Top 27 Quality Control Scientist Interview Questions and Answers [Updated 2025]
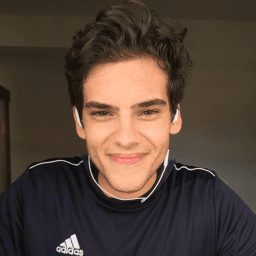
Andre Mendes
•
March 30, 2025
Preparing for a Quality Control Scientist interview can be daunting, but we're here to help you succeed. In this post, we've compiled the most common interview questions for this role, complete with example answers and practical tips on how to respond effectively. Whether you're a seasoned professional or new to the field, this guide will help you confidently tackle your next interview and impress potential employers.
Download Quality Control Scientist Interview Questions in PDF
To make your preparation even more convenient, we've compiled all these top Quality Control Scientistinterview questions and answers into a handy PDF.
Click the button below to download the PDF and have easy access to these essential questions anytime, anywhere:
List of Quality Control Scientist Interview Questions
Behavioral Interview Questions
Can you describe a time when you collaborated with a cross-functional team to improve product quality?
How to Answer
- 1
Identify a specific project where collaboration was key
- 2
Highlight your role and contributions to the team
- 3
Explain the challenges faced and how you overcame them
- 4
Share the outcome and any measurable improvements in quality
- 5
Mention any skills or tools you used during collaboration
Example Answers
In my last role, I worked with R&D and production teams to address high defect rates in a product line. I coordinated meetings to gather insights from both sides, which helped identify the root cause. We implemented new testing protocols that reduced defects by 30% over three months.
Tell me about a situation where you identified a significant quality issue. How did you handle it?
How to Answer
- 1
Start with the context of the situation.
- 2
Explain the quality issue clearly and what impact it had.
- 3
Describe the specific actions you took to address the issue.
- 4
Include the outcome of your actions, focusing on positive results.
- 5
Reflect on what you learned from the experience.
Example Answers
During a routine batch testing, I found that a series of samples had failed to meet the required purity standards, which could have affected patient safety. I immediately halted the batch and initiated an investigation. I coordinated with the production team to identify the source of contamination. After resolving the issue, I implemented additional purification checks to prevent future occurrences, resulting in improved quality assurance protocols. This experience taught me the importance of quick action and thorough follow-up.
Don't Just Read Quality Control Scientist Questions - Practice Answering Them!
Reading helps, but actual practice is what gets you hired. Our AI feedback system helps you improve your Quality Control Scientist interview answers in real-time.
Personalized feedback
Unlimited practice
Used by hundreds of successful candidates
Describe a time when you led a quality improvement project. What was the outcome?
How to Answer
- 1
Choose a specific project and explain your role clearly
- 2
Outline the problem you identified and the goals set for improvement
- 3
Describe the steps you took and the team dynamics involved
- 4
Highlight measurable results to demonstrate impact
- 5
Reflect on what you learned and how it informs your future work
Example Answers
In my previous role, I led a project to reduce product defects. I identified a pattern of errors in the final inspection process. I coordinated with team members to implement a new checklist, which decreased defects by 30% over three months. This experience taught me the importance of team collaboration and data analysis.
Give an example of when you had to adjust your quality control methods in response to new regulations.
How to Answer
- 1
Identify specific regulations that changed and when they were implemented.
- 2
Explain how you assessed the impact of these regulations on existing methods.
- 3
Describe the adjustments made to meet the new requirements.
- 4
Highlight any challenges faced and how you overcame them.
- 5
Mention the positive outcomes from implementing the changes.
Example Answers
When new FDA regulations were introduced for listeria testing, I revised our testing protocols. I assessed our previous methods and realized we needed more rigorous sanitation checks. We implemented weekly equipment audits and cross-training for staff. This led to a 30% reduction in contamination incidents over six months.
How have you effectively communicated quality standards to team members or stakeholders in the past?
How to Answer
- 1
Use specific examples of past communication methods.
- 2
Highlight your use of visual aids, such as charts or presentations.
- 3
Emphasize collaboration and feedback processes.
- 4
Mention any training sessions or workshops you led or participated in.
- 5
Discuss how you adjusted your communication style for different audiences.
Example Answers
In my last role, I created a clear presentation outlining quality standards for a new project and used visuals to engage the team. This led to an increase in compliance by 30%.
Can you provide an example of how your analytical skills contributed to a quality improvement?
How to Answer
- 1
Choose a specific project that involved quality control.
- 2
Highlight the analytical techniques you used, such as statistical analysis.
- 3
Quantify the improvement to demonstrate impact.
- 4
Explain how you communicated findings to the team.
- 5
Conclude with a reflection on the learning experience.
Example Answers
In my last role, I led a project analyzing product defect rates. Using statistical software, I identified a pattern in defects related to a specific supplier. After discussing my findings with the team, we switched suppliers, reducing defects by 30% in three months. This experience taught me the value of data-driven decisions.
Describe an instance where you and a colleague disagreed on a quality issue. How did you resolve it?
How to Answer
- 1
Identify the specific quality issue and your colleague's perspective.
- 2
Explain how you initiated a respectful conversation to discuss the disagreement.
- 3
Describe the steps you took to gather relevant data or evidence.
- 4
Share how you both compromised or found a common ground.
- 5
Conclude with the positive outcome for the project or team.
Example Answers
In a recent project, my colleague felt a product batch passed quality checks, but I believed there were inconsistencies. I arranged a meeting to discuss our viewpoints. We reviewed the data together, and after examining it, we agreed to repeat certain tests. This led to discovering a crucial defect. We then collaborated on improvements, ensuring better quality control going forward.
Tell me about a situation where your attention to detail prevented a potential quality failure.
How to Answer
- 1
Select a specific incident that highlights attention to detail
- 2
Clearly explain the context and your role in the situation
- 3
Describe the potential quality failure and its impact
- 4
Explain the specific action you took to prevent the failure
- 5
Conclude with the successful outcome and any lessons learned
Example Answers
In my previous role, I noticed a discrepancy in a batch report where the pH levels were slightly outside the acceptable range. I flagged the issue to the team, and we reanalyzed the samples, discovering an error in the calibration of our equipment. This prevented a major compliance issue and ensured product integrity.
Describe a time you introduced an innovative solution to improve quality control processes.
How to Answer
- 1
Identify a specific problem in quality control you faced.
- 2
Explain the innovative solution you proposed and why it was different.
- 3
Discuss the implementation steps you took to put the solution into action.
- 4
Share measurable outcomes or improvement metrics after implementing the solution.
- 5
Reflect on lessons learned or how this experience influenced future practices.
Example Answers
In my previous role, we struggled with high error rates in our product inspections. I proposed implementing a digital tracking system using barcode scanners to streamline data collection. After training the team, we saw inspection accuracy improve by 30% within three months, which reduced overall defects. This experience taught me the value of integrating technology into manual processes.
Technical Interview Questions
What quality control regulations and standards are you most familiar with, and how have you applied them in your work?
How to Answer
- 1
Identify key regulations like ISO 9001, GLP, or GMP relevant to your field.
- 2
Provide specific examples of how you've implemented these standards in your work.
- 3
Discuss the impact of your adherence to these standards on product quality or compliance.
- 4
Be prepared to explain any challenges you faced while applying these regulations.
- 5
Highlight your ongoing learning or training in quality control standards.
Example Answers
I am most familiar with ISO 9001 and GMP standards. In my previous role, I conducted internal audits to ensure compliance, which resulted in a 20% reduction in non-conformance incidents.
Explain the importance of measurement and testing methods used in quality control. What methods have you implemented?
How to Answer
- 1
Highlight how accurate measurements ensure product consistency and safety.
- 2
Discuss the role of testing in identifying defects before products reach customers.
- 3
Mention specific methods you've used, like statistical process control or Six Sigma.
- 4
Explain how these methods contribute to regulatory compliance and customer satisfaction.
- 5
Keep the answer focused on real-world applications and your hands-on experience.
Example Answers
Measurement and testing methods are crucial as they guarantee that products meet quality standards, ensuring safety and consistency. I've implemented statistical process control to monitor production processes, which has significantly reduced defects and improved customer satisfaction.
Don't Just Read Quality Control Scientist Questions - Practice Answering Them!
Reading helps, but actual practice is what gets you hired. Our AI feedback system helps you improve your Quality Control Scientist interview answers in real-time.
Personalized feedback
Unlimited practice
Used by hundreds of successful candidates
What statistical tools and techniques do you use for quality data analysis?
How to Answer
- 1
Mention specific statistical tools like SPSS, Minitab, or Python libraries.
- 2
Discuss techniques such as control charts, hypothesis testing, and regression analysis.
- 3
Highlight your experience in using these tools in real-world scenarios.
- 4
Emphasize your ability to interpret data results for actionable insights.
- 5
Show familiarity with data visualization for presenting findings.
Example Answers
I frequently use Minitab for control charts and hypothesis testing to analyze quality data, which helps me identify trends and variances effectively.
Can you describe your approach to conducting a root cause analysis for a quality failure?
How to Answer
- 1
Start with defining the problem clearly.
- 2
Gather data related to the quality failure.
- 3
Use tools like the 5 Whys or fishbone diagram for analysis.
- 4
Involve cross-functional teams for diverse insights.
- 5
Develop and implement corrective actions followed by monitoring.
Example Answers
I begin by clearly defining the quality failure, ensuring everyone has the same understanding. Then I gather relevant data from production logs and quality records. I typically use the 5 Whys technique to drill down to the root cause, often involving colleagues from production and engineering for different perspectives. After identifying the root cause, I propose and implement corrective actions, followed by a monitoring phase to ensure effectiveness.
What is your experience with process validation, and what steps do you follow?
How to Answer
- 1
Start with a brief overview of your experience in process validation.
- 2
Mention specific methodologies or techniques you have used.
- 3
Outline the steps you typically follow in a validation process.
- 4
Highlight any key projects or outcomes related to your experience.
- 5
Emphasize your attention to detail and compliance with regulations.
Example Answers
I have over three years of experience in process validation within the pharmaceutical industry. I primarily use the IQ, OQ, PQ method, where I first ensure equipment is installed correctly, then test operation, and finally verify product performance. In my last project, I reduced validation time by 15% while maintaining compliance.
What quality metrics do you believe are most critical to track, and why?
How to Answer
- 1
Identify key metrics relevant to the specific industry or product.
- 2
Emphasize metrics that impact customer satisfaction and compliance.
- 3
Discuss how metrics help in continuous improvement.
- 4
Include examples of metrics you have tracked in past roles.
- 5
Show awareness of both quantitative and qualitative metrics.
Example Answers
I believe defect density and first-pass yield are critical metrics. Defect density helps identify quality issues early, while first-pass yield shows efficiency in the production process. Tracking both can lead to improved customer satisfaction and reduced costs.
How do you troubleshoot issues in manufacturing processes from a quality perspective?
How to Answer
- 1
Identify specific symptoms or defects in the manufactured product
- 2
Gather data from various stages of production to locate the source of the issue
- 3
Engage cross-functional teams to gain insights and brainstorm solutions
- 4
Implement root cause analysis methods like Fishbone diagrams or Five Whys
- 5
Test and verify solutions to ensure they effectively resolve the issue
Example Answers
I start by pinpointing specific defects in the product, then I collect data across the manufacturing process to identify where things went wrong. I collaborate with production and engineering teams to understand different perspectives and apply root cause analysis techniques to develop a targeted solution.
What quality control software or tools are you experienced in using, and how have they helped your work?
How to Answer
- 1
Identify specific software or tools, such as LIMS or statistical analysis software.
- 2
Briefly describe how you used each tool in your role.
- 3
Highlight the impact on your work, like improving accuracy or efficiency.
- 4
Be prepared to discuss any challenges faced with these tools.
- 5
Mention any certifications or training relevant to the software.
Example Answers
I have experience with LabWare LIMS, which I used to streamline sample tracking and data management. This improved our turnaround time by 20%, allowing for quicker decision-making in product release.
Can you walk me through your experience with internal or external audits in a quality control context?
How to Answer
- 1
Start with your role and the purpose of the audit.
- 2
Explain the audit process and your specific responsibilities.
- 3
Highlight key findings and any corrective actions taken.
- 4
Discuss the impact of the audit on quality control practices.
- 5
Mention any follow-up or continuous improvement initiatives.
Example Answers
In my previous role as a Quality Control Scientist, I participated in internal audits aimed at ensuring compliance with ISO standards. I was responsible for reviewing documentation and conducting performance tests. One audit revealed inconsistencies in procedure documentation, leading to a corrective action plan that improved our SOPs, ultimately enhancing our product quality.
Situational Interview Questions
If you were to discover a batch failure in production, what immediate actions would you take?
How to Answer
- 1
Immediately halt the production line to prevent further affected batches.
- 2
Conduct a preliminary assessment to identify the nature of the failure.
- 3
Notify relevant stakeholders, including production and quality assurance teams.
- 4
Document all findings and the steps taken for transparency and accountability.
- 5
Evaluate potential impacts on product safety and compliance.
Example Answers
First, I would stop the production line to prevent any further issues. Then, I'd assess the batch to understand what went wrong, ensuring I keep stakeholders informed. I'd document everything for future reference and compliance checks.
Don't Just Read Quality Control Scientist Questions - Practice Answering Them!
Reading helps, but actual practice is what gets you hired. Our AI feedback system helps you improve your Quality Control Scientist interview answers in real-time.
Personalized feedback
Unlimited practice
Used by hundreds of successful candidates
If a new team member does not understand quality control protocols, how would you handle their training?
How to Answer
- 1
Assess their current knowledge and identify gaps
- 2
Provide hands-on training with real QC scenarios
- 3
Encourage questions and create an open dialogue
- 4
Offer written materials and resources for reference
- 5
Schedule regular check-ins to monitor progress
Example Answers
I would start by assessing their current understanding and pinpointing specific gaps. Then I'd provide hands-on training, using real-world examples. I would ensure they feel comfortable asking questions and supplement their learning with manuals or guides. Finally, I would check in with them regularly to track their progress.
In a situation where you have conflicting data regarding quality, how would you decide on the next steps?
How to Answer
- 1
Verify the accuracy of the conflicting data by cross-checking sources and methodologies
- 2
Consult with team members or experts to gain additional insights or clarify discrepancies
- 3
Conduct further testing or analysis to gather more data if necessary
- 4
Prioritize the most critical quality aspects that impact product safety or efficacy
- 5
Document your decision-making process for future reference and accountability
Example Answers
I would first verify the accuracy of the conflicting data by cross-referencing the sources. Then, I would consult with my team to discuss our findings and identify any potential oversight. If needed, I would conduct additional tests to clarify the issue before deciding on the necessary course of action.
How would you manage a significant change in your quality control process that is met with resistance from the team?
How to Answer
- 1
Communicate the rationale behind the change clearly.
- 2
Involve team members in the decision-making process.
- 3
Provide training and resources to ease the transition.
- 4
Acknowledge concerns and address them openly.
- 5
Celebrate small wins to build momentum and gain trust.
Example Answers
I would start by clearly explaining the reasons for the change and how it benefits the team. Then, I'd invite feedback and involve team members in the implementation process to give them a sense of ownership.
If faced with limited resources for quality control, how would you prioritize your efforts?
How to Answer
- 1
Identify the critical quality standards that impact safety and compliance
- 2
Focus on high-risk products or processes that have a history of issues
- 3
Use data analysis to target areas with the most significant quality failures
- 4
Collaborate with cross-functional teams to gather insights on priorities
- 5
Regularly review and adjust priorities based on resource changes and results
Example Answers
I would first pinpoint the quality standards that are essential for safety and compliance, then prioritize inspections on high-risk products known for past issues, using data to identify the most problematic areas.
How would you handle communication and collaboration with a production team that does not prioritize quality control?
How to Answer
- 1
Understand their perspective and challenges regarding production timelines.
- 2
Establish regular meetings to discuss quality metrics and issues.
- 3
Use data to demonstrate the benefits of quality control on overall production efficiency.
- 4
Foster a collaborative environment by involving them in quality-related decisions.
- 5
Acknowledge and celebrate improvements in quality to motivate teamwork.
Example Answers
I would start by understanding the production team's challenges, then schedule regular meetings to discuss how quality impacts our goals. By showing data on how prioritizing quality saves time and reduces waste, I aim to foster buy-in and collaboration.
What strategies would you use to engage stakeholders in quality improvement initiatives?
How to Answer
- 1
Identify key stakeholders and their interests early.
- 2
Develop a clear communication plan to share progress and updates.
- 3
Involve stakeholders in planning and decision-making processes.
- 4
Facilitate workshops or meetings to gather feedback and ideas.
- 5
Highlight the benefits of quality improvements to encourage participation.
Example Answers
I would first identify the key stakeholders and their specific interests to tailor my engagement. Then, I would create a clear communication plan to keep everyone updated on progress and achievements, making sure to invite them into workshops to brainstorm ideas and solutions together.
If a potential risk to product quality is identified late in the production process, what steps would you take?
How to Answer
- 1
Assess the risk's impact on product quality and identify the specific issue
- 2
Communicate immediately with team members and relevant stakeholders
- 3
Implement containment measures to stop the production process if necessary
- 4
Analyze root causes to prevent recurrence and suggest corrective actions
- 5
Document the incident thoroughly for compliance and future reference
Example Answers
First, I would assess how the identified risk impacts the overall product quality. Then, I would communicate with the production team to halt progress if necessary, ensuring no defective products are released. Afterward, I'd work on analyzing the root causes and propose corrective measures.
Quality Control Scientist Position Details
Recommended Job Boards
CareerBuilder
www.careerbuilder.com/jobs-quality-control-scientistThese job boards are ranked by relevance for this position.
Related Positions
- Food Safety Scientist
- Product Development Scientist
- Food Scientist
- Food Engineer
- Food Chemist
- Food Technologist
- Food Safety Auditor
- Enologist
- Research Chef
- Quality Control Engineer
Similar positions you might be interested in.
Ace Your Next Interview!
Practice with AI feedback & get hired faster
Personalized feedback
Used by hundreds of successful candidates
Ace Your Next Interview!
Practice with AI feedback & get hired faster
Personalized feedback
Used by hundreds of successful candidates