Top 30 Quality Control Chemist Interview Questions and Answers [Updated 2025]
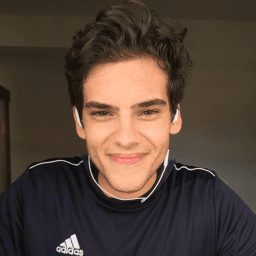
Andre Mendes
•
March 30, 2025
Are you preparing for a Quality Control Chemist interview and feeling unsure about what to expect? This blog post is your essential guide, featuring a curated selection of the most common interview questions for this crucial role. Alongside each question, you'll find example answers and expert tips on how to respond with confidence and clarity. Get ready to impress your interviewers and secure your dream job!
Download Quality Control Chemist Interview Questions in PDF
To make your preparation even more convenient, we've compiled all these top Quality Control Chemistinterview questions and answers into a handy PDF.
Click the button below to download the PDF and have easy access to these essential questions anytime, anywhere: