Top 31 Control Technician Interview Questions and Answers [Updated 2025]
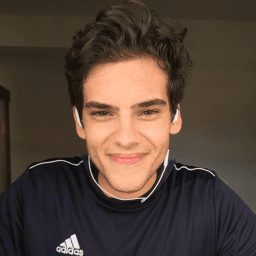
Andre Mendes
•
March 30, 2025
Navigating a job interview can be daunting, especially for specialized roles like that of a Control Technician. In this post, we delve into the most common interview questions you might face, providing not just example answers, but also strategic tips to help you respond with confidence. Prepare to enhance your interview skills and make a lasting impression on potential employers as you explore these essential questions and answers.
Download Control Technician Interview Questions in PDF
To make your preparation even more convenient, we've compiled all these top Control Technicianinterview questions and answers into a handy PDF.
Click the button below to download the PDF and have easy access to these essential questions anytime, anywhere:
List of Control Technician Interview Questions
Behavioral Interview Questions
Can you describe a time when you resolved a complex issue in a control system?
How to Answer
- 1
Identify a specific problem you faced with the control system.
- 2
Explain the steps you took to diagnose and analyze the issue.
- 3
Discuss the solution you implemented and its effectiveness.
- 4
Mention any teamwork or communication skills used during this process.
- 5
Conclude with what you learned from this experience.
Example Answers
In a project, the control system was malfunctioning due to incorrect sensor calibration. I worked with my team to analyze the data, discovered the calibration issue, and recalibrated the sensors. After implementing the solution, the system operated normally, improving efficiency by 20%. I learned the importance of thorough testing and calibration.
Tell me about a time you worked as part of a team to improve system performance. What was your role?
How to Answer
- 1
Choose a specific project where teamwork led to measurable improvement.
- 2
Describe your role clearly and your contributions to the team's success.
- 3
Highlight the problem you were addressing and the system performance metrics you aimed to improve.
- 4
Focus on collaborative efforts and communicate how you worked with team members.
- 5
End with the outcome and what you learned from the experience.
Example Answers
In my last job, we had repeated issues with production line downtime. I worked with a team of technicians to analyze the downtime causes. My role involved collecting and analyzing data on equipment performance. We implemented a schedule for preventive maintenance, which reduced downtime by 30%. This experience taught me the importance of data-driven decisions and effective team communication.
Good Candidates Answer Questions. Great Ones Win Offers.
Reading sample answers isn't enough. Top candidates practice speaking with confidence and clarity. Get real feedback, improve faster, and walk into your next interview ready to stand out.
Master your interview answers under pressure
Boost your confidence with real-time practice
Speak clearly and impress hiring managers
Get hired faster with focused preparation
Used by hundreds of successful candidates
Describe a situation where you had to lead a project. How did you ensure team collaboration?
How to Answer
- 1
Select a relevant project from your experience where you took a leadership role.
- 2
Highlight specific strategies you used to foster collaboration among team members.
- 3
Mention how you communicated goals and expectations clearly to the team.
- 4
Discuss any tools or methods you used to facilitate teamwork and track progress.
- 5
Reflect on the outcome of the project and how collaboration contributed to its success.
Example Answers
In a previous role, I led a project to upgrade our control system. I organized weekly check-ins, set clear objectives, and used project management software to keep track of tasks. This transparency helped the team collaborate effectively, and we completed the project ahead of schedule.
Can you give an example of a new technology or process you quickly learned to improve your work in control systems?
How to Answer
- 1
Identify a specific technology related to control systems.
- 2
Explain the challenge you faced that led to learning this technology.
- 3
Describe how you learned the technology quickly, such as through courses or hands-on experience.
- 4
Highlight the impact of implementing this technology on your work or team.
- 5
Keep your response focused and relevant to the role of a Control Technician.
Example Answers
To improve our automation processes, I quickly learned PLC programming using an online course. Our previous system was inefficient, so I took the initiative to understand ladder logic, which allowed me to streamline our operations, reducing downtime by 30%.
Describe a time when you had to explain a complex control concept to a non-technical stakeholder.
How to Answer
- 1
Identify a specific instance where you explained a control concept.
- 2
Use simple language without jargon to clarify the concept.
- 3
Focus on the stakeholder's perspective and needs.
- 4
Use analogies or visual aids to enhance understanding.
- 5
Summarize the outcome to show the effectiveness of your explanation.
Example Answers
During a project, I needed to explain PID control to our production manager. I avoided technical terms and said it was like a car's cruise control adjusting speed. I used a diagram to show how each element worked together. The manager understood and felt confident in our control adjustments.
Tell me about a time you received critical feedback on your work. How did you respond?
How to Answer
- 1
Choose a specific example that clearly demonstrates the feedback received.
- 2
Explain how you processed the feedback emotionally and professionally.
- 3
Describe the action steps you took to address the feedback.
- 4
Highlight any positive outcomes resulting from your actions.
- 5
Keep your tone positive and focus on growth and learning.
Example Answers
In my last role, I received feedback from my supervisor about my documentation practices being unclear. I took a moment to absorb the criticism without getting defensive. I then revised the documentation following best practices and asked for feedback. The result was improved clarity, and subsequent audits showed better compliance.
Describe a situation where you took the initiative to improve a control process.
How to Answer
- 1
Identify a specific control process you improved.
- 2
Explain the problem you noticed and the reasons for improvement.
- 3
Outline the steps you took to implement the change.
- 4
Highlight the positive outcomes resulting from your initiative.
- 5
Keep it concise and focused on your direct impact.
Example Answers
In my last position, I noticed that our temperature control system had frequent fluctuations that caused product quality issues. I researched a new sensor technology and suggested a trial. After implementing it, we reduced temperature deviations by 30%, improving product consistency significantly.
What accomplishment are you most proud of in your career as a control technician?
How to Answer
- 1
Choose a specific project or achievement that had a significant impact
- 2
Quantify your accomplishment with metrics if possible
- 3
Explain your role and the steps you took to achieve it
- 4
Discuss the skills or techniques you utilized
- 5
Mention how this accomplishment benefited your team or company
Example Answers
I am most proud of overseeing a project that automated our production line, which increased output by 30%. I led a team to integrate new control systems, and my expertise in PLC programming was crucial to its success.
Technical Interview Questions
What programming languages are you proficient in that are relevant to control systems?
How to Answer
- 1
Identify the primary programming languages used in control systems, such as Python, C, and PLC programming languages.
- 2
Mention any specific frameworks or libraries relevant to control systems you have experience with.
- 3
Emphasize your hands-on experience with these languages in real projects.
- 4
Be ready to discuss how you used these languages to solve specific problems or implement solutions.
- 5
Tailor your answer to the technologies used by the company you're interviewing with.
Example Answers
I am proficient in Python, C, and ladder logic for PLCs. I've used Python for data analysis and control algorithm implementation, particularly in my last project where I automated a manufacturing process.
How do you approach troubleshooting a malfunctioning control system?
How to Answer
- 1
Gather information on the symptoms and error messages.
- 2
Check the control system schematics and documentation.
- 3
Isolate the problem area, checking inputs and outputs systematically.
- 4
Test components individually to identify faults.
- 5
Document findings and solutions for future reference.
Example Answers
I start by gathering all relevant information about the malfunction, such as error codes and user reports. Then, I consult the schematics to understand the control logic. After isolating the suspected fault area, I systematically check the inputs and outputs to pinpoint the issue, testing each component before documenting my findings.
Good Candidates Answer Questions. Great Ones Win Offers.
Reading sample answers isn't enough. Top candidates practice speaking with confidence and clarity. Get real feedback, improve faster, and walk into your next interview ready to stand out.
Master your interview answers under pressure
Boost your confidence with real-time practice
Speak clearly and impress hiring managers
Get hired faster with focused preparation
Used by hundreds of successful candidates
Can you explain how you would design a control system for an automated manufacturing process?
How to Answer
- 1
Identify the requirements of the manufacturing process and the desired outcomes.
- 2
Choose the appropriate sensors and actuators needed for monitoring and control.
- 3
Select a suitable control strategy, such as PID, PLC, or distributed control systems.
- 4
Design the user interface for monitoring and control, ensuring it is user-friendly.
- 5
Implement testing and validation plans for the control system to ensure reliability.
Example Answers
First, I would gather all the requirements from stakeholders to understand the process. Then, I'd choose sensors like temperature and pressure sensors for monitoring, and actuators for controlling machinery. I might implement a PID controller for maintaining process variables. Finally, I would design a simple HMI for operators to interact with the system, and ensure thorough testing before deployment.
What types of field instrumentation do you commonly work with in control systems?
How to Answer
- 1
Identify key instrumentation relevant to the position.
- 2
Mention specific types like sensors, transmitters, controllers.
- 3
Discuss your experience with installation and calibration.
- 4
Highlight any troubleshooting skills with these instruments.
- 5
Tailor your answer to align with the company's industry.
Example Answers
I commonly work with pressure transmitters, temperature sensors, and flow meters. My experience includes installing and calibrating these instruments to ensure optimal performance.
What industry standards or regulations are you familiar with that impact control systems?
How to Answer
- 1
Identify key industry standards relevant to control systems like ISA, IEC, or NFPA.
- 2
Discuss any relevant safety regulations such as OSHA or EPA.
- 3
Mention standards specific to the industry sector you have experience with.
- 4
Highlight any certifications or training related to these standards you possess.
- 5
Be prepared to explain how these standards influence your work as a Control Technician.
Example Answers
I am familiar with ISA standards, particularly ISA-95 for integration of control systems in manufacturing environments. Additionally, I have worked in compliance with IEC 61511 for safety instrumented systems.
What experience do you have with Human-Machine Interface (HMI) development or implementation?
How to Answer
- 1
Identify specific HMI projects you have worked on
- 2
Mention the tools and software you used for HMI design
- 3
Explain your role in the development or implementation process
- 4
Highlight any specific results or improvements achieved
- 5
Discuss collaboration with other teams or departments involved in the project
Example Answers
I worked on an HMI project for a manufacturing line using Wonderware InTouch, where I developed user interfaces that improved operator response time by 20%.
Explain your experience with networking protocols commonly used in control systems.
How to Answer
- 1
Start by stating specific protocols you have used.
- 2
Give examples of control systems where you've implemented these protocols.
- 3
Mention any relevant certifications or training related to networking.
- 4
Discuss any troubleshooting or maintenance experience with these protocols.
- 5
Keep your answer relevant to the position and industry.
Example Answers
In my previous role as a Control Technician, I worked extensively with Modbus and Ethernet/IP protocols. I implemented these in our SCADA systems to enhance communication between PLCs and HMI panels. I also received training in industrial networking which helped me troubleshoot network issues effectively.
What types of PLCs are you experienced with, and how have you used them in projects?
How to Answer
- 1
Identify specific PLC brands and models you have worked with.
- 2
Describe your role in projects involving those PLCs.
- 3
Explain how you programmed or configured the PLC for specific tasks.
- 4
Mention any troubleshooting or optimization work done on those PLCs.
- 5
Relate your experience to the job requirements or industry standards.
Example Answers
I have worked with Allen-Bradley ControlLogix and Siemens S7-1200 PLCs. In my last project, I programmed the ControlLogix for a conveyor system automation, optimizing its performance based on sensor feedback.
What is your approach to maintaining documentation for control systems?
How to Answer
- 1
Use a standard template for all documentation to ensure consistency.
- 2
Regularly update documentation after changes in the control systems.
- 3
Utilize version control to keep track of changes and history.
- 4
Include detailed descriptions and diagrams to improve clarity.
- 5
Ensure easy accessibility for team members who need the documentation.
Example Answers
I always use a standard template for documentation, which helps maintain consistency. After any changes, I ensure the documentation is updated promptly. I also use version control tools to track modifications over time.
How do you use data analysis in maintaining and improving control systems?
How to Answer
- 1
Identify specific data types you analyze for control systems, such as performance metrics or error rates
- 2
Discuss how you interpret data to spot trends or anomalies that affect system performance
- 3
Mention tools or software you use for data analysis, like Excel, MATLAB, or custom scripts
- 4
Explain how data analysis informs your decision-making for system improvements
- 5
Provide an example of a past experience where data analysis led to a successful change in a control system
Example Answers
I analyze performance metrics like control loop error rates and use software like Excel to generate trends. Recently, I identified that a loop was oscillating through data analysis, which I corrected by tuning the PID controller, improving stability.
Good Candidates Answer Questions. Great Ones Win Offers.
Reading sample answers isn't enough. Top candidates practice speaking with confidence and clarity. Get real feedback, improve faster, and walk into your next interview ready to stand out.
Master your interview answers under pressure
Boost your confidence with real-time practice
Speak clearly and impress hiring managers
Get hired faster with focused preparation
Used by hundreds of successful candidates
How do you ensure that a control system is scalable for future needs?
How to Answer
- 1
Design with modular components to allow easy upgrades.
- 2
Use industry-standard protocols for interoperability.
- 3
Incorporate flexibility in system architecture to handle varying loads.
- 4
Plan for redundancy and fail-safes to ensure reliability during scaling.
- 5
Regularly review and assess technology trends to stay current.
Example Answers
I ensure scalability by using modular components so that we can upgrade individual sections without overhauling the entire system. This allows easy integration of new technologies as they emerge.
Describe an experience where you had to integrate multiple control systems. What challenges did you face?
How to Answer
- 1
Identify the control systems you integrated and the project context.
- 2
Explain the specific challenges such as compatibility issues or communication errors.
- 3
Discuss the steps you took to overcome those challenges.
- 4
Highlight the results of the integration and any lessons learned.
- 5
Keep your answer focused on your personal contributions.
Example Answers
In my last job, I integrated a SCADA system with a PLC and DCS for a wastewater treatment plant. The biggest challenge was that the protocols were not compatible, leading to data transfer issues. I implemented a middleware solution that allowed for protocol conversion. As a result, we improved communication between systems and reduced response times by 20%.
Situational Interview Questions
If assigned a project with a tight deadline, how would you prioritize your tasks to ensure completion?
How to Answer
- 1
Identify critical tasks that impact project completion
- 2
Break down tasks into smaller, manageable steps
- 3
Establish a timeline for each step based on urgency
- 4
Communicate with team members to delegate tasks if needed
- 5
Review progress regularly and adjust priorities as necessary
Example Answers
I would first identify the essential tasks that must be completed to meet the deadline. Then, I would break those down into smaller steps and create a timeline. I would communicate with my team to ensure everyone is aligned and delegate where appropriate, checking in regularly to track progress.
You encounter a disagreement with a colleague regarding the design of a control system. How would you handle it?
How to Answer
- 1
Listen carefully to your colleague's perspective without interrupting.
- 2
Ask clarifying questions to understand their reasoning in depth.
- 3
Share your own perspective calmly and with supporting evidence.
- 4
Suggest a compromise or alternative solution that incorporates both viewpoints.
- 5
If needed, involve a third party or supervisor to mediate the discussion.
Example Answers
I would start by listening to my colleague's ideas to fully understand their point of view. After discussing our thoughts, I would share my perspective, backing it up with data or examples. If we still disagree, I would propose an alternative design that blends both of our ideas.
Good Candidates Answer Questions. Great Ones Win Offers.
Reading sample answers isn't enough. Top candidates practice speaking with confidence and clarity. Get real feedback, improve faster, and walk into your next interview ready to stand out.
Master your interview answers under pressure
Boost your confidence with real-time practice
Speak clearly and impress hiring managers
Get hired faster with focused preparation
Used by hundreds of successful candidates
What steps would you take if you noticed a safety violation in the control system operations?
How to Answer
- 1
Identify the violation clearly and assess the risk immediately
- 2
Report the violation to your supervisor or safety officer
- 3
Take steps to mitigate any immediate dangers if safe to do so
- 4
Document the violation and the actions taken for future reference
- 5
Participate in follow-up discussions to improve safety protocols
Example Answers
If I noticed a safety violation, I would first assess the situation to ensure it's safe to intervene. I would then report it to my supervisor immediately. If possible, I would place a temporary hold on the operations to prevent any harm and document everything that happened.
If you discovered that a control system you designed was not performing as expected, how would you address it?
How to Answer
- 1
Acknowledge the issue and gather data on the performance.
- 2
Analyze the system to identify potential flaws or design issues.
- 3
Consult with team members or stakeholders for additional insights.
- 4
Develop a clear plan for redesign or adjustments based on findings.
- 5
Implement changes and test rigorously to ensure improved performance.
Example Answers
I would first gather data to understand where the control system is failing. Then, I would analyze the design for any flaws and involve my team for different perspectives. Finally, I'd create a plan to address the issues, implement the changes, and thoroughly test the system.
How would you implement a new control technology in an existing system without disrupting operations?
How to Answer
- 1
Conduct a thorough assessment of the current system and identify integration points.
- 2
Develop a phased implementation plan to minimize impact on ongoing operations.
- 3
Engage with stakeholders and communicate changes to all affected personnel.
- 4
Run pilot tests in a controlled environment before full deployment.
- 5
Train staff on new technology ahead of implementation.
Example Answers
First, I would assess the existing control system to identify how the new technology can fit in. Then, I would develop a phased implementation plan to introduce the new technology gradually. I would ensure to communicate with all stakeholders, keeping everyone informed throughout the process. Before going live, I'd run a pilot test to ensure everything functions correctly. Finally, I would organize training sessions for the staff to get them familiar with the new system.
You are alerted to a failure in a critical control system during a production run. What steps do you take?
How to Answer
- 1
Remain calm and assess the situation quickly
- 2
Identify the nature of the failure and its impact on production
- 3
Communicate with the team and inform them of the issue
- 4
Implement emergency procedures if necessary
- 5
Troubleshoot the problem systematically, documenting your steps
Example Answers
First, I would stay calm and assess the alert to understand the failure's severity. Then, I’d check the control system logs to identify the specific issue and its impact. I would inform my team about the situation so we can handle it together. If it's critical, I’d initiate emergency protocols. Lastly, I would troubleshoot systematically to resolve the issue and take notes for future reference.
You have limited resources for a control system upgrade. How would you decide what to prioritize?
How to Answer
- 1
Assess system criticality and failure impact
- 2
Identify highest risk areas and potential benefits
- 3
Consult with stakeholders for their input and needs
- 4
Evaluate cost-effectiveness and return on investment
- 5
Plan for phased upgrades to spread out resource needs
Example Answers
I would first evaluate which parts of the control system are most critical for safe operations. I would prioritize upgrades that minimize operational risk and have the highest potential impact on efficiency and safety.
If you were tasked with increasing efficiency in a control process, where would you start?
How to Answer
- 1
Analyze the current process to identify bottlenecks
- 2
Collect data on performance metrics to track efficiency
- 3
Consult with team members to gather insights and suggestions
- 4
Implement small-scale changes and monitor their impact
- 5
Use automation tools to optimize repetitive tasks
Example Answers
I would begin by analyzing the current control process to identify any bottlenecks that slow down efficiency. Then, I would collect data on key performance metrics to understand where improvements can be made. After that, I would consult with my team for their insights, as they may have valuable suggestions. Lastly, I'd implement small changes and monitor their effects on efficiency.
How would you handle training new technicians on a complex control system?
How to Answer
- 1
Start with a structured training plan covering key system components.
- 2
Utilize hands-on training to allow practical experience with the system.
- 3
Encourage questions and discussions to clarify complex concepts.
- 4
Implement a mentorship program pairing new technicians with experienced ones.
- 5
Use feedback from trainees to improve future training sessions.
Example Answers
I would create a detailed training plan, ensuring we cover all major components of the control system. I believe hands-on experience is crucial, so I would have new technicians work directly with the system, guided by experienced mentors who can answer questions.
How would you handle a situation where a team member consistently misses deadlines?
How to Answer
- 1
Approach the team member privately to discuss the issue.
- 2
Ask open-ended questions to understand their challenges.
- 3
Suggest collaborative solutions to help them meet deadlines.
- 4
Set clear expectations and follow-up on progress.
- 5
Encourage a culture of accountability within the team.
Example Answers
I would speak to the team member privately to understand any obstacles they face. By discussing their challenges, we can find a way to support them, like adjusting workload or setting smaller milestones.
Good Candidates Answer Questions. Great Ones Win Offers.
Reading sample answers isn't enough. Top candidates practice speaking with confidence and clarity. Get real feedback, improve faster, and walk into your next interview ready to stand out.
Master your interview answers under pressure
Boost your confidence with real-time practice
Speak clearly and impress hiring managers
Get hired faster with focused preparation
Used by hundreds of successful candidates
Control Technician Position Details
Recommended Job Boards
CareerBuilder
www.careerbuilder.com/jobs/controls-technicianZipRecruiter
www.ziprecruiter.com/Jobs/Controls-TechnicianThese job boards are ranked by relevance for this position.
Related Positions
Good Candidates Answer Questions. Great Ones Win Offers.
Master your interview answers under pressure
Boost your confidence with real-time practice
Speak clearly and impress hiring managers
Get hired faster with focused preparation
Used by hundreds of successful candidates
Good Candidates Answer Questions. Great Ones Win Offers.
Master your interview answers under pressure
Boost your confidence with real-time practice
Speak clearly and impress hiring managers
Get hired faster with focused preparation
Used by hundreds of successful candidates