Top 30 Rewinder Operator Interview Questions and Answers [Updated 2025]
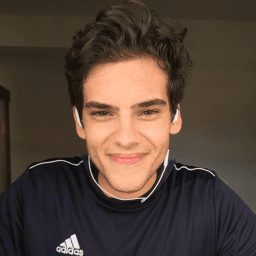
Andre Mendes
•
March 30, 2025
Preparing for a Rewinder Operator interview? This blog post is your ultimate guide to navigating the most common questions you might face. We provide example answers and insightful tips to help you respond effectively, boosting your confidence and readiness. Dive in to enhance your understanding and ensure you're well-prepared to impress your interviewers and secure the position.
Download Rewinder Operator Interview Questions in PDF
To make your preparation even more convenient, we've compiled all these top Rewinder Operatorinterview questions and answers into a handy PDF.
Click the button below to download the PDF and have easy access to these essential questions anytime, anywhere:
List of Rewinder Operator Interview Questions
Behavioral Interview Questions
Can you describe a time when you had to work closely with a team to complete a rewinding operation?
How to Answer
- 1
Choose a specific rewinding project to discuss.
- 2
Highlight your role and contributions to the team.
- 3
Mention any challenges faced and how the team overcame them.
- 4
Emphasize communication and collaboration within the team.
- 5
Conclude with the successful outcome and what you learned.
Example Answers
In my previous role, we had to complete a large rewinding project under a tight deadline. As the lead operator, I coordinated with the technicians to ensure the machines were set up properly. We faced a challenge when a machine malfunctioned, but we quickly communicated and adapted our workflow. Thanks to our teamwork, we completed the project on time, which taught me the importance of collaboration.
Tell me about a challenge you faced while operating a rewinding machine and how you resolved it.
How to Answer
- 1
Identify a specific challenge you faced while operating the machine.
- 2
Describe the symptoms or issues you noticed during the operation.
- 3
Explain the steps you took to diagnose and resolve the issue.
- 4
Highlight the outcome of your actions and any improvements made.
- 5
Emphasize what you learned from the experience and how it has helped you.
Example Answers
While operating a rewinding machine, I noticed inconsistent tension in the rolls, causing misalignment. I carefully adjusted the tension settings and recalibrated the machine. After adjustments, the rewinding process returned to normal, and I improved the monitoring of tension during operations.
Don't Just Read Rewinder Operator Questions - Practice Answering Them!
Reading helps, but actual practice is what gets you hired. Our AI feedback system helps you improve your Rewinder Operator interview answers in real-time.
Personalized feedback
Unlimited practice
Used by hundreds of successful candidates
Describe a situation where you had to quickly adapt to a change in production requirements.
How to Answer
- 1
Use the STAR method: Situation, Task, Action, Result.
- 2
Choose a relevant example from past experiences.
- 3
Highlight your problem-solving skills and flexibility.
- 4
Emphasize the positive impact of your adaptation.
- 5
Keep your response concise and focused.
Example Answers
In my previous job as a Rewinder Operator, we had a sudden increase in order volume due to a client's special event. I quickly assessed the new requirements, adjusted our workflow, and collaborated with my team to prioritize tasks. As a result, we met the deadline and received positive feedback from the client.
Have you ever encountered a safety issue while operating machinery? How did you handle it?
How to Answer
- 1
Describe the situation briefly focusing on the safety issue
- 2
Explain the immediate actions you took to address the issue
- 3
Mention any communication with supervisors or team members
- 4
Highlight any preventive measures you implemented afterwards
- 5
Conclude with the outcome and what you learned from it
Example Answers
During my last job, I noticed a burning smell coming from the machine while operating it. I immediately shut down the machine and unplugged it. I reported the issue to my supervisor, and we discovered it was due to an overheating motor. We serviced the machine, and I learned the importance of continuous monitoring.
Can you give an example of how your attention to detail benefited a project you worked on?
How to Answer
- 1
Choose a specific project to discuss.
- 2
Highlight a particular detail you focused on.
- 3
Explain the impact of your attention to that detail.
- 4
Use metrics or results if available to show success.
- 5
Keep your answer concise and focused.
Example Answers
In a recent project to optimize our packaging process, I noticed that small inconsistencies in label placement were causing customer complaints. I revised our labeling procedure to include precise measurements, which improved our error rate by 30% and greatly reduced customer feedback.
Describe an instance where you took the initiative to improve a process related to rewinding operations.
How to Answer
- 1
Identify a specific process you improved.
- 2
Explain how you recognized the need for improvement.
- 3
Describe the action you took to implement the change.
- 4
Share the outcome of your initiative and any metrics if possible.
- 5
Highlight what you learned from this experience.
Example Answers
In my previous role, I noticed that our rewinding process was causing frequent paper jams. I researched the issue and implemented a regular maintenance schedule for the machines. This reduced jams by 30% and increased our production efficiency.
Can you provide an example of how effective communication enhanced a project involving rewinding?
How to Answer
- 1
Identify a specific project where rewinding was involved
- 2
Describe the communication methods used, such as meetings or reports
- 3
Explain how communication improved team collaboration or efficiency
- 4
Use metrics or outcomes to demonstrate success
- 5
Keep the example focused on your role and contributions
Example Answers
In a project to optimize our rewinding process, I organized weekly team meetings to discuss production targets. This open communication helped us identify bottlenecks and we reduced downtime by 15%.
Describe a time when you had to address a customer's concern regarding the quality of rewound products.
How to Answer
- 1
Choose a specific incident that illustrates your problem-solving skills.
- 2
Explain your approach to understanding the customer's concern.
- 3
Describe the action you took to resolve the issue and ensure product quality.
- 4
Highlight any follow-up actions you took to prevent future issues.
- 5
Mention the positive outcome, emphasizing customer satisfaction.
Example Answers
Once, a customer reported that the rewound rolls had visible defects. I listened carefully to their concerns and inspected the product myself. I discovered a misalignment during the rewinding process. I corrected the issue and arranged to send out a replacement roll, ensuring the quality met our standards. The customer appreciated the prompt resolution.
Have you ever suggested a new process or machinery that improved efficiency in rewinding? What was it?
How to Answer
- 1
Think of a specific example where you identified a problem in the rewinding process.
- 2
Explain the new process or machinery you suggested and how you proposed it.
- 3
Discuss the positive outcomes it had on efficiency, such as time saved or waste reduced.
- 4
Mention any collaboration with team members or management in implementing the change.
- 5
Be ready to share metrics or evidence of the improvement, if possible.
Example Answers
In my previous role, I noticed that manual adjustments on the rewinding machine often slowed down production. I suggested implementing a digital control system that automated these adjustments, which reduced setup time by 30% and minimized waste by ensuring tighter tolerances.
Don't Just Read Rewinder Operator Questions - Practice Answering Them!
Reading helps, but actual practice is what gets you hired. Our AI feedback system helps you improve your Rewinder Operator interview answers in real-time.
Personalized feedback
Unlimited practice
Used by hundreds of successful candidates
Technical Interview Questions
What types of rewinding machines are you familiar with, and what are their key components?
How to Answer
- 1
Identify specific types of rewinding machines you have used.
- 2
Mention the key components of these machines clearly.
- 3
Provide examples of tasks you performed using these machines.
- 4
Discuss any maintenance or troubleshooting you handled.
- 5
Emphasize your understanding of how these machines operate.
Example Answers
I am familiar with both automatic and manual rewinding machines. The key components include the unwind stand, rewind roll, and tension control system. In my previous job, I operated a manual rewinding machine for label production and ensured the proper tension was maintained throughout the process.
Explain the maintenance procedures you have followed for a rewinding machine to ensure its efficient operation.
How to Answer
- 1
Start with regular daily inspections for wear and tear.
- 2
Detail the lubrication schedule and types of lubricants used.
- 3
Mention calibration checks for tension and speed settings.
- 4
Include cleaning procedures to prevent dust accumulation.
- 5
Discuss how you document maintenance activities and findings.
Example Answers
I perform daily inspections to check for any worn parts and ensure all components are functioning. I follow a strict lubrication schedule using high-quality grease for the gears and bearings to minimize friction. Calibration checks for tension settings are done weekly to ensure accuracy, along with regular cleaning to remove dust from the machine.
Don't Just Read Rewinder Operator Questions - Practice Answering Them!
Reading helps, but actual practice is what gets you hired. Our AI feedback system helps you improve your Rewinder Operator interview answers in real-time.
Personalized feedback
Unlimited practice
Used by hundreds of successful candidates
How do you assess the quality of the rewinded product? What specific metrics do you use?
How to Answer
- 1
Specify the visual and tactile inspection methods you use.
- 2
Mention quantitative metrics like tension, uniformity, and alignment.
- 3
Include how you test for defects, such as wrinkles or air bubbles.
- 4
Discuss the importance of adhering to industry standards.
- 5
Explain how feedback loops from quality checks can improve the process.
Example Answers
I assess the quality of the rewinded product through visual inspection, checking for any defects like wrinkles or misalignment. I also measure tension and ensure uniformity across the roll. Additionally, I follow industry standards to validate the product's quality.
What steps do you take to set up a rewinding machine for a new type of material?
How to Answer
- 1
Review the machine manual for specifications.
- 2
Select appropriate winding tension based on the material type.
- 3
Calibrate the machine according to the material thickness.
- 4
Run a test with the new material to check for issues.
- 5
Adjust settings based on the test results before full production.
Example Answers
First, I refer to the machine manual to understand the specifications for the new material. Then, I set the winding tension suitable for the material to prevent damage. After that, I calibrate the machine for the specific thickness. I always run a test to identify any potential issues. Finally, I make necessary adjustments based on the test run before starting the production.
How do you calibrate a rewinding machine, and what are the common issues you monitor?
How to Answer
- 1
Begin with the steps for calibration: checking tension, adjusting speed, and aligning rollers.
- 2
Mention the specific tools or measurements used, like tension gauges or digital readouts.
- 3
Discuss common issues like uneven tension, misalignment, or slippage of the material.
- 4
Highlight how you monitor these issues through regular checks or scheduled maintenance.
- 5
Conclude with an emphasis on the importance of precision for quality output.
Example Answers
To calibrate a rewinding machine, I first check the tension using a tension gauge, then adjust the speed settings according to the material specifications. I also ensure that the rollers are properly aligned. Common issues I monitor include uneven tension, which can cause defects, and material slippage, which can lead to jams. Regular monitoring helps maintain product quality.
What is your process for troubleshooting a faulty rewinding machine?
How to Answer
- 1
Start with a visual inspection of the machine for obvious issues.
- 2
Check electrical connections and components for any signs of damage or wear.
- 3
Test the machine's settings and controls to ensure they are properly configured.
- 4
Run diagnostic tests if available to identify specific errors.
- 5
Document any findings and repair steps taken for future reference.
Example Answers
I first perform a visual inspection of the rewinding machine to check for any physical damage or loose parts. Next, I examine the electrical connections to ensure everything is secure. If nothing is apparent, I review the settings and run any available diagnostics to pinpoint the problem.
What key performance indicators do you monitor while operating a rewinder?
How to Answer
- 1
Identify the most relevant KPIs for rewinding such as material yield, downtime, and production speed
- 2
Discuss how you track these KPIs and their importance in maintaining quality and efficiency
- 3
Explain any tools or software you use for monitoring performance
- 4
Mention how you use KPIs to improve processes and reduce waste
- 5
Be prepared to give specific examples of KPIs you successfully managed in past roles
Example Answers
I monitor material yield, which includes tracking the percentage of usable product versus waste. Downtime is also critical, so I log any machine stops and their causes. These indicators help maintain production efficiency and quality.
What advancements in rewinding technology are you most excited about?
How to Answer
- 1
Research recent trends in rewinding technology before the interview
- 2
Focus on specific technologies like automation and precision control
- 3
Mention how these advancements improve efficiency or product quality
- 4
Relate your excitement to how it impacts the industry or customers
- 5
Be prepared to discuss potential future impacts or trends
Example Answers
I'm excited about the advancements in automation in rewinding technology. Automated systems can significantly reduce downtime and increase throughput, which I believe will greatly benefit production efficiency.
How do you utilize data to improve the performance of the rewinding operations?
How to Answer
- 1
Analyze production data to identify bottlenecks in the process
- 2
Monitor downtime data to reduce interruptions and increase efficiency
- 3
Utilize quality control data to minimize defects in rewinding
- 4
Implement routine data collection and reporting for ongoing analysis
- 5
Share insights with the team to encourage data-driven problem solving
Example Answers
I analyze production data regularly to spot bottlenecks and adjust the workflow accordingly. For example, I've found that certain machines required more maintenance and addressing this reduced downtime significantly.
How do you identify the root cause of issues that arise during the rewinding process?
How to Answer
- 1
Start with data collection from the rewinding process logs.
- 2
Observe and document the specific issues as they occur in real-time.
- 3
Use a problem-solving framework like the 5 Whys to drill down to the root cause.
- 4
Involve team members to gather multiple perspectives on the issue.
- 5
Test potential solutions and monitor their effectiveness before full implementation.
Example Answers
I begin by analyzing the logs from our rewinding machine to see if there's a pattern to the issues. Then, I observe the process live while documenting every detail of the issue. Using the 5 Whys method helps me pinpoint the exact cause, and I often include my team for their insights.
Don't Just Read Rewinder Operator Questions - Practice Answering Them!
Reading helps, but actual practice is what gets you hired. Our AI feedback system helps you improve your Rewinder Operator interview answers in real-time.
Personalized feedback
Unlimited practice
Used by hundreds of successful candidates
Situational Interview Questions
If you are assigned multiple tasks that must be completed in a short timeframe, how would you prioritize them?
How to Answer
- 1
List all tasks and their deadlines
- 2
Assess the urgency and importance of each task
- 3
Choose tasks that align with team goals or deadlines
- 4
Communicate with your team if needed for clarity
- 5
Focus on high-impact tasks first before moving to others
Example Answers
I would first list out all the tasks and their deadlines. Then, I would assess which tasks are most urgent and important to meet immediate needs. I would prioritize tasks that have the biggest impact on the project and communicate with my supervisor if I need clarification.
If you notice a coworker consistently making mistakes on the rewinder, how would you address the situation?
How to Answer
- 1
Observe the coworker to understand the mistakes they are making.
- 2
Approach them privately to discuss your concerns respectfully.
- 3
Offer your assistance or share any tips that could help them improve.
- 4
Encourage a culture of teamwork and learning from mistakes.
- 5
Suggest to your supervisor if the situation does not improve.
Example Answers
I've noticed that a coworker is having some issues with the rewinder settings. I would approach them privately and say, 'I've seen some recurring mistakes and I wanted to check if you need any help with it.' I would offer to share what I've learned about the machinery to support them.
Don't Just Read Rewinder Operator Questions - Practice Answering Them!
Reading helps, but actual practice is what gets you hired. Our AI feedback system helps you improve your Rewinder Operator interview answers in real-time.
Personalized feedback
Unlimited practice
Used by hundreds of successful candidates
What would you do if there was an unexpected machine breakdown during a critical production period?
How to Answer
- 1
Stay calm and assess the situation quickly
- 2
Communicate the issue to your supervisor and team immediately
- 3
Identify the cause of the breakdown if possible
- 4
Follow the emergency protocol for machine repairs
- 5
Prioritize tasks to minimize downtime and maintain production schedules
Example Answers
If there was a machine breakdown, I would first stay calm and assess the situation to understand the problem. Then, I would immediately inform my supervisor and team about the issue. Next, I'd try to identify what caused the breakdown and follow our emergency repair protocols to fix it as quickly as possible. In the meantime, I would prioritize other tasks to ensure production continues smoothly.
If you find that the rewinding process is taking longer than expected, what steps would you take to identify and resolve the issues?
How to Answer
- 1
Check the machine settings for accuracy and proper calibration
- 2
Inspect the material for any defects or inconsistencies
- 3
Monitor the workflow and identify any bottlenecks in the process
- 4
Communicate with team members to gather insights on potential issues
- 5
Implement adjustments or repairs as needed based on findings
Example Answers
I would first check the machine settings to ensure they are correctly calibrated. If everything appears fine, I would inspect the material for any defects. Then, I would analyze the workflow for bottlenecks and discuss with my team to get their input on the slowdown.
How would you handle a disagreement with a supervisor regarding the operation of a rewinding machine?
How to Answer
- 1
Listen to your supervisor's perspective fully before responding
- 2
Present your thoughts clearly and factually, using data if possible
- 3
Be respectful and maintain a calm demeanor throughout the discussion
- 4
Suggest a compromise or alternative solution if applicable
- 5
Follow up after the discussion to ensure alignment moving forward
Example Answers
If I disagreed with my supervisor, I would first listen to their reasoning fully. Then, I would share my perspective with supporting data on why I think a different approach might work better. Maintaining respect is crucial, so I would remain calm and open to dialogue.
Suppose you realize that you are running low on material for the rewinding process. What actions would you take?
How to Answer
- 1
Assess the current inventory levels immediately
- 2
Notify your supervisor or relevant team members about the situation
- 3
Check if there is a reorder process in place and initiate it
- 4
Look for alternative materials that can be used temporarily
- 5
Ensure that production schedules are adjusted to reflect the material shortage
Example Answers
First, I would check the inventory levels to confirm the shortage and then inform my supervisor right away. I would follow up by initiating the reorder process for the necessary materials and explore if any alternatives are available for immediate use.
How would you ensure that all safety and operational regulations are being followed in the rewinding department?
How to Answer
- 1
Conduct regular training sessions for all staff on safety protocols
- 2
Implement daily safety checklists to monitor compliance
- 3
Encourage open communication for reporting hazards or breaches
- 4
Stay informed on regulations and update procedures as necessary
- 5
Lead by example, demonstrating safe practices at all times
Example Answers
I would organize weekly training for the team to reinforce safety protocols and ensure everyone is updated on the latest regulations.
If new technology is introduced that changes the rewinding process, how would you approach learning and using it?
How to Answer
- 1
Research the new technology thoroughly to understand its features and benefits
- 2
Attend training sessions or workshops offered by the company or technology provider
- 3
Practice using the technology hands-on to gain practical experience
- 4
Ask colleagues or supervisors for tips and best practices
- 5
Stay updated with industry trends and feedback from other users
Example Answers
I would start by researching the new technology online to understand how it works and what advantages it offers for the rewinding process. Then, I would take any training provided by the company. After that, I would practice using the technology while asking my colleagues for tips.
What would you do if you were facing pressure to meet a deadline while dealing with a machine malfunction?
How to Answer
- 1
Stay calm and assess the situation quickly
- 2
Communicate with your supervisor about the issue
- 3
Prioritize tasks and focus on critical operations
- 4
Consider temporary workarounds if possible
- 5
Document the malfunction for future reference
Example Answers
If I faced a machine malfunction under pressure, I would first remain calm and assess exactly what the problem is. Then, I would inform my supervisor about the issue to get guidance. I would prioritize the most critical tasks that need to be completed and explore any temporary workarounds until the machine is operational again. Lastly, I would document the issue for future reference.
If you were tasked with training a new rewinder operator, what key points would you emphasize?
How to Answer
- 1
Explain the importance of safety procedures while operating the rewinder.
- 2
Emphasize the need for attention to detail in monitoring the winding process to avoid defects.
- 3
Discuss the significance of understanding machine settings and how they affect product quality.
- 4
Highlight the role of regular maintenance and troubleshooting common issues.
- 5
Encourage effective communication skills for working with the team and addressing production challenges.
Example Answers
I would start by emphasizing safety procedures, as they are critical to ensure a safe working environment. Then, I would focus on monitoring the winding process closely, as small errors can lead to defects. It's also important for the new operator to understand machine settings, since these directly impact quality. Regular maintenance should be covered, alongside common troubleshooting techniques. Lastly, fostering good communication within the team is essential for smooth operations.
Don't Just Read Rewinder Operator Questions - Practice Answering Them!
Reading helps, but actual practice is what gets you hired. Our AI feedback system helps you improve your Rewinder Operator interview answers in real-time.
Personalized feedback
Unlimited practice
Used by hundreds of successful candidates
Rewinder Operator Position Details
Recommended Job Boards
ZipRecruiter
www.ziprecruiter.com/Jobs/Rewinder-OperatorThese job boards are ranked by relevance for this position.
Related Positions
- Rewinder
- Winder Operator
- Roll Operator
- Winder
- Winding Machine Operator
- Ribbon Winder
- Utility Operator
- Spring Winder
- Turning Machine Operator
- Tire Recapper
Similar positions you might be interested in.
Ace Your Next Interview!
Practice with AI feedback & get hired faster
Personalized feedback
Used by hundreds of successful candidates
Ace Your Next Interview!
Practice with AI feedback & get hired faster
Personalized feedback
Used by hundreds of successful candidates