Top 29 Quality Control Engineer Interview Questions and Answers [Updated 2025]
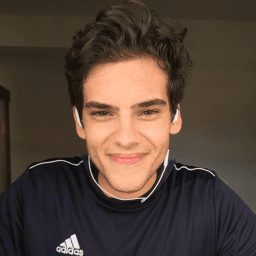
Andre Mendes
•
March 30, 2025
Preparing for a Quality Control Engineer interview can be daunting, but having the right resources can make all the difference. In this post, we delve into the most common interview questions for the role, offering insightful example answers and practical tips to help you respond effectively. Whether you're a seasoned professional or a newcomer, these insights will equip you to impress your interviewers and secure your dream job.
Download Quality Control Engineer Interview Questions in PDF
To make your preparation even more convenient, we've compiled all these top Quality Control Engineerinterview questions and answers into a handy PDF.
Click the button below to download the PDF and have easy access to these essential questions anytime, anywhere:
List of Quality Control Engineer Interview Questions
Situational Interview Questions
You are informed of an upcoming quality audit. How would you prepare your team and processes?
How to Answer
- 1
Review the previous audit findings and corrective actions.
- 2
Conduct a team meeting to communicate the audit scope and expectations.
- 3
Ensure all relevant documentation is up to date and accessible.
- 4
Perform a pre-audit check using a checklist of required standards.
- 5
Schedule practice sessions for the team to familiarize them with the audit process.
Example Answers
I would start by reviewing the last audit report to understand areas of concern. Then, I'd hold a meeting to discuss the upcoming audit and clarify roles. I'd ensure all documentation is current and hold a pre-audit check.
You discover that a batch of products does not meet quality standards right before a major delivery deadline. What steps would you take?
How to Answer
- 1
Assess the extent of the quality issue immediately
- 2
Communicate the problem to stakeholders and the team
- 3
Identify root causes of the quality failure quickly
- 4
Suggest immediate corrective actions to salvage the batch
- 5
Plan for preventive measures to avoid future issues
Example Answers
First, I would assess the severity and scope of the quality issue through quick inspections and testing. Then, I would inform the project manager and key stakeholders about the situation. Next, I would analyze the root cause by reviewing the production process and materials used. Depending on the findings, I would propose a solution, possibly reworking the batch if feasible. Finally, I would implement changes in our quality control protocols to prevent a recurrence of such an issue.
Don't Just Read Quality Control Engineer Questions - Practice Answering Them!
Reading helps, but actual practice is what gets you hired. Our AI feedback system helps you improve your Quality Control Engineer interview answers in real-time.
Personalized feedback
Unlimited practice
Used by hundreds of successful candidates
A customer reports a defect in a product. How would you go about investigating and resolving this issue?
How to Answer
- 1
Acknowledge the customer and thank them for reporting the issue
- 2
Gather detailed information about the defect from the customer
- 3
Review product specifications and quality standards to identify discrepancies
- 4
Conduct a root cause analysis to determine what went wrong
- 5
Implement corrective actions and communicate the resolution back to the customer
Example Answers
I would first thank the customer for bringing the defect to our attention. Then, I would ask for specific details about the issue, such as when it occurred and how it manifested. After gathering this information, I would examine the product specifications to see if it meets quality standards. Next, I would perform a root cause analysis and identify any potential causes. Finally, I would implement the necessary changes and inform the customer of the resolution.
If you notice a particular production process consistently produces defects, what actions would you take to improve it?
How to Answer
- 1
Identify the root cause of the defects using data analysis.
- 2
Implement immediate corrective actions to address the current issues.
- 3
Design and test a process improvement plan.
- 4
Train staff on the updated processes and quality standards.
- 5
Monitor the production process closely for ongoing issues and further refine the solution.
Example Answers
I would first analyze the defect data to pinpoint the root causes, then I would implement immediate corrections to the process. After that, I would design and test a more robust process improvement plan. I would also ensure that all staff are trained on the new procedures and continuously monitor the process to maintain quality.
Imagine you discover a critical defect in a product that has already been shipped. How would you handle the situation?
How to Answer
- 1
Assess the severity of the defect and its potential impact on customers
- 2
Notify your manager and relevant stakeholders immediately
- 3
Gather all available data and documentation related to the defect
- 4
Propose corrective actions and preventive measures to avoid future issues
- 5
Communicate transparently with affected customers, if necessary, about the defect
Example Answers
I would first assess how critical the defect is and determine its impact on users. Then, I would promptly notify my manager and any relevant stakeholders. I would collect all documentation related to the defect, including test results, and suggest corrective actions to address the issue. Finally, I would recommend communicating with affected customers to inform them about the defect and what we are doing to resolve it.
You have limited resources to conduct quality testing. How do you decide where to best allocate resources?
How to Answer
- 1
Identify critical areas that impact customer satisfaction the most
- 2
Use data from past quality issues to prioritize high-risk products or processes
- 3
Engage with stakeholders to understand their quality concerns and priorities
- 4
Implement a risk-based approach to allocate resources effectively
- 5
Consider the cost of failure in each area when making resource allocation decisions
Example Answers
I would start by analyzing data on previous quality failures to identify which products had the highest defect rates. Then, I would prioritize those areas for testing, as they pose the greatest risk to customer satisfaction. Additionally, I would consult with the production team to understand any ongoing concerns they have.
How would you go about assessing and selecting a vendor to ensure they meet quality standards?
How to Answer
- 1
Define clear quality criteria based on industry standards and company needs
- 2
Conduct a thorough review of vendor qualifications and certifications
- 3
Evaluate past performance and references from other clients
- 4
Perform on-site audits if possible to assess facilities and processes
- 5
Establish a trial period or initial project to assess vendor capabilities before full commitment
Example Answers
I would start by defining the quality standards we require based on industry benchmarks. Then, I would review the vendor's certifications and qualifications. After that, I would check their references and past performance. If necessary, I would conduct on-site audits to see their processes firsthand. Finally, I would consider a trial project to gauge their ability to meet our quality expectations.
How would you communicate a significant change in quality procedures to all stakeholders?
How to Answer
- 1
Identify all stakeholders affected by the change including team members, management, and suppliers.
- 2
Prepare a clear and concise message outlining the change and its impact.
- 3
Choose appropriate communication channels such as email, meetings, and presentations.
- 4
Provide supporting documentation and resources for further understanding.
- 5
Encourage feedback and questions to ensure comprehension and buy-in.
Example Answers
I would first identify all stakeholders involved and prepare a clear message explaining the change in quality procedures. Then, I would schedule a meeting to present the information, allowing for questions and feedback to ensure everyone understands the implications.
If a product's quality metrics are consistently just meeting the minimum standards, what strategies would you employ to drive improvement?
How to Answer
- 1
Analyze the current quality metrics to identify trends and patterns.
- 2
Engage with the production team to understand challenges affecting quality.
- 3
Implement a root cause analysis to identify underlying issues.
- 4
Set specific, measurable quality improvement goals and track progress.
- 5
Utilize customer feedback to prioritize areas for improvement.
Example Answers
I would start by analyzing the data to find any recurring issues in the quality metrics. Then, I'd collaborate with the production team to get their insights and identify any obstacles they face. After that, I would conduct a root cause analysis to pinpoint the main areas that need improvement. Finally, I would set clear improvement targets and measure our progress regularly.
Technical Interview Questions
Can you explain how you would use a Pareto chart in a quality control setting?
How to Answer
- 1
Define what a Pareto chart is and its purpose in quality control
- 2
Explain how to collect data for the chart, focusing on defects or issues
- 3
Describe the process of creating the chart, categorizing problems by frequency
- 4
Discuss how to analyze the chart to identify the most significant issues
- 5
Mention taking action based on the analysis to improve quality
Example Answers
A Pareto chart is a visual tool that helps identify the most common issues in a quality control process. I'd collect data on defects, categorize them, and then plot them in a chart to show which defects are most frequent. Analyzing this, I can focus efforts on the top issues to improve quality effectively.
What statistical methods do you use to monitor and improve quality control processes?
How to Answer
- 1
Focus on specific statistical methods you have used like SPC, control charts, and capability analysis.
- 2
Mention how you apply these methods in real-world scenarios to monitor product quality.
- 3
Include examples of outcomes or improvements resulting from these methods.
- 4
Discuss software tools you use for statistical analysis like Minitab or Excel.
- 5
Be prepared to explain why each method is valuable in quality control.
Example Answers
I regularly use Statistical Process Control (SPC) to monitor production processes through control charts. This allows me to identify variations and take corrective action promptly, improving overall quality.
Don't Just Read Quality Control Engineer Questions - Practice Answering Them!
Reading helps, but actual practice is what gets you hired. Our AI feedback system helps you improve your Quality Control Engineer interview answers in real-time.
Personalized feedback
Unlimited practice
Used by hundreds of successful candidates
Explain the principles of Six Sigma and how you have applied them in quality control.
How to Answer
- 1
Define Six Sigma and its goal of reducing defects.
- 2
Mention the DMAIC process (Define, Measure, Analyze, Improve, Control).
- 3
Speak about data-driven decision making.
- 4
Provide a specific example of using Six Sigma in your experience.
- 5
Highlight the impact of your actions on quality improvement.
Example Answers
Six Sigma is a methodology that aims to reduce defects and improve process quality. I followed the DMAIC process in my previous role, where I defined the problem of high defect rates in manufacturing, measured the current defects, analyzed root causes, improved processes by implementing better control measures, and established controls to sustain improvements. As a result, we reduced defects by 30%.
What are the key differences between destructive and non-destructive testing methods?
How to Answer
- 1
Define both destructive and non-destructive testing methods clearly.
- 2
Highlight the main characteristics of each testing method.
- 3
Discuss the typical applications of both methods.
- 4
Mention the advantages and disadvantages of each type.
- 5
Conclude with a summary of when to use each method.
Example Answers
Destructive testing involves testing methods that lead to the failure of the material, such as tensile tests. Non-destructive testing, on the other hand, allows inspections without causing damage, like ultrasound or X-ray tests. Destructive methods help determine material limits, while non-destructive methods are used for routine inspections.
What is the importance of ISO 9001 in quality control, and how have you ensured compliance in your previous roles?
How to Answer
- 1
Explain ISO 9001's role in ensuring consistent quality and customer satisfaction
- 2
Discuss specific quality control processes you've implemented to comply with ISO 9001
- 3
Mention how you trained team members on ISO 9001 standards
- 4
Provide examples of audits or assessments you've conducted to ensure compliance
- 5
Highlight improvements or success stories that resulted from ISO 9001 compliance
Example Answers
ISO 9001 is crucial because it provides a framework for maintaining quality standards and enhancing customer satisfaction. In my previous role, I led the implementation of a quality management system aligned with ISO 9001, which included regular audits and staff training to ensure everyone understood the standards. This compliance led to a 20% reduction in defects over six months.
What techniques do you apply when conducting a root cause analysis?
How to Answer
- 1
Use the 5 Whys technique to drill down to the root cause
- 2
Employ Fishbone diagrams to visualize potential causes
- 3
Collect data and evidence to support your findings
- 4
Involve team members for diverse perspectives
- 5
Document the process and follow up on implemented solutions
Example Answers
I typically start with the 5 Whys technique, asking 'Why?' sequentially to uncover the root cause. I also find Fishbone diagrams helpful for organizing thoughts and exploring different categories of potential causes.
How do control charts help in monitoring the stability and control of a process?
How to Answer
- 1
Define control charts and their purpose in quality control
- 2
Explain how control charts track process variation over time
- 3
Discuss the significance of control limits in identifying stability
- 4
Mention how control charts can signal when a process is out of control
- 5
Provide an example of a control chart application in a real-world scenario
Example Answers
Control charts are tools used in quality control to track the variation in a process over time. They help in identifying whether a process is stable and operating within control limits, indicating consistent quality. For example, if a control chart shows points outside the control limits, it signals that the process may be out of control and needs investigation.
Explain the concept of cost of quality and how it affects overall business performance.
How to Answer
- 1
Define cost of quality clearly, mentioning its components: prevention, appraisal, and failure costs.
- 2
Discuss how investing in quality can reduce failure costs and improve customer satisfaction.
- 3
Emphasize the long-term perspective of cost of quality on profitability and competitiveness.
- 4
Give an example of a business that improved its performance by managing its cost of quality effectively.
- 5
Keep the explanation concise and focus on the impact of quality on both costs and revenue.
Example Answers
Cost of quality refers to the total costs related to ensuring a product meets quality standards, including prevention, appraisal, and failure costs. By investing in prevention and appraisal, companies can significantly reduce failure costs, which leads to better customer satisfaction and increased profits.
What software tools have you used for data analysis in quality management?
How to Answer
- 1
Identify specific software tools you have used.
- 2
Mention your experience level with each tool.
- 3
Describe how you applied these tools in quality management tasks.
- 4
Highlight any relevant results or improvements from using these tools.
- 5
Connect your experience to the job you're applying for.
Example Answers
I have used Minitab and Excel extensively for data analysis in quality management. I am proficient in Minitab for performing statistical analyses and control charting, which helped reduce defects by 15% in my previous role. I also used Excel for tracking quality metrics and reporting, which streamlined our quality review process.
What is Failure Mode and Effects Analysis (FMEA), and how is it applied in quality control?
How to Answer
- 1
Define FMEA as a systematic method for evaluating processes to identify potential failure modes.
- 2
Explain its purpose in prioritizing risks based on the severity and likelihood of failures.
- 3
Mention the process of documenting and analyzing failures and their effects.
- 4
Highlight how FMEA helps in proactive problem-solving during product development.
- 5
Discuss its application in continuous improvement and ensuring quality standards.
Example Answers
FMEA, or Failure Mode and Effects Analysis, is a structured approach used to identify potential failures in a process. In quality control, we use FMEA to assess risks and prioritize them based on their impact and likelihood, allowing us to implement corrective actions more effectively.
Don't Just Read Quality Control Engineer Questions - Practice Answering Them!
Reading helps, but actual practice is what gets you hired. Our AI feedback system helps you improve your Quality Control Engineer interview answers in real-time.
Personalized feedback
Unlimited practice
Used by hundreds of successful candidates
Behavioral Interview Questions
Describe a time when you identified a significant quality issue in a project. How did you handle it?
How to Answer
- 1
Choose a specific example with clear context.
- 2
Outline the quality issue you found succinctly.
- 3
Explain the steps you took to address the issue.
- 4
Highlight the outcomes or improvements resulting from your actions.
- 5
Keep it concise, focusing on your role and contributions.
Example Answers
In a recent project, I noticed that the test results were inconsistent due to a bug in the testing process. I documented the issue and arranged a meeting with the development team. Together, we traced the problem and implemented a fix. This led to improved test accuracy and reduced rework time by 20%.
Can you provide an example of how you worked effectively within a cross-functional team to solve a quality-related problem?
How to Answer
- 1
Choose a specific project or situation where teamwork was essential.
- 2
Describe your role and contributions clearly.
- 3
Highlight how you communicated with other team members.
- 4
Mention the tools or methods you used to track progress and results.
- 5
Conclude with the positive outcome and what you learned.
Example Answers
In a project to launch a new product, I collaborated with design, production, and marketing teams. My role was to identify potential quality issues before the launch. I organized weekly meetings to discuss findings and used a shared tracking tool to manage feedback. This approach helped us identify a critical defect before production, resulting in a successful product release.
Don't Just Read Quality Control Engineer Questions - Practice Answering Them!
Reading helps, but actual practice is what gets you hired. Our AI feedback system helps you improve your Quality Control Engineer interview answers in real-time.
Personalized feedback
Unlimited practice
Used by hundreds of successful candidates
Tell me about a time when you disagreed with a coworker about a quality control process. How did you resolve the disagreement?
How to Answer
- 1
Start with a clear description of the situation.
- 2
Explain the specific disagreement and why it occurred.
- 3
Share the steps you took to address the disagreement.
- 4
Highlight the outcome and any lessons learned.
- 5
Keep your tone positive and collaborative.
Example Answers
In a previous role, I disagreed with a coworker on the use of a specific quality control software. I felt that a more manual approach was beneficial for our team. I initiated a meeting where we discussed the pros and cons of each method, encouraging input from other team members. Ultimately, we decided to pilot both approaches and review the results. This not only resolved our disagreement but also improved our process based on data.
Describe an instance where you had to implement a major change in quality control processes. How did you manage the transition?
How to Answer
- 1
Identify a specific change you implemented and reason behind it
- 2
Explain the steps taken to prepare for the change
- 3
Discuss how you communicated the change to the team
- 4
Highlight any tools or methodologies used during the transition
- 5
Share the results or impact of the change on the quality control process
Example Answers
In my previous role, I implemented a shift to a more data-driven quality control process by introducing statistical process control (SPC) tools. I prepared for this by conducting training sessions for the team, ensuring everyone understood the new methodologies. I communicated regularly through meetings and updates, which helped address concerns early. Ultimately, this shift reduced our defect rate by 15% over six months.
How have you led a team to meet a tight deadline while ensuring high quality standards?
How to Answer
- 1
Identify the specific project and deadline you faced.
- 2
Discuss the strategies you employed to prioritize tasks.
- 3
Explain how you ensured quality was maintained throughout.
- 4
Mention how you motivated and communicated with your team.
- 5
Share the positive outcomes and any metrics that demonstrate success.
Example Answers
In my last role, we had a tight deadline for a product launch. I quickly organized a kickoff meeting to prioritize tasks and assign responsibilities. We implemented daily check-ins to monitor progress and address any issues. I also made sure to emphasize quality by conducting regular quality reviews. As a result, we met the deadline and achieved a 98% approval rating from the client on the first batch.
Give an example of how you effectively managed multiple quality control projects at once.
How to Answer
- 1
Prioritize projects based on their deadlines and impact
- 2
Use project management tools to track progress
- 3
Hold regular status meetings with team members
- 4
Delegate tasks effectively to team members
- 5
Document processes and outcomes for future reference
Example Answers
In my previous role, I managed three quality control projects simultaneously by prioritizing them based on their impact and deadlines. I used a project management tool to keep track of each project's progress and held weekly meetings to ensure my team was on track.
Discuss a time when you implemented an innovative solution to a quality control issue.
How to Answer
- 1
Identify a specific quality control issue you faced.
- 2
Explain the innovative solution you developed.
- 3
Describe the process of implementation and any challenges encountered.
- 4
Highlight the outcomes and improvements resulting from your solution.
- 5
Emphasize teamwork and collaboration if applicable.
Example Answers
In my previous role, we faced high defect rates in our assembly line. I introduced a real-time monitoring system using sensors that tracked defects as they occurred. This allowed us to address issues immediately and reduced defects by 30% within three months. Collaboration with the IT team was key to making this happen.
Describe a situation where your attention to detail prevented a quality issue.
How to Answer
- 1
Think of a specific project where attention to detail was crucial.
- 2
Describe the quality issue that could have occurred if details were overlooked.
- 3
Explain the specific actions you took to ensure quality.
- 4
Highlight the positive outcome and any feedback you received.
- 5
Use metrics or results to demonstrate the impact of your actions.
Example Answers
In a recent project, I noticed discrepancies in the specification documents that could lead to incorrect product features. By cross-referencing the documents with customer requirements, I identified an error that would have caused a major delay. My thorough review led to correcting the specifications before production, saving us time and ensuring customer satisfaction.
How have you adapted to unexpected changes in the quality requirements of a project?
How to Answer
- 1
Use a specific example from a past project to illustrate your adaptability.
- 2
Describe the unexpected change and its impact on the project.
- 3
Explain the steps you took to reassess and implement the new requirements.
- 4
Highlight the positive outcome or lesson learned from the experience.
- 5
Keep your answer focused and relevant to quality control processes.
Example Answers
In my previous role, we suddenly needed to meet new regulatory standards for a product. I quickly gathered the team to analyze the changes and created a revised quality plan. By reallocating resources and conducting extra checks, we met the deadline and passed the audit with no issues.
Have you ever developed a training program for employees on quality standards? How did you ensure its effectiveness?
How to Answer
- 1
Describe the objectives of the training program
- 2
Mention the methods used to develop the program
- 3
Explain how you measured effectiveness
- 4
Include feedback mechanisms from participants
- 5
Share any specific improvements made based on feedback
Example Answers
I developed a training program focused on ISO 9001 standards. I first identified key areas employees needed to understand through surveys. Then, I created engaging materials and incorporated hands-on activities. To measure effectiveness, I used pre- and post-training assessments, which showed a 30% improvement in knowledge retention. After the first session, I gathered feedback which led me to adjust the content and format for future training.
Don't Just Read Quality Control Engineer Questions - Practice Answering Them!
Reading helps, but actual practice is what gets you hired. Our AI feedback system helps you improve your Quality Control Engineer interview answers in real-time.
Personalized feedback
Unlimited practice
Used by hundreds of successful candidates
Quality Control Engineer Position Details
Recommended Job Boards
CareerBuilder
www.careerbuilder.com/jobs/quality-control-engineerThese job boards are ranked by relevance for this position.
Related Positions
Ace Your Next Interview!
Practice with AI feedback & get hired faster
Personalized feedback
Used by hundreds of successful candidates
Ace Your Next Interview!
Practice with AI feedback & get hired faster
Personalized feedback
Used by hundreds of successful candidates