Top 30 Silo Worker Interview Questions and Answers [Updated 2025]
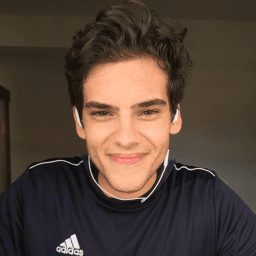
Andre Mendes
•
March 30, 2025
Preparing for a Silo Worker interview? Our updated guide for 2025 covers the most common questions you’re likely to face. Dive into expertly crafted example answers and insightful tips that will help you respond with confidence and clarity. Whether you're new to the field or a seasoned professional, this post is designed to equip you with the tools needed to impress potential employers.
Download Silo Worker Interview Questions in PDF
To make your preparation even more convenient, we've compiled all these top Silo Workerinterview questions and answers into a handy PDF.
Click the button below to download the PDF and have easy access to these essential questions anytime, anywhere:
List of Silo Worker Interview Questions
Behavioral Interview Questions
Can you describe a time when you worked as part of a team to complete a silo operation?
How to Answer
- 1
Think of a specific project or task related to silo operations.
- 2
Focus on your role in the team and how you contributed.
- 3
Highlight successful teamwork and communication.
- 4
Mention any challenges faced and how the team overcame them.
- 5
Emphasize the positive outcome and what you learned from the experience.
Example Answers
At my previous job, we had to empty and clean a grain silo. I was responsible for coordinating with the team to ensure a safe operation. We communicated effectively, and I set up check-ins to monitor progress. We faced an issue with equipment malfunction, but we quickly adapted and worked together to fix it. In the end, we completed the task two days ahead of schedule, and I learned the importance of flexibility and teamwork.
Tell me about a situation where you identified a safety hazard in the silo operations and how you handled it.
How to Answer
- 1
Start with a brief overview of the situation.
- 2
Clearly describe the safety hazard you identified.
- 3
Explain the steps you took to address the hazard.
- 4
Mention any communication with team members or management.
- 5
End with the outcome and any lessons learned.
Example Answers
During a routine inspection, I noticed that the safety alarm was malfunctioning in the grain silo. I immediately reported it to my supervisor and marked the area as unsafe. We conducted a team meeting to ensure everyone was aware of the hazard, and I stayed on-site until the alarm was repaired. This prevented potential accidents and reinforced the importance of regular maintenance checks.
Don't Just Read Silo Worker Questions - Practice Answering Them!
Reading helps, but actual practice is what gets you hired. Our AI feedback system helps you improve your Silo Worker interview answers in real-time.
Personalized feedback
Unlimited practice
Used by hundreds of successful candidates
Describe a challenging situation you faced while working in a silo and how you resolved it.
How to Answer
- 1
Focus on a specific challenge you encountered.
- 2
Explain the steps you took to address the challenge.
- 3
Mention any teamwork or communication efforts involved.
- 4
Highlight the results of your actions and what you learned.
- 5
Make sure to keep it concise and relevant to silo operations.
Example Answers
While operating the grain silo, we experienced an unexpected jam in the unloading system. I quickly assessed the situation and coordinated with my team to clear the blockage safely. We followed safety protocols and managed to resume operations within an hour, minimizing delay and learning the importance of teamwork during a crisis.
Can you give an example of how you communicated important operational updates to your team?
How to Answer
- 1
Choose a specific situation where communication was critical.
- 2
Describe the method of communication you used (e.g., meeting, email, bulletin board).
- 3
Explain the content of the update and why it was important for the team.
- 4
Mention how you ensured everyone understood the information.
- 5
Highlight any feedback or follow-up actions taken by the team.
Example Answers
In a recent project, I scheduled a team meeting to share updates on safety protocol changes. I presented the details clearly, and encouraged questions to ensure everyone understood. After the meeting, I sent a recap email summarizing the key points to reinforce the message.
Have you ever taken the lead in a silo operation? What challenges did you face?
How to Answer
- 1
Briefly describe your leadership experience in silo operations.
- 2
Identify specific challenges you encountered and how you addressed them.
- 3
Highlight how your leadership improved efficiency or safety.
- 4
Share lessons learned from the experience.
- 5
Conclude with how you would apply this experience in future roles.
Example Answers
Yes, I led a small team during a grain loading operation. One challenge was coordinating the workflow to ensure safety and efficiency. We implemented a new schedule and enhanced communication, which resulted in a 15% increase in loading speed.
Can you talk about a time you had to manage tight deadlines in silo operations?
How to Answer
- 1
Identify a specific project with a tight deadline.
- 2
Explain what actions you took to meet the deadline.
- 3
Highlight teamwork or communication strategies you used.
- 4
Mention any tools or methods that helped you stay organized.
- 5
Emphasize the outcome and what you learned from the experience.
Example Answers
In my previous role, we had a situation where a delivery was delayed, and we had to consolidate multiple silo loads within a week. I organized daily briefings with the team to track progress and prioritize tasks. We used a shift roster to maximize our manpower and completed the project two days early, which improved our client relationship.
Describe a conflict you had with a coworker over silo operations. How did you resolve it?
How to Answer
- 1
Identify the conflict clearly and specifically regarding silo operations.
- 2
Explain your role and perspective in the situation calmly.
- 3
Discuss how you approached the conversation with your coworker.
- 4
Highlight the steps taken to reach a resolution.
- 5
Emphasize the outcome and what you learned from the experience.
Example Answers
In a previous job, I disagreed with a coworker about the proper method for loading grain into the silo. I believed we needed to change our process to improve efficiency. I approached my coworker and we had a constructive discussion where we shared our viewpoints. We decided to test each method on a small scale and then review the results. Ultimately, we adopted the more efficient method and improved our operations.
Technical Interview Questions
What types of silo equipment have you operated, and can you discuss their maintenance requirements?
How to Answer
- 1
Identify specific types of silo equipment you have experience with.
- 2
Discuss key maintenance tasks for each type of equipment.
- 3
Mention any safety protocols you followed during operation and maintenance.
- 4
Explain how you handled any maintenance issues that arose during your experience.
- 5
Highlight any training or certifications related to silo operations or equipment maintenance.
Example Answers
I have operated grain silos and used equipment such as augers and conveyor belts. Regular maintenance included checking for wear and tear, lubricating moving parts, and ensuring the equipment was free of grain build-up. I always followed safety protocols, particularly when working at heights.
What is the process you follow for loading and unloading materials in a silo?
How to Answer
- 1
Explain the safety procedures you prioritize before starting the process
- 2
Describe the equipment you use for loading and unloading
- 3
Mention the steps for monitoring material levels during the process
- 4
Highlight the importance of maintaining clear communication with team members
- 5
Conclude with how you handle any potential issues that arise
Example Answers
I start by ensuring all safety gear is on and the area is clear. I use a conveyor system for loading and unloading the materials. Throughout the process, I monitor the silo levels using sensors to prevent overloading. I always communicate with my team to ensure everything is coordinated. If any issues arise, I quickly assess the situation and take appropriate action.
Don't Just Read Silo Worker Questions - Practice Answering Them!
Reading helps, but actual practice is what gets you hired. Our AI feedback system helps you improve your Silo Worker interview answers in real-time.
Personalized feedback
Unlimited practice
Used by hundreds of successful candidates
What safety protocols do you follow when working with hazardous materials in a silo?
How to Answer
- 1
Identify specific safety equipment you use, such as respirators or gloves
- 2
Mention following Material Safety Data Sheets (MSDS) for hazardous materials
- 3
Discuss regular training and drills for emergency responses
- 4
Explain the importance of ventilation and monitoring air quality
- 5
Highlight your adherence to company safety policies and regulatory standards
Example Answers
I always wear necessary personal protective equipment like respirators and gloves, and I ensure I follow the MSDS for any hazardous materials. I also participate in regular safety drills to prepare for emergencies.
How do you monitor the conditions inside a silo to ensure the safety and quality of the stored materials?
How to Answer
- 1
Use temperature and humidity sensors to track environmental conditions.
- 2
Conduct regular visual inspections for signs of spoilage or pests.
- 3
Implement a monitoring system that alerts you to any critical changes.
- 4
Document all findings regularly to maintain a clear record.
- 5
Ensure proper airflow within the silo to prevent mold and spoilage.
Example Answers
I monitor silo conditions by using temperature and humidity sensors to ensure optimal levels. I also conduct visual inspections to check for spoilage and keep a detailed log of all readings.
Can you explain how you troubleshoot a malfunctioning silo system?
How to Answer
- 1
Start with a clear understanding of the silo system and its components.
- 2
Identify and isolate the problem by checking for common issues.
- 3
Use diagnostic tools to gather data on the system's performance.
- 4
Develop a systematic approach to resolving the issue, testing each step.
- 5
Document the process and results to inform future troubleshooting.
Example Answers
I first review the silo system's layout and components. Then I identify hotspots for common issues, like clogs or sensor failures. I use diagnostic tools to monitor performance, make necessary adjustments, and run tests to ensure the system is working properly again.
What records do you maintain during silo operations, and why are they important?
How to Answer
- 1
Talk about inventory records to track what is stored in silos.
- 2
Mention maintenance logs to ensure equipment is in good working condition.
- 3
Include safety records to monitor compliance with safety regulations.
- 4
Discuss quantity and quality reports for the materials being stored.
- 5
Emphasize that these records help in optimizing operations and preventing issues.
Example Answers
During silo operations, I maintain inventory records to manage the amount and type of materials stored. This is crucial for optimizing storage and ensuring we have enough stock for production.
What regulations must be followed in silo management, and how do you comply with them?
How to Answer
- 1
Identify key regulations governing silo management like OSHA, NFPA, and local safety codes.
- 2
Discuss specific compliance procedures such as regular inspections and safety training.
- 3
Mention the importance of maintaining accurate records for inspections and safety drills.
- 4
Explain how you ensure team awareness of safety protocols through meetings and signage.
- 5
Provide examples of how you have implemented these regulations in prior roles.
Example Answers
In silo management, we follow OSHA regulations and NFPA standards. I conduct regular safety inspections and ensure that all team members receive safety training. We maintain detailed records of inspections and training sessions to ensure compliance.
What key elements do you inspect during a routine check of silo equipment?
How to Answer
- 1
Focus on structural integrity of the silo.
- 2
Check for any signs of leakage or corrosion.
- 3
Ensure the safety equipment is functional.
- 4
Inspect the loading and unloading mechanisms.
- 5
Verify that monitoring systems are operational.
Example Answers
During a routine check, I inspect the silo for structural integrity, look for any signs of leakage or corrosion, ensure the safety equipment like alarms are functional, check the loading and unloading mechanisms, and verify that monitoring systems are properly operational.
Situational Interview Questions
If there was an emergency situation such as a fire in a silo, how would you respond?
How to Answer
- 1
Stay calm and assess the situation quickly
- 2
Activate the emergency alarm to alert others
- 3
Follow the established evacuation procedures
- 4
Use fire extinguishers only if it is safe to do so
- 5
Call emergency services once safe from immediate danger
Example Answers
In the event of a fire, I would first remain calm and quickly assess how serious the situation is. I would then activate the emergency alarm to alert my coworkers, and follow the established evacuation procedures to ensure everyone gets out safely. If it's small and safe, I might use a fire extinguisher, but my priority would be to call emergency services afterward.
Imagine you find a blockage in the silo during operation. What steps would you take to resolve it?
How to Answer
- 1
Immediately stop the operation to ensure safety.
- 2
Notify the supervisor and relevant team members about the blockage.
- 3
Assess the blockage type and its location if safe to do so.
- 4
Follow the company's procedure for resolving blockages.
- 5
Document the incident and actions taken for future reference.
Example Answers
First, I would stop the operation to prioritize safety, then notify my supervisor. I would assess the blockage from a safe distance and follow the standard operating procedure to resolve it.
Don't Just Read Silo Worker Questions - Practice Answering Them!
Reading helps, but actual practice is what gets you hired. Our AI feedback system helps you improve your Silo Worker interview answers in real-time.
Personalized feedback
Unlimited practice
Used by hundreds of successful candidates
How would you handle a sudden downtime of silo operations due to equipment failure?
How to Answer
- 1
Stay calm and assess the situation quickly
- 2
Communicate with the team and inform them of the issue
- 3
Follow the emergency procedures outlined for equipment failure
- 4
Contact maintenance or technical support for troubleshooting
- 5
Document the incident and steps taken for future reference
Example Answers
I would assess the cause of the downtime, communicate with my team to keep everyone informed, and follow our standard emergency procedures. Then I would reach out to maintenance while making notes on the issue.
If you were assigned to work with a new team on silo operations, how would you ensure effective collaboration?
How to Answer
- 1
Establish open communication from day one
- 2
Identify individual strengths and roles
- 3
Set common goals for the team
- 4
Encourage feedback and active participation
- 5
Be proactive in resolving conflicts
Example Answers
I would start by introducing myself and encouraging the team to share their experiences and strengths. This helps us understand each other better and fosters open communication.
If you had to choose between following a procedure or addressing an urgent concern, what would you do?
How to Answer
- 1
Evaluate the urgency of the concern and its potential impact
- 2
Consider if the procedure can be adapted to address the concern
- 3
Communicate with a supervisor if necessary for guidance
- 4
Prioritize safety and compliance in your decision
- 5
Document your decision-making process for future reference
Example Answers
I would assess the urgency of the concern first. If it's something that could cause harm or further issues, I would address that concern right away but inform my supervisor and ensure that we follow up with procedure adjustments later.
What would you do if you noticed that the quality of materials being stored was not up to standard?
How to Answer
- 1
Assess the situation to understand the extent of the quality issue.
- 2
Notify your supervisor immediately about the quality concern.
- 3
Isolate the substandard materials to prevent their use.
- 4
Document your findings clearly for future reference.
- 5
Propose solutions or improvements to prevent future occurrences.
Example Answers
I would first assess the materials to understand the quality issue. Then, I would notify my supervisor right away and recommend isolating those materials. I would also document everything I found for clarity.
If a colleague is not following safety protocols while working in the silo, how would you address it?
How to Answer
- 1
Assess the situation calmly and determine if immediate action is needed
- 2
Approach your colleague privately to discuss the issue
- 3
Express your concern for their safety and the importance of protocols
- 4
Listen to their perspective and share the risks of not following procedures
- 5
If necessary, report the behavior to a supervisor after addressing it directly
Example Answers
I would first observe if immediate intervention is needed. Then, I would privately talk to my colleague, expressing my concern for their safety and explaining the risks of not following the safety protocols. If they don’t correct their behavior, I would feel obligated to report it to a supervisor.
How would you handle silo operations during extreme weather conditions?
How to Answer
- 1
Prepare and review the emergency plan for extreme weather.
- 2
Monitor weather forecasts to anticipate conditions affecting operations.
- 3
Ensure all safety equipment is in good condition and accessible.
- 4
Communicate with the team about procedures and safety measures.
- 5
Consider temporary shutdown of operations if safety is compromised.
Example Answers
I would regularly check weather forecasts and have an emergency plan ready. If extreme weather is expected, I would communicate with the team about implementing safety precautions and possibly pausing operations until conditions improve.
What steps would you take if you needed to report a safety concern to management?
How to Answer
- 1
Identify the specific safety issue clearly.
- 2
Document the concern with details such as date, time, and location.
- 3
Follow company protocol for reporting safety issues.
- 4
Communicate the concern to your immediate supervisor first.
- 5
Ensure that the report is submitted in a timely manner.
Example Answers
First, I would identify the specific safety concern and document its details, including when and where it happened. Then, I would report this issue to my supervisor following our company’s safety reporting process.
If you identified a process in silo operations that could be improved, how would you present it to your supervisor?
How to Answer
- 1
Observe the current process and take detailed notes.
- 2
Identify specific areas of improvement and their potential benefits.
- 3
Prepare a clear and concise presentation or report.
- 4
Use data or examples to support your suggestions.
- 5
Be open to feedback and discussion during your presentation.
Example Answers
I would first document the current process, then highlight areas where efficiency could be increased. Next, I would prepare a brief report outlining my suggestions along with relevant data, and finally, I would present this to my supervisor while being open to their insights.
Don't Just Read Silo Worker Questions - Practice Answering Them!
Reading helps, but actual practice is what gets you hired. Our AI feedback system helps you improve your Silo Worker interview answers in real-time.
Personalized feedback
Unlimited practice
Used by hundreds of successful candidates
How would you manage inventory discrepancies when checking the amount of material in the silo?
How to Answer
- 1
Verify measurement tools are calibrated and functioning properly
- 2
Cross-check silo measurements with inventory records
- 3
Investigate the cause of discrepancies through root cause analysis
- 4
Communicate findings with the relevant teams promptly
- 5
Establish a corrective action plan to prevent future discrepancies
Example Answers
I would first ensure that all measurement tools are calibrated before taking measurements. Then, I'd verify these measurements against our inventory records. If discrepancies exist, I would analyze the cause, share my findings with the team, and implement processes to mitigate future issues.
If the production demand increased unexpectedly, how would you adjust silo operations to meet the needs?
How to Answer
- 1
Assess current inventory levels and silo capacity quickly
- 2
Coordinate with production and supply chain teams for real-time updates
- 3
Prioritize loading and unloading schedules based on urgency
- 4
Implement temporary work shifts if necessary to increase output
- 5
Monitor operations closely for any issues during adjustments
Example Answers
I would first check our current inventory and see how much we can supply. Then, I would communicate with the production team to understand their requirements and adjust schedules to prioritize the most urgent needs.
How would you coordinate with other departments that rely on the silo for materials?
How to Answer
- 1
Establish clear communication channels with other departments.
- 2
Schedule regular meetings to discuss material needs and inventory levels.
- 3
Use a shared tracking system to monitor silo inventory and usage.
- 4
Be proactive in addressing any potential supply issues early.
- 5
Encourage feedback from other departments to improve processes.
Example Answers
I would set up weekly meetings with key departments to discuss their material needs and review our inventory levels in the silo. This ensures everyone is aligned on usage and prevents shortages.
If you were asked to perform an operation outside standard protocols, what would you do?
How to Answer
- 1
Assess the situation carefully before acting
- 2
Consider safety implications for yourself and others
- 3
Consult with a supervisor or experienced colleague if possible
- 4
Document any deviation from protocol for transparency
- 5
Ensure that your actions are still in compliance with safety regulations
Example Answers
I would first assess the situation to understand why the deviation is necessary, ensuring that it doesn't pose any safety risks. Then, I would consult my supervisor to verify that we should proceed outside of standard protocols, while documenting everything for future reference.
Silo Worker Position Details
Related Positions
- Silo Operator
- Yarn Worker
- Shovel Operator
- Palletizer
- Coal Handler
- Storer
- Ship Loader
- Machine Stacker
- Crane Helper
- Moveman
Similar positions you might be interested in.
Ace Your Next Interview!
Practice with AI feedback & get hired faster
Personalized feedback
Used by hundreds of successful candidates
Ace Your Next Interview!
Practice with AI feedback & get hired faster
Personalized feedback
Used by hundreds of successful candidates