Top 29 Process Controls Engineer Interview Questions and Answers [Updated 2025]
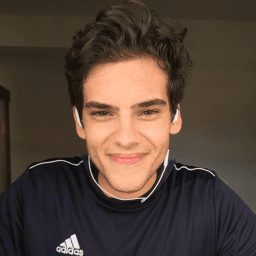
Andre Mendes
•
March 30, 2025
Embarking on a journey to secure a role as a Process Controls Engineer? This blog post is your ultimate guide, featuring the most common interview questions you might face. Dive into expertly crafted example answers and insightful tips to help you tackle each question with confidence and finesse. Prepare yourself to impress potential employers and stand out in your next interview with this comprehensive resource.
Download Process Controls Engineer Interview Questions in PDF
To make your preparation even more convenient, we've compiled all these top Process Controls Engineerinterview questions and answers into a handy PDF.
Click the button below to download the PDF and have easy access to these essential questions anytime, anywhere: