Top 30 Process Control Engineer Interview Questions and Answers [Updated 2025]
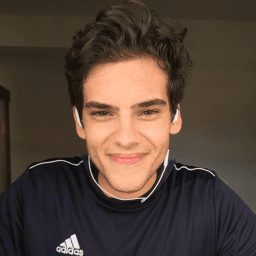
Andre Mendes
•
March 30, 2025
Preparing for a Process Control Engineer interview can be daunting, but we're here to help you succeed. In this post, you'll find a curated list of the most common interview questions for the role, complete with example answers and insightful tips on how to tackle them effectively. Whether you're a seasoned professional or a newcomer, this guide will equip you with the confidence and knowledge needed to excel in your interview.
Download Process Control Engineer Interview Questions in PDF
To make your preparation even more convenient, we've compiled all these top Process Control Engineerinterview questions and answers into a handy PDF.
Click the button below to download the PDF and have easy access to these essential questions anytime, anywhere:
List of Process Control Engineer Interview Questions
Behavioral Interview Questions
Can you describe a time when you worked on a team project to improve a process control system?
How to Answer
- 1
Choose a specific project with clear outcomes
- 2
Describe your role and contributions clearly
- 3
Highlight the process improvements achieved
- 4
Mention collaboration with team members
- 5
Use metrics or results to quantify improvements
Example Answers
In a recent project, our team focused on reducing variability in a chemical mixing process. I led the effort to implement a new control algorithm, which resulted in a 15% decrease in output variability. The collaboration with two other engineers and the operator was crucial for success.
Tell me about a challenge you faced in process control and how you solved it.
How to Answer
- 1
Identify a specific challenge you encountered in a process control project.
- 2
Explain the context and impact of the challenge on the process.
- 3
Describe the steps you took to analyze and solve the issue.
- 4
Share any tools or methodologies you used in your solution.
- 5
Conclude with the results and what you learned from the experience.
Example Answers
In my last role, we faced inconsistent output quality in a distillation unit. The variability was traced back to sensor calibration. I implemented a routine calibration schedule and used data analytics to monitor performance, which reduced variability by 30% and improved product quality.
Don't Just Read Process Control Engineer Questions - Practice Answering Them!
Reading helps, but actual practice is what gets you hired. Our AI feedback system helps you improve your Process Control Engineer interview answers in real-time.
Personalized feedback
Unlimited practice
Used by hundreds of successful candidates
Describe a situation where you had a disagreement with a colleague about a process control approach. How was it resolved?
How to Answer
- 1
Use the STAR method: Situation, Task, Action, Result.
- 2
Focus on the specific disagreement and the reasons for it.
- 3
Explain how you communicated with your colleague.
- 4
Describe the steps you took to resolve the disagreement.
- 5
Highlight the positive outcome or lessons learned.
Example Answers
In a recent project, my colleague and I disagreed on the tuning parameters for a PID controller. I explained my approach based on data analysis, while they preferred a conventional method. We discussed our viewpoints and decided to run a simulation comparing both methods. The results helped us find a compromise that improved system performance, leading to a successful implementation.
Have you ever led a team in upgrading or designing a new control system? What was your approach?
How to Answer
- 1
Start with a brief overview of the project and its objectives.
- 2
Describe your role in the team and the leadership style you used.
- 3
Highlight any key challenges faced and how you overcame them.
- 4
Emphasize the outcome of the project, including metrics or improvements.
- 5
Mention collaboration and communication strategies you implemented.
Example Answers
In my previous role, I led a team in upgrading the DCS for our chemical processing plant. We aimed to enhance safety and efficiency. I adopted a collaborative leadership style, facilitating regular meetings to gather input from all team members. We faced challenges in integrating legacy systems, but I coordinated workshops that led to innovative solutions. The upgrade resulted in a 20% increase in operational efficiency.
Can you describe a situation where you had to adjust to significant changes in a control system quickly?
How to Answer
- 1
Identify a specific situation where changes occurred.
- 2
Explain the nature of the changes in the control system.
- 3
Describe the steps you took to adapt and respond.
- 4
Highlight the outcome and what you learned.
- 5
Keep your answer structured and concise.
Example Answers
In my previous role, our control system was suddenly upgraded due to security concerns. I quickly familiarized myself with the new software by accessing training materials and reached out to colleagues. I ensured our equipment was re-calibrated in the new system and implemented changes within a week. This led to a smoother transition and enhanced system security.
Describe a time when you introduced a new idea or technology to improve process control.
How to Answer
- 1
Choose a specific example from your experience.
- 2
Explain the process or technology you introduced.
- 3
Highlight the challenges you faced and how you addressed them.
- 4
Share the results of your implementation, using metrics if possible.
- 5
Conclude with what you learned from the experience.
Example Answers
In my previous role, I implemented a new predictive maintenance technology using machine learning algorithms. We faced resistance from the team, but I organized training sessions to demonstrate its effectiveness. As a result, we reduced downtime by 20% and improved our response time to failures. I learned the importance of communication in change management.
Give an example of how you effectively communicated complex technical information to a non-technical audience.
How to Answer
- 1
Identify the audience and their level of understanding
- 2
Use analogies or simple language to explain technical terms
- 3
Focus on the key message rather than technical details
- 4
Encourage questions to ensure understanding
- 5
Provide visual aids or examples to illustrate concepts
Example Answers
During a project presentation, I explained a complex control algorithm to a group of managers. I used a simple analogy comparing the algorithm to a thermostat in a home, which they understood well. This helped them grasp the concept without getting lost in technical jargon.
Tell us about a process you improved that resulted in increased efficiency or cost savings.
How to Answer
- 1
Choose a specific process you worked on
- 2
Quantify the improvements with data if possible
- 3
Explain the steps you took to implement changes
- 4
Highlight teamwork or collaboration if applicable
- 5
Conclude with the positive impact on the company
Example Answers
In my previous role, I improved the batch mixing process by reducing the mixing time from 30 minutes to 20 minutes. By analyzing the mixing parameters and adjusting the speed, we achieved a 33% increase in efficiency, saving about $15,000 annually in labor costs.
Technical Interview Questions
How do you approach tuning a PID controller for a new process?
How to Answer
- 1
Understand the process dynamics through initial data collection and testing.
- 2
Start with the Ziegler-Nichols method for obtaining initial PID parameters.
- 3
Gradually test and adjust the PID parameters based on system response.
- 4
Use simulation tools to validate the controller performance before implementation.
- 5
Document the tuning process and results for future reference.
Example Answers
I begin by collecting data on the process dynamics, which helps me understand the behavior of the system. Then, I apply the Ziegler-Nichols method to get initial PID values. After that, I conduct tests and fine-tune the parameters based on the system's response until it's stable.
What are the key differences between DCS and PLC systems?
How to Answer
- 1
Define DCS and PLC systems clearly.
- 2
Highlight the main functions of each system.
- 3
Discuss their typical applications in industry.
- 4
Mention advantages and disadvantages of each.
- 5
Conclude with a summary of when to use each system.
Example Answers
DCS stands for Distributed Control System, and it is used for more complex process control, often in large facilities like chemical plants. PLCs, or Programmable Logic Controllers, are typically used for discrete control tasks, like assembly lines. DCS is better for continuous processes, while PLCs are ideal for event-driven control.
Don't Just Read Process Control Engineer Questions - Practice Answering Them!
Reading helps, but actual practice is what gets you hired. Our AI feedback system helps you improve your Process Control Engineer interview answers in real-time.
Personalized feedback
Unlimited practice
Used by hundreds of successful candidates
Can you explain how you would create a model of a chemical process for control purposes?
How to Answer
- 1
Identify the key process variables and their relationships.
- 2
Choose an appropriate modeling method such as empirical, first principles, or simulation.
- 3
Gather data from the process to inform your model parameters.
- 4
Validate the model against known benchmarks or historical data.
- 5
Ensure the model is adaptable for integration with control systems.
Example Answers
I would start by identifying the main variables like temperature, pressure, and flow rates. Then, I'd use first principles to create a mathematical model of the reactions involved. After that, I'd gather operational data to fine-tune the parameters before validating the model with historical performance data to ensure its accuracy.
What considerations do you take into account when selecting instrumentation for a control system?
How to Answer
- 1
Identify the specific process requirements and parameters that need to be measured.
- 2
Consider the accuracy, range, and response time required for the application.
- 3
Evaluate the environmental conditions where the instrumentation will be used.
- 4
Ensure compatibility with existing control systems and communication protocols.
- 5
Assess the maintenance needs and reliability of the instrumentation.
Example Answers
I consider the process requirements such as pressure and temperature ranges, ensuring the instrumentation can operate accurately within those limits.
Explain the concept of a feedback loop and its importance in process control.
How to Answer
- 1
Define a feedback loop in simple terms
- 2
Explain its main components: measurement, comparison, and adjustment
- 3
Highlight its role in maintaining system stability
- 4
Discuss how it helps in correcting errors in processes
- 5
Provide a real-world example related to process control
Example Answers
A feedback loop is a system where the output is monitored and compared to a desired input. It consists of measurement, comparison, and adjustment stages. This loop is crucial because it maintains the stability of processes by correcting deviations from the desired outcome. For example, in temperature control of a reactor, if the temperature exceeds the setpoint, the feedback loop reduces heating to bring the temperature back down.
What role do Safety Instrumented Systems (SIS) play in process control?
How to Answer
- 1
Define Safety Instrumented Systems and their purpose in safety.
- 2
Explain how SIS mitigate risks in process operations.
- 3
Discuss the relationship between SIS and regulatory standards.
- 4
Mention specific components of SIS and their functions.
- 5
Highlight the importance of SIS in maintaining process safety integrity.
Example Answers
Safety Instrumented Systems are crucial for ensuring the safe operation of industrial processes. They detect unsafe conditions and automatically initiate corrective actions to prevent accidents, thereby mitigating risks and protecting both personnel and equipment.
How would you set up a SCADA system for monitoring and control?
How to Answer
- 1
Identify the key processes to monitor and control
- 2
Select appropriate hardware and software components for SCADA
- 3
Design the communication architecture including protocols
- 4
Implement security measures for the system
- 5
Develop user interfaces for operator interaction and data visualization
Example Answers
I would first identify critical processes and data points needed for monitoring. Then, I would select robust SCADA software like Wonderware or Ignition, and choose PLCs that support the necessary communication protocols. After that, I'd design a secure network architecture with proper firewalls, and finally create intuitive dashboards for operators.
What experience do you have with programming languages commonly used in process control, such as Ladder Logic or Structured Text?
How to Answer
- 1
Mention specific projects or systems where you used Ladder Logic or Structured Text
- 2
Describe the complexity of the tasks you handled with these languages
- 3
Highlight any certifications or training in process control programming
- 4
Discuss your problem-solving approach using these languages in real-world scenarios
- 5
Keep your answer focused on relevant experience to the role
Example Answers
In my previous role at XYZ Corporation, I developed control logic using Ladder Logic for a batch processing system that improved efficiency by 20%.
Explain how a variable frequency drive (VFD) is used to control a pump in a process system.
How to Answer
- 1
Start with a brief definition of a VFD.
- 2
Explain its role in adjusting pump speed.
- 3
Mention the benefits of using a VFD for energy efficiency.
- 4
Include how VFDs can maintain flow and pressure control.
- 5
Wrap up with any relevant safety features related to VFDs.
Example Answers
A variable frequency drive, or VFD, controls the speed of a pump by varying the frequency of the electrical supply to the motor. This allows for precise control over pump speed, which can enhance energy efficiency and reduce wear on the system. By adjusting the pump speed, we can maintain consistent flow rates and pressure levels in the process.
What are the key components of an industrial control network, and how do they interact?
How to Answer
- 1
Identify the main components like sensors, controllers, and actuators.
- 2
Explain the role of communication protocols in network interaction.
- 3
Mention the significance of the Human-Machine Interface (HMI).
- 4
Discuss how data flows between components to control processes.
- 5
Highlight security measures and their importance in network integrity.
Example Answers
An industrial control network typically includes sensors, controllers, actuators, and HMIs. Sensors collect data, which is sent to controllers using communication protocols like Modbus. The controllers process this data and send commands to actuators. The HMI allows operators to monitor and interact with the system, while security measures ensure safe data transmission.
Don't Just Read Process Control Engineer Questions - Practice Answering Them!
Reading helps, but actual practice is what gets you hired. Our AI feedback system helps you improve your Process Control Engineer interview answers in real-time.
Personalized feedback
Unlimited practice
Used by hundreds of successful candidates
Situational Interview Questions
A critical piece of hardware in your control system has failed. How do you handle this situation?
How to Answer
- 1
Assess the impact of the hardware failure on the system's performance.
- 2
Immediately notify the relevant stakeholders or team members.
- 3
Consult the documentation to identify the cause and possible remedies.
- 4
Implement temporary solutions to mitigate the impact if possible.
- 5
Plan and execute a replacement or repair while ensuring minimal downtime.
Example Answers
I would first assess how the hardware failure affects the entire control system, then inform my team about the issue. After that, I would check the documentation for troubleshooting steps and consider temporary solutions like rerouting processes. Finally, I would plan to replace or repair the hardware as quickly as possible.
Imagine a control loop is oscillating. How would you diagnose and resolve the issue?
How to Answer
- 1
Check for tuning parameters that may be too aggressive.
- 2
Examine the feedback signal for noise or interference.
- 3
Look for external disturbances affecting the process.
- 4
Review the control strategy and consider moving to a PID tuning method.
- 5
Perform a system identification to understand the process dynamics.
Example Answers
First, I would review the tuning parameters to ensure they are not set too aggressively. Then, I'd inspect the feedback signal for any noise or disturbances that could be contributing to the oscillation.
Don't Just Read Process Control Engineer Questions - Practice Answering Them!
Reading helps, but actual practice is what gets you hired. Our AI feedback system helps you improve your Process Control Engineer interview answers in real-time.
Personalized feedback
Unlimited practice
Used by hundreds of successful candidates
You need to start up a process from a cold state. What steps will you take to ensure safety and proper control?
How to Answer
- 1
Review the process safety plan to identify hazards
- 2
Verify that all equipment is in good working order and properly calibrated
- 3
Conduct a pre-startup safety review with the team
- 4
Ensure all safety interlocks and alarms are functional
- 5
Slowly ramp up the process while monitoring key parameters closely
Example Answers
First, I will review the safety plan to understand any hazards associated with the process. Then, I will check that all equipment is operational and calibrated. A pre-startup safety review with the team will ensure everyone is aware of their roles. During startup, I will increase the process parameters gradually while monitoring the critical variables closely to spot any issues early.
A process is underperforming. What steps would you take to analyze and improve its performance?
How to Answer
- 1
Gather data on the current process performance metrics.
- 2
Identify the root causes of underperformance using tools like cause-and-effect diagrams.
- 3
Implement small-scale changes to test possible improvements.
- 4
Monitor the impact of changes on performance metrics and adjust accordingly.
- 5
Document findings and standardize successful changes.
- 6
Engage team members in the analysis to incorporate different perspectives.
Example Answers
First, I would collect data on the current performance metrics to understand the extent of the underperformance. Then, I would use root cause analysis to identify specific issues. After pinpointing the causes, I'd propose small adjustments to see if they improve performance. Monitoring the results closely would help determine if these changes are effective, and I’d involve the team for insights throughout the process.
How would you respond if a process deviation causes an immediate safety hazard?
How to Answer
- 1
Identify the safety hazard promptly and communicate it to the team.
- 2
Initiate emergency shutdown procedures if necessary and safe to do so.
- 3
Assess the situation to understand the deviation and its risks.
- 4
Implement containment measures to prevent escalation.
- 5
Document the incident for further analysis and reporting.
Example Answers
I would immediately notify my team about the safety hazard and follow our emergency protocol to ensure everyone’s safety. Next, I would assess the situation and determine if an emergency shutdown is necessary to prevent any harm.
You are tasked with evaluating new control technology. How would you approach this task?
How to Answer
- 1
Identify the specific needs and objectives for the control technology.
- 2
Research available technologies and their performance metrics.
- 3
Evaluate the compatibility of new technology with existing systems.
- 4
Consider the cost-benefit analysis of implementation.
- 5
Seek input from team members and stakeholders for a holistic view.
Example Answers
I would start by defining the goals of the control system, then research various technologies that meet those demands. After gathering data, I'd assess how well these solutions integrate with our current processes and conduct a cost-benefit analysis to justify any investments.
How would you approach a mandate to reduce operational costs through process control improvements?
How to Answer
- 1
Analyze current processes and identify areas with high costs and inefficiencies
- 2
Research and implement advanced process control techniques like PID tuning or model predictive control
- 3
Collaborate with operations and maintenance teams to gather insights and feedback
- 4
Monitor key performance indicators post-implementation to measure cost reductions
- 5
Suggest incremental changes to minimize disruptions while optimizing costs
Example Answers
I would start by analyzing the current process data to identify inefficiencies and high-cost areas. Then, I would implement advanced control strategies such as PID tuning, which can dramatically improve process stability and reduce waste. After these changes, I'd track the impact on KPIs to ensure we're on the right path to reducing costs.
You have been assigned to manage a project to upgrade a control system. What is your plan of action?
How to Answer
- 1
Assess the current control system and identify its limitations.
- 2
Engage stakeholders to gather requirements and expectations.
- 3
Develop a project plan outlining milestones, resources, and budget.
- 4
Select appropriate technologies and vendors for the upgrade.
- 5
Implement a testing and validation phase to ensure system performance.
Example Answers
First, I would evaluate the existing control system to pinpoint issues. Then, I'd hold meetings with key stakeholders to understand their needs for the upgrade. After that, I'd create a project plan that includes schedules and resource allocation. I'll also research and select suitable technology vendors. Finally, I will test the new system thoroughly before deployment to confirm it meets our expectations.
A new regulation affects your process control operations. How will you ensure compliance?
How to Answer
- 1
Review the specific requirements of the new regulation thoroughly
- 2
Assess the current process control systems for compliance gaps
- 3
Implement necessary modifications to processes and control systems
- 4
Document all changes and maintain compliance records
- 5
Train staff on the new regulations and compliance procedures
Example Answers
I will start by carefully reviewing the new regulation to understand its requirements. Then, I'll audit our existing processes to identify any compliance gaps. After that, I will make necessary adjustments to our control systems and document all changes clearly. Additionally, I will ensure that team members are trained on these new compliance requirements to avoid any issues.
You receive negative feedback about a control system you designed. How do you address it?
How to Answer
- 1
Listen carefully to the feedback without interrupting.
- 2
Ask clarifying questions to understand the issues better.
- 3
Acknowledge the feedback and take responsibility if applicable.
- 4
Develop a corrective action plan to improve the system.
- 5
Follow up on the changes and communicate progress to stakeholders.
Example Answers
I first listened to the feedback attentively and made sure I understood the concerns. Then, I asked specific questions to clarify the underlying issues. Acknowledging the points raised, I took responsibility for areas that were lacking. I created a plan to implement improvements and kept stakeholders updated on our progress.
Don't Just Read Process Control Engineer Questions - Practice Answering Them!
Reading helps, but actual practice is what gets you hired. Our AI feedback system helps you improve your Process Control Engineer interview answers in real-time.
Personalized feedback
Unlimited practice
Used by hundreds of successful candidates
How would you handle integrating a new control system into an existing operational environment?
How to Answer
- 1
Assess the current systems and identify compatibility issues
- 2
Engage stakeholders early to gather requirements and expectations
- 3
Develop a phased integration plan to minimize operational disruptions
- 4
Conduct testing in a controlled environment before full deployment
- 5
Provide training for operators on the new system features and functionalities
Example Answers
First, I would review the existing control systems to pinpoint any potential compatibility challenges. Then, I'd involve key stakeholders to understand their needs and concerns. After that, I would create a comprehensive integration timeline, ensuring that we test the new system thoroughly in a lab setting before we start the phased rollout. Finally, I would organize training sessions for the operators to familiarize them with the new technology.
What steps would you take to train operators on a new process control system?
How to Answer
- 1
Assess the current skill levels of the operators
- 2
Develop a tailored training program that includes theory and hands-on practice
- 3
Use simulations to create realistic operating conditions for training
- 4
Incorporate clear and accessible training materials, such as manuals and videos
- 5
Set up a follow-up plan for ongoing support and assessment after training
Example Answers
I would start by assessing the operators' current skills to identify their training needs. Then, I would create a structured training program that combines theoretical knowledge with hands-on practice on the new system. Simulations of the process would help them apply what they've learned in a safe environment. To ensure they have resources to refer to later, I'd provide clear manuals and videos. Finally, I would implement a support system to answer questions and assess their progress after the training.
Process Control Engineer Position Details
Salary Information
Recommended Job Boards
CareerBuilder
www.careerbuilder.com/jobs/process-control-engineerThese job boards are ranked by relevance for this position.
Related Positions
Ace Your Next Interview!
Practice with AI feedback & get hired faster
Personalized feedback
Used by hundreds of successful candidates
Ace Your Next Interview!
Practice with AI feedback & get hired faster
Personalized feedback
Used by hundreds of successful candidates