Top 31 Slurry Mixer Interview Questions and Answers [Updated 2025]
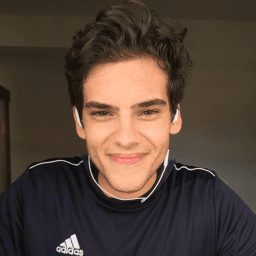
Andre Mendes
•
March 30, 2025
Navigating a job interview can be daunting, especially for specialized roles like a Slurry Mixer. In this post, we've compiled the most common interview questions for this position, complete with example answers and strategic tips to help you respond effectively. Whether you're a seasoned professional or new to the field, our guide will equip you with the insights needed to impress your potential employers.
Download Slurry Mixer Interview Questions in PDF
To make your preparation even more convenient, we've compiled all these top Slurry Mixerinterview questions and answers into a handy PDF.
Click the button below to download the PDF and have easy access to these essential questions anytime, anywhere:
List of Slurry Mixer Interview Questions
Behavioral Interview Questions
Can you describe a time when you had to work closely with a team to ensure the slurry mixing process was successful?
How to Answer
- 1
Choose a specific project where teamwork was essential.
- 2
Briefly outline your role and responsibilities within the team.
- 3
Describe the challenges faced and how the team collaborated to overcome them.
- 4
Highlight the final outcome and any metrics or success indicators.
- 5
Mention any skills or lessons learned that could be beneficial in the future.
Example Answers
In my previous job at ABC Corporation, I worked closely with a team of engineers and operators to improve our slurry mixing efficiency. My role was to lead the team in conducting experiments to optimize the mixing ratios. We faced challenges with inconsistent results initially, but through regular meetings and collaboration, we developed a new mixing protocol that resulted in a 15% increase in efficiency, which we measured over a month of testing.
Tell me about a time when you encountered a problem with the slurry mixer. How did you resolve it?
How to Answer
- 1
Choose a specific incident that shows your problem-solving skills.
- 2
Explain the problem clearly and mention any impact it had on production.
- 3
Describe the steps you took to analyze and resolve the issue.
- 4
Highlight any collaboration with team members or other departments.
- 5
Conclude with the outcome and any lessons learned.
Example Answers
In my previous job, the slurry mixer was not achieving the desired consistency, which affected product quality. I monitored the mixer settings and realized that the paddle speed was too low. I adjusted the paddle speed and conducted tests, collaborating with the quality team to ensure the right consistency was achieved. This improved our quality metrics and minimized waste.
Don't Just Read Slurry Mixer Questions - Practice Answering Them!
Reading helps, but actual practice is what gets you hired. Our AI feedback system helps you improve your Slurry Mixer interview answers in real-time.
Personalized feedback
Unlimited practice
Used by hundreds of successful candidates
Describe a situation where you had to take the lead during a crisis in the mixing process. What steps did you take?
How to Answer
- 1
Identify a specific mixing crisis you encountered.
- 2
Explain the immediate actions you took to assess the situation.
- 3
Describe how you communicated with your team and stakeholders.
- 4
Detail the solutions you implemented to resolve the issue.
- 5
Conclude with the outcome and what you learned from the experience.
Example Answers
In my previous job, we faced a situation where a key ingredient was not blending correctly, causing a separation in the slurry. I quickly assessed the mixing parameters and adjusted the speed and duration to improve integration. I informed my team and gathered their insights, which led us to modify the ingredient addition sequence. As a result, we restored the mix quality and met our production deadline, learning the importance of quick teamwork under pressure.
Describe an instance where you had to adapt to changes in the mixing process requirements. What was the outcome?
How to Answer
- 1
Identify a specific change in mixing requirements you faced.
- 2
Explain the steps you took to adapt to the change.
- 3
Highlight the impact of your adaptation on the process or product.
- 4
Mention any metrics or feedback that demonstrate success.
- 5
Keep your answer focused on the change and your response to it.
Example Answers
In my previous role, we switched from a water-based to a solvent-based mixing process. I researched the new materials and adjusted our mixing speeds and temperatures. This adaptation reduced mixing time by 20% and improved the final product consistency, leading to fewer customer complaints.
Have you ever received constructive criticism about your mixing techniques? How did you respond to it?
How to Answer
- 1
Acknowledge the feedback positively
- 2
Explain the specific criticism you received
- 3
State what actions you took to improve
- 4
Share the results of your improvements
- 5
Reflect on the experience and what you learned
Example Answers
Yes, my supervisor noted that my mixing times were too long, which could lead to inconsistent results. I took this to heart and started timing each mix more carefully. As a result, I improved the consistency of my slurry mixes, which enhanced the overall quality.
Describe a situation where you had to communicate complex information about the slurry mixing process to someone who wasn't technical.
How to Answer
- 1
Identify the key points of the slurry mixing process that are most relevant to the audience.
- 2
Use analogies or simple comparisons to explain complex concepts.
- 3
Be patient and open to questions during the explanation.
- 4
Summarize the main takeaways at the end of your explanation.
- 5
Ensure your language is free of jargon and technical terms.
Example Answers
In a recent project, I needed to explain the slurry mixing process to a new quality control team member. I simplified it by comparing slurry mixing to making a smoothie, highlighting how ingredients need to be blended evenly. I focused on the importance of consistency for product quality and encouraged them to ask questions, which helped clarify their understanding.
Have you ever implemented a new technique or technology in the mixing process? What was the result?
How to Answer
- 1
Think of a specific instance where you introduced a technique or technology.
- 2
Describe the context and reason for the change clearly.
- 3
Explain how you implemented the new approach step-by-step.
- 4
Mention the measurable results or improvements that followed.
- 5
Highlight any feedback from supervisors or team members.
Example Answers
Yes, I introduced a new high-shear mixing technique that reduced mixing time by 30%. I noticed inconsistent homogeneity in our batches, so I researched and proposed a high-shear mixer. After training the team and implementing the change, our quality metrics improved significantly, leading to fewer complaints.
Tell me about a time when you took the initiative to address a long-standing issue in the slurry mixing process.
How to Answer
- 1
Identify a specific issue you observed.
- 2
Describe the steps you took to address the issue.
- 3
Highlight the positive outcome of your actions.
- 4
Emphasize teamwork or collaboration if applicable.
- 5
Be concise and focus on your specific contributions.
Example Answers
In my previous role, I noticed that the slurry mixer was regularly experiencing clogs due to improper mixing ratios. I initiated a review of the mixing guidelines and proposed a new training program for the operators. This led to a 30% reduction in downtime caused by clogs, improving our productivity significantly.
Describe a time when you trained someone new on the handling of slurry mixing equipment. What was your approach?
How to Answer
- 1
Start with the context: explain who you trained and why.
- 2
Describe the training methods you used, such as hands-on practice or demonstrations.
- 3
Highlight any specific challenges encountered during the training.
- 4
Explain how you ensured the trainee understood safety and operational protocols.
- 5
Conclude with the outcome: how the trainee performed after the training.
Example Answers
I trained a new operator on the slurry mixer last year because our team was short-staffed. I used a combination of hands-on demonstrations and step-by-step instructions to show them how to prepare and operate the equipment. One challenge was their initial difficulty in adjusting the mixing speed, so I focused on practical exercises to build their confidence. I also emphasized safety protocols, ensuring they knew the proper handling techniques. By the end of the training, they were able to operate the mixer independently and safely.
Don't Just Read Slurry Mixer Questions - Practice Answering Them!
Reading helps, but actual practice is what gets you hired. Our AI feedback system helps you improve your Slurry Mixer interview answers in real-time.
Personalized feedback
Unlimited practice
Used by hundreds of successful candidates
How do you track improvements in the mixing process over time?
How to Answer
- 1
Identify key performance indicators related to the mixing process.
- 2
Implement consistent measurement techniques to gather data.
- 3
Use software tools to analyze data trends over time.
- 4
Regularly review and document process changes and outcomes.
- 5
Engage the team in regular discussions about mixing efficiency.
Example Answers
I track improvements by measuring key indicators like consistency and batch cycle time. I use software to log these metrics and analyze trends monthly.
What goals have you set for yourself in your role as a slurry mixer, and how have you achieved them?
How to Answer
- 1
Identify specific, measurable goals related to mixing efficiency or quality control.
- 2
Include examples of steps taken to achieve those goals.
- 3
Mention any collaboration with team members or trainings attended.
- 4
Discuss adjustments made based on feedback or outcomes.
- 5
Highlight any quantitative improvements resulting from your efforts.
Example Answers
One goal I set was to reduce the mixing time by 20%. I achieved this by optimizing the mixing process and adjusting speeds based on the material used. I tracked our mixing times weekly to monitor progress.
Technical Interview Questions
What types of mixing equipment are you familiar with, and how do they differ in their operation?
How to Answer
- 1
Identify key types of mixing equipment like agitators, stirrers, and homogenizers.
- 2
Explain the operational principles of each type succinctly.
- 3
Include specific applications or industries where each type is used.
- 4
Mention any personal experience with these mixers, if applicable.
- 5
Be prepared to discuss advantages and disadvantages of different mixing methods.
Example Answers
I'm familiar with several types of mixing equipment, including agitators, which use rotational motion to mix liquids, and homogenizers that create a uniform mixture using high pressure. Agitators are often used in chemical processing, while homogenizers are common in food production.
Can you explain how to calculate the correct proportions of materials for a specific slurry?
How to Answer
- 1
Identify the desired final properties of the slurry, such as viscosity and density.
- 2
Determine the specific gravities of each material involved in the slurry.
- 3
Use a formula or ratio based on material properties to find the correct volume or weight proportions.
- 4
Consider any additional factors such as water content and the effects of additives.
- 5
Perform a test mix to validate the proportions before final production.
Example Answers
To calculate the proportions for a slurry, I first identify the desired viscosity and density. Then, I check the specific gravities of the materials. Using those values, I apply a weight ratio to find the right mix, adjusting for any water or additives needed.
Don't Just Read Slurry Mixer Questions - Practice Answering Them!
Reading helps, but actual practice is what gets you hired. Our AI feedback system helps you improve your Slurry Mixer interview answers in real-time.
Personalized feedback
Unlimited practice
Used by hundreds of successful candidates
What routine maintenance tasks do you typically perform on a slurry mixer to ensure optimal performance?
How to Answer
- 1
Check and clean mixing blades regularly to prevent buildup.
- 2
Inspect and replace seals and gaskets to prevent leaks.
- 3
Monitor and adjust motor settings to ensure proper speed and torque.
- 4
Lubricate bearings and moving parts as specified in the manual.
- 5
Conduct regular tests of the slurry consistency to ensure it meets specifications.
Example Answers
I regularly check and clean the mixing blades to avoid any material buildup, which can affect performance. I also inspect the seals to ensure there are no leaks and replace them as needed.
What techniques do you apply to optimize the mixing process and ensure efficiency?
How to Answer
- 1
Focus on selecting the right mixer type for the materials involved.
- 2
Adjust mixing speed and time based on material properties.
- 3
Implement process monitoring to track efficiency and consistency.
- 4
Use additives or conditioners to improve mix quality.
- 5
Regularly maintain and clean equipment to avoid contamination.
Example Answers
I optimize the mixing process by first selecting a suitable mixer type that matches the materials, such as using a paddle mixer for slurries that are more viscous. I also monitor the mixing time and speed, adjusting them based on the specific materials to achieve uniformity efficiently.
How do you determine the compatibility of different materials in a slurry mix?
How to Answer
- 1
Analyze the properties of each material such as density, particle size, and viscosity.
- 2
Conduct compatibility tests by mixing small samples to observe reactions or settling.
- 3
Consult material safety data sheets (MSDS) for chemical compatibility.
- 4
Consider the intended application and the final product requirements.
- 5
Evaluate past formulations and industry standards for similar slurry mixes.
Example Answers
I first analyze the properties of the materials, focusing on density and viscosity. Then, I conduct small-scale tests by mixing samples to observe their behavior and ensure no adverse reactions occur.
What steps do you take when you notice an unusual sound coming from the slurry mixer?
How to Answer
- 1
Stop the mixer immediately to prevent damage.
- 2
Inspect the mixer for visible signs of wear or obstruction.
- 3
Check for loose components or fasteners that may be causing the noise.
- 4
Refer to the maintenance manual for troubleshooting steps.
- 5
Document the issue and report it to the maintenance team for follow-up.
Example Answers
If I hear an unusual sound from the slurry mixer, my first step is to stop it immediately to avoid further damage. Then, I visually inspect the mixer for any loose parts or blockages. After that, I check the maintenance manual for guidance and document the situation for the maintenance team.
How do you analyze the data from mixing operations to ensure quality?
How to Answer
- 1
Identify key quality metrics relevant to the mixing process such as viscosity, density, and temperature.
- 2
Utilize statistical process control (SPC) charts to monitor variations over time.
- 3
Conduct regular analysis of mixing data to identify trends or anomalies that could indicate problems.
- 4
Implement a feedback loop from quality checks to improve mixing parameters and practices.
- 5
Collaborate with the quality control team to align data analysis with broader quality assurance goals.
Example Answers
I start by monitoring viscosity and density data during mixing operations, using SPC charts to track any deviations over time. This helps identify issues quickly.
What regulations do you have to be aware of when operating a slurry mixer?
How to Answer
- 1
Understand local environmental regulations regarding emissions and waste disposal
- 2
Be familiar with OSHA safety standards for handling materials and equipment
- 3
Know the specific guidelines for handling hazardous materials if applicable
- 4
Review any equipment-specific regulations for operation and maintenance
- 5
Stay updated on industry standards and best practices for slurry mixing
Example Answers
I must be aware of local environmental regulations that limit emissions and dictate waste disposal methods to ensure compliance.
Can you describe different mixing techniques that you have used and their respective advantages?
How to Answer
- 1
Identify at least three mixing techniques relevant to slurry mixing.
- 2
Explain the procedure of each technique briefly.
- 3
Highlight the specific advantages of each technique in practical applications.
- 4
Use clear examples from your experience to illustrate your points.
- 5
Keep your answers concise and focused on the benefits to the operation.
Example Answers
One technique I have used is paddle mixing. It is effective for mixing thick slurries because it provides good shear and can handle high viscosity materials. This method ensures a uniform consistency without overprocessing.
What safety protocols do you follow specifically when working with slurry mixing equipment?
How to Answer
- 1
Always wear appropriate personal protective equipment such as gloves, goggles, and masks
- 2
Conduct a pre-operation check of equipment to identify any hazards or malfunctions
- 3
Ensure that emergency shut-off procedures are understood and followed before starting work
- 4
Maintain a clean and organized work area to prevent slips or spills
- 5
Stay updated on safety training and refreshers regarding slurry mixing operations
Example Answers
I always use PPE like gloves, goggles, and masks to protect myself while working with slurry equipment. Before I begin, I perform a thorough check of the equipment to ensure everything is functioning properly and that there are no leaks.
Don't Just Read Slurry Mixer Questions - Practice Answering Them!
Reading helps, but actual practice is what gets you hired. Our AI feedback system helps you improve your Slurry Mixer interview answers in real-time.
Personalized feedback
Unlimited practice
Used by hundreds of successful candidates
Situational Interview Questions
You notice a safety hazard while operating the slurry mixer. What actions do you take to address this?
How to Answer
- 1
Immediately stop the operation of the slurry mixer.
- 2
Secure the area to prevent others from approaching the hazard.
- 3
Report the hazard to a supervisor or designated safety officer.
- 4
Document the hazard and any steps taken to address it.
- 5
Follow up to ensure corrective actions are implemented.
Example Answers
When I notice a safety hazard, I would stop the slurry mixer immediately to ensure everyone's safety. Then, I would secure the surrounding area to prevent any accidents. I would report the hazard to my supervisor right away and make sure it is documented properly.
If you find that the consistency of the slurry is not meeting specifications, how would you handle the situation?
How to Answer
- 1
Assess the current slurry consistency using appropriate testing methods.
- 2
Identify potential causes for the discrepancy, such as ingredient ratios or equipment malfunction.
- 3
Adjust the mixing process or ingredients to correct the consistency.
- 4
Communicate with the team about the issue and proposed solutions.
- 5
Document the findings and steps taken for future reference.
Example Answers
I would first test the slurry to determine how far off the consistency is from the specifications. Then, I would check the ingredient ratios and mixing equipment for any issues. Based on my findings, I would make adjustments and communicate with my team to ensure everyone is aware of the changes made.
Don't Just Read Slurry Mixer Questions - Practice Answering Them!
Reading helps, but actual practice is what gets you hired. Our AI feedback system helps you improve your Slurry Mixer interview answers in real-time.
Personalized feedback
Unlimited practice
Used by hundreds of successful candidates
If a team member disagrees with your approach to mixing a slurry, how would you manage that conflict?
How to Answer
- 1
Listen actively to their concerns to understand their perspective
- 2
Acknowledge the validity of their input, even if you disagree
- 3
Discuss the reasons behind your approach and seek common ground
- 4
Consider a compromise or alternative solution that incorporates both views
- 5
Follow up after the discussion to ensure the team is aligned and to reinforce collaboration
Example Answers
I would first listen to my colleague's views to fully understand their perspective. Acknowledging their concerns helps create an open dialogue. Then, I would explain my reasoning for my approach while looking for common ground to resolve our differences.
In the event of a slurry spill during mixing, what immediate steps would you take to manage the situation?
How to Answer
- 1
Stop the mixing operation immediately to prevent further spill.
- 2
Alert team members and notify a supervisor about the situation.
- 3
Assess the spill area for hazards and determine the safest way to proceed.
- 4
Use appropriate containment measures to prevent slurry from spreading.
- 5
Follow the company's spill response protocol and properly document the incident.
Example Answers
First, I would stop the mixing process to stop additional slurry from spilling. Then, I would notify my supervisor and team members to make sure everyone is aware of the situation. Next, I'd assess the spill for hazards before containing the slurry with absorbent materials or barriers to prevent it from spreading.
If you are faced with two different mixing protocols for a project, how would you decide which one to follow?
How to Answer
- 1
Evaluate the specific requirements of the project and what each protocol can achieve
- 2
Consider the materials involved and their compatibility with each protocol
- 3
Analyze past performance data or case studies related to both protocols
- 4
Consult with team members or experts for insights on both methods
- 5
Prioritize safety and efficiency in your decision-making process
Example Answers
I would start by reviewing the project requirements and how each protocol aligns with them. Then, I would look at the material compatibility to ensure effectiveness. Finally, I would consult team members for their experiences with both protocols before making a decision.
How would you handle a situation where deadlines are tight, and the mixing process is not going as planned?
How to Answer
- 1
Quickly assess the situation to identify the root cause of the issue.
- 2
Communicate with your team to gather insights and potential solutions.
- 3
Prioritize tasks that can help get the mixing process back on track.
- 4
Consider alternative methods or tools to speed up the process if feasible.
- 5
Keep stakeholders informed about progress and any necessary adjustments.
Example Answers
First, I would quickly assess the mixing process to determine what's causing the delay. Then, I'd communicate with my team to brainstorm solutions and prioritize the most critical tasks. If the issues persist, I would explore if alternative mixing techniques can be applied to meet the deadline.
You have limited resources but a high demand for slurry production. How do you prioritize tasks?
How to Answer
- 1
Identify the most critical orders based on deadlines and customer impact
- 2
Assess the availability of resources and skills for each task
- 3
Communicate with the team to ensure alignment and understanding of priorities
- 4
Implement a flexible schedule that allows for quick adjustments
- 5
Monitor progress closely and be ready to reprioritize as needed
Example Answers
I would first analyze the orders to determine which have the tightest deadlines and highest customer impact. Then, I'd evaluate our available resources and team skills to ensure we allocate tasks effectively.
If quality control indicates that your last batch of slurry failed, what steps would you take to investigate?
How to Answer
- 1
Review the quality control report to understand failure specifics
- 2
Check raw material quality and inventory for any issues
- 3
Inspect the slurry mixing process for deviations from standard procedures
- 4
Conduct tests on the failed batch to identify failure points
- 5
Discuss findings with team members to gather additional insights
Example Answers
I would start by reviewing the quality control report to pinpoint what went wrong. Next, I would check the raw materials used in the batch for any quality issues. Then, I'd inspect the mixing process to see if there were any deviations from our standard operations.
If you are working on multiple batches of slurry, how would you effectively manage your time?
How to Answer
- 1
Prioritize batches based on deadlines and complexity.
- 2
Create a detailed timeline for each batch to track progress.
- 3
Use a checklist to monitor tasks for each batch.
- 4
Communicate regularly with the team to coordinate efforts.
- 5
Review and adjust your schedule as needed based on batch progress.
Example Answers
I would start by prioritizing the batches based on their deadlines. Then, I would create a timeline for each one, ensuring I allocate time for mixing, testing, and adjustments. A checklist would help me stay organized, and I would communicate regularly with my team to ensure we are all aligned.
Slurry Mixer Position Details
Recommended Job Boards
ZipRecruiter
www.ziprecruiter.com/Jobs/SlurryThese job boards are ranked by relevance for this position.
Related Positions
- Food Mixer
- Hand Mixer
- Spice Mixer
- Mud Worker
- Nut Grinder
- Seasoning Mixer
- Grinder
- Cement Worker
- Plasterer
- Syrup Maker
Similar positions you might be interested in.
Ace Your Next Interview!
Practice with AI feedback & get hired faster
Personalized feedback
Used by hundreds of successful candidates
Ace Your Next Interview!
Practice with AI feedback & get hired faster
Personalized feedback
Used by hundreds of successful candidates