Top 30 Repair Technician Interview Questions and Answers [Updated 2025]
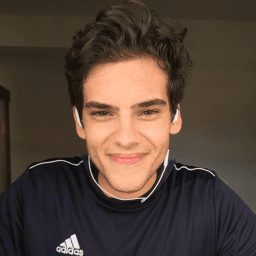
Andre Mendes
•
March 30, 2025
Preparing for a repair technician interview can be daunting, but we've got you covered with the most common questions you'll face. In this post, you'll find example answers and insightful tips to help you respond effectively and confidently. Whether you're a seasoned pro or entering the repair industry, this guide will equip you with the knowledge to impress potential employers and land your dream job.
Download Repair Technician Interview Questions in PDF
To make your preparation even more convenient, we've compiled all these top Repair Technicianinterview questions and answers into a handy PDF.
Click the button below to download the PDF and have easy access to these essential questions anytime, anywhere: