Top 31 Press Operator Interview Questions and Answers [Updated 2025]
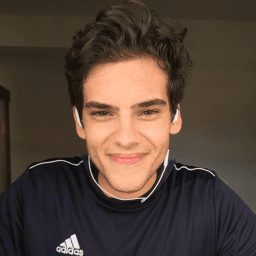
Andre Mendes
•
March 30, 2025
Preparing for a press operator interview can be daunting, but we've got you covered with the most common questions you'll encounter. In this updated post, you'll find insightful example answers and practical tips to help you respond effectively and confidently. Whether you're a seasoned professional or new to the field, this guide will equip you with the knowledge to ace your interview and make a lasting impression.
Get Press Operator Interview Questions PDF
Get instant access to all these Press Operator interview questions and expert answers in a convenient PDF format. Perfect for offline study and interview preparation.
Enter your email below to receive the PDF instantly: