Top 30 Sugar Controller Interview Questions and Answers [Updated 2025]
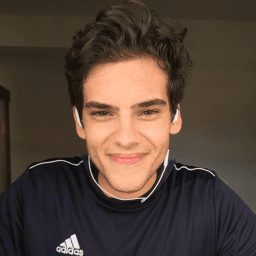
Andre Mendes
•
March 30, 2025
Preparing for a Sugar Controller interview can be daunting, but our updated guide for 2025 is here to help you succeed. This blog post compiles the most common interview questions for the Sugar Controller role, offering example answers and insightful tips for crafting your own responses. Whether you're new to the field or a seasoned professional, you'll find valuable guidance to navigate your interview with confidence.
Download Sugar Controller Interview Questions in PDF
To make your preparation even more convenient, we've compiled all these top Sugar Controllerinterview questions and answers into a handy PDF.
Click the button below to download the PDF and have easy access to these essential questions anytime, anywhere:
List of Sugar Controller Interview Questions
Behavioral Interview Questions
Can you tell us about a time you successfully collaborated with a team to improve sugar processing efficiencies?
How to Answer
- 1
Identify a specific project or situation where teamwork was key
- 2
Highlight your role and contributions to the team effort
- 3
Focus on the outcome and how it improved efficiencies
- 4
Use metrics or data to illustrate the success if possible
- 5
Mention any challenges faced and how they were overcome
Example Answers
In my previous role at XYZ Sugar Co., our team aimed to reduce processing time. I organized a brainstorming session where everyone shared their insights. By implementing a new scheduling system, we reduced downtime by 15%. This improvement saved the company significant costs and ensured smoother operations.
Describe a significant challenge you faced in sugar production and how you overcame it.
How to Answer
- 1
Identify a specific challenge related to sugar production processes or equipment.
- 2
Explain the context and impact of the challenge on production or quality.
- 3
Describe the steps you took to solve the problem, including collaboration with others if relevant.
- 4
Highlight any innovative solutions you implemented or lessons learned.
- 5
Conclude with the positive outcome and how it improved the operation.
Example Answers
In my previous role, we faced a serious issue with sugar crystallization that affected yield. I led a team to analyze the temperatures and syrup concentrations. By adjusting the cooling process and introducing a new crystallization agent, we improved yield by 15%. This not only resolved the immediate problem but also enhanced our production efficiency long-term.
Don't Just Read Sugar Controller Questions - Practice Answering Them!
Reading helps, but actual practice is what gets you hired. Our AI feedback system helps you improve your Sugar Controller interview answers in real-time.
Personalized feedback
Unlimited practice
Used by hundreds of successful candidates
Have you ever had to lead a team through a change in sugar quality standards? What was your approach?
How to Answer
- 1
Start by describing the situation and the need for change in standards.
- 2
Explain your role as a leader and how you communicated the changes to the team.
- 3
Discuss the steps you took to ensure the team adapted to the new standards.
- 4
Include any training or resources you provided to support the team.
- 5
Highlight the outcome and any improvements achieved after the change.
Example Answers
In my previous role, our facility needed to comply with new sugar quality regulations. I organized a team meeting to explain the upcoming changes and their importance. I developed a training program to help the team understand the new standards and conducted regular follow-ups to monitor progress. As a result, we not only met the compliance deadline but also improved our overall sugar quality by 15%.
Give an example of how you communicated complex sugar control metrics to a non-technical audience.
How to Answer
- 1
Identify the specific audience and their level of understanding.
- 2
Simplify complex metrics using analogies or relatable examples.
- 3
Use visual aids like charts or graphs to illustrate key points.
- 4
Encourage questions to clarify any confusion.
- 5
Summarize the key takeaways in clear, straightforward language.
Example Answers
In my previous role, I presented sugar control metrics to a group of dietitians. I used a graph to show trends over time and compared the data to daily activities. I explained it as 'our sugar levels are like a roller coaster, and we want to keep it steady, not going up and down too much.'
Tell us about a conflict you encountered with a colleague regarding sugar measurement protocols and how you resolved it.
How to Answer
- 1
Identify a specific incident involving conflicting views on protocols.
- 2
Explain the impact of the conflict on the team or results.
- 3
Outline the steps you took to resolve the issue through communication.
- 4
Highlight the positive outcome or learning from the resolution.
- 5
Keep your answer structured and focused on your role in the resolution.
Example Answers
In my previous role, I had a disagreement with a colleague about the frequency of calibrating sugar measurement equipment. It affected our accuracy readings. I proposed we meet to discuss our perspectives and consulted our supervisor for guidance. Ultimately, we agreed on a calibration schedule that satisfied both of us, which improved our accuracy in reporting.
Describe an instance where you took the initiative in a project related to sugar processing.
How to Answer
- 1
Identify a specific project you led or contributed to significantly
- 2
Quantify your contributions if possible with metrics or outcomes
- 3
Explain what motivated you to take initiative
- 4
Discuss any challenges you faced and how you overcame them
- 5
Conclude with the impact of your initiative on the team or project
Example Answers
In my last position, I noticed that our sugar extraction process was inefficient, leading to lower yields. I took the initiative to analyze the process and proposed a new method that improved the extraction efficiency by 15%, resulting in a significant increase in our monthly production.
Give an example of how you managed multiple deadlines while overseeing sugar control processes.
How to Answer
- 1
Identify key deadlines and prioritize tasks based on their impact on sugar control.
- 2
Communicate regularly with team members to ensure everyone is aligned on priorities.
- 3
Utilize project management tools to track progress and adjust timelines as needed.
- 4
Break down large tasks into smaller, manageable steps to avoid overwhelm.
- 5
Practice time management techniques to allocate time effectively for each task.
Example Answers
In my previous role, I oversaw multiple projects related to sugar quality testing, which all had overlapping deadlines. To manage this, I prioritized the tasks based on their critical impact on production schedules. I used a project management tool to set clear timelines and communicated regularly with my team to keep everyone informed, which helped us meet all deadlines successfully.
Can you provide an example of how you implemented feedback received from supervisors to improve sugar control?
How to Answer
- 1
Identify specific feedback received from your supervisor.
- 2
Describe how you analyzed the feedback and its impact.
- 3
Explain the steps you took to implement changes based on the feedback.
- 4
Highlight the outcome of those changes and any improvements seen.
- 5
Keep your answer focused and relevant to sugar control.
Example Answers
In my previous role, my supervisor noted that our patient follow-up process could be streamlined. I created a tracking system for patient glucose levels and follow-ups, which reduced missed appointments by 30% and improved our overall sugar control metrics.
Describe a time when you had to adapt quickly to changes in sugar industry regulations.
How to Answer
- 1
Identify a specific regulation change you encountered.
- 2
Explain your immediate response and action steps.
- 3
Highlight any collaboration with your team or stakeholders.
- 4
Discuss the outcome and any lessons learned.
- 5
Emphasize your ability to stay informed and proactive.
Example Answers
When the USDA announced new labeling requirements for sugar content, I organized a team meeting to assess our current packaging. We quickly redesigned the labels to ensure compliance while maintaining our branding. This quick action prevented potential fines and maintained our market reputation.
What motivates you to excel in your role as a Sugar Controller?
How to Answer
- 1
Identify personal passions related to sugar production and quality control.
- 2
Discuss the impact of your work on business success and customer satisfaction.
- 3
Mention teamwork and collaboration as motivators in achieving common goals.
- 4
Highlight a desire for continuous improvement and innovation in processes.
- 5
Share a personal story that connects your motivation with past successes.
Example Answers
I am passionate about ensuring high-quality sugar production because it directly affects the end product that customers enjoy. Knowing that my work contributes to the company’s reputation drives me to excel.
Don't Just Read Sugar Controller Questions - Practice Answering Them!
Reading helps, but actual practice is what gets you hired. Our AI feedback system helps you improve your Sugar Controller interview answers in real-time.
Personalized feedback
Unlimited practice
Used by hundreds of successful candidates
Technical Interview Questions
What methods do you use to determine sugar content during production?
How to Answer
- 1
Mention the use of Brix refractometers for measuring sugar concentration.
- 2
Discuss regular testing of sugar samples from different stages of production.
- 3
Explain the importance of inline sensors for real-time monitoring.
- 4
Highlight collaboration with quality assurance teams for accurate readings.
- 5
Consider the role of software tools for data analysis of sugar content.
Example Answers
I rely on Brix refractometers to gauge the sugar concentration in our syrups during production. I also take regular samples at various production stages to ensure consistency, and I collaborate with our quality assurance team for verification.
Can you describe your experience with chromatographic techniques in sugar analysis?
How to Answer
- 1
Focus on specific chromatographic methods you've used, such as HPLC or GC.
- 2
Mention any relevant software or instrumentation you have experience with.
- 3
Include details on how you've applied these techniques in actual projects.
- 4
Discuss any results or findings that relate to sugar analysis you contributed to.
- 5
Highlight any challenges you faced and how you overcame them.
Example Answers
I have extensive experience using HPLC for sugar analysis, specifically analyzing glucose and fructose in various samples. In my previous role, I ran over 200 tests using this technique and reported findings to our quality control team.
Don't Just Read Sugar Controller Questions - Practice Answering Them!
Reading helps, but actual practice is what gets you hired. Our AI feedback system helps you improve your Sugar Controller interview answers in real-time.
Personalized feedback
Unlimited practice
Used by hundreds of successful candidates
What quality control measures do you implement in sugar refining processes?
How to Answer
- 1
Explain specific quality control measures used at each stage of production.
- 2
Discuss the importance of regular sampling and testing.
- 3
Mention the use of standards and specifications to ensure quality.
- 4
Highlight the role of equipment maintenance in quality control.
- 5
Provide examples of addressing and solving quality issues.
Example Answers
In the sugar refining process, I implement measures such as regular sampling of raw sugar to check for purity levels. I also ensure that all machinery is maintained properly to avoid contamination.
What regulations and standards do you follow in your sugar processing operations?
How to Answer
- 1
Identify key regulations specific to the sugar industry such as food safety and environmental regulations.
- 2
Mention industry standards like ISO, HACCP, or FDA guidelines that apply to sugar processing.
- 3
Emphasize the importance of compliance with local and international standards to ensure quality and safety.
- 4
Provide examples of how you implement these regulations in daily operations.
- 5
Be prepared to discuss any audits or certifications your plant has achieved.
Example Answers
In my previous role, I ensured compliance with FDA regulations for food safety and quality, as well as HACCP standards. We conducted regular audits to maintain certifications and followed strict documentation procedures.
How do you utilize data analysis in monitoring sugar production efficiency?
How to Answer
- 1
Identify key performance indicators for sugar production.
- 2
Use historical data to establish benchmarks and trends.
- 3
Implement software tools to automate data collection.
- 4
Regularly conduct statistical analysis to spot inefficiencies.
- 5
Present findings with clear visuals to communicate insights.
Example Answers
I utilize data analysis by first identifying KPIs like extraction rates and purity levels. I analyze historical production data to set benchmarks and identify trends. This helps me see where improvements can be made.
Which software tools have you used for managing sugar production data and quality control?
How to Answer
- 1
Identify specific software you have hands-on experience with.
- 2
Mention any relevant features of these tools that aid in sugar production.
- 3
Relate your experience to data management and quality control processes.
- 4
Highlight any benefits you've observed from using these tools.
- 5
If applicable, discuss how you've integrated these tools into workflow.
Example Answers
I have used FactoryTalk and SCADA systems for managing production data. These tools help automate data collection and improve our quality control through real-time analysis.
What are the key stages in the sugar refining process that you are familiar with?
How to Answer
- 1
Start with the initial extraction of sugarcane or sugar beets
- 2
Describe the juicing or crushing process
- 3
Explain the purification method, including carbonation or phosphatation
- 4
Mention the crystallization stage where sugar crystals form
- 5
Conclude with the drying and packaging process
Example Answers
The sugar refining process begins with extracting juice from sugarcane or sugar beets. Next, the juice is purified, often using carbonation. After that, the juice is evaporated to form syrup and then crystallized. Finally, the crystals are dried and packaged for distribution.
What analytical tools do you use to assess changes in sugar quality throughout the production process?
How to Answer
- 1
Mention specific tools or software you are familiar with.
- 2
Explain how you use these tools in quality assessment.
- 3
Highlight any metrics you monitor regularly.
- 4
Discuss the importance of each tool in maintaining quality.
- 5
Provide an example of a successful assessment you conducted.
Example Answers
I often use HPLC and GC-MS for detailed sugar composition analysis. These tools help me monitor glucose and fructose levels throughout production, ensuring consistent quality. For instance, by analyzing samples at different stages, I can identify deviations early and adjust the process accordingly.
How do you incorporate sustainability practices into sugar production and processing?
How to Answer
- 1
Discuss the use of renewable energy sources in production.
- 2
Mention water conservation techniques implemented during processing.
- 3
Highlight waste reduction practices and recycling initiatives.
- 4
Explain the importance of sourcing sugar from sustainable farms.
- 5
Include any certifications or standards followed for sustainability.
Example Answers
I focus on using renewable energy, such as solar panels, to power processing facilities. Additionally, we have implemented water recycling systems to minimize usage during sugar extraction.
What recent advancements in sugar processing technology have you found most beneficial?
How to Answer
- 1
Research recent innovations in sugar processing such as automation and filtration.
- 2
Mention specific technologies like membrane technology or improved crystallization methods.
- 3
Relate advancements to efficiency improvements or cost reductions.
- 4
Use examples from industry case studies or notable companies.
- 5
Express enthusiasm for how these advancements impact sustainability and quality.
Example Answers
One of the most beneficial advancements I’ve seen is the use of membrane technology for sugar filtration, which greatly improves yield and reduces energy costs.
Don't Just Read Sugar Controller Questions - Practice Answering Them!
Reading helps, but actual practice is what gets you hired. Our AI feedback system helps you improve your Sugar Controller interview answers in real-time.
Personalized feedback
Unlimited practice
Used by hundreds of successful candidates
Situational Interview Questions
If you were to notice a drop in sugar yield, what steps would you take to investigate and rectify the issue?
How to Answer
- 1
Check production data for trends indicating the drop's onset
- 2
Inspect equipment for malfunction or inefficiency
- 3
Review raw material quality and consistency
- 4
Consult with team members for insights or observations
- 5
Implement changes based on findings and monitor results
Example Answers
I would start by reviewing the production data to pinpoint when the drop began. Then, I would check the equipment for any signs of malfunction. After that, I would review the raw materials for quality before consult with my team for further insights.
Imagine a scenario where the sugar crystallization process fails unexpectedly. How would you react?
How to Answer
- 1
Stay calm and assess the situation quickly
- 2
Identify the potential causes of the failure
- 3
Communicate the issue to your team promptly
- 4
Implement contingency plans or adjustments
- 5
Document the process and outcomes to prevent future issues
Example Answers
First, I would calm the team and gather all relevant data about the crystallization process. Then, I would analyze potential causes, like temperature fluctuations or impurities in the feedstock. After identifying the issue, I'd communicate with the team to devise a solution, such as adjusting the process parameters. Finally, I would document everything to improve our protocol for next time.
Don't Just Read Sugar Controller Questions - Practice Answering Them!
Reading helps, but actual practice is what gets you hired. Our AI feedback system helps you improve your Sugar Controller interview answers in real-time.
Personalized feedback
Unlimited practice
Used by hundreds of successful candidates
If faced with two different suppliers for raw sugar with varying costs and quality, how would you make your choice?
How to Answer
- 1
Evaluate the total cost including shipping and other fees.
- 2
Consider quality metrics such as purity and consistency.
- 3
Analyze the suppliers' reliability and delivery track records.
- 4
Assess the impact on production and customer satisfaction.
- 5
Negotiate terms that might make a more expensive option viable.
Example Answers
I would first calculate the total cost of each supplier including fees. Then, I would review quality reports to ensure the sugar meets our standards. If one supplier offers significantly better quality, it might justify a higher price, especially if it affects production efficiency.
What would you do if you identified non-compliance with safety protocols in the sugar production area?
How to Answer
- 1
Immediately assess the situation to understand the severity of the non-compliance
- 2
Notify your supervisor and relevant safety personnel without delay
- 3
Document the non-compliance and any actions taken on-site
- 4
Implement corrective actions where possible to mitigate risks
- 5
Follow up to ensure that the safety protocols are reinstated and maintained
Example Answers
If I identified non-compliance with safety protocols, I would quickly assess how serious the issue is. Then I would inform my supervisor and safety officer right away. I’d document what I found and take any immediate corrective actions I could manage, like isolating the risky area, while ensuring it gets fully resolved after.
How would you handle a situation where your team disagrees on the best method to optimize sugar extraction?
How to Answer
- 1
Encourage open discussion to understand all perspectives
- 2
Propose a structured approach to evaluate each method
- 3
Use data and past results to make informed decisions
- 4
Facilitate a consensus-building session to find common ground
- 5
Highlight the importance of team collaboration and learning
Example Answers
I would start by inviting each team member to share their method and rationale, ensuring everyone feels heard. Then, I would suggest that we evaluate the methods based on data from past extractions to see which has proven most effective. This way, we can make a decision grounded in evidence.
If you were tasked with reducing production costs while maintaining sugar quality, what strategies would you employ?
How to Answer
- 1
Analyze the current production process for inefficiencies.
- 2
Invest in technology that automates processes to reduce labor costs.
- 3
Negotiate better pricing with suppliers for raw materials.
- 4
Implement regular quality control to prevent costly reworks.
- 5
Explore alternative methods or ingredients that maintain quality at lower costs.
Example Answers
I would start by analyzing the entire production process to identify any inefficiencies, then invest in automation technology to reduce labor costs. Simultaneously, I would negotiate with suppliers for better prices and ensure regular quality control to avoid expensive product reworks.
What approach would you take to train new team members on the sugar control processes?
How to Answer
- 1
Start with an overview of the sugar control processes and their importance.
- 2
Utilize hands-on training with real-life scenarios to demonstrate concepts.
- 3
Provide access to detailed documentation and resources for self-study.
- 4
Encourage questions and discussions to clarify understanding.
- 5
Schedule regular follow-ups to assess progress and address any challenges.
Example Answers
I would begin by giving a brief overview of our sugar control processes and explain why they are crucial for our operations. Then, I'd conduct hands-on training where new team members can work through real scenarios. I would also provide them with access to our documentation for further reading and encourage them to ask questions throughout.
How would you handle a situation where a customer complains about the quality of the sugar supplied?
How to Answer
- 1
Listen carefully to the customer's complaint and show empathy.
- 2
Ask for specific details about the quality issue and document them.
- 3
Examine the quality control reports and gather relevant facts.
- 4
Propose a solution, such as a replacement or refund, based on company policy.
- 5
Follow up with the customer to ensure their satisfaction with the resolution.
Example Answers
I would first listen to the customer's complaint attentively and acknowledge their concerns. I would then ask specific questions to understand the quality issue they experienced. After gathering the information, I would check the quality control documentation. If the complaint is valid, I would offer a replacement or refund, as per our policy. I would make sure to follow up afterward to confirm they are satisfied with the resolution.
If you needed to collaborate with the marketing team to promote a new sugar product, what information would you provide?
How to Answer
- 1
Identify key selling points of the product like taste, health benefits, and versatility.
- 2
Provide data on target demographics and market trends for sugar products.
- 3
Suggest potential marketing channels that align with the brand identity, such as social media or in-store promotions.
- 4
Offer insights on packaging and labeling regulations for food products.
- 5
Prepare samples or product demos for marketing to use in campaigns.
Example Answers
I would share the product's unique attributes such as its low-calorie sweetness and natural ingredients, along with data showing the trend towards healthier sugar alternatives among consumers.
How would you analyze the impact of a major supplier change on sugar quality and production timelines?
How to Answer
- 1
Identify key quality parameters affected by supplier change.
- 2
Assess historical data on supplier performance regarding quality.
- 3
Engage with both the production team and quality control to gather insights.
- 4
Consider logistical changes and lead times from the new supplier.
- 5
Perform a risk assessment to identify potential issues in production timelines.
Example Answers
To analyze the impact of a supplier change, I would first look at key quality parameters like sweetness, moisture, and color. Then, I would review historical data on the previous supplier's quality metrics. Engaging with production and quality control would help me understand any specific concerns they have. Additionally, I would evaluate the new supplier's lead times and delivery reliability to gauge any changes in our production timelines. Finally, I would conduct a risk assessment to highlight potential challenges.
Don't Just Read Sugar Controller Questions - Practice Answering Them!
Reading helps, but actual practice is what gets you hired. Our AI feedback system helps you improve your Sugar Controller interview answers in real-time.
Personalized feedback
Unlimited practice
Used by hundreds of successful candidates
Sugar Controller Position Details
Related Positions
- Sugar Refiner
- Cake Wrapper
- Syrup Maker
- Spring Layer
- Spinner Operator
- Seasoner
- Buttoner
- Cake Stripper
- Storage Worker
- Color Developer
Similar positions you might be interested in.
Ace Your Next Interview!
Practice with AI feedback & get hired faster
Personalized feedback
Used by hundreds of successful candidates
Ace Your Next Interview!
Practice with AI feedback & get hired faster
Personalized feedback
Used by hundreds of successful candidates