Top 32 Saw Boss Interview Questions and Answers [Updated 2025]
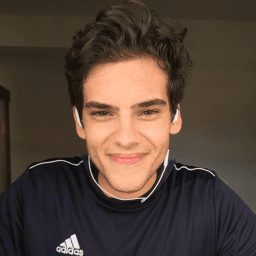
Andre Mendes
•
March 30, 2025
Preparing for a Saw Boss interview can be daunting, but we've got you covered with the most common questions you'll face. In this post, you'll find example answers and insightful tips to help you respond with confidence and clarity. Whether you're a seasoned pro or new to the role, our guide ensures you're ready to impress and secure your position. Dive in and start preparing today!
Download Saw Boss Interview Questions in PDF
To make your preparation even more convenient, we've compiled all these top Saw Bossinterview questions and answers into a handy PDF.
Click the button below to download the PDF and have easy access to these essential questions anytime, anywhere:
List of Saw Boss Interview Questions
Technical Interview Questions
What metrics do you track to evaluate the performance of the sawing process?
How to Answer
- 1
Identify key performance indicators relevant to sawing.
- 2
Mention metrics for efficiency and output.
- 3
Include quality measures like tolerance levels.
- 4
Discuss time metrics related to production speed.
- 5
Talk about maintenance metrics to ensure uptime.
Example Answers
I track production yield, which measures the amount of usable material produced versus waste. Additionally, I monitor cycle time to ensure we're meeting production targets efficiently.
What types of saws have you operated, and which one do you feel most proficient with?
How to Answer
- 1
List all types of saws you have used in previous jobs.
- 2
Mention specific tasks you accomplished with each saw.
- 3
Highlight the saw you are most proficient with and why.
- 4
Use specific examples to demonstrate your proficiency.
- 5
Be honest about your experience level with each type of saw.
Example Answers
I have operated circular saws and jigsaws extensively. I feel most proficient with the circular saw because I've used it for cutting various materials like plywood and 2x4s in multiple construction projects. My accuracy and speed have improved through practice.
Don't Just Read Saw Boss Questions - Practice Answering Them!
Reading helps, but actual practice is what gets you hired. Our AI feedback system helps you improve your Saw Boss interview answers in real-time.
Personalized feedback
Unlimited practice
Used by hundreds of successful candidates
What steps do you take to ensure that sawing equipment is properly maintained?
How to Answer
- 1
Perform regular inspections to check for wear and damage
- 2
Keep a maintenance schedule and log all service activities
- 3
Utilize proper cleaning techniques after each use
- 4
Ensure all safety features are functional before operation
- 5
Train team members on maintenance protocols and best practices
Example Answers
I conduct weekly inspections to identify any signs of wear and ensure blades are sharp, logging maintenance activities in a shared log.
What are the different cutting techniques you apply for various materials?
How to Answer
- 1
Identify the materials you work with most often
- 2
Explain specific techniques you use for each material
- 3
Mention how factors like thickness impact your technique
- 4
Discuss safety measures you implement during cutting
- 5
Share any innovative methods or technologies you adopt
Example Answers
For wood, I typically use straight cuts with a table saw, adjusting the blade height based on thickness. For metal, I prefer using a band saw with a fine-tooth blade to minimize burrs. When cutting plastic, a jigsaw works best to avoid cracking.
How would you troubleshoot a saw that is producing inaccurate cuts?
How to Answer
- 1
Check the blade alignment and ensure it is square to the table.
- 2
Inspect the blade for wear or damage; replace if necessary.
- 3
Examine the feed rate to ensure it is consistent and not too fast or slow.
- 4
Verify the saw's settings for the material you are cutting; adjust if needed.
- 5
Ensure the workpiece is secured properly to prevent movement during cutting.
Example Answers
First, I would start by checking if the blade is properly aligned with the table and making sure it is square; misalignment can cause inaccurate cuts. Next, I'd inspect the blade for any signs of wear or damage and replace it if it's dull. Additionally, I would look at the feed rate to ensure it's consistent and matches the material being cut, as too fast of a feed can lead to inaccuracies.
What safety protocols do you consider crucial when operating saws?
How to Answer
- 1
Always wear appropriate personal protective equipment such as goggles, gloves, and hearing protection.
- 2
Ensure the saw is maintained and inspected regularly to avoid malfunction.
- 3
Keep hands and body parts away from the cutting area at all times.
- 4
Follow the manufacturer's guidelines for operating procedures and safety measures.
- 5
Be aware of your surroundings and ensure no one is within a dangerous distance while operating.
Example Answers
I believe wearing proper PPE like goggles and gloves is essential. Regular maintenance of the saw also prevents accidents.
How do you determine the appropriate material feed rate for various types of saws?
How to Answer
- 1
Identify the material's properties such as hardness and density.
- 2
Consider the specifications of the saw, including blade type and power.
- 3
Adjust feed rate based on desired precision and finish quality.
- 4
Monitor saw performance and make real-time adjustments as needed.
- 5
Consult manufacturer guidelines for optimal feed rates based on material and saw type.
Example Answers
I determine the feed rate by first analyzing the material's hardness and density, then aligning it with the saw's specifications, ensuring I follow manufacturer recommendations.
What is your experience with setting up different types of sawing machines?
How to Answer
- 1
Identify specific types of sawing machines you have experience with
- 2
Describe the setup process you followed for each machine
- 3
Mention any troubleshooting techniques you applied during setup
- 4
Include examples of materials you worked with and their requirements
- 5
Highlight any safety protocols you observed while setting up
Example Answers
I have experience setting up band saws and table saws. For the band saw, I would check blade tension and alignment before starting. When setting up a table saw, I ensure the fence is parallel to the blade. I also make sure to adjust the height for different materials, like plywood or hardwood, following all safety guidelines.
Explain the process you follow for calibrating a saw to ensure it operates correctly.
How to Answer
- 1
Start by checking the manufacturer's specifications for calibration.
- 2
Ensure the saw is clean and free from debris before starting the process.
- 3
Use a calibrated measuring instrument to check the blade alignment.
- 4
Adjust the blade tension and alignment as per the specifications.
- 5
Finally, run a test cut to verify the saw operates correctly.
Example Answers
I begin by consulting the manufacturer's specifications for the saw. After cleaning the saw, I use a measuring instrument to check the blade alignment. I then adjust the tension and make necessary alignment corrections. Finally, I run a test cut to ensure everything is functioning properly.
How have you used technology to improve sawing operations in your past roles?
How to Answer
- 1
Identify specific technologies you have implemented or used.
- 2
Explain the problems these technologies solved in sawing operations.
- 3
Include measurable outcomes or improvements from the technology use.
- 4
Mention any software or automated systems that enhanced efficiency.
- 5
Share how these improvements benefited the overall workflow and safety.
Example Answers
In my previous role, I implemented a computer-controlled saw which reduced material waste by 15%. This system also integrated with our inventory management software for better resource tracking.
Don't Just Read Saw Boss Questions - Practice Answering Them!
Reading helps, but actual practice is what gets you hired. Our AI feedback system helps you improve your Saw Boss interview answers in real-time.
Personalized feedback
Unlimited practice
Used by hundreds of successful candidates
How do you ensure compliance with local regulations and safety standards in sawing operations?
How to Answer
- 1
Stay updated on local regulations and safety standards relevant to sawing.
- 2
Conduct regular safety training for all employees involved in sawing operations.
- 3
Implement a daily checklist to ensure all equipment is compliant and safe to use.
- 4
Document all safety procedures and audits to maintain records for inspection.
- 5
Encourage a culture of safety where employees feel comfortable reporting hazards.
Example Answers
I ensure compliance by regularly reviewing local regulations and conducting monthly training sessions for my team on safety protocols.
Behavioral Interview Questions
Can you describe a time when you had to lead a team in a challenging project related to sawing operations?
How to Answer
- 1
Set the context of the project and its challenges
- 2
Highlight your role and leadership approach during the project
- 3
Discuss the specific actions you took to address the challenges
- 4
Share the outcomes and what your team achieved
- 5
Reflect on what you learned as a leader from the experience
Example Answers
In my previous role, we faced a tight deadline to complete a custom sawing project for a key client. As the team leader, I organized daily meetings to track progress and address concerns. I implemented a new workflow that improved efficiency by 20%. Ultimately, we delivered the project on time and received positive feedback from the client, which strengthened our relationship.
Tell me about a time when you identified a safety issue in the workplace and how you addressed it.
How to Answer
- 1
Choose a specific example where you identified a clear safety issue.
- 2
Describe the context and the nature of the safety concern.
- 3
Explain the steps you took to address the issue.
- 4
Highlight the outcome of your actions, including any benefits to the workplace.
- 5
Mention any procedures you put in place to prevent future issues.
Example Answers
During a routine inspection, I noticed that some power tools were being left plugged in after use, which posed a risk of accidental injury. I immediately reported it to my supervisor and suggested implementing a tool storage policy. We created a protocol for unplugging tools and properly storing them after use, which reduced the risk of accidents significantly.
Don't Just Read Saw Boss Questions - Practice Answering Them!
Reading helps, but actual practice is what gets you hired. Our AI feedback system helps you improve your Saw Boss interview answers in real-time.
Personalized feedback
Unlimited practice
Used by hundreds of successful candidates
Give an example of a difficult decision you made regarding machine maintenance and what the outcome was.
How to Answer
- 1
Select a specific situation that highlights your decision-making skills.
- 2
Focus on the challenges you faced and why the decision was difficult.
- 3
Explain the thought process that led to your final decision.
- 4
Discuss the outcomes and what you learned from the scenario.
- 5
Emphasize any improvements in efficiency or safety that resulted from your decision.
Example Answers
In my previous role, we had a critical machine showing signs of wear but was still operational. I decided to halt production for a thorough inspection rather than risk a breakdown. This decision cost us downtime, but we discovered a major issue that could have led to an accident. We repaired it promptly and improved our maintenance schedule, leading to safer operations.
Describe a situation where you had to collaborate closely with others to ensure production targets were met.
How to Answer
- 1
Choose a specific project that required teamwork.
- 2
Highlight your role and contributions to the team.
- 3
Discuss how you communicated and resolved conflicts.
- 4
Mention the outcome and how targets were achieved.
- 5
Show the impact of teamwork on overall success.
Example Answers
In my last job, we had a project where we needed to increase production by 20%. I coordinated daily meetings with my team to track progress. We divided tasks based on strengths and used a shared platform for updates. By collaborating closely, we not only met our target but exceeded it by 5%.
Describe a situation where you had to manage multiple deadlines. How did you succeed?
How to Answer
- 1
Identify the key tasks and deadlines you faced.
- 2
Explain the prioritization method you used.
- 3
Discuss any tools or techniques that helped you stay organized.
- 4
Share how you communicated progress with stakeholders.
- 5
Conclude with the outcome and any lessons learned.
Example Answers
In my previous role, I managed three projects with overlapping deadlines. I prioritized tasks based on urgency and impact, using a project management tool to track progress. I held weekly updates with my team to ensure alignment, which helped us meet all deadlines. As a result, we delivered each project on time and received positive feedback from clients.
Can you describe a time when you had to adapt your work style to meet changing conditions on the floor?
How to Answer
- 1
Think of a specific situation where changes occurred quickly.
- 2
Explain your original work style and why it needed to change.
- 3
Describe the new conditions and how they affected your work.
- 4
Discuss the actions you took to adapt and the results of those actions.
- 5
Reflect on what you learned from the experience.
Example Answers
During a production surge, I initially followed our standard procedure. When unexpected machine downtime occurred, I quickly organized the team to focus on manual processes instead. This change helped us meet the target without sacrificing quality, and we completed the shift ahead of schedule.
Can you talk about a time when you received constructive criticism on your performance and how you responded?
How to Answer
- 1
Choose a specific example that highlights your willingness to learn.
- 2
Briefly explain what the criticism was and who gave it.
- 3
Describe how you reacted initially to the feedback.
- 4
Explain the steps you took to improve based on the criticism.
- 5
Conclude with the positive outcome resulting from applying the feedback.
Example Answers
In my previous role as a technician, my supervisor pointed out that I was too focused on completing tasks quickly, which sometimes affected quality. Initially, I felt defensive, but I took some time to reflect on the feedback. I then started to prioritize quality checks in my workflow and I even collaborated with more experienced coworkers to refine my techniques. As a result, my error rate decreased significantly, and I became known for delivering high-quality work.
Have you ever suggested changes that improved the sawing process? What were they?
How to Answer
- 1
Think about specific instances where you noticed inefficiencies.
- 2
Discuss the changes you proposed and the reasoning behind them.
- 3
Include measurable outcomes if possible, such as time saved or increased productivity.
- 4
Be clear about your role in implementing the changes.
- 5
Highlight how teamwork or collaboration played a part in the improvements.
Example Answers
In my previous role, I noticed that we frequently experienced delays due to blade dulling. I recommended a regular maintenance schedule for blade inspection, which reduced downtime by 20%.
Describe an experience where you contributed to reducing costs in sawing operations.
How to Answer
- 1
Identify a specific project where you saw cost reductions.
- 2
Quantify the impact of your contribution, such as percentage saved.
- 3
Mention techniques or methods you implemented to achieve savings.
- 4
Highlight collaboration with team members or departments.
- 5
Conclude with the benefits realized for the operation and the company.
Example Answers
In a recent project, I noticed we were wasting 15% more material due to improper saw calibration. I proposed a bi-weekly calibration schedule, leading to a 10% reduction in material costs over three months.
Don't Just Read Saw Boss Questions - Practice Answering Them!
Reading helps, but actual practice is what gets you hired. Our AI feedback system helps you improve your Saw Boss interview answers in real-time.
Personalized feedback
Unlimited practice
Used by hundreds of successful candidates
Tell me about a time when you had to learn a new technology or technique for sawing quickly.
How to Answer
- 1
Select a specific technology or technique you learned.
- 2
Describe the context of why learning was necessary.
- 3
Explain the steps you took to learn it effectively.
- 4
Discuss any challenges you faced and how you overcame them.
- 5
Conclude with the outcome of your learning and its impact.
Example Answers
In my previous job, we adopted a new high-speed band saw. It was crucial to improve production times. I dedicated time after hours to watch tutorial videos and practice on the machine. Initially, I struggled with adjusting the blade tension but eventually mastered it by consulting with a senior operator. As a result, I increased our cutting efficiency by 20%.
Situational Interview Questions
If a machine were to malfunction during a busy production period, what immediate actions would you take?
How to Answer
- 1
Stay calm and assess the situation quickly
- 2
Immediately notify your supervisor about the malfunction
- 3
Isolate the machine to ensure safety for all personnel
- 4
Determine if the issue can be resolved quickly or if maintenance is needed
- 5
Communicate with your team to divert workflow and maintain productivity
Example Answers
First, I would stay calm and assess the malfunction to understand its nature. Then, I would immediately inform my supervisor to get the right support, while ensuring the machine is isolated to prevent any safety risks. Next, I’d communicate with my team to reallocate resources and keep production moving smoothly.
You have a limited number of saw operators and a high volume of work. How would you prioritize tasks?
How to Answer
- 1
Assess the urgency and deadlines of each task
- 2
Consider the complexity and skill level required for each job
- 3
Evaluate the overall impact of each task on production goals
- 4
Communicate with your team to understand their capacities
- 5
Create a prioritization plan that can be adjusted as needed
Example Answers
I would first review all tasks based on their deadlines and urgency. Then, I would prioritize tasks that are critical for upcoming shipments or that will keep the production line moving. I would also talk to my operators to see who can handle more complex tasks, ensuring we maximize our efficiency.
Don't Just Read Saw Boss Questions - Practice Answering Them!
Reading helps, but actual practice is what gets you hired. Our AI feedback system helps you improve your Saw Boss interview answers in real-time.
Personalized feedback
Unlimited practice
Used by hundreds of successful candidates
How would you handle a request to improve the efficiency of the sawing operation amid tight deadlines?
How to Answer
- 1
Assess current operation processes to identify bottlenecks
- 2
Engage with team members for their insights on improvements
- 3
Implement small changes incrementally to monitor effects
- 4
Utilize data to track output and adjust strategies accordingly
- 5
Maintain open communication with stakeholders about progress
Example Answers
I would start by analyzing our current sawing processes to identify any time-consuming bottlenecks. I'd involve my team to gather their input on potential improvements. By implementing changes gradually, I can measure their impact on efficiency without overwhelming our operations.
If a new team member lacks experience with sawing equipment, how would you approach their training?
How to Answer
- 1
Begin with a thorough orientation on safety procedures.
- 2
Demonstrate the equipment operation step-by-step.
- 3
Provide hands-on training with supervision.
- 4
Encourage questions and clarify any misunderstandings.
- 5
Gradually increase responsibility as their skills improve.
Example Answers
I would start their training with a comprehensive safety briefing, followed by a demonstration of the saw in action. After that, I’d allow them to practice under supervision, encouraging them to ask questions and confirming their understanding throughout.
What would you do if you found that the quality of the cuts was not meeting company standards?
How to Answer
- 1
Identify the root cause of the quality issue by analyzing the cuts.
- 2
Engage with the team to gather insights and ensure everyone understands quality standards.
- 3
Implement a corrective action plan, adjusting techniques or equipment as necessary.
- 4
Document the changes and monitor the results to ensure improvement.
- 5
Communicate transparently with management about the situation and progress.
Example Answers
I would first analyze the cuts to identify any specific patterns causing the quality issues. After that, I would involve my team for feedback, ensuring everyone is aligned with the quality standards. We would then create a plan to improve our technique and monitor the results closely.
How would you motivate your team during a particularly tough production period?
How to Answer
- 1
Acknowledge the challenges your team is facing.
- 2
Set clear short-term goals to achieve small wins.
- 3
Communicate openly and provide regular updates.
- 4
Encourage teamwork and collaboration among team members.
- 5
Recognize and celebrate individual and team efforts.
Example Answers
I would start by acknowledging the tough situation we're facing. Then, I would set achievable short-term goals to create a sense of accomplishment. Frequent check-ins and updates would help keep everyone aligned and motivated.
How would you handle a request for urgent cutting jobs while maintaining regular production?
How to Answer
- 1
Assess the urgency of the request and its impact on regular production.
- 2
Communicate with your team to prioritize tasks effectively.
- 3
Allocate resources efficiently to manage both urgent and regular jobs.
- 4
Establish a clear timeline for the urgent job without compromising quality.
- 5
Keep stakeholders informed about progress and resource allocation.
Example Answers
I would first evaluate the urgency of the cutting job and how it affects our current production schedule. Then, I'd discuss with my team to see how we can rearrange priorities and allocate any extra resources needed to meet the urgent request while still keeping our regular production on track.
If a significant flaw is discovered in the product after it has been cut, how would you manage the fallout?
How to Answer
- 1
Acknowledge the issue promptly and take it seriously.
- 2
Investigate the root cause of the flaw immediately.
- 3
Communicate transparently with all stakeholders involved.
- 4
Develop a corrective action plan to address the flaw.
- 5
Implement measures to prevent similar issues in the future.
Example Answers
First, I would acknowledge the flaw and ensure that it is documented. Then, I would investigate how the flaw happened, involving the relevant team members. I would communicate the issue to my supervisors and stakeholders to keep them informed. After identifying the cause, I would create a plan to fix the flawed product and improve our processes.
What would you do to foster a positive safety culture in your team?
How to Answer
- 1
Lead by example and demonstrate safe work practices yourself
- 2
Encourage open communication about safety concerns without fear of retaliation
- 3
Provide regular training and refreshers on safety procedures
- 4
Recognize and reward safe behavior among team members
- 5
Establish clear safety protocols and ensure they are easily accessible
Example Answers
I would lead by example, consistently following safety protocols myself, which sets the tone for the team. I would also create an environment where team members feel comfortable discussing safety issues we might encounter.
How would you address a situation where a team member consistently fails to meet performance expectations?
How to Answer
- 1
Identify the root cause of their performance issues through a one-on-one conversation.
- 2
Set clear expectations and provide specific examples of what improvement looks like.
- 3
Offer support and resources, such as additional training or mentorship.
- 4
Establish a follow-up plan to monitor progress and provide ongoing feedback.
- 5
Document all conversations and agreements to ensure accountability.
Example Answers
I would first have a private conversation with the team member to understand their challenges. After identifying the issues, I'd clarify my expectations and give them specific goals to achieve. I would also offer resources such as training sessions to help them develop. Finally, I would set a timeline for follow-up meetings to assess their progress.
Don't Just Read Saw Boss Questions - Practice Answering Them!
Reading helps, but actual practice is what gets you hired. Our AI feedback system helps you improve your Saw Boss interview answers in real-time.
Personalized feedback
Unlimited practice
Used by hundreds of successful candidates
Saw Boss Position Details
Related Positions
- Woods Boss
- Camp Boss
- Boom Boss
- Farm Boss
- Boom Master
- Gamekeeper
- Crew Foreman
- Saw Repairer
- Saw Setter
- Mine Boss
Similar positions you might be interested in.
Ace Your Next Interview!
Practice with AI feedback & get hired faster
Personalized feedback
Used by hundreds of successful candidates
Ace Your Next Interview!
Practice with AI feedback & get hired faster
Personalized feedback
Used by hundreds of successful candidates