Top 30 Continuous Improvement Engineer Interview Questions and Answers [Updated 2025]
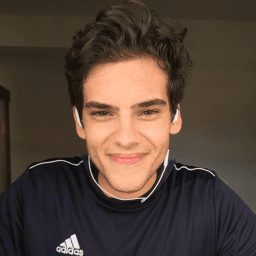
Andre Mendes
•
March 30, 2025
Are you gearing up for a Continuous Improvement Engineer interview? This blog post is your ultimate guide to navigating the most common questions you might encounter. We've compiled a comprehensive list of essential interview questions, complete with example answers and effective answering tips. Whether you're a seasoned professional or a newcomer to the field, this resource will help you confidently present your skills and knowledge.
Download Continuous Improvement Engineer Interview Questions in PDF
To make your preparation even more convenient, we've compiled all these top Continuous Improvement Engineerinterview questions and answers into a handy PDF.
Click the button below to download the PDF and have easy access to these essential questions anytime, anywhere:
List of Continuous Improvement Engineer Interview Questions
Behavioral Interview Questions
Can you describe a time when you identified a process improvement opportunity and successfully implemented it?
How to Answer
- 1
Think of a specific project where you noticed inefficiency.
- 2
Explain the steps you took to analyze the problem.
- 3
Highlight the solution you proposed and how it was implemented.
- 4
Share the results and any metrics that demonstrate the improvement.
- 5
Conclude with what you learned from the experience.
Example Answers
In my previous role, I noticed that our inventory tracking system was causing delays. I analyzed the process and discovered that manual entries were prone to errors. I proposed switching to an automated system, which I helped implement. As a result, our inventory accuracy improved by 30% and fulfillment times were reduced by 20%. I learned the importance of using data to drive decisions.
Tell me about a time when you led a cross-functional team to achieve a significant efficiency improvement.
How to Answer
- 1
Select a specific project where you led a diverse team.
- 2
Clearly describe the goal of the project and the efficiency improvement aimed for.
- 3
Detail your leadership role and how you facilitated collaboration.
- 4
Share the approach or strategies used to implement improvements.
- 5
Highlight the measurable results achieved as a consequence.
Example Answers
In my previous role at XYZ Corp, I led a cross-functional team to streamline our order processing system. Our goal was to reduce processing time by 30%. I organized weekly meetings where team members from IT, operations, and customer service collaborated to identify bottlenecks. By implementing a new software tool and redesigning workflows, we achieved a 40% reduction in processing time.
Don't Just Read Continuous Improvement Engineer Questions - Practice Answering Them!
Reading helps, but actual practice is what gets you hired. Our AI feedback system helps you improve your Continuous Improvement Engineer interview answers in real-time.
Personalized feedback
Unlimited practice
Used by hundreds of successful candidates
Can you give an example of how you fostered a culture of continuous improvement in a previous role?
How to Answer
- 1
Identify specific initiatives you led or participated in.
- 2
Describe how you engaged the team in improvement processes.
- 3
Highlight any tools or methodologies you used, like Lean or Six Sigma.
- 4
Mention measurable outcomes or results of the initiatives.
- 5
Emphasize the importance of feedback and open communication.
Example Answers
In my last role, I established a 'Kaizen' board where team members could submit improvement ideas. We held weekly meetings to discuss these suggestions, and by the end of the year, we implemented over 15 ideas that improved our process by reducing waste by 20%.
Describe a time when you worked with a team to solve a complex problem. What was your role?
How to Answer
- 1
Choose a specific example involving teamwork.
- 2
Clearly define the problem and its complexity.
- 3
Explain your individual contributions to the solution.
- 4
Highlight the results achieved as a team.
- 5
Focus on what you learned and how it applies to future challenges.
Example Answers
In a project to reduce production costs, our team faced unexpected delays. I facilitated brainstorming sessions and collected feedback. I proposed a lean approach that streamlined a key process, resulting in a 15% cost reduction.
Tell me about a creative solution you developed for a challenging process issue.
How to Answer
- 1
Identify a specific process issue you faced
- 2
Describe the creative solution you implemented
- 3
Highlight the impact of your solution and measurable results
- 4
Keep your answer concise and focused
- 5
Use the STAR method (Situation, Task, Action, Result) to structure your response
Example Answers
In my previous role, we faced high defect rates in our production line. I analyzed the data and noticed a pattern relating to operator training. I developed a new training program incorporating gamified learning to engage the team. After implementation, the defect rate dropped by 30% within three months.
Give an example of how you adapted to a major change in a process improvement project.
How to Answer
- 1
Identify a specific project that faced a major change.
- 2
Describe the nature of the change briefly.
- 3
Explain your initial response to the change.
- 4
Highlight the steps you took to adapt effectively.
- 5
Conclude with the positive outcomes from your adaptation.
Example Answers
In a project aimed at reducing cycle time, we unexpectedly shifted to a new software tool mid-project. I quickly organized a training session for the team and created guides to ease the transition. As a result, we adapted within two weeks and still met our timeline.
Describe a situation where you managed risks in a process improvement project.
How to Answer
- 1
Identify a specific project and provide context.
- 2
Discuss the risks you identified early in the project.
- 3
Explain the risk management strategies you implemented.
- 4
Highlight the outcome and improvements achieved.
- 5
Use quantifiable metrics to showcase success.
Example Answers
In a recent lean manufacturing project, I identified potential delays due to equipment failure. I implemented a predictive maintenance schedule and trained operators on quick fixes. This reduced downtime by 30% and ensured timely project completion.
Describe a time when you improved a process to enhance customer satisfaction.
How to Answer
- 1
Choose a specific example where you identified a process issue.
- 2
Explain the actions you took to analyze and improve the process.
- 3
Share the outcome and how it positively impacted customer satisfaction.
- 4
Use metrics or feedback to demonstrate success if possible.
- 5
Keep your answer focused on your role in the improvement process.
Example Answers
In my previous role, I noticed that customer complaints about order delays were increasing. I mapped the entire order fulfillment process and identified bottlenecks in the packaging stage. After implementing a new scheduling system for packers, order processing time improved by 30%. Customer feedback showed a 20% increase in satisfaction with delivery times.
Tell me about a successful collaboration with another department to improve a process.
How to Answer
- 1
Choose a specific project where collaboration was key
- 2
Mention the departments involved and their contributions
- 3
Describe the process that was improved and the results achieved
- 4
Use metrics or qualitative data to demonstrate success
- 5
Highlight your role and how you facilitated teamwork
Example Answers
In a project to reduce downtime on our assembly line, I collaborated with the maintenance and production teams. We implemented a scheduling system for routine maintenance that decreased downtime by 30%. My role was to gather data and facilitate meetings to ensure everyone was aligned.
Don't Just Read Continuous Improvement Engineer Questions - Practice Answering Them!
Reading helps, but actual practice is what gets you hired. Our AI feedback system helps you improve your Continuous Improvement Engineer interview answers in real-time.
Personalized feedback
Unlimited practice
Used by hundreds of successful candidates
Technical Interview Questions
What is the difference between Lean and Six Sigma, and how have you applied them in previous projects?
How to Answer
- 1
Define Lean as a methodology focused on waste reduction and efficiency.
- 2
Define Six Sigma as a data-driven approach aimed at reducing defects and improving quality.
- 3
Discuss a project where you utilized Lean concepts to streamline processes.
- 4
Discuss a project where you applied Six Sigma tools to analyze data and improve outcomes.
- 5
Highlight the combination of both methodologies for holistic improvement.
Example Answers
Lean focuses on removing waste to create value, while Six Sigma uses data to eliminate defects. In a previous project, I applied Lean principles to reduce cycle time by 30% by streamlining our production process. Additionally, I used Six Sigma tools to analyze quality data, which led to a 25% reduction in defects.
What tools and methods do you use for data analysis in process improvement?
How to Answer
- 1
Identify specific tools you have experience with, like Excel, Minitab, or Tableau.
- 2
Mention methods such as Six Sigma, DMAIC, or Lean.
- 3
Explain how you have applied these tools in real-world scenarios.
- 4
Highlight any software skills you have that support data visualization and analysis.
- 5
Focus on results: mention improvements or outcomes derived from your analysis.
Example Answers
I often use Excel for data manipulation and Minitab for statistical analysis. In my previous role, I applied the DMAIC method to improve a production line, resulting in a 20% increase in efficiency.
Don't Just Read Continuous Improvement Engineer Questions - Practice Answering Them!
Reading helps, but actual practice is what gets you hired. Our AI feedback system helps you improve your Continuous Improvement Engineer interview answers in real-time.
Personalized feedback
Unlimited practice
Used by hundreds of successful candidates
How do you apply Kaizen principles in process improvement projects?
How to Answer
- 1
Identify specific areas needing improvement using data analysis.
- 2
Engage team members in brainstorming sessions to gather insights.
- 3
Implement small, incremental changes and monitor their impact.
- 4
Regularly review the results and adjust processes accordingly.
- 5
Foster a culture of continuous feedback and learning.
Example Answers
In my last project, I analyzed production data to find bottlenecks. I organized a team meeting to discuss potential solutions. We implemented small changes, like adjusting shift schedules, which significantly reduced downtime. We monitored the results weekly and made further adjustments based on team feedback.
What techniques do you use to perform root cause analysis?
How to Answer
- 1
Start by mentioning specific techniques like 5 Whys or Fishbone Diagrams
- 2
Explain how you gather data and involve stakeholders
- 3
Emphasize the importance of validating root causes through testing
- 4
Discuss how you document findings for future reference
- 5
Mention how you implement solutions and monitor their effectiveness
Example Answers
I often use the 5 Whys technique to drill down to the root cause. For example, if there's a defect in a product, I would ask 'why' it happened multiple times until I discover the underlying issue. I also involve team members to get diverse insights.
What is value stream mapping, and how have you used it in process improvement?
How to Answer
- 1
Define value stream mapping clearly and succinctly.
- 2
Explain the purpose: to identify waste and improve process flow.
- 3
Share a specific example of a value stream mapping project you've led or been a part of.
- 4
Describe the tools or methods you used during the mapping.
- 5
Mention the results or improvements achieved from your mapping efforts.
Example Answers
Value stream mapping is a visual tool used to analyze and design the flow of materials and information required to bring a product to a customer. I used it to map the production process in my last job, which helped us identify bottlenecks and eliminate waste. As a result, we reduced lead time by 20%.
Which statistical tools are most effective for process improvement, and can you provide an example of their use?
How to Answer
- 1
Identify key statistical tools like Six Sigma, Control Charts, and Pareto Analysis.
- 2
Explain how each tool contributes to process improvement.
- 3
Provide concrete examples of how you've used these tools in past projects.
- 4
Be prepared to discuss outcomes and benefits realized from using these tools.
- 5
Tailor your examples to the industry of the company you're interviewing with.
Example Answers
One effective tool is Control Charts, which help monitor process stability. For instance, in a manufacturing project, I used Control Charts to analyze defect rates over time, which led to identifying a specific production line with high variability. After adjustments, we reduced defects by 30%.
How do you create a process map, and why is it important?
How to Answer
- 1
Identify the process you want to map and gather relevant information.
- 2
Engage with stakeholders to understand current steps and bottlenecks.
- 3
Use standard symbols like ovals for start/end and rectangles for processes to draw the map.
- 4
Review the draft with teams to verify accuracy and completeness.
- 5
Highlight areas of improvement or inefficiencies to emphasize importance.
Example Answers
To create a process map, I start by identifying the process and gathering all relevant details from stakeholders. I then draft the map using standard symbols, showing each step clearly. Finally, I review the map with the team to ensure everyone is on the same page and to identify improvement opportunities. It's crucial because it visually captures the process, making inefficiencies easier to spot.
Explain the PDCA cycle and provide an example of its application in process improvement.
How to Answer
- 1
Define each stage of the PDCA cycle: Plan, Do, Check, Act.
- 2
Provide a real-world example for each stage related to process improvement.
- 3
Keep the explanation concise and focused on a specific process.
- 4
Use clear terminology and avoid jargon for clarity.
- 5
Conclude with the results or benefits observed from the example.
Example Answers
The PDCA cycle consists of four stages: Plan where we identify a problem and develop a strategy, Do where we implement the plan on a small scale, Check where we review the results and collect data, and Act where we standardize the successful strategy. For instance, in a manufacturing process, we identified defects in a production line (Plan), ran a small trial of a new quality check (Do), analyzed defect rates post-trial (Check), and then implemented the new check across the whole line (Act). This led to a 25% reduction in defects.
How do you use benchmarking in continuous improvement efforts?
How to Answer
- 1
Identify key metrics for benchmarking relevant to your industry
- 2
Select best-in-class organizations to compare against
- 3
Gather data through research or networking
- 4
Analyze gaps between your performance and benchmarks
- 5
Develop an action plan to bridge these gaps and improve
Example Answers
I use benchmarking by first identifying our key performance indicators and then researching industry leaders to understand how they achieve those metrics. This helps us identify areas for improvement.
Can you explain the 5 Whys technique and give an example of how you've used it?
How to Answer
- 1
Define the 5 Whys technique clearly and concisely.
- 2
Share a specific example demonstrating your use of the technique.
- 3
Outline the problem you faced, the initial why, and subsequent whys.
- 4
Highlight the root cause identified and any actions taken.
- 5
Keep your explanation straightforward and focused on results.
Example Answers
The 5 Whys technique is a method to explore the root cause of a problem by asking 'why' five times. For example, in a project, we had a delay in delivery. First, I asked why, and the answer was 'the supplier was late.' Then, I asked why again, 'the supplier faced production issues.' Continuing this, I discovered that the root cause was a lack of communication about our order size. We improved our communication process with suppliers, and on the next project, we delivered on time.
Don't Just Read Continuous Improvement Engineer Questions - Practice Answering Them!
Reading helps, but actual practice is what gets you hired. Our AI feedback system helps you improve your Continuous Improvement Engineer interview answers in real-time.
Personalized feedback
Unlimited practice
Used by hundreds of successful candidates
Situational Interview Questions
Imagine you propose a process change, but one of the department heads is resistant. How would you handle this situation?
How to Answer
- 1
Listen to the department head's concerns carefully.
- 2
Seek to understand their perspective and the reasons for their resistance.
- 3
Present data and evidence supporting the proposed change.
- 4
Collaborate to find a compromise or alternative that addresses their concerns.
- 5
Follow up after discussions to keep the lines of communication open.
Example Answers
I would start by listening to the department head's concerns to understand their viewpoint better. After that, I would present data highlighting the benefits of the process change and discuss how it aligns with our goals. If they're still resistant, I'd work with them to brainstorm a compromise solution that meets both our needs.
If a process is running over budget and time, what steps would you take to analyze and improve it?
How to Answer
- 1
Identify the key metrics that are exceeding expectations.
- 2
Conduct a root cause analysis to find underlying issues.
- 3
Engage with team members for insights on process inefficiencies.
- 4
Implement quick wins that can lead to immediate improvements.
- 5
Develop a plan with measurable goals to monitor progress.
Example Answers
First, I'd analyze the key performance indicators to pinpoint where costs and timelines are exceeding limits. Then, I'd carry out a root cause analysis, possibly using tools like the 5 Whys or Fishbone diagram, to identify the specific issues. I would involve the team to gather their input on what might be causing delays and waste. Next, I'd implement quick fixes to address those inefficiencies. Finally, I'd create a plan with clear metrics to track improvements over time.
Don't Just Read Continuous Improvement Engineer Questions - Practice Answering Them!
Reading helps, but actual practice is what gets you hired. Our AI feedback system helps you improve your Continuous Improvement Engineer interview answers in real-time.
Personalized feedback
Unlimited practice
Used by hundreds of successful candidates
You implement a new process, but initial results are not meeting expectations. What actions would you take?
How to Answer
- 1
Assess the data to identify why results are below expectations
- 2
Engage stakeholders to gather their feedback and insights
- 3
Conduct root cause analysis to pinpoint issues in the process
- 4
Adjust the process based on findings and re-implement
- 5
Monitor the revised process closely to ensure it meets goals
Example Answers
First, I would analyze the data from the new process to understand the specific areas where it is falling short. Then, I would meet with team members and stakeholders to gather their feedback. After identifying any root causes, I would make the necessary adjustments to the process and implement those changes. Finally, I would closely monitor the updated process to track improvements.
You have multiple process improvement projects to complete, but limited resources. How would you prioritize them?
How to Answer
- 1
Identify the impact of each project on overall business goals.
- 2
Evaluate the feasibility based on available resources and timelines.
- 3
Consider quick wins that can deliver immediate value.
- 4
Assess stakeholder urgency and their impact on project success.
- 5
Use a scoring system to rank projects objectively.
Example Answers
I would start by aligning each project with the company's strategic goals, focusing on those that have the highest potential impact. Then, I'd assess the resource availability and identify quick wins, which can be implemented faster for immediate benefit.
A process improvement project goes over budget. How do you address this with stakeholders?
How to Answer
- 1
Acknowledge the issue transparently and honestly.
- 2
Provide a clear explanation of why the budget was exceeded.
- 3
Present solutions or next steps to manage the situation.
- 4
Focus on how you will prevent this in the future.
- 5
Remain calm and maintain a collaborative tone with stakeholders.
Example Answers
I would first acknowledge that the project has gone over budget and explain the reasons, highlighting unexpected challenges. Then, I would present my proposed solutions to mitigate costs going forward and assure stakeholders that I am implementing checks to prevent this in future projects.
A supplier's product quality impacts your process efficiency. How do you manage this issue?
How to Answer
- 1
Identify the specific quality issues with the supplier's product.
- 2
Communicate openly with the supplier to address quality concerns.
- 3
Develop a plan for monitoring supplier quality metrics closely.
- 4
Consider alternative suppliers or additional quality checks if issues persist.
- 5
Engage cross-functional teams to improve overall process efficiency.
Example Answers
I start by analyzing the specific quality issues affecting our process. I then reach out to the supplier to discuss these concerns directly and work collaboratively to enhance their quality controls. Additionally, I monitor key quality metrics closely to ensure improvements are being made.
How would you engage stakeholders who have different priorities in a process improvement initiative?
How to Answer
- 1
Identify all stakeholders involved and understand their priorities.
- 2
Facilitate a workshop to discuss goals and concerns of each stakeholder.
- 3
Find common ground by aligning the initiative's benefits with stakeholder objectives.
- 4
Communicate regularly and transparently to keep everyone informed and engaged.
- 5
Encourage collaboration by creating cross-functional teams to address diverse perspectives.
Example Answers
I would start by mapping out all stakeholders and their priorities. Then, I would organize a workshop to allow everyone to express their views and find mutual goals. By aligning the initiative with shared benefits, we can foster cooperation and commitment across the board.
You realize a process improvement project is behind schedule. What steps do you take to address the delay?
How to Answer
- 1
Assess the current status of the project and identify the specific reasons for the delay
- 2
Communicate with the team to gather input and understand challenges
- 3
Realign resources and priorities to address the identified issues
- 4
Set a revised schedule with realistic milestones and checkpoints
- 5
Implement quick wins that can help get the project back on track
Example Answers
First, I assess the project to identify the root causes of the delay, like resource constraints or unclear objectives. Then, I meet with the team to discuss these findings and gather their insights. I realign our resources to tackle critical bottlenecks and set a new timeline with achievable deadlines. Lastly, I implement quick wins that can help us gain momentum again.
During the implementation phase, an unexpected issue arises. How do you handle it?
How to Answer
- 1
Stay calm and assess the situation quickly
- 2
Gather your team to discuss the issue
- 3
Identify the root cause of the problem
- 4
Develop a corrective action plan
- 5
Communicate changes and new actions clearly to all stakeholders
Example Answers
I would first take a moment to assess the issue calmly. Then, I'd gather the team to brainstorm potential causes and solutions. After pinpointing the root cause, I would draft a corrective action plan and communicate this to everyone involved to ensure alignment.
How would you establish performance metrics for a new process improvement project?
How to Answer
- 1
Identify key objectives for the improvement project
- 2
Define specific, measurable outcomes related to those objectives
- 3
Involve stakeholders to ensure metrics align with business goals
- 4
Utilize historical data to set benchmarks for performance
- 5
Plan for regular reviews and adjustments of the metrics
Example Answers
I would first identify the key objectives of the process improvement project, such as reducing cycle time or increasing quality. Then, I would define specific metrics like average cycle time in minutes and defect rate percentage. Stakeholder input would ensure these metrics meet the business goals. I would use past data to set benchmarks and plan regular reviews to adapt the metrics as needed.
Don't Just Read Continuous Improvement Engineer Questions - Practice Answering Them!
Reading helps, but actual practice is what gets you hired. Our AI feedback system helps you improve your Continuous Improvement Engineer interview answers in real-time.
Personalized feedback
Unlimited practice
Used by hundreds of successful candidates
Continuous Improvement Engineer Position Details
Recommended Job Boards
These job boards are ranked by relevance for this position.
Related Positions
Ace Your Next Interview!
Practice with AI feedback & get hired faster
Personalized feedback
Used by hundreds of successful candidates
Ace Your Next Interview!
Practice with AI feedback & get hired faster
Personalized feedback
Used by hundreds of successful candidates