Top 32 Palletizer Interview Questions and Answers [Updated 2025]
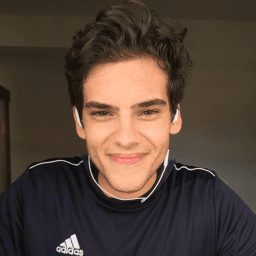
Andre Mendes
•
March 30, 2025
Preparing for a Palletizer interview? You've come to the right place! This blog post compiles the most common interview questions for the Palletizer role, offering insightful example answers and practical tips to help you respond confidently and effectively. Whether you're new to the field or looking to sharpen your interview skills, our guide is designed to set you up for success and help you stand out.
Download Palletizer Interview Questions in PDF
To make your preparation even more convenient, we've compiled all these top Palletizerinterview questions and answers into a handy PDF.
Click the button below to download the PDF and have easy access to these essential questions anytime, anywhere:
List of Palletizer Interview Questions
Situational Interview Questions
If a safety alarm goes off while you are working, what actions would you take?
How to Answer
- 1
Immediately stop all work and assess the situation
- 2
Follow the established safety protocols and procedures
- 3
Notify your supervisor or safety officer if necessary
- 4
Evacuate the area if required, and help others to do the same
- 5
Do not re-enter the area until it is deemed safe
Example Answers
If a safety alarm goes off, I would stop my work, follow the emergency procedures, and evacuate the area quickly while ensuring others are leaving too.
What would you do if a palletizer jams during a high-speed production run?
How to Answer
- 1
Stay calm and assess the situation quickly.
- 2
Stop the palletizer safely to prevent further issues.
- 3
Identify the cause of the jam systematically.
- 4
Communicate with the team to inform them of the situation.
- 5
Once cleared, restart the machine and monitor for further issues.
Example Answers
I would quickly stop the palletizer to avoid damaging the equipment, identify the cause of the jam, and communicate with my team so we can resolve it effectively.
Don't Just Read Palletizer Questions - Practice Answering Them!
Reading helps, but actual practice is what gets you hired. Our AI feedback system helps you improve your Palletizer interview answers in real-time.
Personalized feedback
Unlimited practice
Used by hundreds of successful candidates
How would you handle a situation where you must complete palletizing while the order is running behind schedule?
How to Answer
- 1
Prioritize tasks to identify which pallets need immediate attention.
- 2
Communicate with your team to ensure everyone is aware of the situation.
- 3
Optimize your workflow by focusing on efficiency techniques, such as having materials ready ahead.
- 4
Consider adjusting the palletizing method or techniques to speed up the process without sacrificing quality.
- 5
Stay calm and focused to maintain productivity under pressure.
Example Answers
I would assess which orders are closest to completion and prioritize palletizing those first. I would also communicate with my team to ensure we are all aligned on the urgency.
If you noticed unsafe practices being followed in the palletizing area, what steps would you take?
How to Answer
- 1
Assess the situation quickly and identify specific unsafe practices.
- 2
Prioritize immediate safety and remove any personnel from danger if necessary.
- 3
Report the unsafe practices to a supervisor or safety officer promptly.
- 4
Suggest corrective actions or improvements based on your observations.
- 5
Follow up to ensure that safety measures are implemented.
Example Answers
I would first assess the situation to clearly identify the unsafe practices. If someone is in immediate danger, I would ensure their safety and then report the issue to my supervisor, suggesting specific improvements based on what I observed.
How would you resolve a disagreement with a team member regarding the setup of the palletizer?
How to Answer
- 1
Listen actively to the team member's concerns and ideas
- 2
Share your own perspective clearly and constructively
- 3
Seek common ground that meets operational needs
- 4
Suggest a trial run of both setups to evaluate performance
- 5
Involve a supervisor if a resolution cannot be reached collaboratively
Example Answers
I would first listen to my teammate's setup proposal and understand their reasoning. Then, I would explain my approach and how it aligns with our goals. If we still disagree, I would suggest we test both setups and see which one performs better, allowing us to make an informed decision together.
If productivity dropped unexpectedly, how would you analyze and address the issue?
How to Answer
- 1
Review production data to identify when and where the drop occurred.
- 2
Check equipment for malfunctions or inefficiencies impacting output.
- 3
Assess workforce performance and morale to determine if there's a human factor.
- 4
Communicate with team members for insights and suggestions on potential issues.
- 5
Implement small tests or adjustments to see if productivity improves.
Example Answers
I would first review the production data to identify when the drop started and its specific location. Then I'd inspect the equipment for any malfunctions. I would also speak with my team to gather their input on the situation and make necessary adjustments based on our findings.
How would you react if your supervisor asked you to change the way you palletize without much notice?
How to Answer
- 1
Acknowledge the request positively
- 2
Ask questions to clarify the new method
- 3
Express willingness to adapt and learn
- 4
Mention the importance of safety and efficiency
- 5
Share any relevant experience with similar changes
Example Answers
I would respond positively and ask my supervisor for more details about the new palletizing method to ensure I understand their expectations clearly.
If raw materials for palletizing are delayed, how would you manage workflow?
How to Answer
- 1
Assess current inventory levels and prioritize available materials.
- 2
Communicate with the supplier to get updated timelines on raw material delivery.
- 3
Adjust team schedules and tasks to keep everyone productive.
- 4
Implement temporary alternative workflows with existing materials.
- 5
Document the situation and prepare for reporting and future process improvements.
Example Answers
I would first check our current stock and determine what materials are available. Then, I would get in touch with the supplier to find out when the raw materials are expected. Meanwhile, I'd work with my team to shift tasks around to keep everyone focused on productive activities that don't rely on the delayed materials.
What would you do if you noticed a colleague was struggling to keep up with palletizing tasks?
How to Answer
- 1
Observe the colleague's work pace and the specific tasks they are struggling with.
- 2
Approach the colleague in a supportive manner, asking if they need help.
- 3
Offer to assist them with their current tasks to lighten their load.
- 4
Suggest taking a short break together to recharge and refocus.
- 5
Communicate with your supervisor if the issue persists and requires additional support.
Example Answers
I would first assess what specific tasks my colleague is having trouble with and then approach them to see if they need any help. I would offer to assist with some of their palletizing duties to ease their workload.
How would you handle a situation where a critical piece of palletizing equipment fails mid-shift?
How to Answer
- 1
Assess the situation quickly and ensure safety for all employees.
- 2
Notify your supervisor and the maintenance team immediately.
- 3
Implement a temporary solution if possible, like manual palletizing.
- 4
Communicate effectively with your team about the situation and next steps.
- 5
Ensure to document the incident for future reference and improvement.
Example Answers
In the event of equipment failure, I would first ensure everyone's safety and shut down the equipment. Then, I would promptly inform my supervisor and maintenance. If time allows, I would briefly engage the team to see if we could manually assist with palletizing while waiting for repairs.
Don't Just Read Palletizer Questions - Practice Answering Them!
Reading helps, but actual practice is what gets you hired. Our AI feedback system helps you improve your Palletizer interview answers in real-time.
Personalized feedback
Unlimited practice
Used by hundreds of successful candidates
How would you approach making improvements to standard operating procedures in the palletizing area?
How to Answer
- 1
Identify key performance metrics currently used
- 2
Gather input from team members for practical insights
- 3
Analyze any inefficiencies or bottlenecks in the process
- 4
Test new procedures on a small scale before full implementation
- 5
Document changes and train staff on new procedures
Example Answers
I would start by reviewing current performance metrics to identify areas for improvement. Then, I'd gather feedback from the team to understand their challenges and suggestions.
Technical Interview Questions
What are the key quality control measures you use during the palletizing process?
How to Answer
- 1
Identify critical checkpoints in the palletizing process for inspections
- 2
Use specific metrics to measure load stability and item placement
- 3
Implement regular training for staff on quality control standards
- 4
Document any discrepancies and take corrective actions swiftly
- 5
Encourage a culture of quality awareness among team members
Example Answers
I focus on three key areas: ensuring that each layer of product is stacked according to specifications, verifying the weight distribution on the pallet, and conducting final inspections before the pallets are wrapped and shipped.
What factors do you consider when following packaging specifications for different products?
How to Answer
- 1
Understand the specific product requirements and characteristics
- 2
Follow safety and compliance regulations precisely
- 3
Ensure proper materials are used for each product type
- 4
Check weight and size specifications to meet shipping standards
- 5
Maintain consistency to prevent damage during transportation
Example Answers
I consider the product's characteristics, like fragility, to choose the right materials and ensure compliance with safety regulations.
Don't Just Read Palletizer Questions - Practice Answering Them!
Reading helps, but actual practice is what gets you hired. Our AI feedback system helps you improve your Palletizer interview answers in real-time.
Personalized feedback
Unlimited practice
Used by hundreds of successful candidates
What types of palletizing equipment have you operated, and what is your level of proficiency with each?
How to Answer
- 1
Identify specific types of palletizing equipment you've used.
- 2
State your proficiency level clearly for each type.
- 3
Include any relevant certifications or training.
- 4
Mention your experience in fast-paced environments.
- 5
Highlight any troubleshooting skills you have.
Example Answers
I have operated both robotic and manual palletizers. I'm proficient with robotic palletizers, having worked with the KUKA and FANUC models for over 3 years. I have basic experience with manual palletizing, where I efficiently stacked products for 2 years.
Can you explain the basic maintenance procedures necessary for a palletizer?
How to Answer
- 1
Mention regular inspections of mechanical parts for wear and tear
- 2
Include lubrication schedules for moving components
- 3
Discuss troubleshooting common issues like jams or misalignment
- 4
Highlight the importance of cleaning the palletizer to prevent debris buildup
- 5
Explain the need for periodic software updates and adjustments
Example Answers
Basic maintenance for a palletizer includes regular inspections for wearing parts and ensuring all mechanical elements are in good condition. I follow a routine lubrication schedule for components like conveyors and bearings to minimize friction.
How do you determine the best way to stack and arrange products on a pallet?
How to Answer
- 1
Consider the weight distribution to ensure stability.
- 2
Stack heavier items at the bottom and lighter ones on top.
- 3
Use uniform shapes for easier stacking.
- 4
Follow manufacturer guidelines for stacking limits.
- 5
Take into account the size of the pallets and transportation methods.
Example Answers
I assess the weight and size of each product, placing heavier items first on the pallet to maintain balance. I also ensure uniform shapes are stacked together to prevent movement during transport.
Describe the troubleshooting steps you take when a palletizer malfunctions.
How to Answer
- 1
Begin with observing the system for visible issues.
- 2
Check the error codes on the control panel for specific guidance.
- 3
Inspect critical components such as sensors and drive motors.
- 4
Test the palletizer after each fix to see if the issue is resolved.
- 5
Document findings and solutions to build a knowledge base for future maintenance.
Example Answers
First, I observe the palletizer to identify any obvious mechanical issues. Then, I check for error codes and, if necessary, inspect components like sensors. If adjustments don't work, I test the system to confirm if the problem persists.
What experience do you have with automated palletizing systems?
How to Answer
- 1
Mention any specific automated palletizing systems you have worked with
- 2
Describe your role and responsibilities in using these systems
- 3
Share any troubleshooting or maintenance experience you had with them
- 4
Highlight any improvements or efficiencies you contributed to while using the systems
- 5
Be ready to discuss safety protocols and training you have received related to palletizing
Example Answers
I have worked with the XYZ Automated Palletizer for over two years in my previous position. I operated the system daily, ensuring optimal performance and conducting routine maintenance. I identified several efficiency improvements that increased our throughput by 15%. I also adhered to strict safety protocols during operation.
What specific safety inspections do you perform before operating a palletizer?
How to Answer
- 1
Check for any visible damage to the palletizer or surrounding equipment.
- 2
Ensure that safety guards and emergency stops are functional.
- 3
Verify that the area is clear of hazards and obstacles.
- 4
Inspect the pallet size and specifications for compliance.
- 5
Make sure all safety lights and indicators are operational.
Example Answers
Before operating the palletizer, I check for any visible damage, ensure safety guards are in place, and verify that all emergency stops are functioning properly.
How do you determine the appropriate handling techniques for different types of packages?
How to Answer
- 1
Assess the size and weight of the package to ensure safe handling.
- 2
Identify the material of the package and its contents to prevent damage.
- 3
Consider the shape of the package for effective stacking and stability.
- 4
Check for any special handling instructions on the package label.
- 5
Use equipment and techniques suited for the package type, such as forklifts for heavy loads.
Example Answers
I start by checking the package size and weight to decide if I need extra help or equipment. Then, I look at the material and contents to ensure I handle it properly. If it’s fragile, I’m extra careful.
What software or monitoring systems are you familiar with in regard to palletizing processes?
How to Answer
- 1
Identify specific palletizing software you have used, such as SAP or Oracle.
- 2
Mention any monitoring systems like SCADA or PLC you have experience with.
- 3
Talk about how these systems improve efficiency and reduce errors in the palletizing process.
- 4
Relate your experience to real-world outcomes, like production speed or accuracy.
- 5
Keep your answer concise and relevant to the job description.
Example Answers
I have experience using SAP for tracking pallet inventory and monitoring production levels. Additionally, I'm familiar with SCADA systems that help oversee the palletizing process, ensuring that everything runs smoothly and efficiently.
Don't Just Read Palletizer Questions - Practice Answering Them!
Reading helps, but actual practice is what gets you hired. Our AI feedback system helps you improve your Palletizer interview answers in real-time.
Personalized feedback
Unlimited practice
Used by hundreds of successful candidates
Behavioral Interview Questions
Describe a time when you had to work closely with a team to meet a production deadline.
How to Answer
- 1
Select a specific project where teamwork was essential.
- 2
Outline the goal and the deadline you faced.
- 3
Describe your role and how you contributed to the team.
- 4
Highlight any challenges you faced and how you overcame them.
- 5
Conclude with the outcome and what you learned from the experience.
Example Answers
In my previous role as a production assistant, we had a major order due in two weeks. I coordinated with the assembly team to streamline processes. We faced a delay due to a supply shortage, but I communicated with suppliers to expedite deliveries. In the end, we met the deadline, and I learned the importance of clear communication.
Can you tell me about a situation where you identified a problem in the palletizing process and how you resolved it?
How to Answer
- 1
Describe a specific problem you encountered.
- 2
Explain how you identified the root cause.
- 3
Detail the solution you implemented.
- 4
Mention any tools or techniques you used.
- 5
Share the outcome and any improvements seen.
Example Answers
In a previous role, I noticed that the pallets were becoming unstable during transport. I identified that improper load distribution was the issue. I organized a review of the palletizing method and used specific load balancing techniques. After implementing changes, we saw a 25% decrease in product damage during shipping.
Don't Just Read Palletizer Questions - Practice Answering Them!
Reading helps, but actual practice is what gets you hired. Our AI feedback system helps you improve your Palletizer interview answers in real-time.
Personalized feedback
Unlimited practice
Used by hundreds of successful candidates
Give an example of a time when you ensured safety standards were met in your previous role.
How to Answer
- 1
Think of a specific incident where you prioritized safety.
- 2
Describe the safety standards you followed or implemented.
- 3
Explain your role in ensuring compliance with those standards.
- 4
Highlight the outcome or impact of your actions on safety.
- 5
Keep it concise, focusing on clear actions and results.
Example Answers
In my last job, I noticed that some employees were not wearing their safety gear while operating the palletizer. I organized a brief training session on the importance of personal protective equipment, and ensured everyone had the correct gear. This led to a 30% reduction in minor injuries over the following months.
Tell me about a time when you had to communicate an important change to your team.
How to Answer
- 1
Choose a specific situation where change was necessary.
- 2
Explain the context and why the change was important.
- 3
Describe how you communicated the change to the team.
- 4
Discuss the outcome and how the team responded.
- 5
Highlight any skills you used, like clarity or empathy.
Example Answers
In my previous role, we had to switch suppliers for our packing materials due to cost issues. I gathered the team, explained the reasons for the change, and emphasized how it would improve efficiency. We then discussed their concerns, and I made sure to address each one. The team adapted well, and the new supplier ultimately saved us time and money.
Describe a situation where you took the lead in a palletizing project.
How to Answer
- 1
Identify a specific project where you led the palletizing effort.
- 2
Describe your role and responsibilities clearly.
- 3
Explain the challenges faced and how you overcame them.
- 4
Highlight the results and improvements achieved due to your leadership.
- 5
Use metrics or data if available to quantify your success.
Example Answers
In my previous role at XYZ Corp, I led a palletizing project to optimize our packaging line. I organized the team, scheduled shifts, and implemented a new stacking method. We faced issues with product stability, but I introduced quality checks that reduced damage by 30%. As a result, we increased throughput by 20%.
Describe how you prioritize your tasks during a busy shift.
How to Answer
- 1
Identify the most urgent tasks first based on deadlines or impact.
- 2
Use a checklist to track completed tasks and manage remaining ones.
- 3
Communicate with team members to delegate responsibilities when possible.
- 4
Stay flexible and ready to adjust priorities as situations change.
- 5
Regularly review your progress to keep on track and avoid getting overwhelmed.
Example Answers
During a busy shift, I start by listing out the tasks I need to complete and identifying which ones are most urgent, like filling pallets for shipping deadlines. I keep a checklist to mark off tasks as I complete them. If I see that I'm falling behind, I communicate with my teammates to share the workload.
Tell me about a time when you went above and beyond your regular job duties as a palletizer.
How to Answer
- 1
Identify a specific situation where you took extra initiative.
- 2
Explain the task you went above and beyond in clearly.
- 3
Describe the impact of your actions on your team, product, or process.
- 4
Use quantifiable results if possible, like time saved or increased efficiency.
- 5
Connect your experience to how it relates to the role you are applying for.
Example Answers
At my last job, we faced a high demand that required faster palletizing. I stayed late to help my team improve our workflow. By reorganizing our layout, we increased our output by 20%, ensuring timely deliveries.
Can you provide an example of how attention to detail helped you avoid a mistake while palletizing?
How to Answer
- 1
Think of a specific instance where you caught a mistake because of careful checking.
- 2
Mention the steps you took to ensure everything was correct during the palletizing process.
- 3
Highlight what the result was after your attention to detail saved the day.
- 4
Keep your answer focused on your personal involvement and actions.
- 5
Use clear and concise language to make your point.
Example Answers
Once, while palletizing a shipment, I noticed that the weight distribution was off. I double-checked the product weights and realized I was about to place a heavier box on top of a lighter one. I rearranged them to maintain stability, which prevented damage during transport.
Have you ever trained a new employee on palletizing? What was the experience like?
How to Answer
- 1
Start with a brief overview of your training experience.
- 2
Include specific techniques you used to teach palletizing.
- 3
Mention any challenges faced and how you overcame them.
- 4
Highlight the positive outcomes for the new employee.
- 5
Conclude with what you learned from the training experience.
Example Answers
Yes, I trained a new employee on palletizing by showing them the proper techniques and safety protocols. We practiced together for a few shifts, which helped reinforce their learning. Initially, they struggled with speed, but by the end of the week, they were efficient and confident. It was rewarding to see their progress and I learned the importance of patience in training.
Don't Just Read Palletizer Questions - Practice Answering Them!
Reading helps, but actual practice is what gets you hired. Our AI feedback system helps you improve your Palletizer interview answers in real-time.
Personalized feedback
Unlimited practice
Used by hundreds of successful candidates
How do you handle constructive feedback about your work in the palletizing area?
How to Answer
- 1
Listen actively to the feedback without interrupting.
- 2
Ask clarifying questions if anything is unclear.
- 3
Thank the person for their feedback to show appreciation.
- 4
Reflect on the feedback and identify specific actions to improve.
- 5
Implement the feedback in your work and follow up to show progress.
Example Answers
I always listen carefully to constructive feedback and take notes if necessary. If I don't fully understand, I ask questions to get clarity. I appreciate the feedback because it helps me improve my palletizing skills.
Palletizer Position Details
Recommended Job Boards
These job boards are ranked by relevance for this position.
Related Positions
- Machine Stacker
- Packer
- Rack Carrier
- Hauler
- Mule Packer
- Silo Operator
- Ship Loader
- Package Pick Up
- Pick Up
- Silo Worker
Similar positions you might be interested in.
Ace Your Next Interview!
Practice with AI feedback & get hired faster
Personalized feedback
Used by hundreds of successful candidates
Ace Your Next Interview!
Practice with AI feedback & get hired faster
Personalized feedback
Used by hundreds of successful candidates