Top 30 Process Improvement Engineer Interview Questions and Answers [Updated 2025]
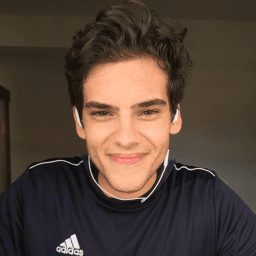
Andre Mendes
•
March 30, 2025
Are you preparing for a Process Improvement Engineer interview and eager to make a lasting impression? This blog post compiles the most common interview questions for this dynamic role, offering insightful example answers and invaluable tips to help you respond with confidence and clarity. Dive in to discover how to articulate your expertise and stand out in your next interview.
Download Process Improvement Engineer Interview Questions in PDF
To make your preparation even more convenient, we've compiled all these top Process Improvement Engineerinterview questions and answers into a handy PDF.
Click the button below to download the PDF and have easy access to these essential questions anytime, anywhere:
List of Process Improvement Engineer Interview Questions
Behavioral Interview Questions
Describe a time when you worked as part of a team to improve a process. What was your role and what was the outcome?
How to Answer
- 1
Choose a specific project where teamwork was essential.
- 2
Clearly define your role and contributions to the team.
- 3
Summarize the problem you addressed and the process improvement made.
- 4
Quantify the results or improvements achieved where possible.
- 5
Reflect on what you learned from this experience.
Example Answers
In a manufacturing project, I collaborated with a cross-functional team to reduce production downtime. My role was to analyze data and identify bottlenecks. We implemented a revised maintenance schedule, which decreased downtime by 20% and saved the company approximately $50,000 annually.
Can you give an example of a major process challenge you faced in your previous role and how you solved it?
How to Answer
- 1
Choose a specific challenge relevant to process improvement.
- 2
Use the STAR method: Situation, Task, Action, Result.
- 3
Quantify the results where possible to show impact.
- 4
Highlight teamwork and collaboration in your solution.
- 5
Reflect on what you learned from the experience.
Example Answers
In my last role, we faced high defect rates in our production line. I led a cross-functional team to analyze the root causes, which included poor training and outdated equipment. We implemented a new training program and upgraded automation tools, reducing defects by 30% within three months.
Don't Just Read Process Improvement Engineer Questions - Practice Answering Them!
Reading helps, but actual practice is what gets you hired. Our AI feedback system helps you improve your Process Improvement Engineer interview answers in real-time.
Personalized feedback
Unlimited practice
Used by hundreds of successful candidates
Tell me about a time when you led a project aimed at process improvement. What strategies did you use?
How to Answer
- 1
Use the STAR method: Situation, Task, Action, Result.
- 2
Highlight specific metrics or outcomes that improved.
- 3
Mention collaboration with team members or stakeholders.
- 4
Include any tools or methodologies applied, like Lean or Six Sigma.
- 5
Show your leadership skills in facilitating change.
Example Answers
In my previous role, we had an issue with high production waste. I led a project where we mapped the current process. We implemented Lean principles which resulted in a 20% reduction in waste over three months, saving the company $50,000 annually.
Describe a situation where you had to communicate a complex process change to a team. How did you ensure understanding?
How to Answer
- 1
Identify the process change clearly and concisely.
- 2
Use simple language and avoid jargon.
- 3
Involve the team by asking for their input and questions.
- 4
Provide visual aids, such as flowcharts or diagrams.
- 5
Follow up with a summary and check for understanding.
Example Answers
In my last project, we implemented a new reporting system. I scheduled a team meeting where I explained the change using a flowchart that illustrated the new process step-by-step. I encouraged questions throughout and sent a follow-up email summarizing the key points.
Can you provide an instance when you had to quickly adapt your process improvement approach to a changing situation?
How to Answer
- 1
Choose a specific project where circumstances changed unexpectedly.
- 2
Explain the original process and what changes occurred.
- 3
Describe how you modified your approach to address the new situation.
- 4
Highlight the outcome and any positive impact from your adaptation.
- 5
Keep your response focused on your actions and the results achieved.
Example Answers
In my last role, we were implementing a new software system when the vendor changed the delivery timeline unexpectedly. I quickly reassessed our training schedule and prioritized critical features to ensure the team was prepared. This flexibility allowed us to meet project deadlines without sacrificing quality, leading to a smooth rollout.
Can you provide an example of how you have fostered a culture of continuous improvement in your workplace?
How to Answer
- 1
Identify a specific initiative that encouraged improvement
- 2
Describe the steps taken to involve team members
- 3
Highlight measurable outcomes or results
- 4
Mention any tools or methodologies used
- 5
Discuss how feedback was incorporated into the process
Example Answers
In my previous role, I initiated a monthly Kaizen event where team members could present improvement ideas. We used value stream mapping to identify waste and streamline our processes, which led to a 20% reduction in cycle time over six months.
Describe a time when you trained others on a new process. What challenges did you face?
How to Answer
- 1
Choose a specific training experience that highlights your role.
- 2
Identify key challenges you faced during the training.
- 3
Explain how you overcame those challenges effectively.
- 4
Mention the positive outcomes or improvements resulting from the training.
- 5
Reflect on any feedback you received and what you learned.
Example Answers
In my previous role, I trained a team on a new inventory management system. A major challenge was resistance to change, as some team members preferred the old system. I organized hands-on workshops to demonstrate benefits and addressed their concerns directly. By the end of the training, team efficiency improved by 20%, and I received positive feedback for my approach.
Describe a situation where you had to manage multiple competing deadlines in a process improvement initiative.
How to Answer
- 1
Clearly define the competing deadlines and their importance.
- 2
Explain how you prioritized tasks based on impact and urgency.
- 3
Describe the tools or methods you used to keep track of progress.
- 4
Highlight communication with stakeholders to set expectations.
- 5
Share the outcome and any lessons learned from the experience.
Example Answers
In my previous role, I faced a situation with two overlapping deadlines for process audits. I prioritized the one with a higher impact on compliance, then created a timeline for both projects. I used project management software to track progress and updated stakeholders regularly, resulting in successful completion of both audits ahead of time.
Don't Just Read Process Improvement Engineer Questions - Practice Answering Them!
Reading helps, but actual practice is what gets you hired. Our AI feedback system helps you improve your Process Improvement Engineer interview answers in real-time.
Personalized feedback
Unlimited practice
Used by hundreds of successful candidates
Technical Interview Questions
What process improvement methodologies are you familiar with, and how have you applied them in your work?
How to Answer
- 1
Identify 2 to 3 methodologies like Lean, Six Sigma, or Kaizen.
- 2
Share a specific project where you implemented one of these methodologies.
- 3
Explain the problem you addressed and the results you achieved.
- 4
Use metrics or data to show the impact of your improvements.
- 5
Be prepared to discuss challenges faced during implementation.
Example Answers
I am familiar with Lean and Six Sigma. In my previous role, I led a project using Lean principles to reduce waste in our production line, which resulted in a 20% increase in efficiency and saved the company $50,000 annually.
What tools or software have you used for process mapping and analysis?
How to Answer
- 1
Identify specific tools you have experience with.
- 2
Explain how you used each tool in a project.
- 3
Highlight any certifications or training related to these tools.
- 4
Mention the outcomes or improvements achieved using these tools.
- 5
Keep your response concise and focused on relevant experience.
Example Answers
I have used Visio for creating process maps and identifying bottlenecks. In my last project, I collaborated with team members to streamline workflows, resulting in a 20% reduction in processing time.
Don't Just Read Process Improvement Engineer Questions - Practice Answering Them!
Reading helps, but actual practice is what gets you hired. Our AI feedback system helps you improve your Process Improvement Engineer interview answers in real-time.
Personalized feedback
Unlimited practice
Used by hundreds of successful candidates
Explain how you have used data analysis in a previous process improvement project.
How to Answer
- 1
Identify a specific project where you applied data analysis.
- 2
Describe the data you collected and the methods used for analysis.
- 3
Explain how the analysis influenced the improvement decisions.
- 4
Quantify the results or improvements achieved through the project.
- 5
Use clear and straightforward language to communicate your findings.
Example Answers
In a recent project, I analyzed production efficiency data using statistical process control charts. By identifying trends, we reduced waste by 20%, leading to increased productivity.
What key performance metrics do you consider when evaluating process efficiency?
How to Answer
- 1
Identify specific metrics that align with the process goals
- 2
Include quantitative measures like cycle time and throughput
- 3
Discuss qualitative metrics such as customer satisfaction
- 4
Mention how you track and analyze these metrics over time
- 5
Provide examples of how these metrics have influenced past projects
Example Answers
I focus on cycle time and throughput as they indicate how quickly a process runs. I also look at defect rates, as they show areas needing improvement. Tracking these metrics helps us identify trends and address inefficiencies.
How do you approach benchmarking in process improvement? Can you provide an example?
How to Answer
- 1
Identify key performance indicators relevant to your process
- 2
Research industry standards and best practices for comparison
- 3
Collect data on both internal and external benchmarks
- 4
Analyze gaps between your performance and benchmark data
- 5
Create actionable plans based on findings to improve processes
Example Answers
In my last role, I benchmarked our production efficiency against industry standards. I found that we lagged behind by 15%. By implementing Lean principles based on best practices, we increased our efficiency by 20% within six months.
What techniques do you use for root cause analysis in a process improvement context?
How to Answer
- 1
Start by defining the problem clearly and gathering relevant data
- 2
Utilize techniques like the 5 Whys to drill down to the root cause
- 3
Employ Fishbone Diagrams to visually categorize potential causes
- 4
Consider using Failure Mode and Effects Analysis (FMEA) for a structured approach
- 5
Involve cross-functional teams to gain diverse perspectives on the issue
Example Answers
I define the problem clearly and gather data before applying the 5 Whys technique. This method helps me identify the root cause by asking 'why' multiple times until we reach the fundamental issue.
Can you explain how you have applied Lean principles in your previous work?
How to Answer
- 1
Identify a specific project where you implemented Lean principles
- 2
Describe the problem or waste you addressed
- 3
Explain the Lean tools or techniques you used
- 4
Share measurable results or improvements achieved
- 5
Discuss how the team responded to changes
Example Answers
In my previous role, I led a project to reduce cycle time in our assembly line. We identified excess motion as a key waste. By implementing 5S and value stream mapping, we reorganized the workspace and streamlined processes, resulting in a 20% reduction in cycle time.
What experience do you have with process mapping, and which tools do you prefer for it?
How to Answer
- 1
Identify specific projects where you utilized process mapping.
- 2
Mention the tools you used and why you prefer them.
- 3
Highlight the impact your process mapping had on project outcomes.
- 4
Discuss any team collaboration involved during the mapping process.
- 5
Stay concise and focus on relevant experiences.
Example Answers
In my last role, I led a project to map the supply chain process using Visio. This helped identify bottlenecks, resulting in a 20% reduction in lead time.
What strategies have you used to achieve cost reduction through process improvements?
How to Answer
- 1
Identify specific processes you improved and the baseline costs.
- 2
Explain the tools or methodologies you applied, like Lean or Six Sigma.
- 3
Quantify the cost savings and timeframe to show impact.
- 4
Highlight collaboration with teams to implement changes.
- 5
Discuss any follow-up measures to ensure sustainability of improvements.
Example Answers
In my previous role, I streamlined the inventory management process, reducing excess stock by 30%. I used Lean methodologies to eliminate waste, resulting in annual savings of $50,000 within six months.
What is your experience with Six Sigma, and how have you implemented its concepts in your work?
How to Answer
- 1
Mention your specific Six Sigma certification level and training.
- 2
Describe a project where you applied Six Sigma methods.
- 3
Use metrics to demonstrate the impact of your actions.
- 4
Highlight your role in a team and any leadership aspects.
- 5
Discuss ongoing use of Six Sigma principles in your current work.
Example Answers
I am a Six Sigma Green Belt certified professional. In my last project, I led a team to reduce defects in our manufacturing line by 30% using DMAIC methodology. This resulted in cost savings of $50,000 annually. I regularly apply these principles to streamline processes, ensuring continuous improvement.
Don't Just Read Process Improvement Engineer Questions - Practice Answering Them!
Reading helps, but actual practice is what gets you hired. Our AI feedback system helps you improve your Process Improvement Engineer interview answers in real-time.
Personalized feedback
Unlimited practice
Used by hundreds of successful candidates
Situational Interview Questions
If you encounter resistance from team members regarding a process change, how would you handle the situation?
How to Answer
- 1
Acknowledge their concerns and listen actively to understand their perspective
- 2
Communicate the benefits of the change clearly to the team
- 3
Involve team members in the implementation process to gain their buy-in
- 4
Provide training and support to help ease the transition
- 5
Follow up and seek feedback after implementation to address any ongoing issues
Example Answers
I would start by listening to the team's concerns about the process change. Understanding their perspective allows me to address specific worries. Then, I would explain the benefits of the change, ensuring they see how it helps not just the organization but also their workload.
Imagine you have multiple process improvement projects with tight deadlines. How would you prioritize them?
How to Answer
- 1
Assess the impact of each project on business goals
- 2
Evaluate the urgency based on deadlines and resources available
- 3
Consult with stakeholders to understand their needs
- 4
Consider dependencies and how one project may affect another
- 5
Use a scoring system to objectively rank the projects
Example Answers
I would first evaluate each project's impact on key business objectives to ensure alignment with company goals. Next, I would identify which projects have the tightest deadlines and assess available resources. Consulting with stakeholders would be crucial to grasp their priorities, and I'd analyze any dependencies among projects to avoid bottlenecks, ultimately scoring them to prioritize effectively.
Don't Just Read Process Improvement Engineer Questions - Practice Answering Them!
Reading helps, but actual practice is what gets you hired. Our AI feedback system helps you improve your Process Improvement Engineer interview answers in real-time.
Personalized feedback
Unlimited practice
Used by hundreds of successful candidates
How would you involve stakeholders in identifying process improvement opportunities?
How to Answer
- 1
Engage stakeholders through regular meetings to discuss their pain points and observations.
- 2
Use surveys or questionnaires to gather input on current processes and their effectiveness.
- 3
Facilitate workshops to brainstorm ideas for improvement, ensuring all voices are heard.
- 4
Encourage stakeholders to track and report inefficiencies they encounter in their daily tasks.
- 5
Create a feedback loop by keeping stakeholders informed about implemented changes and outcomes.
Example Answers
I would organize regular meetings with stakeholders to discuss their challenges and gather insights on processes. This would help us identify improvement opportunities directly from those impacted.
If tasked with developing a new process for an unfamiliar area, what steps would you take to ensure its effectiveness?
How to Answer
- 1
Conduct thorough research to understand the current practices and challenges in the area.
- 2
Engage stakeholders to gather insights and identify their needs and expectations.
- 3
Develop a clear process map that outlines each step in the new process.
- 4
Implement a pilot program to test the new process in a controlled environment.
- 5
Gather feedback and make iterative improvements based on real-world performance.
Example Answers
I would start by researching existing processes and challenges to gain a solid understanding. Then, I would engage with stakeholders to ensure their needs are incorporated. Developing a clear process map would follow next, and I'd run a pilot program to test and refine the process based on feedback.
What actions would you take if a new process implementation led to unforeseen issues?
How to Answer
- 1
Assess the root cause of the issues immediately
- 2
Communicate transparently with all stakeholders about the problems
- 3
Develop a corrective action plan with clear timelines
- 4
Test proposed solutions on a small scale before full implementation
- 5
Monitor the revised process closely and solicit feedback
Example Answers
First, I would investigate the root cause of the issues by reviewing data and gathering insights from team members. Then, I would inform stakeholders of the situation and work collaboratively to develop a corrective action plan. After devising potential solutions, I’d implement them on a small scale, assess their impact, and adjust as needed based on feedback.
If you have limited resources for a project, how would you ensure successful implementation of process improvements?
How to Answer
- 1
Identify critical processes that yield the greatest impact
- 2
Engage team members for ideas and support in resource allocation
- 3
Utilize data to prioritize improvements based on cost-effectiveness
- 4
Pilot test improvements on a small scale before full implementation
- 5
Monitor progress and adapt strategies based on feedback
Example Answers
I would begin by identifying the most critical processes that can deliver significant results. Next, I would engage my team to gather insights and determine the best way to allocate our limited resources effectively. Using data analysis, I would prioritize improvements that are cost-effective, then run pilot tests to ensure viability before full-scale implementation. Throughout this process, I'd consistently monitor progress and adjust as necessary.
How would you gather and incorporate feedback from end users after implementing a process change?
How to Answer
- 1
Schedule follow-up meetings with end users shortly after the implementation.
- 2
Create a simple feedback form to collect user insights and suggestions.
- 3
Observe users in their workflow to identify any issues or improvements.
- 4
Establish a dedicated communication channel for ongoing feedback.
- 5
Analyze feedback and prioritize changes based on user impact and feasibility.
Example Answers
I would organize follow-up meetings with end users to discuss their experience and gather insights. Additionally, I'd create a feedback form to collect structured responses and encourage all users to participate.
How would you evaluate the success of a process improvement initiative you've led?
How to Answer
- 1
Define clear metrics before implementing the initiative
- 2
Use quantitative data to measure performance changes
- 3
Gather qualitative feedback from stakeholders
- 4
Compare results against baseline performance
- 5
Document lessons learned for future improvements
Example Answers
I defined key performance indicators such as cycle time and error rates before the initiative. After implementation, I tracked these metrics and found a 25% reduction in cycle time, which I validated through stakeholder feedback.
If team dynamics are negatively impacting a process improvement project, what steps would you take?
How to Answer
- 1
Identify specific team dynamics causing issues.
- 2
Facilitate an open discussion to hear everyone’s concerns.
- 3
Encourage collaboration by setting common goals.
- 4
Implement team-building activities to improve relationships.
- 5
Monitor progress and adjust strategies as needed.
Example Answers
I would first analyze the team dynamics to pinpoint where the conflicts are. Then, I would hold a discussion where each member shares their concerns, encouraging an open dialogue to address issues. By setting common goals, I would align the team’s focus, followed by team-building activities to enhance trust and collaboration.
If you identify an innovative idea for process improvement that may not align with existing workflows, how would you approach it?
How to Answer
- 1
Research the innovative idea's potential impact on current processes
- 2
Gather data to support your proposal and address concerns
- 3
Engage key stakeholders early to understand their perspectives
- 4
Develop a pilot plan to test the idea without full implementation
- 5
Communicate clearly how the change benefits the team and organization
Example Answers
I would start by researching how my idea could enhance efficiency. After gathering relevant data, I would present it to key stakeholders to get their feedback. If they have concerns, I would address them before proposing a small-scale pilot to demonstrate the idea's effectiveness.
Don't Just Read Process Improvement Engineer Questions - Practice Answering Them!
Reading helps, but actual practice is what gets you hired. Our AI feedback system helps you improve your Process Improvement Engineer interview answers in real-time.
Personalized feedback
Unlimited practice
Used by hundreds of successful candidates
Process Improvement Engineer Position Details
Salary Information
Recommended Job Boards
These job boards are ranked by relevance for this position.
Related Positions
Ace Your Next Interview!
Practice with AI feedback & get hired faster
Personalized feedback
Used by hundreds of successful candidates
Ace Your Next Interview!
Practice with AI feedback & get hired faster
Personalized feedback
Used by hundreds of successful candidates