Top 30 Pole Maker Interview Questions and Answers [Updated 2025]
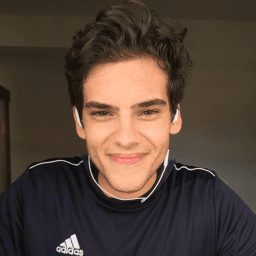
Andre Mendes
•
March 30, 2025
Preparing for a 'Pole Maker' interview can be daunting, but our updated 2025 guide is here to help. In this post, we delve into the most common interview questions for this specialized role, providing you with sample answers and insightful tips to respond confidently and effectively. Whether you’re a seasoned professional or a newcomer, equip yourself with the knowledge to stand out in your interview.
Download Pole Maker Interview Questions in PDF
To make your preparation even more convenient, we've compiled all these top Pole Makerinterview questions and answers into a handy PDF.
Click the button below to download the PDF and have easy access to these essential questions anytime, anywhere:
List of Pole Maker Interview Questions
Situational Interview Questions
What would you do if there was a disruption in the supply of core materials for pole making?
How to Answer
- 1
Assess the impact of the disruption on production timelines.
- 2
Identify alternative suppliers or materials that can be used.
- 3
Communicate with your team about the situation and solutions.
- 4
Explore potential adjustments in production processes.
- 5
Develop a contingency plan to minimize future disruptions.
Example Answers
If there was a disruption, I would first evaluate how it affects our current projects and timelines. Then, I would reach out to alternative suppliers to see if they can provide the materials. It's important to keep the team informed and work together to find a solution.
Imagine you find a defect in a batch of poles. How would you handle this situation?
How to Answer
- 1
Assess the nature and extent of the defect immediately
- 2
Isolate the defective poles to prevent usage
- 3
Document the defect with images and notes
- 4
Notify supervisors and relevant teams promptly
- 5
Suggest corrective actions to prevent future defects
Example Answers
I would first inspect the defect closely and identify how many poles are affected. Then, I would set them aside and document my findings with pictures and descriptions to keep a record. After that, I'd inform my supervisor so we can discuss next steps for either repairing or replacing them.
Don't Just Read Pole Maker Questions - Practice Answering Them!
Reading helps, but actual practice is what gets you hired. Our AI feedback system helps you improve your Pole Maker interview answers in real-time.
Personalized feedback
Unlimited practice
Used by hundreds of successful candidates
You are asked to maintain quality during a large production run. How would you ensure all poles meet quality standards?
How to Answer
- 1
Implement a checklist for quality checks at each stage of production
- 2
Train staff on quality standards and inspection criteria
- 3
Establish a random sampling method for quality assurance
- 4
Use sensors and measurement tools to monitor specifications in real-time
- 5
Document any defects and continuously improve processes based on feedback
Example Answers
I would create a comprehensive checklist that outlines quality checks at each production stage, ensuring every pole is inspected for size, strength, and finish.
A client requests an urgent order, but your team is already at capacity. How would you prioritize tasks and manage this request?
How to Answer
- 1
Evaluate the urgency of the client's request and its impact on business.
- 2
Communicate transparently with the team about current capacity and needs.
- 3
Consider if any lower priority tasks can be delayed or reassigned.
- 4
Seek client understanding and negotiate a feasible timeline.
- 5
Document the decision-making process for future reference.
Example Answers
I would first assess the urgency of the client's order compared to our current tasks. Then, I'd discuss with the team to see if any lower priority tasks can be pushed back. I would then communicate with the client to negotiate a new timeline based on our capacity.
If you were asked to improve the efficiency of the pole making process, what changes would you consider?
How to Answer
- 1
Analyze the current workflow to identify bottlenecks
- 2
Research automation options for repetitive tasks
- 3
Implement quality control measures early in the process
- 4
Explore the use of new materials that enhance durability and reduce cost
- 5
Gather feedback from current workers on daily challenges and suggestions
Example Answers
To improve efficiency, I would start by mapping out the current making process to identify where delays occur. Then, I would consider introducing automation for tasks like cutting and shaping that are repetitive, allowing workers to focus on quality.
What steps would you take if a critical piece of manufacturing equipment failed during production?
How to Answer
- 1
Assess the situation quickly to understand the impact on production.
- 2
Notify the supervisor and relevant team members about the failure.
- 3
Initiate a troubleshooting process based on your knowledge and resources.
- 4
Implement a temporary workaround if possible to minimize downtime.
- 5
Document the issue and the steps taken for future reference and analysis.
Example Answers
First, I would quickly assess which equipment has failed and how it affects our production line. Then, I would notify my supervisor and the maintenance team. I'd use my troubleshooting skills to identify possible solutions and, if feasible, apply a temporary workaround to keep production flowing. Finally, I'd document everything for our records and to help prevent future issues.
A client is dissatisfied with an order of poles due to a perceived defect. How would you handle the situation?
How to Answer
- 1
Listen to the client carefully to understand their concerns
- 2
Acknowledge their dissatisfaction and express empathy
- 3
Ask clarifying questions to gather specific details about the defect
- 4
Propose a solution, such as a replacement or refund
- 5
Follow up with the client after the resolution to ensure their satisfaction
Example Answers
I would start by listening to the client’s concerns without interruption. I’d acknowledge their feelings and ask specific questions about what they perceive as a defect. Based on their feedback, I might offer a replacement or refund, and then follow up to ensure they are satisfied with the outcome.
Imagine a safety incident occurs in your facility. What immediate actions would you take?
How to Answer
- 1
Assess the situation and ensure your safety first
- 2
Notify emergency services if needed
- 3
Secure the area to prevent further incidents
- 4
Provide first aid to those injured, if qualified
- 5
Document the incident and report it to your supervisor
Example Answers
First, I would ensure that I am safe and then assess the situation. If there are severe injuries, I would call emergency services immediately. Then, I would secure the area and ensure no one else is in danger before providing first aid to anyone who is injured.
Your manager asks you to reduce production costs. What areas would you examine for potential savings?
How to Answer
- 1
Analyze material costs and consider alternative suppliers.
- 2
Evaluate labor efficiency and identify any training needs.
- 3
Examine machinery and equipment for potential maintenance that reduces downtime.
- 4
Review inventory management to minimize waste and excess.
- 5
Explore energy consumption and identify areas to implement energy-saving measures.
Example Answers
To reduce production costs, I would start by examining our material costs. I would look for alternative suppliers who could offer lower prices without compromising quality. Additionally, I'd assess our labor efficiency and provide training where needed to enhance productivity.
How would you prepare for an emergency that could impact operations, such as a natural disaster affecting the supply chain?
How to Answer
- 1
Identify potential risks specific to the supply chain and operations.
- 2
Develop a communication plan for stakeholders during an emergency.
- 3
Establish relationships with alternative suppliers before an emergency occurs.
- 4
Create a contingency plan detailing steps to take if a disaster strikes.
- 5
Regularly review and update the emergency preparedness plan.
Example Answers
I would first identify the main risks to our supply chain, focusing on key suppliers and logistics. Then, I'd establish a solid communication plan for updates during an emergency. Building relationships with alternative suppliers would be crucial to maintain operations. I'd also create a detailed contingency plan to ensure we're ready to respond effectively and review this plan regularly.
Don't Just Read Pole Maker Questions - Practice Answering Them!
Reading helps, but actual practice is what gets you hired. Our AI feedback system helps you improve your Pole Maker interview answers in real-time.
Personalized feedback
Unlimited practice
Used by hundreds of successful candidates
Behavioral Interview Questions
Can you give an example of a time when paying close attention to small details in your work made a big difference?
How to Answer
- 1
Choose a relevant example from your experience as a Pole Maker.
- 2
Highlight a specific detail that you noticed and acted upon.
- 3
Explain the positive impact of your attention to detail on the outcome.
- 4
Keep the story concise and focused on the details involved.
- 5
Conclude with what you learned and how it applies to the job.
Example Answers
In my last job, I noticed that the wood grain on the poles I was crafting was different than usual. I adjusted my sanding technique to ensure the finish looked uniform. This small change improved the final product's appeal, leading to positive feedback from customers.
Describe a time when you worked as part of a team to complete a challenging task. What was your role, and what was the outcome?
How to Answer
- 1
Think of a specific project where teamwork was essential.
- 2
Clearly state your role in the team and your contributions.
- 3
Focus on the challenges faced and how the team addressed them.
- 4
Highlight the positive outcome and what you learned.
- 5
Relate the experience to skills relevant to the Pole Maker position.
Example Answers
In my previous job, we had a project to upgrade the production line for pole making. I was the team leader and coordinated efforts between engineers and manufacturing staff. We faced delays due to supply chain issues, but through effective communication and problem-solving, we managed to complete the upgrade on time, which improved efficiency by 20%.
Don't Just Read Pole Maker Questions - Practice Answering Them!
Reading helps, but actual practice is what gets you hired. Our AI feedback system helps you improve your Pole Maker interview answers in real-time.
Personalized feedback
Unlimited practice
Used by hundreds of successful candidates
Tell me about a time when you had to communicate complex information to someone else. How did you ensure they understood?
How to Answer
- 1
Choose a specific example that highlights your communication skills.
- 2
Describe the complexity of the information clearly.
- 3
Explain your method of breaking down the information.
- 4
Mention how you checked for understanding.
- 5
Share the outcome to show effectiveness.
Example Answers
In a previous role as a technician, I had to explain the details of a new pole design to a non-technical sales team. I used simple analogies related to everyday items and visual aids to illustrate key points. After explaining, I asked them to summarize what they understood, which helped ensure clarity. The team was then able to confidently present the new design to clients.
Describe a situation where you had a conflict with a colleague. How did you resolve it?
How to Answer
- 1
Identify a specific conflict situation that showcases your conflict resolution skills.
- 2
Use the STAR method: Situation, Task, Action, Result to structure your answer.
- 3
Emphasize communication and understanding in your resolution approach.
- 4
Highlight the positive outcome and any lessons learned from the experience.
- 5
Make sure the example aligns with teamwork and collaboration values.
Example Answers
In my previous job, I had a disagreement with a colleague over the design of a new product. We both had strong opinions, but instead of arguing, I suggested we sit down to discuss our perspectives. By actively listening to her ideas and sharing my concerns, we found common ground and ended up merging our designs. The product was well-received, and we learned to collaborate better.
Give an example of a time when you had to adapt to a significant change at work. What was the situation, and how did you handle it?
How to Answer
- 1
Identify a specific change that impacted your role
- 2
Describe the context of the change briefly
- 3
Explain your thought process in reacting to it
- 4
Detail the steps you took to adapt effectively
- 5
Share the outcome and any lessons learned
Example Answers
In my previous job, our company underwent a merger that resulted in new software systems. I quickly learned the new system by attending training sessions and set up a help group with colleagues. As a result, my team adapted well and we maintained our productivity during the transition.
Can you describe a time when you took initiative on a project? What was the result?
How to Answer
- 1
Choose a specific project where your initiative made a difference.
- 2
Clearly describe the challenge you faced before taking action.
- 3
Explain the steps you took to take initiative.
- 4
Highlight the positive outcome that resulted from your actions.
- 5
Emphasize any lessons learned or skills gained from the experience.
Example Answers
In my previous job at a woodworking shop, we often had delays in pole production due to inefficient scheduling. I took the initiative to analyze our workflow and proposed a new scheduling plan that balanced workload across our team. As a result, we improved our production speed by 20%, and I also gained leadership experience.
Tell me about a time when you improved a process at work. What steps did you take to implement this improvement?
How to Answer
- 1
Identify a specific process you improved.
- 2
Explain the problem with the original process.
- 3
Detail the steps you took to improve it.
- 4
Mention the results of the improvement.
- 5
Be concise and focus on your specific role.
Example Answers
At my previous job, I noticed that the pole manufacturing line was consistently slow. I analyzed the workflow and identified that material handling was causing delays. I proposed a new layout for the raw material storage, which reduced travel time. After implementing this, we increased our production speed by 20%.
How do you manage multiple deadlines to ensure timely completion of projects?
How to Answer
- 1
Prioritize tasks based on urgency and importance
- 2
Use a project management tool to track progress
- 3
Set personal deadlines ahead of actual deadlines
- 4
Break projects into smaller, manageable tasks
- 5
Communicate proactively with stakeholders about any issues
Example Answers
I prioritize tasks by identifying the most urgent deadlines first, then use a project management tool to keep track of each project’s progress. This helps me stay organized and ensure nothing slips through the cracks.
Can you describe a situation where you led a project or team? What strategies did you use to guide the team?
How to Answer
- 1
Choose a relevant project that showcases your leadership.
- 2
Explain the goal of the project and your role clearly.
- 3
Describe specific strategies you employed, such as communication or task delegation.
- 4
Highlight the outcomes of the project and what you learned.
- 5
Keep your answer structured: situation, actions, and results.
Example Answers
In my last role, I led a project to develop a new line of poles. I set clear objectives for the team, held weekly check-ins to ensure alignment, and encouraged open communication. As a result, we completed the project ahead of schedule, which increased sales by 15%.
Describe an instance in which you failed to meet a job expectation. What did you learn from this experience?
How to Answer
- 1
Choose a relevant situation where you didn't meet an expectation.
- 2
Explain the context briefly and your specific role in the failure.
- 3
Focus on what you learned and how you applied that knowledge later.
- 4
Highlight any steps you took to rectify the situation afterward.
- 5
Keep the tone constructive, showing growth from the experience.
Example Answers
In my previous role as a carpenter, I once underestimated the time needed to complete a project, resulting in a deadline not being met. I learned to always factor in buffer time for unexpected issues. After that, I started using a project management tool to track timelines better, which improved my on-time delivery rate.
Don't Just Read Pole Maker Questions - Practice Answering Them!
Reading helps, but actual practice is what gets you hired. Our AI feedback system helps you improve your Pole Maker interview answers in real-time.
Personalized feedback
Unlimited practice
Used by hundreds of successful candidates
Technical Interview Questions
What types of materials are typically used to make poles and why?
How to Answer
- 1
Identify common materials like wood, metal, fiberglass, and plastics.
- 2
Explain the properties that make each material suitable for pole making.
- 3
Mention durability, weight, cost, and resistance to elements or corrosion.
- 4
Consider the specific use cases for different types of poles.
- 5
Be prepared to discuss environmental impact or sustainability of materials.
Example Answers
Poles are commonly made from wood, metal, fiberglass, and plastics. Wood is strong and used for traditional applications, while metal like aluminum offers durability and is lightweight. Fiberglass is great for poles that need to resist corrosion, and plastics can be economical for lightweight applications.
Explain the process of pole fabrication from raw material to finished product.
How to Answer
- 1
Start with identifying the raw materials used for poles, such as wood, steel, or composite materials.
- 2
Describe the treatment processes for the raw materials, including preservatives or coatings if applicable.
- 3
Outline the fabrication steps, like cutting, shaping, and assembling the materials into poles.
- 4
Mention the quality checks and testing procedures to ensure the poles meet industry standards.
- 5
Conclude with the finishing touches and packaging for delivery.
Example Answers
The process begins with sourcing raw materials like treated wood or steel. The wood is then treated with preservatives to prevent decay. Next, the materials are cut to size and assembled. After fabrication, we conduct quality checks on strength and durability. Finally, poles are finished and packaged for distribution.
Don't Just Read Pole Maker Questions - Practice Answering Them!
Reading helps, but actual practice is what gets you hired. Our AI feedback system helps you improve your Pole Maker interview answers in real-time.
Personalized feedback
Unlimited practice
Used by hundreds of successful candidates
What tools and equipment are essential for pole making, and how do you use them?
How to Answer
- 1
Identify the key tools like lathes, saws, and drills.
- 2
Explain the purpose of each tool in the pole making process.
- 3
Discuss safety equipment and its importance during the work.
- 4
Mention any specialized tools related to the specific type of poles you make.
- 5
Provide a brief overview of the order of operations when using these tools.
Example Answers
For pole making, essential tools include lathes for shaping the wood, saws for cutting to length, and drills for creating holes. Each tool has a specific role, with lathes providing the precision needed for a smooth finish.
What safety standards are relevant in pole manufacturing, and how do you adhere to them?
How to Answer
- 1
Research specific safety standards like OSHA regulations and industry guidelines.
- 2
Emphasize adherence to personal protective equipment (PPE) protocols, ensuring all workers wear necessary gear.
- 3
Discuss the importance of regular safety training and drills for all staff members.
- 4
Highlight the implementation of safety audits and inspections in the manufacturing process.
- 5
Mention documenting safety practices and incidents to identify areas for improvement.
Example Answers
In pole manufacturing, I prioritize adherence to OSHA standards, ensuring all workers wear PPE such as helmets and gloves. I also conduct regular safety training sessions and audits to keep everyone informed on best practices.
How do you ensure that you accurately follow technical specifications when manufacturing poles?
How to Answer
- 1
Review the technical specifications thoroughly before starting production
- 2
Use checklists to track each step of the manufacturing process
- 3
Double-check measurements and materials against the specifications
- 4
Collaborate with team members to confirm understanding of specs
- 5
Maintain a record of any deviations and communicate them to supervisors
Example Answers
I start by carefully reviewing the technical specifications to ensure I understand every detail. I create a checklist for the manufacturing process that I follow step by step. Before finalizing any measurements, I always double-check them against the specs to ensure accuracy.
How do you perform load bearing calculations to ensure a pole meets necessary standards?
How to Answer
- 1
Identify the load requirements for the specific application.
- 2
Use appropriate engineering standards and codes for calculations.
- 3
Calculate material strength and safety factors based on load.
- 4
Consider environmental factors such as wind and snow loads.
- 5
Verify calculations with peer reviews or software tools.
Example Answers
I begin by assessing the load requirements for the pole's intended use, such as weight support and environmental factors. I then apply relevant engineering standards, like the ASTM specifications, to determine the necessary strength. From there, I perform calculations considering safety factors to ensure reliability.
Discuss your experience with welding and how it applies to pole fabrication.
How to Answer
- 1
Highlight specific welding techniques you have used relevant to pole making.
- 2
Mention any certifications or training you have in welding.
- 3
Discuss how your welding experience improves the durability and quality of poles.
- 4
Provide examples of projects where you successfully used welding in fabrication.
- 5
Emphasize safety practices you follow while welding.
Example Answers
I have three years of experience in MIG welding, which I used in fabricating outdoor utility poles. This technique allows for strong joints that withstand weather conditions. I also completed a welding certification course which ensures my work meets industry standards.
What experience do you have with design software used in pole manufacturing?
How to Answer
- 1
Identify specific design software you have used in pole manufacturing.
- 2
Mention any relevant projects where you applied these software skills.
- 3
Highlight your proficiency level with each software tool.
- 4
Discuss how you used the software to solve design challenges or improve efficiency.
- 5
If applicable, reference any training or certifications related to the software.
Example Answers
I have extensive experience using AutoCAD for designing pole structural components. In my previous job, I led a project where I implemented a new design feature, which resulted in a 20% reduction in material costs.
Explain the role of CNC machining in pole manufacturing.
How to Answer
- 1
Highlight precision and efficiency of CNC machining.
- 2
Mention automation in production processes.
- 3
Explain how CNC reduces material waste.
- 4
Discuss versatility in creating complex designs.
- 5
Emphasize faster turnaround times for production.
Example Answers
CNC machining plays a crucial role in pole manufacturing by providing precision and efficiency in cutting and shaping materials. It automates the process, reducing labor costs, and minimizes waste due to its accuracy. With CNC, we can create complex designs quickly, allowing for faster production times.
What environmental regulations must be followed when manufacturing poles, and how do they affect production?
How to Answer
- 1
Identify key environmental regulations relevant to pole manufacturing like waste management and emissions standards.
- 2
Explain how these regulations influence production processes and materials used.
- 3
Discuss the importance of compliance and potential penalties for violations.
- 4
Mention any certifications that could be relevant, such as ISO 14001.
- 5
Highlight any sustainable practices the company might use in manufacturing.
Example Answers
In pole manufacturing, regulations like the Clean Water Act and the Resource Conservation and Recovery Act are critical. They require proper waste management and limit emissions, which can lead to changes in material sourcing and production techniques to stay compliant. Non-compliance can result in fines and legal actions, so companies often adopt sustainable practices and seek certifications like ISO 14001 to demonstrate their commitment.
Don't Just Read Pole Maker Questions - Practice Answering Them!
Reading helps, but actual practice is what gets you hired. Our AI feedback system helps you improve your Pole Maker interview answers in real-time.
Personalized feedback
Unlimited practice
Used by hundreds of successful candidates
Pole Maker Position Details
Related Positions
- Pole Cutter
- Pole River
- Poler
- Piece Maker
- Piling Cutter
- Cable Puller
- Groundman
- Bottom Loader
- Chain Puller
- Bolt Cutter
Similar positions you might be interested in.
Ace Your Next Interview!
Practice with AI feedback & get hired faster
Personalized feedback
Used by hundreds of successful candidates
Ace Your Next Interview!
Practice with AI feedback & get hired faster
Personalized feedback
Used by hundreds of successful candidates