Top 29 Efficiency Engineer Interview Questions and Answers [Updated 2025]
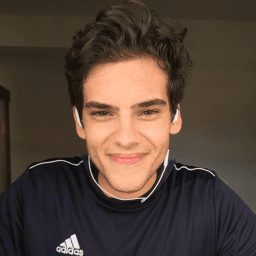
Andre Mendes
•
March 30, 2025
Are you preparing for an interview as an Efficiency Engineer? Our updated guide equips you with the most common interview questions for this crucial role, providing example answers and insightful tips to help you respond effectively. Dive into this post to enhance your interview skills, boost your confidence, and increase your chances of landing that coveted position. Let's get started on your path to success!
Download Efficiency Engineer Interview Questions in PDF
To make your preparation even more convenient, we've compiled all these top Efficiency Engineerinterview questions and answers into a handy PDF.
Click the button below to download the PDF and have easy access to these essential questions anytime, anywhere:
List of Efficiency Engineer Interview Questions
Technical Interview Questions
How do you apply operations management theories to improve efficiency in a production environment?
How to Answer
- 1
Identify key operations management theories relevant to production, such as Lean and Six Sigma.
- 2
Discuss specific tools or methodologies from these theories that you have used.
- 3
Provide a real-world example of a situation where you applied a theory to improve efficiency.
- 4
Quantify the results of your actions if possible, to show impact.
- 5
Emphasize continuous improvement and how you sustain efficiency gains.
Example Answers
In my previous role, I applied Lean principles to streamline our assembly line, reducing waste by reorganizing workflows. This resulted in a 20% reduction in production time.
What methodologies do you use to conduct process optimization, and can you explain one in detail?
How to Answer
- 1
Identify specific methodologies you are familiar with like Lean, Six Sigma, or Value Stream Mapping.
- 2
Choose one methodology to explain in detail with a relevant example from your experience.
- 3
Highlight the steps you took in the process, including any tools or metrics used.
- 4
Discuss the impact of the optimization on efficiency and results achieved.
- 5
Be clear and concise, focusing on how the methodology was applied practically.
Example Answers
I often use Lean methodology for process optimization. For example, in my previous role, I implemented a Lean approach to streamline our production line. I conducted value stream mapping to identify non-value-added activities, which led us to reduce cycle time by 20% and improve overall throughput.
Don't Just Read Efficiency Engineer Questions - Practice Answering Them!
Reading helps, but actual practice is what gets you hired. Our AI feedback system helps you improve your Efficiency Engineer interview answers in real-time.
Personalized feedback
Unlimited practice
Used by hundreds of successful candidates
What statistical methods are you familiar with for analyzing efficiency data? How do you choose the right one?
How to Answer
- 1
Identify commonly used statistical methods like regression analysis, ANOVA, and control charts.
- 2
Discuss how to select methods based on the type of data (continuous vs categorical) and the analysis goals.
- 3
Mention the importance of validating assumptions for each method you consider.
- 4
Be ready to provide an example of a situation where you applied a statistical method.
- 5
Explain how software tools can aid in performing these analyses efficiently.
Example Answers
I am familiar with regression analysis, which I use to determine relationships between variables related to efficiency. I choose this method when I have continuous data and want to predict outcomes based on input variables.
Can you explain the core principles of Lean Manufacturing and how you have applied them?
How to Answer
- 1
Start with defining Lean Manufacturing and its purpose.
- 2
List the core principles: value, value stream, flow, pull, and perfection.
- 3
Share a specific example from your past experience relating to these principles.
- 4
Be concise and focus on measurable outcomes of your application.
- 5
Use industry-relevant terminology to demonstrate your expertise.
Example Answers
Lean Manufacturing focuses on maximizing customer value while minimizing waste. The core principles include identifying value, mapping the value stream, ensuring continuous flow, using a pull system, and striving for perfection. In my previous role at XYZ Corp, I mapped our production process and identified bottlenecks, which reduced our cycle time by 15%.
What experience do you have with Six Sigma methodologies in improving process efficiency?
How to Answer
- 1
Identify specific projects where you applied Six Sigma methodologies.
- 2
Explain your role and the tools you used, such as DMAIC or DMADV.
- 3
Discuss measurable outcomes, like percentage reductions in waste or time.
- 4
Use examples that show teamwork and collaboration in process improvement.
- 5
Relate your experience to the company’s industry or specific challenges.
Example Answers
In my previous role, I led a project using the DMAIC framework to reduce cycle time in our manufacturing process. We achieved a 20% reduction in waste, resulting in significant cost savings.
What software tools do you typically use for efficiency analysis and process mapping?
How to Answer
- 1
Identify key software you have hands-on experience with.
- 2
Mention specific tools relevant to efficiency analysis and process mapping.
- 3
Explain how you use these tools to enhance processes.
- 4
Be prepared to discuss any metrics or outcomes from using the tools.
- 5
Tailor your answer to align with the job requirements.
Example Answers
I typically use Microsoft Visio for process mapping to visualize workflows, and I also utilize Tableau for data analysis to identify efficiency gaps.
How do you approach identifying and implementing automation opportunities in a manufacturing process?
How to Answer
- 1
Conduct a thorough analysis of the existing process to understand its inefficiencies.
- 2
Engage with operators and stakeholders to gather insights on pain points and repetitive tasks.
- 3
Research and evaluate potential automation technologies suitable for your process.
- 4
Pilot new automation solutions on a small scale to assess their impact before full implementation.
- 5
Establish metrics to measure the effectiveness of the automation and refine as necessary.
Example Answers
I start by analyzing the workflow to identify bottlenecks. Then, I consult with team members to pinpoint repetitive tasks. Based on this, I evaluate technologies like robotic process automation. I would pilot the best options in a controlled environment to see how they improve efficiency and track the results.
Describe a time when you used quantitative methods to assess and improve organizational processes.
How to Answer
- 1
Choose a specific project with measurable outcomes.
- 2
Explain the quantitative methods used, like data analysis or statistical tools.
- 3
Describe the problem you aimed to solve with data.
- 4
Highlight the results achieved through your improvements.
- 5
Emphasize how data-driven decisions impacted the organization.
Example Answers
In my previous role, I used a statistical analysis to identify bottlenecks in our manufacturing process. I collected cycle time data for each workstation and applied regression analysis to pinpoint inefficiencies. By optimizing the slowest stations, we reduced overall production time by 15%, which increased our output significantly.
How do you create and utilize value stream maps to identify waste in a process?
How to Answer
- 1
Identify the process to map and gather relevant data.
- 2
Use symbols to represent different elements of the process in the map.
- 3
Highlight steps that add value and those that do not.
- 4
Analyze the map to pinpoint waste such as delays and excess inventory.
- 5
Iterate on the map to formulate solutions for waste reduction.
Example Answers
I begin by selecting the specific process I want to analyze and gathering data regarding cycle times and work steps. Then, I create a value stream map using standard symbols to detail the process flow, distinguishing between value-adding and non-value-adding steps. This visual representation allows me to quickly identify bottlenecks and waste like unnecessary wait times, which I then target for improvement.
How do you approach optimizing logistics to reduce costs and improve delivery times?
How to Answer
- 1
Analyze current logistics processes to identify bottlenecks.
- 2
Utilize data analytics to forecast demand and optimize inventory.
- 3
Explore alternative shipping methods or carriers for better rates.
- 4
Implement just-in-time delivery to reduce storage costs.
- 5
Collaborate with suppliers to streamline processes and improve communication.
Example Answers
I start by analyzing the current logistics process to identify bottlenecks. For instance, in my last project, we found that our shipping schedules were not synchronized with production, which caused delays. I then used data analytics to better forecast demand and adjust our inventory accordingly.
Don't Just Read Efficiency Engineer Questions - Practice Answering Them!
Reading helps, but actual practice is what gets you hired. Our AI feedback system helps you improve your Efficiency Engineer interview answers in real-time.
Personalized feedback
Unlimited practice
Used by hundreds of successful candidates
Behavioral Interview Questions
Can you describe a time when you identified a significant inefficiency in a process and how you addressed it?
How to Answer
- 1
Choose a specific example from your experience.
- 2
Clearly explain the process you evaluated.
- 3
Detail the signs or metrics that indicated inefficiency.
- 4
Describe the solution you implemented and its impact.
- 5
Use quantifiable results to demonstrate improvements.
Example Answers
In my previous role, I noticed our inventory restocking process was causing delays. I tracked the order fulfillment times and found they were 30% longer than acceptable. I streamlined the process by consolidating supplier deliveries and optimized our storage layout. As a result, we reduced restocking time by 40%.
Tell us about a time when you worked with a team to improve operational efficiency. What was your role?
How to Answer
- 1
Choose a specific project where you contributed to efficiency gains
- 2
Clearly define your role and responsibilities in the team
- 3
Describe the actions taken to improve efficiency
- 4
Share measurable outcomes or results from the project
- 5
Reflect on what you learned from the experience
Example Answers
In my last position, we faced delays in our shipping process. I led a team to map out the workflow and identify bottlenecks. We implemented a new inventory tracking system that improved order processing time by 20%. This experience taught me the importance of data analysis in operational efficiency.
Don't Just Read Efficiency Engineer Questions - Practice Answering Them!
Reading helps, but actual practice is what gets you hired. Our AI feedback system helps you improve your Efficiency Engineer interview answers in real-time.
Personalized feedback
Unlimited practice
Used by hundreds of successful candidates
Describe a situation where you led an initiative to enhance efficiency in your department. What challenges did you face?
How to Answer
- 1
Choose a specific project or initiative that had measurable outcomes
- 2
Explain your role in leading the initiative clearly and confidently
- 3
Discuss specific challenges you encountered and how you addressed them
- 4
Highlight the results and improvements achieved due to your initiative
- 5
Reflect on any lessons learned and how they can apply to future projects
Example Answers
In my previous role, I led a project to optimize our supply chain process. We identified bottlenecks that were causing delays and implemented a new software system to track inventory. One major challenge was resistance from some team members who were hesitant to change. I organized training sessions to ease this transition. As a result, we improved our delivery time by 20%.
Give an example of a conflict that arose during a process optimization project and how you resolved it.
How to Answer
- 1
Identify a specific conflict related to roles or goals.
- 2
Explain the context of the project and the stakeholders involved.
- 3
Show how you facilitated communication between parties.
- 4
Describe the solution and the positive outcome achieved.
- 5
Highlight what you learned and how it improved future projects.
Example Answers
In a recent project, the engineering team wanted to streamline a process they felt was inefficient, but the operations team was concerned about potential disruptions. I organized a workshop where both teams presented their viewpoints. Through open discussion, we found a compromise that incorporated gradual changes, addressing operational concerns while still pursuing efficiency. The improved process saved time without significant disruption.
Tell me about a complex data analysis project you worked on to identify inefficiencies. What tools did you use?
How to Answer
- 1
Start with the scope and goal of the project.
- 2
Describe the data sources you used.
- 3
Mention specific tools and techniques you applied.
- 4
Highlight the outcome or findings you achieved.
- 5
Conclude with any impact this had on the organization.
Example Answers
In my last project, I analyzed manufacturing data to identify bottlenecks in production. I gathered data from our ERP system and used Python with Pandas for analysis. By visualizing the data with Tableau, I identified areas where downtime was occurring. This led to a 15% increase in efficiency in our assembly line operations.
Situational Interview Questions
You have identified multiple areas for improvement, but limited resources. How would you prioritize which projects to tackle?
How to Answer
- 1
Evaluate each project's potential impact on efficiency and cost savings.
- 2
Consider the resources required for each project and compare them.
- 3
Assess timelines for achieving results and prioritize quicker wins.
- 4
Engage stakeholders to understand their priorities and gain support.
- 5
Align projects with overall business goals to ensure strategic relevance.
Example Answers
I would start by assessing the potential impact of each project on our overall efficiency and cost savings. After identifying the top three projects with the highest impact, I would analyze the resources they require and compare them. Quick wins that can deliver results within a few months would be prioritized to showcase early successes to stakeholders.
How would you handle a situation where employees resist a new process you are trying to implement for better efficiency?
How to Answer
- 1
Listen to employee concerns and understand their resistance
- 2
Communicate the benefits of the new process clearly
- 3
Involve employees in the implementation to gain buy-in
- 4
Provide training and support to ease the transition
- 5
Use positive reinforcement to encourage adoption of the new process
Example Answers
I would first listen to the concerns of the employees to understand their perspective. Then, I'd clearly communicate the benefits of the new process, highlighting how it will make their work easier. I would also involve them in the implementation, asking for their input and feedback, which helps to gain their buy-in.
Don't Just Read Efficiency Engineer Questions - Practice Answering Them!
Reading helps, but actual practice is what gets you hired. Our AI feedback system helps you improve your Efficiency Engineer interview answers in real-time.
Personalized feedback
Unlimited practice
Used by hundreds of successful candidates
Suppose an efficiency project you implemented is not delivering the expected results. How do you proceed?
How to Answer
- 1
Analyze the current data to identify specific shortcomings
- 2
Engage with the team to gather feedback and insights
- 3
Adjust the project plan based on findings and team input
- 4
Test revised strategies on a small scale before full implementation
- 5
Communicate transparently with stakeholders about the changes
Example Answers
First, I would analyze the data to understand why the project is underperforming. After identifying specific issues, I would bring the team together to discuss their observations and gather insights. Based on this feedback, I would adjust our approach and test the new strategies on a smaller scale before rolling them out fully. I would also keep stakeholders informed throughout the process to ensure alignment.
How would you proceed if budget cuts limit your ability to implement your planned efficiency improvements?
How to Answer
- 1
Identify and prioritize critical efficiency projects.
- 2
Explore low-cost alternatives or methods to achieve similar results.
- 3
Engage cross-functional teams for creative solutions.
- 4
Leverage data to showcase the value of proposed changes.
- 5
Communicate transparently with stakeholders about constraints and options.
Example Answers
In light of budget cuts, I would first prioritize the efficiency projects with the highest impact and return on investment. Then, I would seek alternatives that require less funding, such as process adjustments rather than new technology.
You need to implement a process change that affects multiple departments. How would you manage the coordination?
How to Answer
- 1
Identify key stakeholders from each affected department
- 2
Establish a clear communication plan with regular updates
- 3
Create a timeline for the implementation phases
- 4
Facilitate cross-departmental meetings to gather feedback
- 5
Monitor progress and adapt the plan as necessary
Example Answers
First, I would identify key stakeholders in each department and invite them to a kick-off meeting. Next, I would set up a communication plan that includes weekly updates via email and monthly check-in meetings. I would also create a phased timeline for implementation, ensuring we allow time for feedback at every stage.
You have a critical deadline approaching for an efficiency project. However, unexpected issues arise. How do you manage it?
How to Answer
- 1
Assess the issues quickly to understand their impact on the project timelines
- 2
Prioritize the tasks based on urgency and importance to keep the project moving
- 3
Communicate openly with your team and stakeholders about the challenges and any changes
- 4
Consider reallocating resources or asking for additional support if necessary
- 5
Document the issues and resolutions for future reference and continuous improvement
Example Answers
I would first identify the critical issues and determine their impact on our deadline. Then, I'd prioritize the most urgent tasks and allocate team members accordingly. Open communication with the team and stakeholders would be key to manage expectations. If needed, I’d seek additional resources to stay on track. Lastly, I would ensure to capture lessons learned from this experience for future projects.
How do you continuously identify and implement small improvements in a stable operational process?
How to Answer
- 1
Engage with team members to gather feedback on pain points
- 2
Use data analysis to pinpoint inefficiencies
- 3
Establish regular review sessions to evaluate existing processes
- 4
Encourage a culture of experimentation for small changes
- 5
Document and share successful changes to replicate across processes
Example Answers
I regularly meet with my team to discuss any frustrations they face in our processes, which often leads to identifying small areas of improvement. For example, we discovered that a particular reporting tool was cumbersome, and after discussing alternatives, we switched to a more user-friendly platform, significantly reducing our processing time.
While planning a process change, you identify significant risk factors. How do you address these in your implementation plan?
How to Answer
- 1
Identify the specific risks associated with the process change
- 2
Prioritize risks based on their impact and likelihood
- 3
Develop mitigation strategies for each key risk
- 4
Include contingency plans in case risks materialize
- 5
Communicate the risks and plans to stakeholders clearly
Example Answers
I would first list the identified risks, such as potential delays or resource shortages. Next, I would assess which risks pose the greatest threat and focus on those. For each high-priority risk, I'd create a mitigation strategy, like securing backup resources. Additionally, I would have a contingency plan ready, and finally, communicate these risks and plans to all relevant stakeholders to ensure everyone is informed.
A proposed change to improve efficiency might negatively affect customer satisfaction. How do you handle this trade-off?
How to Answer
- 1
Assess the impact of the proposed change on both efficiency and customer satisfaction.
- 2
Engage stakeholders to gather feedback and understand customer priorities.
- 3
Explore alternative solutions that might balance efficiency and customer satisfaction.
- 4
Develop a plan to monitor impacts after implementation.
- 5
Communicate transparently with customers about the changes and their benefits.
Example Answers
I would first analyze the data to understand how the efficiency change impacts customer satisfaction. Then, I would involve stakeholders to discuss the trade-offs and explore alternatives. This way, we can find a solution that minimizes negative effects while still improving efficiency.
What strategies would you use to balance sustainability goals with efficiency improvements?
How to Answer
- 1
Identify key sustainability metrics relevant to the organization.
- 2
Analyze existing processes for inefficiencies that also impact sustainability.
- 3
Develop initiatives that improve efficiency while using sustainable resources.
- 4
Engage stakeholders to create buy-in for sustainability and efficiency objectives.
- 5
Monitor progress and adapt strategies based on results and feedback.
Example Answers
To balance sustainability and efficiency, I would first identify metrics such as energy consumption and waste reduction. Then, I would analyze our current processes to find areas where we could cut waste without sacrificing quality. For example, switching to energy-efficient machinery can reduce costs while lowering our carbon footprint.
Don't Just Read Efficiency Engineer Questions - Practice Answering Them!
Reading helps, but actual practice is what gets you hired. Our AI feedback system helps you improve your Efficiency Engineer interview answers in real-time.
Personalized feedback
Unlimited practice
Used by hundreds of successful candidates
You need to implement a new technology to enhance efficiency. How do you ensure a smooth transition?
How to Answer
- 1
Assess current processes to identify improvement areas
- 2
Involve stakeholders in planning and decision-making
- 3
Develop a clear implementation timeline with milestones
- 4
Provide thorough training for users on the new technology
- 5
Gather feedback during and after the transition for continuous improvement
Example Answers
First, I would analyze our existing processes to pinpoint exactly where we can improve efficiency. Then, I would engage stakeholders to ensure their needs and concerns are addressed in the planning phase. Next, I’d create a detailed timeline that includes training sessions and key milestones. Following the rollout, I’d actively seek feedback to make adjustments as necessary.
A stakeholder questions the data-driven recommendations you've made for process improvements. How do you handle their concerns?
How to Answer
- 1
Acknowledge their concerns to show you value their input
- 2
Present your data in a clear and understandable way
- 3
Explain the methodology used to arrive at your recommendations
- 4
Provide examples of past successes from similar recommendations
- 5
Invite further discussion to address any unresolved doubts
Example Answers
Thank you for your feedback. I understand your concerns. Let me clarify the data sources we used and how they lead to the proposed improvements. In the past, similar changes resulted in a 20% increase in efficiency, and I can share those case studies with you.
How would you adapt a successful efficiency strategy in one region to another with a different cultural work environment?
How to Answer
- 1
Research the cultural values and work ethics of the new region
- 2
Engage local stakeholders to understand their perspectives and needs
- 3
Customize the strategy to align with local practices and communication styles
- 4
Pilot the adapted strategy on a small scale before full implementation
- 5
Gather feedback and iterate on the strategy based on local responses
Example Answers
I would start by researching the local culture to understand work values. I'd involve local team leaders to discuss the original strategy and get their inputs on necessary adaptations. Then, I would implement a pilot program to test the changes and gather feedback before wider application.
A competitor introduces a more efficient process. How would you learn from and adapt to this change?
How to Answer
- 1
Research the competitor’s process to understand its efficiency gains.
- 2
Identify key performance indicators that the new process improves.
- 3
Engage with your team to brainstorm potential adaptations.
- 4
Propose pilot testing to evaluate the new methods in your context.
- 5
Continuously monitor results and iteratively refine the process.
Example Answers
I would analyze the competitor's process thoroughly to see what specific efficiencies they achieved. Then, I would assess our current process against those benchmarks and work with my team to adapt the most relevant aspects of their approach, starting with a small pilot program.
Efficiency Engineer Position Details
Recommended Job Boards
CareerBuilder
www.careerbuilder.com/jobs/efficiency-engineerZipRecruiter
www.ziprecruiter.com/Jobs/Efficiency-EngineerThese job boards are ranked by relevance for this position.
Related Positions
Ace Your Next Interview!
Practice with AI feedback & get hired faster
Personalized feedback
Used by hundreds of successful candidates
Ace Your Next Interview!
Practice with AI feedback & get hired faster
Personalized feedback
Used by hundreds of successful candidates