Top 30 Presser Interview Questions and Answers [Updated 2025]
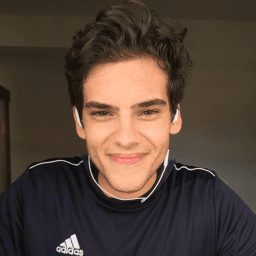
Andre Mendes
•
March 30, 2025
Navigating a presser interview can be daunting, but preparation is key to success. In this blog post, we delve into the most common interview questions for the presser role, providing example answers and insightful tips to help you respond confidently and effectively. Whether you're an experienced presser or new to the field, this guide is designed to equip you with the knowledge to make a lasting impression.
Download Presser Interview Questions in PDF
To make your preparation even more convenient, we've compiled all these top Presserinterview questions and answers into a handy PDF.
Click the button below to download the PDF and have easy access to these essential questions anytime, anywhere:
List of Presser Interview Questions
Behavioral Interview Questions
Describe an instance where your attention to detail prevented a potential issue in the pressing process.
How to Answer
- 1
Identify a specific instance where you caught an error before it became a problem.
- 2
Explain the details of the mistake you noticed and your thought process in addressing it.
- 3
Discuss the outcome and how it benefited the pressing process or the final product.
- 4
Use clear, concise language to communicate your example.
- 5
Be prepared to show how this instance reflects your overall work ethic and quality standards.
Example Answers
While working on a large order of dress shirts, I noticed that the fabric under one of the pressing machines was misaligned. I double-checked the machine settings and adjusted the fabric position, preventing uneven creases. This ensured all shirts were pressed correctly, meeting our quality standards.
Can you describe a time when you worked in a team to meet a pressing deadline? What was your role?
How to Answer
- 1
Choose a specific team project with a clear deadline.
- 2
Explain your role and responsibilities in the team.
- 3
Focus on how you communicated and collaborated with others.
- 4
Highlight any obstacles the team faced and how you overcame them.
- 5
Conclude with the outcome and what you learned from the experience.
Example Answers
In my last job, we had a critical marketing campaign due in one week. I was the project coordinator, making sure everyone was aligned and deadlines were clear. We faced delays in graphic design, so I stepped in to create some visuals myself while communicating closely with the designer. We delivered the campaign on time and it increased our engagement by 25%.
Don't Just Read Presser Questions - Practice Answering Them!
Reading helps, but actual practice is what gets you hired. Our AI feedback system helps you improve your Presser interview answers in real-time.
Personalized feedback
Unlimited practice
Used by hundreds of successful candidates
Tell me about a challenging situation you faced while pressing garments. How did you resolve it?
How to Answer
- 1
Describe a specific situation with clear details.
- 2
Focus on the challenge and its impact on the pressing process.
- 3
Explain the steps you took to resolve the issue.
- 4
Highlight any skills or techniques you used.
- 5
Mention the positive outcome and what you learned.
Example Answers
I once faced a situation where the fabric got scorched due to incorrect heat settings. I quickly adjusted the temperature and switched to a lower pressure. I also tested on a scrap piece to ensure it wouldn't happen again. The garments were saved, and I learned to always check the fabric type before pressing.
Have you ever had to adapt your pressing technique to accommodate a particularly delicate fabric? How did you handle it?
How to Answer
- 1
Identify the delicate fabric and its properties such as heat sensitivity.
- 2
Explain how you adjusted the temperature settings on the iron or press.
- 3
Discuss the use of pressing cloths or steam techniques.
- 4
Mention the importance of testing on a scrap piece first.
- 5
Share a specific example that highlights your attention to detail.
Example Answers
In my last position, I pressed chiffon, which is very delicate and can easily scorch. I lowered the iron's temperature setting and used a pressing cloth to protect the fabric.
Can you provide an example of how you managed your time effectively during a busy shift?
How to Answer
- 1
Think of a specific scenario where time management was crucial.
- 2
Highlight the tools or methods you used to prioritize tasks.
- 3
Mention how you handled unexpected challenges or distractions.
- 4
Emphasize the positive outcome of your time management strategy.
- 5
Keep your answer concise and focused on one main example.
Example Answers
During a busy Saturday shift, I used a checklist to prioritize my tasks. I tackled the most urgent orders first while keeping track of incoming requests. This helped me complete all orders on time and reduce customer wait times.
Tell me about a time you found a quality issue with a pressed item. What was your approach to correcting it?
How to Answer
- 1
Use a specific example from your experience.
- 2
Describe the quality issue clearly.
- 3
Explain how you identified the issue and its impact.
- 4
Outline the steps you took to correct it.
- 5
Conclude with the positive outcome of your actions.
Example Answers
In my last position, I noticed that a batch of pressed shirts had uneven seams. I flagged this issue during the quality check and traced it back to a miscalibrated machine. I recalibrated the machine myself and conducted further tests on the remaining batches. As a result, all shirts met our quality standards and we avoided significant returns.
Describe a time when you took the initiative to improve a pressing process or workflow.
How to Answer
- 1
Think of a specific situation where you saw room for improvement.
- 2
Describe the problem clearly and why it was important to address.
- 3
Explain the steps you took to improve the process.
- 4
Mention the positive outcomes of your actions and any metrics if applicable.
- 5
Conclude with what you learned from the experience.
Example Answers
In my previous job, I noticed our monthly report preparation took too long due to manual data entry. I proposed using a spreadsheet template that automatically pulled data from our database. After implementing this, report preparation time decreased by 40%, which allowed us to focus on data analysis instead of entry.
Situational Interview Questions
While pressing garments, a customer asks you for fabric care advice. How would you respond?
How to Answer
- 1
Identify the fabric type of the garment.
- 2
Offer specific care instructions based on the fabric.
- 3
Mention the correct temperature settings for pressing.
- 4
Include any special notes, like pre-washing or avoiding bleach.
- 5
Encourage them to read care labels for additional guidance.
Example Answers
For cotton, I recommend using a medium-high heat setting for pressing. Always check the care label first, and if it's heavily soiled, consider pre-washing to remove stains.
If a customer returns a pressed item due to unsatisfactory results, how would you handle the situation?
How to Answer
- 1
Acknowledge the customer's concerns with empathy.
- 2
Ask for specific feedback on what was unsatisfactory.
- 3
Offer a solution, such as a remake or refund.
- 4
Ensure the customer feels valued throughout the process.
- 5
Follow up to confirm their satisfaction after resolution.
Example Answers
I would first listen to the customer and acknowledge their disappointment. Then, I'd ask them to explain what specific issues they experienced. Based on their feedback, I would offer to remake the item or provide a refund. It's important they feel heard and valued.
Don't Just Read Presser Questions - Practice Answering Them!
Reading helps, but actual practice is what gets you hired. Our AI feedback system helps you improve your Presser interview answers in real-time.
Personalized feedback
Unlimited practice
Used by hundreds of successful candidates
Imagine you notice a batch of garments showing consistent pressing flaws. What steps would you take to address this?
How to Answer
- 1
Inspect the garments closely to identify the specific flaws.
- 2
Analyze the pressing process to pinpoint potential causes.
- 3
Communicate findings with the team and involve them in problem-solving.
- 4
Implement corrective measures and adjust the pressing technique.
- 5
Monitor subsequent batches for improvement and consistency.
Example Answers
I would start by inspecting the batch to identify the exact pressing flaws, such as creases or uneven seams. Then, I would review the pressing process to see if the temperature or pressure settings need adjustment. After that, I'd discuss the issue with my team to find the best solution together, implement the necessary changes, and closely monitor future batches for improvements.
If you are required to train a new team member on pressing techniques, what key points would you emphasize?
How to Answer
- 1
Explain the importance of fabric types in pressing techniques.
- 2
Demonstrate the correct use of the pressing iron and steam settings.
- 3
Emphasize the importance of proper press cloth use to avoid damage.
- 4
Show how to press various seams and hems for the best finish.
- 5
Discuss safety measures when using pressing equipment.
Example Answers
I would start by explaining how different fabrics react to heat and moisture, emphasizing the need to adjust the pressing technique accordingly. Then, I would demonstrate how to use the iron properly, including steam settings that suit specific fabrics. Using a press cloth is essential to prevent burns or shine, so I'd show how to use that effectively. I would also time for practicing pressing seams and hems, highlighting the best ways to achieve a professional finish. Finally, I'd stress the importance of safety, ensuring they know how to handle the iron without accidents.
You are running behind schedule due to equipment malfunction. How do you prioritize your tasks to minimize delays?
How to Answer
- 1
Assess the situation and identify the most critical tasks
- 2
Communicate with the team about the malfunction and reprioritize
- 3
Focus on tasks that can progress without the faulty equipment
- 4
Consider reallocating resources or personnel to alleviate delays
- 5
Implement contingency plans if available to keep production moving
Example Answers
First, I would evaluate which tasks are most urgent and necessary for the workflow. Then, I would inform my team about the equipment issue and adjust our priorities accordingly, focusing on tasks that can be done without that equipment. If possible, I would reassign team members to assist with different tasks to keep things moving while we solve the malfunction.
If you encounter an irate customer who claims their items were damaged during pressing, what would be your response?
How to Answer
- 1
Listen to the customer without interrupting
- 2
Apologize for their unpleasant experience
- 3
Ask for details about the damage
- 4
Offer a solution, like a refund or redo
- 5
Ensure follow-up to maintain customer satisfaction
Example Answers
I would first listen to the customer to fully understand their issue. Then, I would apologize for any inconvenience and ask them to describe the damage. Based on their response, I would offer to redo the item or provide a refund if that’s acceptable. Lastly, I would reassure them that we value their satisfaction and will address the issue.
You receive a garment without care instructions that appears delicate. How would you proceed to ensure it is pressed correctly?
How to Answer
- 1
Examine the fabric type and texture closely to determine its delicacy.
- 2
Start with a lower heat setting on the iron to avoid damage.
- 3
Test a small, inconspicuous area with steam to see how the fabric reacts.
- 4
Use a pressing cloth to protect the surface from direct heat.
- 5
Consult with colleagues or supervisors if unsure about the garment.
Example Answers
First, I would inspect the fabric carefully to identify its type. Then, I would set the iron on a low heat and test a small area with steam. If it seems safe, I would use a pressing cloth to avoid direct contact while pressing the garment.
How would you handle a situation where you see a coworker using pressing equipment unsafely?
How to Answer
- 1
Stay calm and assess the situation before acting.
- 2
Make sure you understand the unsafe behavior clearly.
- 3
Speak to the coworker privately about your concerns.
- 4
Suggest safer alternatives or discuss proper procedures.
- 5
If the behavior continues, report it to a supervisor for safety.
Example Answers
I would first observe the situation to confirm that the equipment is being used unsafely. Then I would approach my coworker privately and explain my concerns, suggesting that we follow the safety protocols together to ensure everyone's safety.
Suppose you need to improve the efficiency of your pressing operation during peak hours. What strategies would you implement?
How to Answer
- 1
Analyze the current workflow to identify bottlenecks.
- 2
Implement a schedule to prioritize the most critical pressing tasks.
- 3
Train staff on best practices to speed up the process.
- 4
Consider investing in technology for better automation.
- 5
Regularly review performance metrics to track improvements.
Example Answers
I would first analyze the current workflow to pinpoint where delays occur. By prioritizing critical tasks in the schedule, we can focus on what impacts throughput the most. Additionally, training staff on efficient pressing techniques can help them work faster.
A pressing machine breaks down during a busy time. What steps would you take to deal with the situation?
How to Answer
- 1
Immediately assess the situation to determine the nature of the breakdown.
- 2
Notify your supervisor and the maintenance team about the issue.
- 3
Minimize downtime by reallocating tasks or using backup equipment if available.
- 4
Keep communication open with your team to manage workflow and expectations.
- 5
Document the incident and any actions taken for future reference.
Example Answers
First, I would quickly identify the problem with the pressing machine. Then, I would alert my supervisor and the maintenance team to address the issue. If there are backup machines, I would switch operations to them, and inform the team about the changes to keep everyone on the same page.
Don't Just Read Presser Questions - Practice Answering Them!
Reading helps, but actual practice is what gets you hired. Our AI feedback system helps you improve your Presser interview answers in real-time.
Personalized feedback
Unlimited practice
Used by hundreds of successful candidates
You have a shipment of garments that should be pressed before delivery. How do you ensure they meet quality standards?
How to Answer
- 1
Inspect fabrics for defects before pressing
- 2
Use appropriate pressing temperatures for each fabric type
- 3
Implement a systematic pressing process to ensure consistency
- 4
Perform a final quality check after pressing to catch any issues
- 5
Document any issues to prevent future occurrences
Example Answers
I start by inspecting each garment for any fabric defects or stains before pressing. I then set my iron to the correct temperature for the specific fabric and follow a systematic pressing method to ensure each piece is finished uniformly. After pressing, I conduct a quality check to ensure everything meets our standards.
Technical Interview Questions
Explain the different types of pressing equipment you have used. How do you determine which is appropriate for a specific fabric?
How to Answer
- 1
Identify key types of pressing equipment like irons, steamers, and heat presses.
- 2
Discuss the features of each type and their specific uses.
- 3
Explain factors influencing fabric choice such as weight, content, and texture.
- 4
Mention safety considerations, like temperature control to avoid fabric damage.
- 5
Give examples of fabrics and the equipment best suited for them.
Example Answers
I have experience using steam irons for lightweight fabrics like silk and cotton blends, while I prefer heat presses for heavier materials like canvas. I assess the fabric's weight and texture to choose the right equipment, ensuring I use the correct temperature settings to prevent damage.
What techniques do you use for preventing shine on fabrics during pressing?
How to Answer
- 1
Use a pressing cloth to protect the fabric surface.
- 2
Adjust the iron temperature according to the fabric type.
- 3
Use steam instead of direct heat when possible.
- 4
Press from the reverse side of the fabric for delicate materials.
- 5
Keep the iron moving to avoid concentrating heat in one spot.
Example Answers
I always use a pressing cloth to create a barrier between the iron and the fabric, which helps prevent shine. I also make sure to adjust the heat setting appropriately for each fabric type.
Don't Just Read Presser Questions - Practice Answering Them!
Reading helps, but actual practice is what gets you hired. Our AI feedback system helps you improve your Presser interview answers in real-time.
Personalized feedback
Unlimited practice
Used by hundreds of successful candidates
How do you adjust the temperature settings on the pressing equipment based on different fabric types?
How to Answer
- 1
Identify the fabric type before pressing for optimal settings
- 2
Consult the manufacturer's guidelines for temperature recommendations
- 3
Adjust the temperature lower for delicate fabrics like silk and higher for sturdy fabrics like cotton
- 4
Test a small hidden area first to ensure no damage occurs
- 5
Regularly maintain and calibrate the pressing equipment for accuracy
Example Answers
I first determine the fabric type, then I refer to the manufacturer's guidelines for the proper temperature settings. For example, I would set the iron to a lower heat for silk and increase it for cotton.
What regular maintenance do you perform on pressing equipment to ensure optimal performance?
How to Answer
- 1
Discuss daily checks such as cleaning and inspecting for wear.
- 2
Mention weekly maintenance tasks like lubrication of moving parts.
- 3
Include monthly inspections for deeper checks of equipment conditions.
- 4
Emphasize the importance of keeping a maintenance log to track issues.
- 5
Highlight the need for following manufacturer guidelines for maintenance.
Example Answers
I perform daily checks to ensure the pressing equipment is clean and inspect for any wear or damage. Weekly, I lubricate moving parts to keep them functioning smoothly, and I conduct a more thorough inspection monthly to check the overall condition. I always document my findings in a maintenance log.
What signs do you look for to identify equipment malfunctions during pressing?
How to Answer
- 1
Listen for unusual noises such as grinding or squeaking
- 2
Check for inconsistent pressure in the press
- 3
Look for signs of leaking hydraulic fluid
- 4
Monitor the temperature of the equipment, excessive heat can indicate problems
- 5
Inspect the quality of the pressed material for defects or irregularities
Example Answers
I listen carefully for any unusual noises that might indicate wear or failure, such as grinding or squeaking. I also monitor the pressure gauge for inconsistencies that could suggest an issue.
What is your process for removing stubborn stains from garments before or after pressing?
How to Answer
- 1
Identify the type of stain for targeted treatment.
- 2
Use a stain remover appropriate for the fabric type.
- 3
Test the remover on a hidden area first to avoid damage.
- 4
For tough stains, allow the remover to sit for a few minutes.
- 5
After treatment, re-wash or rinse the garment before pressing.
Example Answers
I first identify the type of stain to ensure I choose the right treatment. I apply an appropriate stain remover, testing it on a hidden area first. For tough stains, I let it sit for a few minutes before rinsing and washing the garment again.
How do you determine the appropriate pressing technique for different types of fabric blends?
How to Answer
- 1
Identify the fiber content of the fabric blend.
- 2
Consult the care label for recommended pressing temperatures.
- 3
Test on a small, inconspicuous area first.
- 4
Adjust steam levels based on the fabric's durability.
- 5
Use a pressing cloth for delicate fabrics to prevent damage.
Example Answers
I first check the fabric blend to know the fibers involved. Then, I refer to the care label for the ideal temperature. I always test on a hidden area to ensure no adverse reactions.
What is the role of steam in the pressing process, and how do you control its use?
How to Answer
- 1
Explain how steam relaxes the fabric fibers.
- 2
Mention the importance of moisture in achieving crisp results.
- 3
Discuss controlling steam levels based on fabric type.
- 4
Highlight safety measures when using steam.
- 5
Emphasize the balance between steam and pressure.
Example Answers
Steam plays a crucial role in pressing by relaxing the fibers, which allows for better shaping and crispness. I control its use by adjusting the steam output according to the fabric type, ensuring that delicate materials receive minimal steam to prevent damage.
Can you explain the impact of pressure and heat on various fabric types during pressing?
How to Answer
- 1
Identify key fabric types like cotton, polyester, and wool.
- 2
Explain how heat influences the fibers (e.g., melting, shrinking).
- 3
Describe how pressure helps in setting seams and removing wrinkles.
- 4
Mention the importance of fabric care labels for safe pressing conditions.
- 5
Discuss the risks of excessive heat or pressure on delicate fabrics like silk.
Example Answers
Cotton reacts well with heat and pressure, as it sets seams and removes wrinkles efficiently. However, too much heat can scorch the fabric. Polyester is heat-sensitive and can melt, so lower temperatures are necessary. Wool benefits from steam to reshape garments but can shrink if overheated.
What types of chemical treatments do you apply to garments before pressing, if any?
How to Answer
- 1
Identify common pre-pressing treatments like starch or sizing.
- 2
Explain the purpose of each treatment in enhancing fabric appearance.
- 3
Mention how different fabrics require specific treatments.
- 4
Discuss any personal preferences or techniques you have.
- 5
Highlight the importance of following garment care labels.
Example Answers
I usually apply a light starch to cotton garments to give them a crisp finish. For delicate fabrics, I prefer a sizing spray that doesn't weigh them down, ensuring they retain their drape.
Don't Just Read Presser Questions - Practice Answering Them!
Reading helps, but actual practice is what gets you hired. Our AI feedback system helps you improve your Presser interview answers in real-time.
Personalized feedback
Unlimited practice
Used by hundreds of successful candidates
What common pressing errors have you encountered, and how do you rectify them?
How to Answer
- 1
Identify specific pressing errors you've faced, such as uneven pressure or misalignment.
- 2
Describe the steps you took to diagnose the problem objectively.
- 3
Explain how you implemented a solution and tested its effectiveness.
- 4
Mention any tools or techniques that helped in rectifying the errors.
- 5
Share any lessons learned to prevent future occurrences.
Example Answers
One common pressing error I encountered was misalignment of fabric layers. I noticed this during production, so I stopped the press, remeasured the alignment, and made adjustments to the guides. To prevent this, I now double-check alignment before each pressing session.
Presser Position Details
Salary Information
Recommended Job Boards
These job boards are ranked by relevance for this position.
Related Positions
- Car Pusher
- Machine Presser
- Buttoner
- Tongue Presser
- Machine Puller
- Toe Puncher
- Print Washer
- Puncher
- Flexographic Press Operator
- Charge Hand
Similar positions you might be interested in.
Ace Your Next Interview!
Practice with AI feedback & get hired faster
Personalized feedback
Used by hundreds of successful candidates
Ace Your Next Interview!
Practice with AI feedback & get hired faster
Personalized feedback
Used by hundreds of successful candidates