Top 29 Factory Engineer Interview Questions and Answers [Updated 2025]
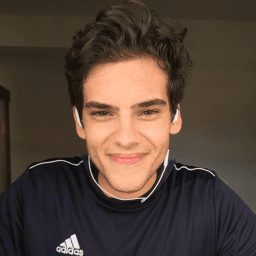
Andre Mendes
•
March 30, 2025
Preparing for a Factory Engineer interview can be daunting, but we've got you covered with this comprehensive guide. In this post, you'll find the most common interview questions for the Factory Engineer role, complete with example answers and insightful tips to help you respond effectively. Whether you're a seasoned professional or a newcomer to the field, these expert insights will equip you to impress your interviewers and secure the job.
Download Factory Engineer Interview Questions in PDF
To make your preparation even more convenient, we've compiled all these top Factory Engineerinterview questions and answers into a handy PDF.
Click the button below to download the PDF and have easy access to these essential questions anytime, anywhere:
List of Factory Engineer Interview Questions
Behavioral Interview Questions
Can you describe a time when you successfully solved a complex problem on the factory floor?
How to Answer
- 1
Use the STAR method: Situation, Task, Action, Result.
- 2
Start with a brief description of the problem you faced.
- 3
Clearly explain your role in addressing the problem.
- 4
Highlight specific actions you took and tools or methods you used.
- 5
Share the positive outcome and any metrics to back it up.
Example Answers
At my last job, we faced frequent machine breakdowns that slowed production. I noticed that the maintenance schedule was inconsistent. I took the initiative to implement a new preventive maintenance plan, which reduced downtime by 30% over the next three months.
Tell us about a time when you had to work closely with a team to implement a new process in the factory. How did you approach it and what was the outcome?
How to Answer
- 1
Select a specific example of a process implementation.
- 2
Describe your role clearly and how you collaborated with the team.
- 3
Focus on the steps you took to ensure effective communication and buy-in.
- 4
Highlight any challenges you faced and how you overcame them.
- 5
Conclude with the results and what you learned from the experience.
Example Answers
At my previous job, we needed to implement a new inventory tracking system. I organized a series of meetings to gather input from each team member. We created a shared document to outline responsibilities, which helped keep everyone aligned. After addressing some initial resistance, the team adapted well. The system reduced errors by 30% in the first month.
Good Candidates Answer Questions. Great Ones Win Offers.
Reading sample answers isn't enough. Top candidates practice speaking with confidence and clarity. Get real feedback, improve faster, and walk into your next interview ready to stand out.
Master your interview answers under pressure
Boost your confidence with real-time practice
Speak clearly and impress hiring managers
Get hired faster with focused preparation
Used by hundreds of successful candidates
Describe a situation where you disagreed with a colleague about an engineering decision. How did you resolve the conflict?
How to Answer
- 1
Focus on a specific instance that demonstrates teamwork.
- 2
Clearly explain the disagreement without assigning blame.
- 3
Highlight how you communicated your perspective respectfully.
- 4
Describe the resolution process, emphasizing collaboration.
- 5
Conclude with what was learned from the experience.
Example Answers
In a project to optimize a production line, I disagreed with a colleague who wanted to use a new, untested machine. I explained my concerns in a meeting, backing them up with data and examples. We decided to run a small pilot test before full implementation, which ultimately led to a successful outcome. We learned to value both caution and innovation.
Provide an example of a process improvement you implemented in a previous role. What were the results?
How to Answer
- 1
Choose a specific process improvement you led.
- 2
Describe the problem you identified and your rationale.
- 3
Explain the steps you took to implement the improvement.
- 4
Highlight measurable results or outcomes.
- 5
Use the STAR method to structure your response.
Example Answers
In my last position, we faced long lead times in our manufacturing process. I analyzed the workflow and identified bottlenecks. I proposed and implemented a new scheduling system that reduced idle times. As a result, we improved our lead times by 30%, which increased customer satisfaction.
Have you ever led a project that required coordination between different departments? How did you manage it?
How to Answer
- 1
Identify the project and its objectives clearly.
- 2
Explain the departments involved and their roles.
- 3
Describe the communication strategies used to keep everyone aligned.
- 4
Mention any challenges faced and how you resolved them.
- 5
Conclude with the outcomes and what was learned.
Example Answers
In my previous role, I led a project to streamline the production line. I coordinated with the engineering, quality assurance, and supply chain departments. I set up weekly meetings to ensure everyone was informed and could share updates. We faced a challenge with supply delays, which I managed by finding alternative suppliers. The project resulted in a 20% increase in efficiency.
Tell me about a time you introduced an innovative solution that significantly improved a process or resolved a long-standing issue in a factory.
How to Answer
- 1
Think of a specific example with measurable outcomes.
- 2
Describe the issue you faced and its impact on the factory.
- 3
Explain the innovative solution you proposed and implemented.
- 4
Highlight the results and improvements that followed.
- 5
Use the STAR method: Situation, Task, Action, Result.
Example Answers
In my previous role, we faced high downtime due to equipment failures (Situation). I was tasked with reducing downtime (Task). I researched and implemented a predictive maintenance system using IoT sensors which monitored equipment health (Action). As a result, we reduced downtime by 30% and saved the company $50,000 annually (Result).
Describe a complex engineering project you managed from start to finish. What were the biggest challenges and how did you overcome them?
How to Answer
- 1
Start with a brief overview of the project, including scope and objectives.
- 2
Identify the major challenges you faced during the project.
- 3
Explain the strategies you used to overcome each challenge.
- 4
Discuss the outcomes and what you learned from the experience.
- 5
Keep it concise but impactful, focusing on your role and contributions.
Example Answers
I managed a project to redesign a production line for increased efficiency. The main challenges were coordinating with multiple teams and ensuring minimal downtime. I facilitated regular meetings to maintain communication and implemented a phased rollout plan. This reduced downtime to 10%, and we increased productivity by 25%. I learned the importance of collaboration.
Give an example of how you communicated a technical issue to non-technical stakeholders effectively.
How to Answer
- 1
Identify the technical issue clearly and succinctly.
- 2
Use simple language and avoid jargon when explaining.
- 3
Relate the issue to its impact on the business or project goals.
- 4
Use visuals or analogies where possible to aid understanding.
- 5
Encourage questions to ensure comprehension and engagement.
Example Answers
In a recent project, we faced a software integration issue that affected our production timeline. I explained this to the management team using a simple diagram that illustrated the workflow impact. I highlighted how this delay could affect our delivery dates and customer satisfaction, which helped them understand the urgency.
Technical Interview Questions
What methods do you use to identify and optimize inefficient processes in a factory setting?
How to Answer
- 1
Analyze production data to pinpoint delays and bottlenecks.
- 2
Utilize value stream mapping to visualize process flow.
- 3
Conduct regular training sessions for staff on best practices.
- 4
Implement continuous improvement programs like Lean or Six Sigma.
- 5
Encourage feedback from operators for ground-level insights.
Example Answers
I analyze production data to find patterns in delays and bottlenecks. Then, I use value stream mapping to visualize and streamline the process flow. I also encourage operators to give feedback on inefficiencies they notice.
How do you approach integrating new automation technologies into existing manufacturing processes?
How to Answer
- 1
Assess current processes and identify areas for improvement
- 2
Research suitable automation technologies that fit existing workflows
- 3
Involve key stakeholders from different departments for input
- 4
Pilot the integration with a small-scale project before full deployment
- 5
Evaluate the results and adjust as necessary for optimization
Example Answers
I start by analyzing our current manufacturing processes to pinpoint inefficiencies. Then, I research automation options that could enhance productivity. Collaboration with team members is crucial, so I regularly engage with operations and IT to gather their insights. I would propose a pilot project to test the selected technology before a broader application, ensuring we can measure its impact accurately.
Good Candidates Answer Questions. Great Ones Win Offers.
Reading sample answers isn't enough. Top candidates practice speaking with confidence and clarity. Get real feedback, improve faster, and walk into your next interview ready to stand out.
Master your interview answers under pressure
Boost your confidence with real-time practice
Speak clearly and impress hiring managers
Get hired faster with focused preparation
Used by hundreds of successful candidates
Can you explain the steps you take to conduct a root cause analysis when there is a production line failure?
How to Answer
- 1
Define the problem clearly and gather data on the failure.
- 2
Use tools like the 5 Whys or Fishbone diagram to identify possible causes.
- 3
Evaluate each potential cause and gather evidence to support or refute them.
- 4
Identify the root cause and formulate an action plan to address it.
- 5
Implement the solution and monitor to ensure the issue does not recur.
Example Answers
First, I clearly define the problem by collecting data from the production line. Then, using the 5 Whys method, I dig deeper into potential causes. I evaluate each cause with evidence, identify the root cause, and develop an action plan to fix it. Finally, I implement the solution and monitor the line closely to ensure it remains effective.
What safety protocols do you typically implement to ensure a safe working environment on the factory floor?
How to Answer
- 1
Identify key safety protocols relevant to the factory environment
- 2
Mention specific training and education efforts for workers
- 3
Discuss regular safety audits and inspections
- 4
Include incident reporting procedures and their importance
- 5
Highlight the role of personal protective equipment (PPE) in safety plans
Example Answers
I implement key protocols such as regular safety audits, mandatory PPE usage, and comprehensive training for all employees to ensure they understand safety standards.
How do you apply Lean Manufacturing principles in your work as a factory engineer?
How to Answer
- 1
Identify key Lean principles like value stream mapping and waste reduction.
- 2
Provide specific examples from your past experiences.
- 3
Explain how you measure success, such as through reduced cycle time.
- 4
Discuss collaboration with teams to implement Lean processes.
- 5
Highlight continuous improvement efforts and employee engagement.
Example Answers
In my last role, I implemented value stream mapping to identify bottlenecks, which helped us reduce lead time by 20%.
How proficient are you with CAD software, and how do you use it in your engineering tasks?
How to Answer
- 1
Mention specific CAD software you have experience with, such as AutoCAD or SolidWorks.
- 2
Describe how you use CAD in your design processes, like creating models and simulations.
- 3
Talk about any projects where CAD played a critical role in your engineering work.
- 4
Include any relevant certifications or training related to CAD software.
- 5
Be confident in your ability to learn new CAD tools if needed.
Example Answers
I am highly proficient in AutoCAD and SolidWorks. I regularly use these tools to create 3D models for components and assemblies, which I've done for projects like redesigning our assembly line equipment.
What is your approach to developing maintenance schedules for factory equipment?
How to Answer
- 1
Assess equipment criticality and failure rates to prioritize maintenance tasks
- 2
Utilize manufacturer recommendations and historical data on equipment performance
- 3
Implement a predictive maintenance strategy using sensors and monitoring tools
- 4
Schedule regular reviews of the maintenance plan to adjust for new insights or changes
- 5
Collaborate with operators and technicians for a comprehensive view of equipment needs
Example Answers
I prioritize maintenance tasks by analyzing equipment criticality and historical failure rates. This helps to ensure that the most important machines receive attention first. I also refer to manufacturer's recommendations to set baseline schedules.
Describe your experience with process control systems in a manufacturing environment.
How to Answer
- 1
Identify specific systems you have worked with and their purpose.
- 2
Explain your role and contributions to those systems.
- 3
Mention any software or tools you used for process control.
- 4
Highlight any process improvements or efficiencies you achieved.
- 5
Discuss how you collaborated with other teams or departments.
Example Answers
In my last role, I worked with a SCADA system to monitor real-time production data. I was responsible for configuring alarms and optimizing system parameters to reduce downtime by 15%.
What industrial engineering techniques do you commonly utilize to improve factory productivity?
How to Answer
- 1
Identify specific techniques you have experience with such as Lean, Six Sigma, or Kaizen.
- 2
Provide examples of how you implemented these techniques to achieve measurable results.
- 3
Discuss any tools or software you used in the process.
- 4
Highlight collaboration with teams to ensure successful implementation.
- 5
Emphasize continuous improvement and adaptation based on data and feedback.
Example Answers
I often use Lean techniques to reduce waste on the production floor. For example, I implemented a Kanban system that improved inventory turnover by 30%.
How do you use data analysis to drive decision-making in a factory environment?
How to Answer
- 1
Identify key performance indicators relevant to factory operations.
- 2
Use statistical tools to analyze production data and identify trends.
- 3
Present data findings to stakeholders in a clear and actionable format.
- 4
Implement continuous monitoring systems for real-time analysis.
- 5
Make decisions based on data-driven insights rather than intuition.
Example Answers
In my previous role, I focused on key performance indicators like production rate and defect rate. I used statistical analysis to track these metrics weekly and identify trends, which helped us decrease defects by 15%.
Good Candidates Answer Questions. Great Ones Win Offers.
Reading sample answers isn't enough. Top candidates practice speaking with confidence and clarity. Get real feedback, improve faster, and walk into your next interview ready to stand out.
Master your interview answers under pressure
Boost your confidence with real-time practice
Speak clearly and impress hiring managers
Get hired faster with focused preparation
Used by hundreds of successful candidates
What strategies do you employ to ensure quality control in manufacturing processes?
How to Answer
- 1
Explain the use of statistical process control to monitor and control quality.
- 2
Describe regular audits and inspections throughout the manufacturing process.
- 3
Discuss the importance of employee training and engagement in quality standards.
- 4
Mention the implementation of standardized operating procedures (SOPs) to ensure consistency.
- 5
Highlight using feedback loops and continuous improvement methods like Six Sigma.
Example Answers
I utilize statistical process control methods to monitor production metrics in real-time. This allows us to detect variations early and take corrective actions immediately to maintain quality.
Situational Interview Questions
If a critical piece of machinery fails, how would you ensure minimal impact on production?
How to Answer
- 1
Identify the contingency plan for equipment failures
- 2
Communicate with the team to assess the situation
- 3
Arrange for immediate repairs or replacement parts
- 4
Implement backup systems to maintain production
- 5
Analyze the situation to prevent future failures
Example Answers
I would quickly activate our contingency plan, assess the damage with the team, and arrange for fast repairs or pull resources from other areas. Our backup systems would kick in to keep production flowing smoothly until the issue is resolved.
Imagine you are tasked with evaluating a new technology for potential implementation. How do you assess its feasibility?
How to Answer
- 1
Identify the specific requirements and objectives for the technology.
- 2
Conduct a cost-benefit analysis to understand financial implications.
- 3
Evaluate the technology against existing systems and processes.
- 4
Assess potential risks and challenges related to implementation.
- 5
Gather feedback from stakeholders who will be impacted by the change.
Example Answers
To assess the feasibility of a new technology, I would first define our specific needs and goals for its implementation. Then, I'd perform a cost-benefit analysis to ensure the investment aligns with our budget. Next, I would compare the new technology with our existing systems to evaluate compatibility. I would also identify potential risks, such as training requirements or disruptions to current operations, and gather input from team members to address their concerns.
Good Candidates Answer Questions. Great Ones Win Offers.
Reading sample answers isn't enough. Top candidates practice speaking with confidence and clarity. Get real feedback, improve faster, and walk into your next interview ready to stand out.
Master your interview answers under pressure
Boost your confidence with real-time practice
Speak clearly and impress hiring managers
Get hired faster with focused preparation
Used by hundreds of successful candidates
A safety hazard is detected in one of the production lines. How would you handle the situation?
How to Answer
- 1
Immediately assess the nature and severity of the hazard
- 2
Alert all affected personnel and stop the production line if necessary
- 3
Implement safety protocols and isolate the hazard area
- 4
Document the incident and report it to the safety manager
- 5
Investigate the cause and recommend measures to prevent future hazards
Example Answers
First, I would assess the hazard to determine its severity. If there's an immediate risk, I would stop the line and notify all personnel. Then, I would isolate the area to prevent accidents and document the incident. Lastly, I would work with the safety manager to investigate and suggest improvements.
You are asked to reduce production costs by 10% without compromising quality. What steps would you take?
How to Answer
- 1
Analyze current production processes for inefficiencies.
- 2
Implement lean manufacturing techniques to eliminate waste.
- 3
Negotiate with suppliers for lower material costs.
- 4
Invest in employee training to improve productivity.
- 5
Use data analytics to identify cost-saving opportunities.
Example Answers
I would start by analyzing the current processes to identify inefficiencies. Then, I'd implement lean techniques to reduce waste in production. Additionally, I would negotiate with our suppliers to secure better prices for raw materials.
How would you go about implementing a new production process that requires changes in several departments?
How to Answer
- 1
Identify the key stakeholders in each department and engage them early.
- 2
Map out the existing processes and pinpoint areas that need change.
- 3
Develop a clear communication plan outlining the benefits and reasons for the new process.
- 4
Provide training and support to those affected by the changes.
- 5
Establish metrics to measure the success of the new process post-implementation.
Example Answers
First, I would identify the key stakeholders in each department and hold meetings to gather their input. After understanding their concerns, I would map out current processes and highlight necessary changes. I would then communicate the benefits of the new process to everyone involved and provide training to ensure a smooth transition. Finally, I would set up metrics to track the process's success.
Your team is divided over the approach to a project. How would you facilitate a resolution?
How to Answer
- 1
Encourage open discussion to understand all viewpoints
- 2
Identify common goals shared by the team members
- 3
Facilitate a brainstorming session to explore solutions
- 4
Ask each member to suggest a compromise or alternative approach
- 5
Summarize the points made and guide towards a consensus
Example Answers
I would start by inviting everyone to express their thoughts in an open forum. Then, I would identify common goals to align the team. After that, we could brainstorm together to explore all possible solutions and work towards a compromise that everyone can support.
A batch of products failed quality control. How would you investigate and resolve the issue?
How to Answer
- 1
Review quality control reports to identify failure patterns
- 2
Inspect the batch to determine visible defects
- 3
Consult with team members involved in production for insights
- 4
Analyze the production process for any deviations
- 5
Implement corrective actions and retest the products
Example Answers
I would start by reviewing the quality control reports to see if there are any patterns in the failures. Next, I'd inspect the batch for any visible defects. Then, I would discuss with the production team to gather insights on anything that changed recently.
A sudden increase in demand requires a boost in production capacity. How would you address this challenge?
How to Answer
- 1
Assess current production capabilities and identify bottlenecks
- 2
Explore options for overtime or additional shifts with existing staff
- 3
Consider temporary hiring or outsourcing to meet short-term needs
- 4
Evaluate and streamline processes for efficiency gains
- 5
Implement plans for long-term capacity improvements if demand is sustained
Example Answers
First, I would analyze our production line metrics to pinpoint bottlenecks that can be optimized. Then, I would discuss with my team about implementing additional shifts or overtime to meet the immediate demand.
A key supplier fails to deliver parts on time. What steps would you take to mitigate the impact on production?
How to Answer
- 1
Communicate immediately with the supplier to understand the delay and timeline.
- 2
Assess the impact on production schedules and determine critical tasks affected.
- 3
Identify alternative suppliers or backup plans to source required parts.
- 4
Adjust production plans to prioritize tasks that do not require the delayed parts.
- 5
Keep all stakeholders informed about the situation and mitigation steps being taken.
Example Answers
I would first reach out to the supplier to get details on the delay and expected resolution. Then, I would evaluate which production schedules are impacted and look for alternative suppliers to fill the gap. Meanwhile, I'd adjust our production priorities to keep workflows moving as much as possible.
Factory Engineer Position Details
Recommended Job Boards
CareerBuilder
www.careerbuilder.com/jobs/factory-engineerZipRecruiter
www.ziprecruiter.com/Jobs/Factory-Engineer/These job boards are ranked by relevance for this position.
Related Positions
Good Candidates Answer Questions. Great Ones Win Offers.
Master your interview answers under pressure
Boost your confidence with real-time practice
Speak clearly and impress hiring managers
Get hired faster with focused preparation
Used by hundreds of successful candidates
Good Candidates Answer Questions. Great Ones Win Offers.
Master your interview answers under pressure
Boost your confidence with real-time practice
Speak clearly and impress hiring managers
Get hired faster with focused preparation
Used by hundreds of successful candidates