Top 30 Quality Inspector Interview Questions and Answers [Updated 2025]
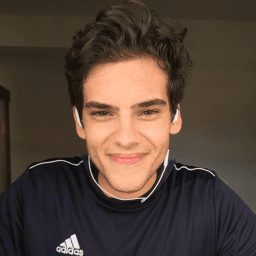
Andre Mendes
•
March 30, 2025
Navigating the interview process for a Quality Inspector position can be daunting, but preparation is key to success. In this blog post, we've compiled the most common interview questions for this crucial role, complete with example answers and valuable tips on how to respond effectively. Whether you're a seasoned professional or new to the field, these insights will help you shine in your next interview.
Download Quality Inspector Interview Questions in PDF
To make your preparation even more convenient, we've compiled all these top Quality Inspectorinterview questions and answers into a handy PDF.
Click the button below to download the PDF and have easy access to these essential questions anytime, anywhere: