Top 30 Process Engineer Interview Questions and Answers [Updated 2025]
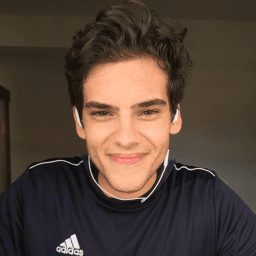
Andre Mendes
•
March 30, 2025
Navigating the competitive field of process engineering requires thorough preparation, especially when it comes to interviews. In this post, we delve into the most common interview questions for the Process Engineer role, providing you with example answers and effective tips. Whether you're a seasoned professional or a recent graduate, this guide will equip you with the insights needed to impress your potential employers.
Get Process Engineer Interview Questions PDF
Get instant access to all these Process Engineer interview questions and expert answers in a convenient PDF format. Perfect for offline study and interview preparation.
Enter your email below to receive the PDF instantly:
List of Process Engineer Interview Questions
Behavioral Interview Questions
Describe a time when you faced a significant challenge in a bioprocessing project. How did you approach solving it?
How to Answer
- 1
Identify a specific challenge that had a measurable impact on the project.
- 2
Explain the steps you took to analyze the problem and develop a plan.
- 3
Detail any collaboration with team members or stakeholders to gather insights.
- 4
Discuss the outcome, emphasizing what you learned and how it improved your skills.
- 5
Keep it concise and focused on your actions and results.
Example Answers
In a recent project, we encountered unexpected yield loss during fermentation. I analyzed the process data and identified temperature fluctuations as a potential cause. Collaborating with my team, we adjusted the temperature control system and monitored the results, ultimately increasing our yield by 15%. This taught me the importance of data analysis and team collaboration.
Can you give an example of a project where you had to adapt quickly to changing requirements or processes?
How to Answer
- 1
Identify a specific project with clear changing requirements
- 2
Use the STAR method: Situation, Task, Action, Result
- 3
Emphasize your problem-solving skills and flexibility
- 4
Highlight any collaboration with team members
- 5
Conclude with what you learned from the experience
Example Answers
In my previous project on developing a bioreactor system, mid-way we received new compliance requirements from the regulatory body. I quickly assessed the impact on our timeline and organized a team meeting to brainstorm solutions. We adapted our design and submitted it ahead of the revised deadline, ensuring regulatory compliance. This taught me the importance of swift communication and teamwork in a dynamic environment.
Good Candidates Answer Questions. Great Ones Win Offers.
Reading sample answers isn't enough. Top candidates practice speaking with confidence and clarity. Get real feedback, improve faster, and walk into your next interview ready to stand out.
Master your interview answers under pressure
Boost your confidence with real-time practice
Speak clearly and impress hiring managers
Get hired faster with focused preparation
Used by thousands of successful candidates
Tell me about a time you led a team in a bioprocess engineering project. What was the outcome?
How to Answer
- 1
Choose a specific project example with measurable outcomes
- 2
Describe your role and actions as a leader clearly
- 3
Highlight teamwork and collaboration among members
- 4
Mention any challenges faced and how they were overcome
- 5
Conclude with the positive impact or results of the project
Example Answers
In my last position, I led a team to optimize a bioreactor process. We aimed to increase yield by 20%. I facilitated weekly meetings to track progress and share insights. We encountered an issue with nutrient uptake, but by adjusting the feeding strategy, we met our target with a 25% yield increase.
Have you ever had to explain complex bioprocessing concepts to someone without a technical background? How did you do it?
How to Answer
- 1
Identify key points of the concept
- 2
Use analogies or everyday examples
- 3
Avoid technical jargon
- 4
Gradually build complexity based on the listener's understanding
- 5
Encourage questions to ensure clarity
Example Answers
When explaining fermentation processes, I likened it to baking bread, where yeast consumes sugar to produce gas and alcohol. This analogy helped the audience grasp the essential concept without technical terms.
Describe a situation where you had to resolve a conflict within a project team. How did you handle it and what was the result?
How to Answer
- 1
Identify a specific conflict situation you faced.
- 2
Explain your approach to understanding different perspectives.
- 3
Describe the steps you took to facilitate a resolution.
- 4
Highlight the skills you used, such as communication or negotiation.
- 5
Conclude with the positive outcome and what you learned.
Example Answers
During a project on developing a new bioreactor, two team members disagreed on the optimal design. I arranged a meeting where each could present their views. I facilitated the discussion, encouraging them to respect each other's opinions. We ended up merging the best aspects of both designs, resulting in an improved bioreactor that performed well in testing.
Can you describe an instance where you identified and implemented a process improvement in a bioprocess engineering project?
How to Answer
- 1
Select a specific project where you noticed inefficiencies.
- 2
Explain the data or observations that led to your identification of the problem.
- 3
Describe the solution you proposed and how you implemented it.
- 4
Quantify the results of the improvement if possible.
- 5
Keep the focus on your role and contributions.
Example Answers
In my last project on enzyme production, I noticed that our fermentation process had a long lag phase. By analyzing the growth data, I discovered that temperature fluctuations were causing stress on the microorganisms. I collaborated with the automation team to implement tighter temperature controls, reducing the lag phase by 20%, which led to a 15% increase in yield.
Give an example of a time when your attention to detail prevented a significant problem in a bioprocessing project.
How to Answer
- 1
Identify a specific project or situation where detail was crucial.
- 2
Describe the potential problem that could arise without attention to detail.
- 3
Explain your specific actions that demonstrated your attention to detail.
- 4
Highlight the positive outcome as a result of your actions.
- 5
Keep your answer focused and concise, aiming for a clear narrative.
Example Answers
During a mammalian cell culture project, I noticed that the pH levels were outside the standard operating range during a critical phase. I promptly adjusted the buffers before continuing the fermentation process, which prevented cell death and ensured a successful yield.
Describe how you have worked effectively as part of a multidisciplinary team in a bioprocessing project.
How to Answer
- 1
Identify the project and your role clearly.
- 2
Highlight collaboration with diverse specialists.
- 3
Emphasize communication skills and tools used.
- 4
Discuss contributions to the project's success.
- 5
Mention any challenges faced and how they were resolved.
Example Answers
In a recent bioprocessing project, I worked as a bioprocess engineer alongside chemists and quality assurance specialists. We held weekly meetings to track progress and address any issues collaboratively. My role involved optimizing the fermentation process, which required constant feedback from the team to align our goals and results. This approach led to a successful scale-up of production that met our timeline and quality standards.
How do you stay updated with the latest advancements in bioprocess technology and integrate them into your work?
How to Answer
- 1
Follow key industry journals and publications relevant to bioprocess engineering.
- 2
Attend industry conferences and workshops to network and learn about new technologies.
- 3
Participate in online forums and communities focused on bioprocessing.
- 4
Subscribe to relevant newsletters or podcasts that cover advancements in bioprocess technology.
- 5
Practice applying new knowledge by conducting small projects or experiments.
Example Answers
I regularly read journals like Biochemical Engineering and attend the annual Bioprocessing Summit where I learn about cutting-edge technologies. Recently, I integrated a new cell culture technique I discovered at a workshop into our processes, which improved yield by 15%.
Tell me about a time you received constructive feedback in a bioprocessing role. How did you respond to it?
How to Answer
- 1
Choose a specific example that highlights your ability to learn.
- 2
Explain the feedback clearly, showing that you understand its importance.
- 3
Describe your immediate reaction or feelings to the feedback.
- 4
Outline the steps you took to address the feedback.
- 5
Share the positive outcome or what you learned from the experience.
Example Answers
In my previous role, I received feedback that my data analysis was often too slow. I initially felt a bit defensive, but I recognized the importance of being efficient. I started using data analysis software to streamline my process. As a result, I improved my analysis time by 30%, which enhanced project timelines.
Good Candidates Answer Questions. Great Ones Win Offers.
Reading sample answers isn't enough. Top candidates practice speaking with confidence and clarity. Get real feedback, improve faster, and walk into your next interview ready to stand out.
Master your interview answers under pressure
Boost your confidence with real-time practice
Speak clearly and impress hiring managers
Get hired faster with focused preparation
Used by thousands of successful candidates
Technical Interview Questions
What are the key considerations when designing a bioreactor for a new microbial fermentation process?
How to Answer
- 1
Identify the microbial strain and its metabolic requirements
- 2
Determine the physical design including volume, shape, and materials
- 3
Consider the control of environmental parameters like temperature and pH
- 4
Plan for nutrient feeding strategies and oxygen transfer rates
- 5
Ensure scalability and compliance with regulatory standards
Example Answers
When designing a bioreactor for microbial fermentation, first identify the specific strain and its growth conditions. Then, design the physical structure to optimize volume and materials for compatibility. Control temperature and pH is crucial for optimal fermentation, alongside carefully planning nutrient additions and oxygen supply.
What factors must be considered when scaling up a bioprocess from laboratory to production scale?
How to Answer
- 1
Assess the consistency of the biological material and process.
- 2
Evaluate the impact of scale on mixing and mass transfer.
- 3
Consider the nutrient supply and design of the bioreactor.
- 4
Analyze heat transfer and temperature control needs.
- 5
Investigate regulatory compliance and safety factors.
Example Answers
When scaling up a bioprocess, it's essential to assess the consistency of the biological material. We also need to evaluate how mixing and mass transfer will be affected at larger scales, along with ensuring adequate nutrient supply in the bioreactor design.
Good Candidates Answer Questions. Great Ones Win Offers.
Reading sample answers isn't enough. Top candidates practice speaking with confidence and clarity. Get real feedback, improve faster, and walk into your next interview ready to stand out.
Master your interview answers under pressure
Boost your confidence with real-time practice
Speak clearly and impress hiring managers
Get hired faster with focused preparation
Used by thousands of successful candidates
Describe the differences between batch, fed-batch, and continuous culture in bioprocessing.
How to Answer
- 1
Define each culture type clearly and succinctly.
- 2
Highlight the key operational differences between them.
- 3
Mention an example application for each type.
- 4
Discuss the advantages and disadvantages of each method for clarity.
- 5
Keep it concise and focused on essential points.
Example Answers
Batch culture is a closed system where nutrients are added all at once, and the production occurs until the nutrients are depleted. It is simple and easy to manage but can have lower overall yield.
What methodologies do you use for optimizing fermentation parameters to improve yield and productivity?
How to Answer
- 1
Discuss using Design of Experiments (DoE) to systematically evaluate multiple parameters.
- 2
Mention strain selection and improvement through genetic engineering or adaptive evolution.
- 3
Talk about real-time monitoring and feedback control strategies during fermentation.
- 4
Highlight the importance of scale-up methods from lab to pilot and industrial scale to retain efficiency.
- 5
Include using statistical process control for consistent product quality.
Example Answers
I primarily utilize Design of Experiments to assess the impact of various fermentation parameters such as pH, temperature, and nutrient concentrations on yield. This allows for a systematic approach to optimization.
What are some common techniques for purifying proteins in downstream processing?
How to Answer
- 1
Start with general techniques like filtration and chromatography.
- 2
Mention specific types of chromatography such as gel filtration or affinity chromatography.
- 3
Discuss the importance of buffer selection in purification.
- 4
Include any additional methods like precipitation or ultrafiltration.
- 5
Emphasize the need for optimization at each step to achieve high purity.
Example Answers
Common techniques for purifying proteins include affinity chromatography, where we use tags to isolate our target protein. Gel filtration can help separate proteins based on size, and I often utilize ion exchange chromatography to exploit charge differences. Careful buffer selection is also crucial to maintaining protein stability and activity.
How do you ensure the quality and consistency of a bioprocessed product?
How to Answer
- 1
Establish robust SOPs for every step in the bioprocess.
- 2
Implement regular monitoring of critical process parameters.
- 3
Conduct thorough validation of equipment and processes.
- 4
Perform routine quality control testing on samples.
- 5
Ensure compliance with regulatory guidelines throughout production.
Example Answers
I ensure quality and consistency by implementing standard operating procedures for all bioprocess steps, monitoring critical parameters like pH and temperature continuously, and validating all equipment to avoid deviations.
What analytical techniques are commonly used in bioprocessing to monitor cellular growth and product formation?
How to Answer
- 1
Start by mentioning major techniques like optical density measurement, cell counting, and chromatography.
- 2
Explain how each technique contributes to monitoring growth and product formation.
- 3
Be specific about the instruments used for these techniques, e.g., spectrophotometers for optical density.
- 4
Include any recent advancements or trends in analytical techniques related to bioprocessing.
- 5
Keep your answer concise while showcasing your knowledge of the bioprocessing field.
Example Answers
Common techniques include measuring optical density using a spectrophotometer to assess cell growth, using hemocytometers for direct cell counting, and applying HPLC for product analysis. These methods provide real-time insights into the bioprocess effectiveness.
What are the critical differences between glass and single-use bioreactors in bioprocessing?
How to Answer
- 1
Identify key advantages and disadvantages of each type.
- 2
Discuss sterility assurance levels and contamination risks.
- 3
Consider cost implications and scalability factors.
- 4
Mention ease of use and installation for operators.
- 5
Highlight environmental impact and sustainability concerns.
Example Answers
Glass bioreactors offer higher durability and reusability, but they require extensive cleaning and sterilization processes, which increases contamination risk. In contrast, single-use bioreactors significantly reduce contamination risks and are more convenient, but can be costly over time and less environmentally sustainable due to plastic waste.
How do you implement and monitor process control strategies in a bioprocess?
How to Answer
- 1
Identify key process parameters to monitor such as temperature, pH, and dissolved oxygen.
- 2
Utilize control software and analytics for real-time data tracking.
- 3
Establish standard operating procedures (SOPs) for implementing control strategies.
- 4
Perform routine checks and calibrations to ensure instruments are accurate.
- 5
Regularly review process data and make adjustments to optimize performance.
Example Answers
I implement process control strategies by first identifying critical parameters like pH and temperature, using software tools to track these data points in real time. I follow SOPs to ensure consistency and regularly calibrate instruments to maintain accuracy.
What does cGMP stand for, and why is it important in bioprocessing?
How to Answer
- 1
Explain that cGMP stands for current Good Manufacturing Practices.
- 2
Discuss the role of cGMP in ensuring product quality and safety.
- 3
Mention regulatory compliance and its significance to bioprocessing.
- 4
Highlight how cGMP contributes to reproducibility and consistency in production.
- 5
Conclude with the impact on patient safety and market approval.
Example Answers
cGMP stands for current Good Manufacturing Practices. It is important in bioprocessing because it ensures that products are consistently produced and controlled according to quality standards, which is crucial for safety and efficacy.
Good Candidates Answer Questions. Great Ones Win Offers.
Reading sample answers isn't enough. Top candidates practice speaking with confidence and clarity. Get real feedback, improve faster, and walk into your next interview ready to stand out.
Master your interview answers under pressure
Boost your confidence with real-time practice
Speak clearly and impress hiring managers
Get hired faster with focused preparation
Used by thousands of successful candidates
How can bioinformatics tools be applied in the optimization of bioprocesses?
How to Answer
- 1
Identify specific bioinformatics tools relevant to bioprocessing.
- 2
Discuss how these tools can improve data analysis for strain optimization.
- 3
Mention how modeling and simulations can lead to better process design.
- 4
Highlight examples of genomics or proteomics data contributing to process efficiency.
- 5
Emphasize the importance of integrating bioinformatics with experimental data.
Example Answers
Bioinformatics tools like genome analysis can help identify genetic modifications in strains that enhance yield. By analyzing sequence data, we can pinpoint mutations that optimize metabolic pathways for better production rates.
Situational Interview Questions
Suppose a fermentation process starts developing unexpected contamination issues. How would you approach troubleshooting this problem?
How to Answer
- 1
Identify and isolate the source of contamination through sampling and testing.
- 2
Review historical data of the fermentation conditions for any deviations.
- 3
Implement changes incrementally to assess their impact on contamination.
- 4
Consult with teammates or experts for additional perspectives and solutions.
- 5
Document the process and findings to improve future protocols.
Example Answers
First, I would start by sampling the fermentation broth to identify the type of contamination. From there, I would review our SOPs to check for any procedural lapses that could have led to this issue.
You are tasked with reducing the cost of a bioprocess without significant impact on product quality. What steps would you take to approach this challenge?
How to Answer
- 1
Identify high-cost materials and explore alternatives.
- 2
Optimize process conditions to enhance yield and productivity.
- 3
Implement process automation to reduce labor costs.
- 4
Review and streamline the supply chain for cost efficiencies.
- 5
Conduct a risk assessment to ensure quality is not compromised.
Example Answers
First, I would analyze the raw materials and see if there are cheaper alternatives that maintain quality. Then, I would optimize the fermentation conditions to boost cell yield, which can lower costs per unit. Lastly, I'd assess our suppliers to negotiate better prices.
Good Candidates Answer Questions. Great Ones Win Offers.
Reading sample answers isn't enough. Top candidates practice speaking with confidence and clarity. Get real feedback, improve faster, and walk into your next interview ready to stand out.
Master your interview answers under pressure
Boost your confidence with real-time practice
Speak clearly and impress hiring managers
Get hired faster with focused preparation
Used by thousands of successful candidates
A new bioprocess must be developed in a tight timeline. How would you prioritize tasks and manage resources to meet the deadline?
How to Answer
- 1
Identify critical path tasks that directly impact the timeline
- 2
Allocate resources based on task priority and expertise
- 3
Communicate clearly with team members about deadlines and progress
- 4
Utilize agile methodologies to adapt quickly to changes
- 5
Conduct regular reviews to adjust priorities as needed
Example Answers
I would start by mapping out the critical path of the bioprocess development, focusing on tasks that must be completed to keep the project on schedule. I would prioritize those tasks, ensuring that our key resources are allocated accordingly. Regular check-ins with the team would help us stay aligned and make adjustments as necessary.
You notice a colleague is not following established safety protocols in the lab. What steps would you take to address the situation?
How to Answer
- 1
Observe the situation fully to ensure accuracy
- 2
Approach the colleague privately and professionally
- 3
Express your concerns about safety protocols respectfully
- 4
Encourage them to adhere to the guidelines
- 5
If the behavior continues, escalate the issue to a supervisor
Example Answers
I would first watch to confirm the colleague isn't following protocols. Then, I'd speak to them privately to express my concerns and emphasize the importance of safety. If they don't change their behavior, I'd report it to our supervisor.
You have been asked to reduce waste in a current bioprocess. How would you identify areas for improvement?
How to Answer
- 1
Start by mapping the entire bioprocess flow to visualize all steps.
- 2
Analyze data from each phase of the process to identify bottlenecks or inefficiencies.
- 3
Engage with team members to gather insights on areas where waste is observed.
- 4
Conduct a waste audit to quantify waste types and sources in the process.
- 5
Look into industry best practices for bioprocesses and compare with current methods.
Example Answers
First, I would map the entire bioprocess to identify all stages. Then, I would analyze the data to spot inefficiencies. Engaging with the team would help me gather insights about waste issues they encounter. Finally, I would conduct a waste audit to quantify waste sources.
If a critical equipment piece in a bioprocess fails unexpectedly, what steps would you take to mitigate the impact on production schedules?
How to Answer
- 1
Assess the situation and determine the cause of the failure immediately
- 2
Implement a contingency plan or standard operating procedure for equipment failure
- 3
Communicate with your team and stakeholders about the impact and next steps
- 4
Consider alternative solutions or temporary equipment to maintain production
- 5
Document the incident for future reference and to improve processes
Example Answers
First, I would quickly assess the cause of the equipment failure to determine the next steps. Then, I would notify my team about the issue and begin implementing our contingency plan. We have a spare piece of equipment that we can set up to continue production while the main equipment is offline. Finally, I would document the incident to analyze it later and improve our processes.
You are tasked with preparing a production facility for an upcoming regulatory audit. How would you ensure compliance and readiness?
How to Answer
- 1
Review all recent SOPs and ensure they are up to date with the latest regulatory standards.
- 2
Conduct a mock audit to identify potential compliance gaps and address them beforehand.
- 3
Engage the team in training sessions focused on audit preparedness and compliance requirements.
- 4
Verify that all documentation, including batch records and equipment logs, are complete and accessible.
- 5
Ensure all equipment is calibrated and maintained according to regulatory guidelines before the audit.
Example Answers
I would start by reviewing all SOPs to ensure they align with current regulations. Then, I would organize a mock audit to assess our compliance status, followed by addressing any gaps that we find. Team training on the audit process would further prepare us, and I would confirm that all necessary documentation is organized and complete.
Your team is considering implementing a new technology for bioprocess monitoring. How would you evaluate and decide on this technology?
How to Answer
- 1
Identify the specific needs and goals for the monitoring technology
- 2
Research the available technologies and their capabilities
- 3
Assess the cost-effectiveness and ROI of each option
- 4
Involve stakeholders and gather feedback on requirements
- 5
Run a pilot test to evaluate performance in a real-world scenario
Example Answers
First, I would clarify our monitoring needs, such as data accuracy and integration with existing systems. Then, I'd research technologies that meet those requirements. Next, I would compare costs and expected ROI. Gathering input from the team and stakeholders would be essential, and finally, I would advocate for a pilot test to ensure the chosen technology performs well in practice.
How would you perform a risk assessment for a new bioprocess development project?
How to Answer
- 1
Identify potential risks in the bioprocess such as equipment failure or contamination.
- 2
Evaluate the likelihood and impact of each risk on project objectives.
- 3
Develop mitigation strategies for high-impact or high-likelihood risks.
- 4
Involve cross-functional teams for diverse insights on risk factors.
- 5
Document all findings and review them regularly throughout the project.
Example Answers
I would start by identifying key risks like contamination and equipment reliability, assessing how likely they are to happen and their potential impact on product quality. Next, I'd create mitigation plans for the top risks, involving team input to ensure we cover all angles. Finally, I'd keep a detailed log of risks and review them regularly throughout the bioprocess development.
Process Engineer Position Details
Salary Information
Average Salary
$94,125
Source: Indeed
Recommended Job Boards
CareerBuilder
www.careerbuilder.com/jobs/process-engineerZipRecruiter
www.ziprecruiter.com/Jobs/Process-EngineerThese job boards are ranked by relevance for this position.
Related Positions
Good Candidates Answer Questions. Great Ones Win Offers.
Master your interview answers under pressure
Boost your confidence with real-time practice
Speak clearly and impress hiring managers
Get hired faster with focused preparation
Used by thousands of successful candidates
Good Candidates Answer Questions. Great Ones Win Offers.
Master your interview answers under pressure
Boost your confidence with real-time practice
Speak clearly and impress hiring managers
Get hired faster with focused preparation
Used by thousands of successful candidates