Top 31 Quality Control Inspector Interview Questions and Answers [Updated 2025]
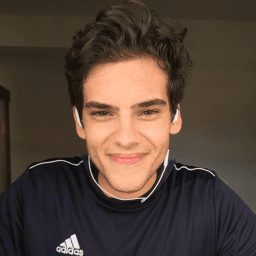
Andre Mendes
•
March 30, 2025
Navigating the interview process for a Quality Control Inspector role can be daunting, but preparation is key to success. This blog post compiles the most common interview questions you'll encounter, complete with example answers and expert tips on crafting effective responses. Whether you're a seasoned professional or new to the field, this guide will help you confidently tackle your next interview and demonstrate your expertise.
Download Quality Control Inspector Interview Questions in PDF
To make your preparation even more convenient, we've compiled all these top Quality Control Inspectorinterview questions and answers into a handy PDF.
Click the button below to download the PDF and have easy access to these essential questions anytime, anywhere: