Top 33 Scale Technician Interview Questions and Answers [Updated 2025]
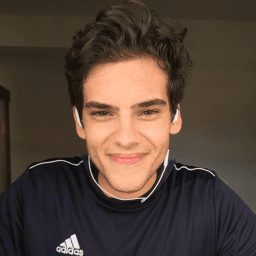
Andre Mendes
•
March 30, 2025
Preparing for a Scale Technician interview can be daunting, but we're here to help you succeed. In this blog post, you'll find a collection of the most common interview questions for this specialized role, complete with example answers and insightful tips on how to respond effectively. Dive in to enhance your confidence and readiness, ensuring you leave a lasting impression on your potential employer.
Download Scale Technician Interview Questions in PDF
To make your preparation even more convenient, we've compiled all these top Scale Technicianinterview questions and answers into a handy PDF.
Click the button below to download the PDF and have easy access to these essential questions anytime, anywhere:
List of Scale Technician Interview Questions
Situational Interview Questions
If you are collaborating with engineers on a new scale model, what key factors would you discuss with them?
How to Answer
- 1
Identify the purpose of the scale model and its intended use.
- 2
Discuss the material requirements for the model to ensure durability and accuracy.
- 3
Consider the scale and dimensions necessary for the model to meet specifications.
- 4
Talk about the timeline for development and any project constraints.
- 5
Ensure clear communication regarding testing methods and performance expectations.
Example Answers
I would first clarify the purpose of the scale model to align on expectations. Then, I would discuss material choices that will best represent the final product and ensure the model’s durability.
During a busy season, how do you handle stress while ensuring all scales are operating correctly?
How to Answer
- 1
Prioritize tasks based on urgency and importance.
- 2
Maintain a checklist to ensure all scales are functioning and calibrated.
- 3
Practice deep breathing techniques to stay calm under pressure.
- 4
Communicate proactively with team members about workload and challenges.
- 5
Take short breaks to recharge and maintain focus.
Example Answers
I prioritize tasks by focusing first on the scales that have the highest impact on operations. I keep a checklist to ensure all equipment is operational and calibrated. When I feel stressed, I use deep breathing to regain my focus and communicate any challenges to my team clearly.
Don't Just Read Scale Technician Questions - Practice Answering Them!
Reading helps, but actual practice is what gets you hired. Our AI feedback system helps you improve your Scale Technician interview answers in real-time.
Personalized feedback
Unlimited practice
Used by hundreds of successful candidates
Imagine a customer complains that their scale is consistently providing incorrect readings. How would you handle this situation?
How to Answer
- 1
Listen carefully to the customer's complaint without interrupting.
- 2
Ask specific questions to understand the nature of the incorrect readings.
- 3
Reassure the customer that you will help resolve the issue promptly.
- 4
Explain the troubleshooting steps you will take to diagnose the problem.
- 5
Follow up with the customer after resolving the issue to ensure satisfaction.
Example Answers
I would listen to the customer and let them explain the issue. Then, I would ask questions, like what the readings are versus what they should be. I would reassure them that I will take steps to fix the problem, like checking the calibration and ensuring it is properly set up.
If you were faced with a tight deadline and an essential scale malfunctioned, what steps would you take to resolve the issue?
How to Answer
- 1
Quickly assess the situation to determine the scale's problem and any immediate impact.
- 2
Prioritize temporary solutions to restore functionality, like recalibrating or resetting the scale.
- 3
Communicate the issue and the plan to the team to keep everyone informed.
- 4
If the issue cannot be resolved quickly, seek alternative methods to fulfill the task, like using a backup scale.
- 5
Document the malfunction and troubleshooting steps for future reference.
Example Answers
I would first analyze the issue to identify if it's a calibration or a mechanical problem. If it's fixable with a quick reset or recalibration, I would implement that. Meanwhile, I would inform my team and consider using a backup scale if time runs out.
If two team members disagreed on how to calibrate a specific scale, how would you mediate the situation?
How to Answer
- 1
Listen carefully to both team members' perspectives.
- 2
Encourage a respectful dialogue between them.
- 3
Ask clarifying questions to understand their reasoning.
- 4
Suggest a trial calibration using both methods if feasible.
- 5
Reinforce the goal of accurate calibration for the team's success.
Example Answers
I would first listen to both team members to understand their viewpoints. Then, I would facilitate a respectful discussion to allow them to explain their methods. If it makes sense, I could suggest we conduct a test calibration using both approaches to see which yields better results.
You have multiple scales requiring immediate attention. How do you prioritize your tasks?
How to Answer
- 1
Assess the current operational impact of each scale issue.
- 2
Identify any safety risks associated with each scale.
- 3
Determine which scales have the highest usage or dependency.
- 4
Communicate with team members to gather information on urgency.
- 5
Plan your work based on a combination of impact and urgency.
Example Answers
I would first assess which scales are impacting production the most. If one scale has stopped an entire line, I'd prioritize fixing that one first. I'd also check if any issues pose safety risks and address those immediately.
If you are asked to improve the scale testing process, what changes might you propose?
How to Answer
- 1
Identify current inefficiencies in the process
- 2
Suggest specific technology or tools to adopt
- 3
Propose a training program for staff
- 4
Recommend a schedule for regular reviews
- 5
Emphasize data collection and analysis for continuous improvement
Example Answers
I would analyze the current scale testing workflow to find bottlenecks and recommend using automated data collection tools to speed up the process.
If you needed parts for a scale repair and the usual supplier is out of stock, what would you do?
How to Answer
- 1
Check alternative suppliers for the required parts even if they are not the usual ones.
- 2
Contact the original supplier to see if they have an estimated restock date.
- 3
Explore the possibility of using similar parts or compatible substitutes.
- 4
Consult with team members for recommendations on where to source parts.
- 5
Document the issue and keep track of any changes made for future reference.
Example Answers
I would first check with alternative suppliers I know. If they also lack the parts, I'd reach out to our usual supplier to ask about restock timelines. If time is critical, I might look for compatible substitute parts and discuss the situation with my team for possible solutions.
What steps would you take if you discovered a scale that does not meet legal weight certification?
How to Answer
- 1
Immediate isolation of the scale to prevent further use
- 2
Document the scale's current condition and readings
- 3
Notify a supervisor or compliance officer without delay
- 4
Arrange for a professional calibration or repair service
- 5
Ensure that records of the incident are maintained for compliance tracking
Example Answers
If I found a scale that isn't legally certified, I would first isolate it and make sure no one uses it. Then, I would document its condition and immediately inform my supervisor. Next, I'd arrange for a certified technician to evaluate and repair the scale. Finally, I'd keep records of all actions taken to ensure compliance.
If you were given the responsibility to train new staff on scale operation, what topics would you cover?
How to Answer
- 1
Start with the fundamentals of scale operation including calibration and maintenance.
- 2
Explain safety protocols specific to handling scales and weighing products.
- 3
Discuss common issues that can arise with scales and troubleshooting techniques.
- 4
Teach proper documentation practices for weight data and compliance.
- 5
Emphasize teamwork and communication in a scaling operation context.
Example Answers
I would cover the basics of scale calibration and regular maintenance to ensure accuracy. Next, I would emphasize safety protocols to prevent accidents. I would also provide training on troubleshooting common scale issues and how to document weight data correctly.
Don't Just Read Scale Technician Questions - Practice Answering Them!
Reading helps, but actual practice is what gets you hired. Our AI feedback system helps you improve your Scale Technician interview answers in real-time.
Personalized feedback
Unlimited practice
Used by hundreds of successful candidates
What would you do if a digital scale consistently underreported weight measurements during calibration?
How to Answer
- 1
Identify the root cause of the underreporting.
- 2
Check the calibration settings and ensure they are correct.
- 3
Inspect the scale for physical obstructions or damage.
- 4
Use known weights to test accuracy after adjustments.
- 5
Document findings and actions taken for future reference.
Example Answers
I would start by verifying the calibration settings to ensure they are correctly set up. Then, I'd inspect the scale for any obstructions or physical issues. After making necessary adjustments, I'd conduct a test using standard weights to confirm accuracy.
Behavioral Interview Questions
Can you describe a time when you diagnosed a malfunction in a scale? What steps did you take to resolve the issue?
How to Answer
- 1
Start with a specific example from your past experience.
- 2
Briefly explain the symptoms you noticed in the scale.
- 3
Describe the diagnostic process you followed to identify the issue.
- 4
Outline the steps you took to fix the malfunction.
- 5
Conclude with the outcome and any lessons learned.
Example Answers
In my previous role, I noticed an industrial scale was frequently giving incorrect readings. I first checked the calibration and found it was off by several grams. I recalibrated the scale according to the manufacturer's specifications and tested it with known weights. After confirming accuracy, I monitored it for a week to ensure stability. The scale is now functioning perfectly, and I've implemented a regular calibration schedule to prevent future issues.
Tell me about a situation where you had to work closely with a colleague to ensure accurate scale calibration.
How to Answer
- 1
Describe the specific calibration task and your colleague's role.
- 2
Mention any challenges you faced and how you communicated.
- 3
Highlight the steps you took to collaborate effectively.
- 4
Emphasize the outcome and its impact on scale accuracy.
- 5
Reflect on what you learned from the experience.
Example Answers
In my previous job, I worked with a fellow technician on calibrating a large industrial scale. We divided the tasks based on our strengths and met daily to discuss our progress. During the process, we encountered issues with readings that were consistently off. By reviewing our methodology together, we pinpointed a misconfiguration. This collaboration ensured accurate calibration, and we improved our procedure for future calibrations.
Don't Just Read Scale Technician Questions - Practice Answering Them!
Reading helps, but actual practice is what gets you hired. Our AI feedback system helps you improve your Scale Technician interview answers in real-time.
Personalized feedback
Unlimited practice
Used by hundreds of successful candidates
Describe a situation where you had to explain a technical issue related to scales to a non-technical person.
How to Answer
- 1
Identify a specific technical issue you encountered.
- 2
Explain in simple terms without jargon.
- 3
Use analogies or relatable examples to clarify the issue.
- 4
Show empathy and patience during the explanation.
- 5
Briefly summarize the resolution or solution to reinforce understanding.
Example Answers
I once had to explain a calibration issue with a digital scale to a store manager. I told her that just like a car needs regular oil changes to run smoothly, scales also need calibrating to ensure they provide accurate weights. I demonstrated the calibration process and showed her how to recognize when the scale might need recalibrating.
Give an example of a time when your attention to detail affected the outcome of a scale-related project.
How to Answer
- 1
Think of a specific project related to scales.
- 2
Describe your role and the details you focused on.
- 3
Explain how your attention to detail made a difference.
- 4
Mention any positive outcomes or results from your actions.
- 5
Be clear and concise in your storytelling.
Example Answers
In my previous job as a scale technician, I was responsible for calibrating a batch of weighing scales. I noticed that one of the scales had a minor misalignment that could affect its accuracy. I took the time to realign it properly, which resulted in all scales being within tolerance. This ensured the lab's measurements were precise, leading to a successful product launch.
Have you ever been in a leadership role overseeing a team working on scale installation? What challenges did you face?
How to Answer
- 1
Describe your leadership experience during a specific scale installation project.
- 2
Mention key challenges such as communication, logistics, or technical issues.
- 3
Explain how you addressed these challenges with actionable solutions.
- 4
Highlight any outcomes or improvements from your leadership.
- 5
Keep the answer focused and relevant to the scale technician role.
Example Answers
In my previous job, I led a team for a large scale installation at a manufacturing site. One major challenge was coordinating schedules since each technician had different availability. I implemented a shared calendar for everyone to see deadlines and availability, which improved our efficiency by 30%.
Can you discuss a time you learned a new skill related to scale technology that improved your work?
How to Answer
- 1
Identify a specific skill that is relevant to scale technology
- 2
Describe the context or reason for learning the skill
- 3
Explain how you learned the skill (e.g., training, self-study)
- 4
Detail the impact the skill had on your work or team
- 5
Use metrics or specific results to quantify the improvement if possible
Example Answers
I learned to calibrate digital scales through an online course when I noticed inaccuracies affecting our inventory. After training, I implemented regular calibration checks, which reduced errors by 30%, improving our stock accuracy.
Describe a time when you went above and beyond your normal responsibilities as a Scale Technician.
How to Answer
- 1
Choose a specific instance that highlights your initiative
- 2
Focus on the positive outcomes of your actions
- 3
Make sure it reflects skills relevant to the Scale Technician role
- 4
Quantify your contributions when possible
- 5
Show how your actions benefited your team or company
Example Answers
During a busy season, I noticed our scale calibration was behind schedule. I volunteered to stay late and recalibrate all scales, reducing downtime and ensuring accuracy for the entire month, which improved our production flow.
Don't Just Read Scale Technician Questions - Practice Answering Them!
Reading helps, but actual practice is what gets you hired. Our AI feedback system helps you improve your Scale Technician interview answers in real-time.
Personalized feedback
Unlimited practice
Used by hundreds of successful candidates
Technical Interview Questions
What is the process for calibrating a scale? Can you detail the steps involved?
How to Answer
- 1
Start with a power-on check of the scale.
- 2
Use standard calibration weights that match the scale's capacity.
- 3
Zero the scale before adding weights to ensure accuracy.
- 4
Measure the weight incrementally, comparing with known weights.
- 5
Adjust the scale settings if discrepancies are found.
Example Answers
First, I power on the scale and allow it to warm up. Then I use standard calibration weights to ensure accuracy. I zero the scale with no weights on it. After that, I add weights incrementally, checking each time against known values. Lastly, if there are discrepancies, I adjust the scale as needed.
Describe the routine maintenance checks you perform on scales to ensure they are in good working condition.
How to Answer
- 1
List specific checks you perform regularly
- 2
Mention calibration procedures and frequency
- 3
Include visual inspections for damage or wear
- 4
Discuss cleaning protocols to maintain accuracy
- 5
Highlight any software updates or diagnostics
Example Answers
I perform visual inspections for any signs of wear or damage, calibrate the scales at least once a month, and ensure they are cleaned regularly to avoid dirt affecting measurements.
Don't Just Read Scale Technician Questions - Practice Answering Them!
Reading helps, but actual practice is what gets you hired. Our AI feedback system helps you improve your Scale Technician interview answers in real-time.
Personalized feedback
Unlimited practice
Used by hundreds of successful candidates
What common issues do you encounter with weight scales, and how do you troubleshoot them?
How to Answer
- 1
Identify typical problems, such as calibration issues, electronic malfunctions, and environmental factors affecting accuracy.
- 2
Explain the step-by-step troubleshooting process for each issue.
- 3
Use clear examples from past experiences where you successfully resolved scale issues.
- 4
Mention the importance of regular maintenance and calibration.
- 5
Be concise and focus on your problem-solving skills.
Example Answers
One common issue is inaccurate readings due to calibration errors. I usually check the calibration settings and perform adjustments using certified weights to ensure precision.
Are you familiar with any software used for managing scale data? If so, please elaborate.
How to Answer
- 1
Mention specific software you have used.
- 2
Explain your level of expertise with it.
- 3
Describe how you used the software in practical scenarios.
- 4
Highlight any relevant outcomes or improvements from using the software.
- 5
If applicable, discuss your learning process for new software.
Example Answers
I have experience using a software called 'Weighbridge Software Pro'. I used it for tracking scale data in the logistics department, where it improved our reporting speed by 30%.
What methods do you use to evaluate the performance of various scales?
How to Answer
- 1
Start by mentioning different types of scales you have experience with
- 2
Discuss both analytical and practical testing methods
- 3
Include specific performance metrics you monitor, like accuracy and precision
- 4
Mention regular maintenance checks and calibration procedures
- 5
Highlight documentation practices for tracking performance over time
Example Answers
I evaluate scales by performing daily checks for accuracy using certified weights, ensuring they meet specification tolerances, and I document performance in a maintenance log.
What types of scales do you have experience with, and how do they differ in terms of calibration and maintenance?
How to Answer
- 1
Identify specific types of scales you have worked with, like floor scales, bench scales, or lab balances.
- 2
Explain the calibration process for each type, noting any unique methods or tools required.
- 3
Discuss regular maintenance tasks associated with each scale type.
- 4
Mention any industry-specific standards or regulations you follow.
- 5
Relate personal experiences or challenges you faced while working with different scales.
Example Answers
I have experience with floor scales and lab balances. Floor scales typically require calibration with certified weights while lab balances often use internal calibration features. Maintenance for floor scales includes regular cleaning and ensuring the leveling feet are adjusted, while lab balances require more delicate care to avoid contamination.
What tools or equipment do you use to check the accuracy of a scale?
How to Answer
- 1
Mention specific tools like calibration weights and test weights.
- 2
Explain the importance of using standard weights for accuracy.
- 3
Discuss software or calibration devices used for advanced checks.
- 4
Emphasize adherence to industry standards during checks.
- 5
Include any relevant experience or specific examples from past work.
Example Answers
I commonly use certified calibration weights to check the accuracy of scales. For example, I would place a known weight on the scale and verify that it displays the correct value.
Can you explain how you would troubleshoot a scale with an electrical fault?
How to Answer
- 1
Identify the symptoms of the electrical fault clearly
- 2
Check the power supply and connections first
- 3
Use a multimeter to test for continuity and voltage
- 4
Inspect internal components for any visible damage
- 5
Refer to the service manual for specific fault codes or indicators
Example Answers
First, I would identify the symptoms of the scale malfunction, such as no power or erratic readings. Then, I would check the power supply and ensure all connections are secure. Using a multimeter, I would test for continuity in the wiring and voltage at various points. If there are any signs of damage in the internal components, I would replace them. Lastly, I would consult the service manual for any fault codes that could give further insights.
How do you integrate scale systems with other operational technologies like inventory management?
How to Answer
- 1
Identify key data points shared between scale systems and inventory management.
- 2
Discuss protocols and software used for integration, like APIs or middleware.
- 3
Explain the importance of real-time data synchronization for accuracy.
- 4
Mention any experience with specific technologies or platforms.
- 5
Highlight problem-solving skills in resolving integration issues.
Example Answers
I integrate scale systems with inventory management by using APIs to share weight data directly. This allows us to update inventory levels in real-time and ensure accuracy in stock management.
Don't Just Read Scale Technician Questions - Practice Answering Them!
Reading helps, but actual practice is what gets you hired. Our AI feedback system helps you improve your Scale Technician interview answers in real-time.
Personalized feedback
Unlimited practice
Used by hundreds of successful candidates
What procedures do you follow to ensure data accuracy from electronic scales?
How to Answer
- 1
Calibrate the scales regularly according to the manufacturer's guidelines
- 2
Perform routine maintenance and check for wear and tear
- 3
Ensure proper environmental conditions (temperature, humidity) during measurements
- 4
Use test weights to verify the accuracy before major weighings
- 5
Keep records of calibrations and maintenance for accountability
Example Answers
I calibrate the scales according to the manufacturer's specifications at regular intervals and use certified test weights to verify their accuracy before each major use.
What is your procedure for handling emergencies involving heavy machinery connected to scales?
How to Answer
- 1
Stay calm and assess the situation quickly
- 2
Ensure all machinery is powered down safely to avoid further harm
- 3
Notify relevant personnel or emergency services immediately
- 4
Follow established safety protocols and emergency procedures
- 5
Document the incident for future reference and training purposes
Example Answers
In an emergency with heavy machinery, I first stay calm and quickly assess the situation. I ensure the machinery is powered down to prevent any further accidents. Then, I notify my supervisor and emergency services as needed, following our emergency protocols closely. Finally, I document everything that happened for our records.
Scale Technician Position Details
Salary Information
Recommended Job Boards
ZipRecruiter
www.ziprecruiter.com/Jobs/Scale-TechnicianThese job boards are ranked by relevance for this position.
Related Positions
Ace Your Next Interview!
Practice with AI feedback & get hired faster
Personalized feedback
Used by hundreds of successful candidates
Ace Your Next Interview!
Practice with AI feedback & get hired faster
Personalized feedback
Used by hundreds of successful candidates