Top 31 Rewinder Interview Questions and Answers [Updated 2025]
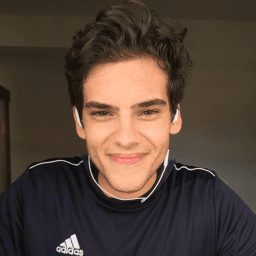
Andre Mendes
•
March 30, 2025
Navigating the interview process for a Rewinder position can be daunting, but preparation is key. In this blog post, we've compiled the most common Rewinder interview questions, complete with example answers and tips for responding effectively. Whether you're a seasoned professional or new to the field, this guide will help you articulate your skills and experience confidently, setting you up for success in your interview.
Download Rewinder Interview Questions in PDF
To make your preparation even more convenient, we've compiled all these top Rewinderinterview questions and answers into a handy PDF.
Click the button below to download the PDF and have easy access to these essential questions anytime, anywhere:
List of Rewinder Interview Questions
Behavioral Interview Questions
What steps have you taken in the past to ensure the quality of the products being rewound?
How to Answer
- 1
Explain your understanding of quality standards that apply to rewinding.
- 2
Describe specific procedures you followed during the rewinding process.
- 3
Mention tools or equipment you used to monitor quality.
- 4
Share how you addressed any quality issues that arose.
- 5
Highlight any training or protocols you have implemented.
Example Answers
I always followed the established quality standards by checking each product for proper alignment before rewinding and using calibration tools to ensure tension was correct.
Can you describe a time when you had to solve a problem related to the rewinding process?
How to Answer
- 1
Identify a specific problem you faced in the rewinding process.
- 2
Describe the steps you took to analyze the issue.
- 3
Explain the solution you implemented and the reasoning behind it.
- 4
Provide measurable results that demonstrate the success of your solution.
- 5
Reflect on what you learned from the experience and how it could apply to future situations.
Example Answers
In my previous position, we faced frequent jams during the rewinding process. I analyzed the machine settings and noticed misalignments. I recalibrated the setup and adjusted the tension. As a result, we reduced jams by 30% and increased productivity.
Don't Just Read Rewinder Questions - Practice Answering Them!
Reading helps, but actual practice is what gets you hired. Our AI feedback system helps you improve your Rewinder interview answers in real-time.
Personalized feedback
Unlimited practice
Used by hundreds of successful candidates
Tell me about a time you collaborated with a team to improve the rewinding efficiency.
How to Answer
- 1
Start with a specific project or situation.
- 2
Describe your role in the teamwork.
- 3
Explain the process you followed to identify inefficiencies.
- 4
Mention tools or strategies used to boost efficiency.
- 5
Conclude with the measurable outcomes or improvements.
Example Answers
In my last job, we worked on a project where we noticed rewinding took longer than expected. I led a team to analyze the workflow using a time tracking tool, and we identified bottlenecks in material handling. After reorganizing the layout and streamlining communication, we reduced rewinding time by 20%.
Describe a situation where you had to adapt to changes in production requirements.
How to Answer
- 1
Think of a specific project or task where requirements changed.
- 2
Explain the context and why the changes occurred.
- 3
Detail the steps you took to adapt effectively.
- 4
Highlight any positive outcomes or lessons learned.
- 5
Keep your answer structured: situation, action, result.
Example Answers
In my last project, we received new production targets due to a sudden increase in demand. I organized a team meeting to discuss the changes and reassigned tasks based on our strengths. We managed to meet the new deadline ahead of schedule, which boosted team morale and client satisfaction.
Have you ever encountered a safety issue while operating rewinding machinery? How did you handle it?
How to Answer
- 1
Describe a specific safety issue you faced
- 2
Explain the immediate actions you took to address the issue
- 3
Highlight any safety protocols you followed
- 4
Discuss the outcome of your actions
- 5
Mention any lessons learned or changes made afterward
Example Answers
I encountered a situation where a safety guard was missing from the rewinding machine. I immediately stopped the machine and reported the issue to my supervisor. We followed the safety protocol to evaluate the situation and made sure the machine was safe before any further operation. This incident reminded us to regularly inspect equipment to prevent similar issues.
Can you give an example of how you handled receiving constructive criticism about your work?
How to Answer
- 1
Acknowledge the criticism without defensiveness
- 2
Express appreciation for the feedback
- 3
Explain the specific steps you took to address the feedback
- 4
Highlight the positive outcome of implementing the change
- 5
Keep it concise and focused on a single example
Example Answers
When I received feedback that my reports were too lengthy, I thanked my manager for the input and worked on condensing my writing. I started using bullet points and tables, which helped improve clarity. The next report received positive feedback for its brevity and effectiveness.
Have you ever trained someone on how to operate a rewinding machine? How did you approach it?
How to Answer
- 1
Describe the specific steps you took during the training process
- 2
Mention how you assessed the person's current skill level
- 3
Include any methods you used to simplify complex tasks
- 4
Highlight the importance of safety and precision in your training
- 5
Share feedback mechanisms you implemented for continuous improvement
Example Answers
I trained a new employee by first assessing their understanding of the rewinding machine. I started with a thorough demonstration, breaking down each step and highlighting safety protocols. Then, I had them practice under supervision, providing real-time feedback until they were comfortable operating the machine independently.
Describe a time when you had to learn a new skill quickly to perform your job effectively.
How to Answer
- 1
Select a specific instance that showcases a skill relevant to the job.
- 2
Explain how the need to learn arose and the urgency involved.
- 3
Describe the methods you used to learn the new skill quickly.
- 4
Emphasize the positive outcomes of your quick learning.
- 5
Reflect briefly on what you learned from the experience.
Example Answers
In my previous job, I had to quickly learn a new project management tool due to an unexpected team shift. I dedicated one weekend to complete the online tutorials and practice using the software. Within a week, I was able to lead my project team using the tool effectively, enhancing our productivity. This experience taught me the importance of adaptability in a fast-paced environment.
Can you provide an example of when you took the initiative to improve a process in your workplace?
How to Answer
- 1
Identify a specific process you enhanced.
- 2
Explain the problem with the original process.
- 3
Describe the action you took to improve it.
- 4
Share the positive outcome of your initiative.
- 5
Keep the example relevant to the role of a Rewinder.
Example Answers
At my previous job, the packaging process for products was slow and caused delays. I noticed that we could save time by reorganizing the workspace for better flow. I rearranged the tables and tools used in the process. This change cut down our packaging time by 20%, which helped us meet our shipping deadlines.
Don't Just Read Rewinder Questions - Practice Answering Them!
Reading helps, but actual practice is what gets you hired. Our AI feedback system helps you improve your Rewinder interview answers in real-time.
Personalized feedback
Unlimited practice
Used by hundreds of successful candidates
Technical Interview Questions
What types of rewinding equipment are you familiar with?
How to Answer
- 1
List specific types of rewinding equipment you have experience with
- 2
Include any relevant brands or models if applicable
- 3
Mention the contexts or industries you've used these machines in
- 4
Be prepared to describe your hands-on experience with each type
- 5
Highlight any additional skills related to maintenance or troubleshooting
Example Answers
I have experience with automatic and manual rewinding machines, specifically the XYZ and ABC models used in textile manufacturing and printing. I've set them up, operated them, and performed routine maintenance.
Can you explain the basic principles of the rewinding process?
How to Answer
- 1
Start with the definition of rewinding in the context of the job.
- 2
Mention key components involved in the process, like the spool and tension.
- 3
Explain the importance of maintaining tension for quality.
- 4
Discuss typical materials that are rewound and their characteristics.
- 5
Conclude with an emphasis on safety and precision in the process.
Example Answers
Rewinding is the process of taking material from one spool and transferring it onto another, often with careful attention to tension to prevent damage. Key components include the spool and the mechanism used to manage tension. It's crucial to ensure that the material maintains uniform tension throughout to achieve a high-quality end product.
Don't Just Read Rewinder Questions - Practice Answering Them!
Reading helps, but actual practice is what gets you hired. Our AI feedback system helps you improve your Rewinder interview answers in real-time.
Personalized feedback
Unlimited practice
Used by hundreds of successful candidates
What maintenance procedures do you perform regularly on rewinding equipment?
How to Answer
- 1
Identify key maintenance tasks like cleaning and lubrication.
- 2
Mention the importance of inspection for wear and tear.
- 3
Include specific schedules, such as daily or weekly tasks.
- 4
Discuss any checks on electrical components and safety features.
- 5
Highlight the importance of keeping a maintenance log.
Example Answers
I regularly clean the rollers and guides at the beginning of each shift, lubricate moving parts weekly, and inspect the tension controls daily for any signs of wear.
How would you troubleshoot a malfunctioning rewinder?
How to Answer
- 1
Check for any visible obstructions or jams in the rewinder mechanism.
- 2
Verify that the rewinder is properly calibrated and set to the correct tension.
- 3
Inspect the motor and electrical components for signs of wear or damage.
- 4
Consult the machine's manual for troubleshooting steps and error codes.
- 5
Run a test reel to isolate whether the issue is mechanical or related to the material.
Example Answers
First, I would visually inspect the rewinder for any obstructions or jams. If everything looks clear, I'd then check the calibration settings to ensure it's set for the correct tension. If that's fine, I'd examine the motor and its connections for any faults. Finally, I'd refer to the manual for specific troubleshooting advice.
What types of materials are typically used in the rewinding process, and how do they affect operation?
How to Answer
- 1
Identify common materials like paper, plastic films, and metals used in rewinding.
- 2
Explain the characteristics of each material and its impact on performance.
- 3
Discuss how material thickness and flexibility influence the rewinding process.
- 4
Mention the importance of material compatibility with the machine and adhesive properties.
- 5
Consider how material properties affect waste, speed, and product quality.
Example Answers
In the rewinding process, common materials include paper, plastic films, and metals. Paper is often used for its ease of handling and cost-effectiveness, while plastic films are valued for their moisture resistance. The thickness and flexibility of these materials affect how they are handled during rewinding, impacting the speed and quality of the final product.
How do you measure the efficiency of your rewinding process?
How to Answer
- 1
Identify key performance indicators like speed and material waste.
- 2
Use time tracking to assess how long each rewind cycle takes.
- 3
Monitor machine downtime and setup times to find inefficiencies.
- 4
Implement regular quality checks to reduce rework rates.
- 5
Analyze feedback from operators to identify process improvements.
Example Answers
I measure efficiency by tracking the rewind cycle time and comparing it to our benchmarks. I also monitor material waste during the process to ensure we are minimizing losses.
How do you integrate the rewinding process with other production line activities?
How to Answer
- 1
Explain the importance of coordination between rewinding and other processes.
- 2
Mention the role of communication with team members during production.
- 3
Highlight the use of scheduling to ensure timely rewinding.
- 4
Discuss quality checks to ensure seamless integration.
- 5
Emphasize flexibility to adapt to production changes.
Example Answers
I integrate the rewinding process by coordinating closely with the cutting and packing teams. Clear communication helps us align schedules and avoid bottlenecks. I also implement quality checks to ensure smooth handoffs between functions.
What is the importance of calibrating a rewinder, and how is it done?
How to Answer
- 1
Explain calibration as crucial for accurate winding tension
- 2
Discuss the impact on product quality and consistency
- 3
Mention steps such as checking tension settings and alignment
- 4
Highlight tools used like tension meters and alignment gauges
- 5
Conclude with the frequency of calibration checks required
Example Answers
Calibrating a rewinder is essential because it ensures the proper tension during the winding process, which directly affects the quality of the final product. Calibration is done by first checking the tension settings with a meter, making adjustments as necessary, and ensuring the rollers and alignment are correct before starting production. Regular checks should be performed to maintain accuracy.
What safety standards do you follow while operating rewinding machinery?
How to Answer
- 1
Mention specific safety gear you wear, like gloves and goggles.
- 2
Talk about proper training and certifications you have received.
- 3
Explain procedures for machine lockout/tagout to prevent accidental starts.
- 4
Describe your routine checks for machine safety features before operation.
- 5
Emphasize adherence to workplace safety protocols and guidelines.
Example Answers
I always wear my safety goggles and gloves when operating the rewinding machine. I have completed safety training courses, and I ensure to use the lockout/tagout procedure before starting any maintenance work.
Are you familiar with any software used for monitoring production processes in rewinding?
How to Answer
- 1
Mention any specific software you have used in production environments.
- 2
Describe your experience with features that monitor or optimize processes.
- 3
Discuss how you have used data from software to make improvements.
- 4
If you haven't used specific software, express your willingness to learn.
- 5
Refer to any related skills or systems that provide a foundation for understanding.
Example Answers
Yes, I have experience with software like SAP and MES systems which help monitor production processes. I utilized their dashboard features to track efficiency and identify bottlenecks.
Don't Just Read Rewinder Questions - Practice Answering Them!
Reading helps, but actual practice is what gets you hired. Our AI feedback system helps you improve your Rewinder interview answers in real-time.
Personalized feedback
Unlimited practice
Used by hundreds of successful candidates
How do mechanical issues affect the rewinding process, and how can they be mitigated?
How to Answer
- 1
Identify common mechanical issues such as misalignment, tension problems, and blade wear.
- 2
Explain how these issues can lead to quality defects and production delays.
- 3
Suggest regular maintenance schedules to inspect and adjust equipment.
- 4
Discuss the importance of operator training to recognize and address problems early.
- 5
Consider implementing technology for monitoring equipment performance.
Example Answers
Mechanical issues like misalignment can cause uneven rewinding, leading to defects. Regularly checking alignment and ensuring equipment is properly calibrated can help mitigate this problem.
Situational Interview Questions
If you notice a co-worker consistently making the same error during rewinding, how would you approach the situation?
How to Answer
- 1
Observe the error and ensure you fully understand what is happening.
- 2
Choose a private setting to discuss the issue to avoid embarrassment.
- 3
Use 'I' statements to express your observations and concerns.
- 4
Offer to help them correct the mistake or suggest a solution.
- 5
Follow up later to see if they have improved or if they need further assistance.
Example Answers
I would first make sure that I fully understand the mistake they are making. Then, I would ask to speak with them privately, and I might say something like, 'I've noticed that you've been having some challenges with rewinding. Can we go over it together?' I would offer to assist if they need help.
Imagine you are behind schedule with your rewinding tasks. How would you prioritize your work?
How to Answer
- 1
Assess the most urgent tasks and their deadlines
- 2
Identify any tasks that have dependencies on others
- 3
Communicate with your team about your situation
- 4
Focus on high-impact tasks that will relieve bottlenecks
- 5
Use a time management technique like the Pomodoro method to stay focused
Example Answers
I would first assess which rewinding tasks are due soonest and prioritize those. I would also check if any tasks depend on my completion to help prioritize effectively. I would communicate with my supervisor to manage expectations and then structure my work in focused intervals to maximize productivity.
Don't Just Read Rewinder Questions - Practice Answering Them!
Reading helps, but actual practice is what gets you hired. Our AI feedback system helps you improve your Rewinder interview answers in real-time.
Personalized feedback
Unlimited practice
Used by hundreds of successful candidates
How would you handle a disagreement with a colleague about the correct way to operate a rewinder?
How to Answer
- 1
Listen actively to your colleague's perspective without interruption.
- 2
Ask clarifying questions to understand their viewpoint better.
- 3
Share your insights and reasoning calmly to explain your approach.
- 4
Suggest a practical test of both methods to see which works better.
- 5
Be open to compromise and working together to find the best solution.
Example Answers
I would start by listening to my colleague's method to fully understand their reasoning. Then, I would share my own approach, and we could discuss the pros and cons of each. If needed, we could run a small test using both methods to see which yields better results.
If you find a batch of rewound material does not meet quality standards, what steps would you take?
How to Answer
- 1
Assess the extent of the quality issue quickly.
- 2
Isolate the affected batch to prevent further use.
- 3
Document the quality issue and the specific flaws observed.
- 4
Notify the relevant teams or supervisors about the issue.
- 5
Suggest or implement corrective actions to resolve the problem.
Example Answers
First, I would quickly assess how significant the quality issue is. Then I would isolate the affected batch to ensure it doesn't get used. Next, I would document the specific flaws I found and notify my supervisor about the situation. Finally, I would work with the team to implement corrective actions to fix the issue.
You observe that the rewinding process is slower than expected. What actions would you take to improve it?
How to Answer
- 1
Identify bottlenecks in the process by monitoring the workflow
- 2
Communicate with team members to gather feedback on issues
- 3
Check equipment and tools for maintenance needs or malfunctions
- 4
Explore process optimization techniques such as re-arranging workstations
- 5
Implement small changes and measure impact to ensure improvement
Example Answers
I would first observe the rewinding process to identify any specific bottlenecks. Then I would talk to team members to hear their insights. Lastly, I would ensure that all equipment is functioning properly before making any changes.
If you notice another operator bypassing safety protocols, how would you respond?
How to Answer
- 1
Stay calm and assess the situation before reacting.
- 2
Prioritize safety and ensure no immediate danger is present.
- 3
Approach the colleague privately and discuss your concerns.
- 4
Remind them of the importance of safety protocols.
- 5
Report the incident if the behavior continues or poses a risk.
Example Answers
I would first ensure that there is no immediate risk before addressing the issue. Then, I would calmly speak to the operator privately to express my concern about bypassing safety protocols and remind them how crucial these measures are for everyone's safety.
What would you do if a fire alarm went off while you were operating a rewinding machine?
How to Answer
- 1
Stay calm and follow safety protocols.
- 2
Immediately stop the machine and ensure it is in a safe state.
- 3
Evacuate the area quickly and safely, following the designated exit routes.
- 4
Do not try to gather personal belongings or re-enter the area.
- 5
Report to the designated assembly point for headcount.
Example Answers
I would first remain calm, stop the rewinding machine to ensure it is safely off, and then quickly evacuate the area using the nearest exit. I would not attempt to retrieve my belongings, as safety is the priority.
If resources for the rewinding process were limited, how would you manage the situation?
How to Answer
- 1
Identify the most critical tasks that need to be accomplished.
- 2
Prioritize resource allocation to those tasks.
- 3
Consider alternative methods or tools that could increase efficiency.
- 4
Collaborate with the team to brainstorm innovative solutions.
- 5
Regularly review and adjust the strategy based on progress and new information.
Example Answers
I would start by assessing the tasks that are vital for the rewinding process and allocate my limited resources there. I would also explore alternative tools that might help us achieve more with less.
How do you handle stress when there is a high demand for production?
How to Answer
- 1
Prioritize tasks based on urgency and importance.
- 2
Practice deep breathing or mindfulness techniques to stay calm.
- 3
Communicate openly with your team about workload and challenges.
- 4
Take short breaks to recharge and maintain focus.
- 5
Stay organized with a to-do list to track progress and manage time.
Example Answers
I prioritize tasks by their deadlines and importance, and I take short breaks to ensure I stay focused. I also recommend team check-ins to voice any concerns.
If you were assigned to a project that required extensive collaboration with other departments, how would you ensure effective communication?
How to Answer
- 1
Set up regular check-in meetings to update all departments involved.
- 2
Use collaborative tools like Slack or Trello for real-time communication.
- 3
Create a shared document or space for project notes and updates.
- 4
Clarify roles and responsibilities upfront to avoid confusion.
- 5
Encourage open feedback and suggestions from all teams.
Example Answers
I would schedule weekly check-in meetings to discuss progress and ensure everyone is on the same page. Additionally, I would set up a Slack channel specifically for the project to facilitate ongoing communication and quick updates.
Don't Just Read Rewinder Questions - Practice Answering Them!
Reading helps, but actual practice is what gets you hired. Our AI feedback system helps you improve your Rewinder interview answers in real-time.
Personalized feedback
Unlimited practice
Used by hundreds of successful candidates
Rewinder Position Details
Salary Information
Average Salary
$33,150
Source: Talent.com
Recommended Job Boards
ZipRecruiter
www.ziprecruiter.com/Jobs/RewinderThese job boards are ranked by relevance for this position.
Related Positions
- Rewinder Operator
- Winder
- Ribbon Winder
- Winder Operator
- Spring Winder
- Tire Recapper
- Film Spooler
- Wire Twister
- Cable Reeler
- Winding Machine Operator
Similar positions you might be interested in.
Ace Your Next Interview!
Practice with AI feedback & get hired faster
Personalized feedback
Used by hundreds of successful candidates
Ace Your Next Interview!
Practice with AI feedback & get hired faster
Personalized feedback
Used by hundreds of successful candidates