Top 32 Production Supervisor Interview Questions and Answers [Updated 2025]
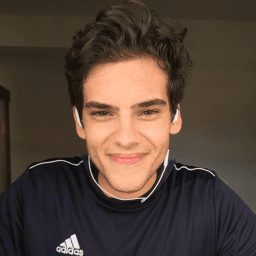
Andre Mendes
•
March 30, 2025
Navigating the competitive landscape of production supervision requires more than just technical expertise—it demands strategic communication skills and leadership acumen. In this blog post, we delve into the most common interview questions for the 'Production Supervisor' role, providing not only example answers but also invaluable tips on how to answer effectively. Prepare to enhance your interview prowess and leave a lasting impression with confidence and clarity.
Download Production Supervisor Interview Questions in PDF
To make your preparation even more convenient, we've compiled all these top Production Supervisorinterview questions and answers into a handy PDF.
Click the button below to download the PDF and have easy access to these essential questions anytime, anywhere: