Top 30 Refinery Operator Interview Questions and Answers [Updated 2025]
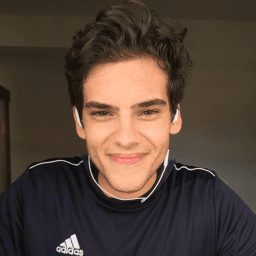
Andre Mendes
•
March 30, 2025
Preparing for a refinery operator interview can be daunting, but with the right guidance, you can excel. In this post, we present the most common interview questions for the refinery operator role, complete with example answers and expert tips to help you respond effectively. Whether you're a seasoned professional or a newcomer, these insights will boost your confidence and readiness for the big day.
Download Refinery Operator Interview Questions in PDF
To make your preparation even more convenient, we've compiled all these top Refinery Operatorinterview questions and answers into a handy PDF.
Click the button below to download the PDF and have easy access to these essential questions anytime, anywhere: