Top 33 Shell Worker Interview Questions and Answers [Updated 2025]
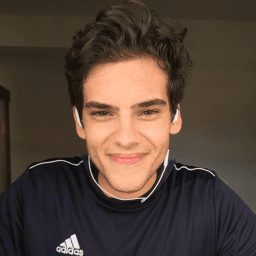
Andre Mendes
•
March 30, 2025
Preparing for a Shell Worker interview can be daunting, but this blog post has you covered with the most common questions candidates face. Dive into expertly crafted example answers and gain valuable tips on how to respond effectively, boosting your confidence and readiness. Whether you're a seasoned professional or a newcomer, this guide is your go-to resource for interview success.
Download Shell Worker Interview Questions in PDF
To make your preparation even more convenient, we've compiled all these top Shell Workerinterview questions and answers into a handy PDF.
Click the button below to download the PDF and have easy access to these essential questions anytime, anywhere: