took to address the problem.
- 3
Discuss the outcome and what you learned from the experience.
- 4
Highlight teamwork or communication if applicable.
- 5
Be concise but specific with your example.
Example Answers
Once, we had a schedule conflict while transporting racks for a crucial event. I coordinated with the team to rearrange our routes and set new timelines, ensuring that we still met the deadline by working extra hours. It taught me the importance of flexibility and communication.
Give an example of how you had to adapt your approach during a potential change in logistics involving rack carriers.
How to Answer
- 1
Identify a specific situation where a change was proposed.
- 2
Explain the initial plan and how it needed to change.
- 3
Describe the adjustments you made to accommodate the new logistics.
- 4
Highlight the outcome of your adaptation.
- 5
Emphasize teamwork or communication aspects if applicable.
Example Answers
In my previous role, we faced a sudden change in supplier schedules. We were initially set to use a standard rack carrier method, but had to switch to a more flexible ordering process. I coordinated closely with the supplier and our logistics team to adjust the delivery frequency, which minimized delays and kept our inventory steady. As a result, we managed to maintain customer satisfaction despite the changes.
Describe a time when you had to lead a team in handling a difficult rack-moving project.
How to Answer
- 1
Select a specific project that had challenges.
- 2
Outline your role and the team's dynamics clearly.
- 3
Highlight the strategies you used to overcome obstacles.
- 4
Emphasize the outcome and what you learned.
- 5
Keep it concise and focused on leadership actions.
Example Answers
In my previous role, we had to move several heavy racks to a new warehouse. I led a team of 5 people and we encountered issues with the loading dock being too small. I organized a brainstorming session, and we devised a plan to disassemble the racks and move them in parts. This approach not only resolved the space issue but also allowed us to work more efficiently, completing the project ahead of schedule. I learned the importance of teamwork and adaptive planning.
Tell me about a time when you successfully improved the stock management system for racks.
How to Answer
- 1
Identify a specific problem with the previous system
- 2
Explain the solution you proposed and implemented
- 3
Highlight the results and benefits of your improvement
- 4
Mention any tools or systems you used to support your solution
- 5
Consider including teamwork or collaboration aspects if relevant
Example Answers
In my previous role, I noticed that our rack stock management was inefficient due to outdated software. I proposed implementing a new inventory management system that integrated barcode scanning. This reduced our stock retrieval time by 30% and improved accuracy in tracking inventory levels. My supervisor noted a significant decrease in stock discrepancies after the implementation.
Have you ever suggested a change that improved efficiency in rack handling? What was it?
How to Answer
- 1
Think of a specific instance where you identified a problem in rack handling.
- 2
Describe the change you suggested and why it was necessary.
- 3
Mention any metrics or outcomes that demonstrate the improvement.
- 4
Focus on your role in the change process and how you communicated it.
- 5
Keep the answer concise and relevant to rack handling efficiency.
Example Answers
In my previous job, I noticed that our rack layout caused delays during peak hours due to congestion. I suggested reorganizing the rack layout to separate outgoing shipments by destination, which reduced retrieval time by 30%.
Can you give an example of a time when you took initiative in a project involving rack carriers?
How to Answer
- 1
Identify a specific project where you noticed a problem or opportunity.
- 2
Explain the steps you took to address the issue or improve the project.
- 3
Describe the outcome and how it benefited the team or company.
- 4
Use metrics or concrete results to demonstrate impact if possible.
- 5
Keep your response clear and focus on your individual contribution.
Example Answers
In my previous job, I noticed our rack carriers were often disorganized, slowing down the workflow. I took the initiative to design a new storage plan that made it easier to find and retrieve carriers. As a result, we reduced retrieval time by 30%, which improved overall efficiency.
Describe a time you had to handle a customer's concern related to rack delivery.
How to Answer
- 1
Use the STAR method: Situation, Task, Action, Result.
- 2
Focus on a specific incident to make your answer compelling.
- 3
Explain how you understood the customer's concern.
- 4
Detail the steps you took to resolve the issue.
- 5
Share the positive outcome and what you learned.
Example Answers
In my previous role, a customer called upset because their rack delivery was delayed. I listened carefully to their concern, reassured them that I would investigate, and contacted the logistics team. I discovered a shipping error and arranged for expedited delivery. The customer received their racks the following day and thanked me for my prompt assistance.
Don't Just Read Rack Carrier Questions - Practice Answering Them!
Reading helps, but actual practice is what gets you hired. Our AI feedback system helps you improve your Rack Carrier interview answers in real-time.
Personalized feedback
Unlimited practice
Used by hundreds of successful candidates
Technical Interview Questions
What types of equipment have you used in the handling of rack carriers, and how proficient are you with each?
How to Answer
- 1
List specific equipment you've used with rack carriers like forklifts or pallet jacks.
- 2
Mention your level of proficiency for each piece of equipment.
- 3
Include any training or certifications relevant to the equipment.
- 4
Provide examples of scenarios where you successfully used the equipment.
- 5
Keep your answer structured, starting from the most familiar equipment.
Example Answers
I have used forklifts extensively in my previous jobs, and I am certified to operate them. I am proficient in loading and unloading rack carriers safely and efficiently.
Explain the standard procedures for loading and unloading racks in a warehouse setting.
How to Answer
- 1
Start with safety protocols including personal protective equipment (PPE)
- 2
Describe the organization of racks for easy access and efficient loading
- 3
Explain the use of equipment such as pallet jacks or forklifts for heavy loads
- 4
Mention the importance of checking inventory accuracy during both loading and unloading
- 5
Conclude with the need for clear communication among team members
Example Answers
When loading or unloading racks in a warehouse, I prioritize safety by wearing appropriate PPE. I organize the items by size and weight to ensure easy access. I use a forklift for heavier items, and I always double-check the inventory to make sure records match. Finally, clear communication with my team helps to streamline the process.
Don't Just Read Rack Carrier Questions - Practice Answering Them!
Reading helps, but actual practice is what gets you hired. Our AI feedback system helps you improve your Rack Carrier interview answers in real-time.
Personalized feedback
Unlimited practice
Used by hundreds of successful candidates
What safety protocols do you follow when operating heavy machinery for rack transportation?
How to Answer
- 1
Always conduct a pre-operation inspection of the machinery.
- 2
Wear appropriate personal protective equipment like hard hats and gloves.
- 3
Follow the manufacturer's operating guidelines for the machinery.
- 4
Maintain a clear communication with team members during operation.
- 5
Stay aware of your surroundings and identify potential hazards.
Example Answers
Before operating any heavy machinery, I always perform a thorough pre-operation inspection to ensure everything is functioning correctly. I also make sure to wear my hard hat and gloves for safety and follow the manufacturer's guidelines for operation.
How do you keep track of inventory levels and ensure accuracy when working with racks?
How to Answer
- 1
Use inventory management software or tools for tracking.
- 2
Conduct regular physical counts of inventory to verify records.
- 3
Label racks and items clearly for easy identification.
- 4
Implement a first-in-first-out (FIFO) system to manage stock efficiently.
- 5
Create a checklist for handling new stock and inventory adjustments.
Example Answers
I use inventory management software to track stock levels and ensure accuracy. Regular physical counts help me verify that our records match what is actually in the racks.
Describe how you perform routine maintenance checks on rack carrier equipment.
How to Answer
- 1
Start with a checklist of components to inspect regularly.
- 2
Explain how you document findings and track maintenance performed.
- 3
Emphasize safety precautions you take during maintenance checks.
- 4
Mention any tools or equipment you use for inspections.
- 5
Include how you report issues and follow up on repairs.
Example Answers
I conduct routine maintenance checks by following a checklist that includes inspecting the hoist, chain, and brakes. I document any findings in our maintenance log and prioritize any necessary repairs according to urgency.
What software or systems have you used for managing rack inventory and logistics?
How to Answer
- 1
Identify specific software you have used such as WMS systems.
- 2
Mention any experience with inventory tracking or logistics software.
- 3
Highlight your familiarity with systems like SAP or Oracle, if applicable.
- 4
Discuss your ability to adapt to new software quickly.
- 5
Provide examples of how you have used these systems to improve processes.
Example Answers
I have used a Warehouse Management System (WMS) like Manhattan Associates for tracking our rack inventory and streamlining logistics.
Can you explain how rack carriers fit into the overall supply chain process?
How to Answer
- 1
Define what rack carriers are and their primary function.
- 2
Describe their role in transportation across the supply chain.
- 3
Explain how they improve efficiency and reduce costs.
- 4
Mention their importance in inventory management and order fulfillment.
- 5
Highlight the connection between rack carriers and logistics providers.
Example Answers
Rack carriers are specialized vehicles designed to transport goods efficiently. They are crucial in the supply chain as they help move products from manufacturers to warehouses, optimizing the transportation process. By using rack carriers, businesses can reduce costs and improve delivery times.
What industry regulations must one comply with when working with rack carriers?
How to Answer
- 1
Research specific regulations related to freight and transportation logistics.
- 2
Understand safety regulations such as OSHA standards for equipment.
- 3
Familiarize yourself with local and federal regulations like DOT guidelines.
- 4
Mention relevant certifications or compliance requirements for handling goods.
- 5
Highlight the importance of environmental regulations, if applicable.
Example Answers
When working with rack carriers, it's essential to comply with DOT regulations and ensure all safety standards from OSHA are met, especially regarding equipment use and transport safety.
How do you determine the safe load capacity for racks during transportation?
How to Answer
- 1
Review manufacturer specifications for load capacity.
- 2
Consider the type of materials being transported.
- 3
Evaluate the conditions of transportation such as road type and weather.
- 4
Use tools like load calculators or software if available.
- 5
Perform a risk assessment to account for safety margins.
Example Answers
I start by consulting the manufacturer's specifications to find the rated load capacity. Then, I assess the materials I'm transporting, considering their weight and stability. It's also crucial to factor in the transportation conditions, like potholes or wet roads that might increase risk.
What strategies do you employ to optimize routes for transporting racks?
How to Answer
- 1
Analyze the delivery locations to identify the most efficient routes.
- 2
Utilize route optimization software to minimize travel time and distance.
- 3
Consider traffic patterns and peak hours to avoid delays.
- 4
Group deliveries by geographic area to reduce backtracking.
- 5
Regularly review and adjust routes based on performance data.
Example Answers
I use route optimization software to find the quickest paths and adjust based on traffic updates. By grouping nearby deliveries, I can minimize backtracking and save time.
Don't Just Read Rack Carrier Questions - Practice Answering Them!
Reading helps, but actual practice is what gets you hired. Our AI feedback system helps you improve your Rack Carrier interview answers in real-time.
Personalized feedback
Unlimited practice
Used by hundreds of successful candidates
Situational Interview Questions
If you were in the middle of a rack transport and a safety incident occurred, what steps would you take?
How to Answer
- 1
Assess the immediate situation for danger and the safety of personnel
- 2
Communicate clearly with the team about the incident
- 3
Follow established safety protocols and procedures
- 4
Report the incident to a supervisor or safety officer
- 5
Ensure the safety of equipment and goods if possible
Example Answers
Firstly, I would quickly assess the situation to determine if anyone is in immediate danger and ensure their safety. I would alert my team about the incident. Then, I would follow our safety protocols, reporting the incident to my supervisor, and taking steps to secure the area if necessary.
You have multiple racks to transport but limited time. How would you decide which tasks to prioritize?
How to Answer
- 1
Assess the urgency of each transport task based on deadlines.
- 2
Consider the weight and volume of the racks to optimize logistics.
- 3
Evaluate the destination distances to minimize travel time.
- 4
Prioritize tasks based on location clustering to reduce backtracking.
- 5
Communicate with the team to ensure resources are allocated effectively.
Example Answers
I would first look at which racks have the closest deadlines and transport those first. Then, I'd group the remaining racks by destination to minimize travel time.
Don't Just Read Rack Carrier Questions - Practice Answering Them!
Reading helps, but actual practice is what gets you hired. Our AI feedback system helps you improve your Rack Carrier interview answers in real-time.
Personalized feedback
Unlimited practice
Used by hundreds of successful candidates
What would you do if a conflict arose with a co-worker over the handling of racks?
How to Answer
- 1
Stay calm and listen to your co-worker's perspective.
- 2
Acknowledge the conflict and validate their concerns.
- 3
Suggest finding a mutual solution by discussing the issues together.
- 4
Focus on the goal of safe and efficient rack handling.
- 5
If needed, involve a supervisor for mediation.
Example Answers
I would first listen to my co-worker to understand their viewpoint. Then, I would acknowledge their concerns and suggest we discuss the issue together to find a solution that works for both of us.
Imagine a rack is damaged during transport. What process would you follow to address this situation?
How to Answer
- 1
Inspect the damage immediately and document it with photos.
- 2
Assess the extent of the damage to determine if repairs are possible.
- 3
Notify your supervisor and relevant stakeholders about the incident.
- 4
Follow company policies for reporting and handling damaged equipment.
- 5
Arrange for repairs or replacements based on company procedures.
Example Answers
First, I would inspect the rack to assess the damage and take photos for documentation. Then, I would inform my supervisor and follow the company's reporting process to ensure everyone is aware and to initiate repairs or replacements as needed.
How would you handle discovering that racks do not meet quality standards during inspections?
How to Answer
- 1
Identify the specific quality standards that were not met
- 2
Communicate findings to the relevant team or supervisor
- 3
Implement an immediate corrective action plan to address the issue
- 4
Document the inspection results and actions taken for accountability
- 5
Review and adjust inspection processes if necessary to prevent future issues
Example Answers
I would first determine the exact quality standards that were not met during the inspection. Then, I would notify my supervisor immediately to discuss the findings. Together, we would create a corrective action plan to fix the issue, ensuring all affected racks are re-evaluated. Finally, I would document everything to maintain clear records.
How would you deal with an unexpected delay in the delivery of racks?
How to Answer
- 1
Stay calm and assess the situation immediately
- 2
Communicate the delay to relevant stakeholders promptly
- 3
Identify alternative solutions or temporary measures
- 4
Document the delay and implications for future reference
- 5
Follow up with the supplier to expedite the delivery.
Example Answers
I would first assess the cause of the delay and then notify my team and any affected clients right away. Next, I would explore alternative ways to fulfill our immediate needs, such as sourcing racks from a nearby supplier.
If you were assigned to train new staff on using rack carriers, what key points would you cover?
How to Answer
- 1
Start with basic safety protocols when using rack carriers
- 2
Explain the components and functions of the rack carrier
- 3
Demonstrate proper loading and unloading techniques
- 4
Discuss the importance of weight distribution and balance
- 5
Highlight maintenance checks before usage to ensure safety
Example Answers
I would begin with safety protocols to ensure everyone operates the rack carriers safely. Then, I'd explain its components and how each part functions. It's crucial to demonstrate proper loading techniques, so everyone understands weight distribution. Lastly, I would emphasize regular maintenance checks to keep the equipment in good working order.
How would you communicate an unexpected issue with a load of racks to your supervisor?
How to Answer
- 1
Stay calm and assess the situation first
- 2
Gather all necessary details about the issue
- 3
Communicate clearly and concisely to your supervisor
- 4
Use specific examples to illustrate the problem
- 5
Suggest possible solutions or next steps if applicable
Example Answers
I would first take a moment to understand the problem, then I'd inform my supervisor about the issue, including details such as the type of rack affected and the nature of the problem. I would also suggest checking the load limits as a potential next step.
If you realized you made an error in loading the racks, what would you do to rectify it?
How to Answer
- 1
Acknowledge the error quickly to prevent further issues.
- 2
Assess the impact of the error on the load and safety.
- 3
Communicate with the team about the mistake.
- 4
Take immediate corrective action to fix the loading.
- 5
Document the error and corrective steps for future reference.
Example Answers
I would immediately acknowledge the error and stop any further loading. Then, I would assess the situation to see how it affects the load. I would inform my supervisor and the team, and work together to safely unload and reload the racks correctly. Finally, I would document what went wrong to help prevent this in the future.
How would you handle a situation where two team members have conflicting views on how to tackle a rack-moving task?
How to Answer
- 1
Listen to both team members' perspectives fully before intervening.
- 2
Encourage open communication and collaboration to find common ground.
- 3
Suggest a compromise or a pilot test of both approaches if possible.
- 4
Focus on the overall goal of the task and how to achieve it effectively.
- 5
Remain neutral and objective, facilitating the discussion rather than taking sides.
Example Answers
I would first listen to both team members to understand their viewpoints. Then, I would facilitate a discussion where they can express their ideas and find a compromise. If the views are equally valid, we might try a pilot of both approaches to see which works better.
Don't Just Read Rack Carrier Questions - Practice Answering Them!
Reading helps, but actual practice is what gets you hired. Our AI feedback system helps you improve your Rack Carrier interview answers in real-time.
Personalized feedback
Unlimited practice
Used by hundreds of successful candidates
Rack Carrier Position Details
Related Positions
- Drum Carrier
- Top Carrier
- Cloth Carrier
- Machine Stacker
- Palletizer
- Packer
- Hauler
- Mule Packer
- Coal Carrier
- Package Pick Up
Similar positions you might be interested in.
Ace Your Next Interview!
Practice with AI feedback & get hired faster
Personalized feedback
Used by hundreds of successful candidates
Ace Your Next Interview!
Practice with AI feedback & get hired faster
Personalized feedback
Used by hundreds of successful candidates