Top 30 Tool Changer Interview Questions and Answers [Updated 2025]
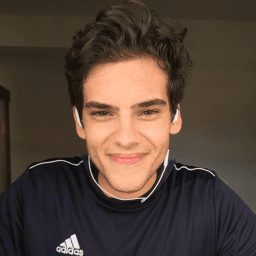
Andre Mendes
•
March 30, 2025
Preparing for a Tool Changer interview? You've come to the right place! This blog post features the most common interview questions for the Tool Changer role, complete with example answers and effective answering tips. Whether you're a seasoned professional or new to the field, this guide will help you showcase your skills and land the job. Dive in to enhance your interview readiness!
Download Tool Changer Interview Questions in PDF
To make your preparation even more convenient, we've compiled all these top Tool Changerinterview questions and answers into a handy PDF.
Click the button below to download the PDF and have easy access to these essential questions anytime, anywhere:
List of Tool Changer Interview Questions
Behavioral Interview Questions
Can you describe a time when you successfully implemented a new tool into a production process?
How to Answer
- 1
Identify the specific tool you implemented
- 2
Explain the problem it addressed in the production process
- 3
Describe the steps you took to implement the tool
- 4
Highlight the results and benefits gained from the implementation
- 5
Mention any challenges faced and how you overcame them
Example Answers
In my previous role, I implemented an automated torque wrench that reduced assembly time by 30%. The existing manual process was slow and error-prone. I researched the tool, trained the team, and integrated it into our workflow. This significantly improved accuracy and efficiency, resulting in fewer returns due to assembly mistakes.
Tell me about a situation where you faced a malfunctioning tool. How did you address the issue?
How to Answer
- 1
Describe the specific tool and the malfunction you encountered.
- 2
Explain the steps you took to diagnose the problem.
- 3
Discuss how you resolved the issue effectively.
- 4
Highlight any preventative measures you implemented afterward.
- 5
Reflect on what you learned from the experience.
Example Answers
In my previous role as a technician, I dealt with a robotic arm that was not picking up tools correctly. I first checked the calibration settings and found they were off. I recalibrated the arm and tested it, which resolved the issue. Afterward, I documented the procedure to ensure future calibration checks were performed regularly, preventing similar problems.
Don't Just Read Tool Changer Questions - Practice Answering Them!
Reading helps, but actual practice is what gets you hired. Our AI feedback system helps you improve your Tool Changer interview answers in real-time.
Personalized feedback
Unlimited practice
Used by hundreds of successful candidates
Describe a time when you worked closely with a team to improve tool efficiency. What was your role?
How to Answer
- 1
Think of a specific project where you collaborated with others.
- 2
Highlight your specific contributions to the team.
- 3
Mention measurable outcomes or improvements achieved.
- 4
Describe how you communicated and coordinated with team members.
- 5
Reflect on any challenges faced and how the team overcame them.
Example Answers
In my last job, we had an issue with tool change times. As the lead technician, I organized a team meeting to analyze our processes. I suggested standardizing the tool setup, which reduced our changeover time by 30%. We used a tracking sheet to monitor improvements and communicated weekly to ensure we stayed on track.
Have you ever had to explain a complex tool change process to someone unfamiliar with it? How did you do it?
How to Answer
- 1
Start with the basic concept of tool changing.
- 2
Break down the process into simple, clear steps.
- 3
Use analogies to relate to something the person understands.
- 4
Encourage questions to ensure understanding.
- 5
Summarize the process at the end to reinforce key points.
Example Answers
Yes, I explained the tool change process while training a new team member. I started by outlining what a tool change is and then broke it into four simple steps: removing the old tool, installing the new tool, calibrating it, and testing it. I used the analogy of changing a car tire to illustrate each step, making it relatable. I also paused for questions to clarify any confusion.
Can you provide an example of when you had to quickly adapt to a change in tooling specifications?
How to Answer
- 1
Think of a specific situation where tooling changed suddenly
- 2
Describe the change clearly and its impact on the process
- 3
Explain the steps you took to adapt to the new specifications
- 4
Highlight any positive outcomes from your adaptation
- 5
Keep it concise and focused on your role and actions
Example Answers
In my last role, we had a last-minute change in the specifications for a tool due to a new material. I quickly reviewed the new requirements, consulted with the engineering team, and reprogrammed the CNC machine to accommodate the changes. This allowed us to meet the production deadline without delays.
What is a key lesson you learned from a mistake made while changing tools?
How to Answer
- 1
Choose a specific mistake that is relevant to tool changing.
- 2
Focus on the lesson learned from the experience.
- 3
Explain how you applied this lesson in future tool changes.
- 4
Keep the answer focused and concise.
- 5
Only discuss solutions, not just the problem.
Example Answers
Once, I forgot to secure a tool properly, which caused delays. I learned to always double-check my tools before starting. Now, I have a checklist that ensures everything is locked in place.
How do you incorporate feedback from your team regarding tool changes?
How to Answer
- 1
Encourage open communication and create a safe environment for feedback
- 2
Actively listen to team members' suggestions and concerns about tools
- 3
Analyze the feedback and assess its impact on productivity and efficiency
- 4
Collaborate with the team to pilot changes or implement suggestions
- 5
Follow up after changes to gather further feedback on the new tools
Example Answers
I make it a point to encourage my team to share their thoughts on tool usage. I listen to their feedback and evaluate it based on our workflow. If their suggestions seem beneficial, I propose pilot testing those changes.
What strategies do you use to set goals for tool performance and efficiency?
How to Answer
- 1
Analyze historical performance data to identify trends.
- 2
Set SMART goals: Specific, Measurable, Achievable, Relevant, Time-bound.
- 3
Implement regular maintenance schedules to ensure optimal tool performance.
- 4
Engage with team feedback to adjust goals based on real-world usage.
- 5
Use benchmarking against industry standards to evaluate performance expectations.
Example Answers
I analyze past performance data to identify areas for improvement. This helps me set SMART goals that are both measurable and achievable, ensuring that our targets are aligned with actual tool usage.
Describe your experience in training colleagues on using specific tools.
How to Answer
- 1
Start with a specific example of a tool you trained others on.
- 2
Explain the context – why training was needed and who your audience was.
- 3
Describe your training approach and methods used.
- 4
Highlight any positive outcomes or feedback from the training.
- 5
Keep it concise and focused on your impact.
Example Answers
I trained my team on using the new ERP software last year because we needed to improve our inventory management. I created a step-by-step guide and held a workshop. The feedback was positive, with most of my colleagues reporting increased efficiency in their tasks.
Don't Just Read Tool Changer Questions - Practice Answering Them!
Reading helps, but actual practice is what gets you hired. Our AI feedback system helps you improve your Tool Changer interview answers in real-time.
Personalized feedback
Unlimited practice
Used by hundreds of successful candidates
Technical Interview Questions
What are the essential tools you have experience with in a manufacturing environment?
How to Answer
- 1
Identify specific tools relevant to tool changers like robotic arms, grippers, and CNC machines.
- 2
Mention your experience level with each tool, such as beginner, intermediate, or expert.
- 3
Explain how you have used these tools to improve efficiency or solve problems.
- 4
Include any certifications or training related to these tools to strengthen your answer.
- 5
Be prepared to give examples of projects or tasks where you successfully used these tools.
Example Answers
I have extensive experience with robotic arms and pneumatic grippers, having used them in assembly lines to improve cycle times by 20%.
How do you conduct regular maintenance checks on tools to ensure their functionality?
How to Answer
- 1
Establish a regular maintenance schedule for each tool based on usage frequency.
- 2
Inspect tools visually for any signs of wear or damage before each use.
- 3
Clean tools thoroughly after each use to prevent buildup that affects performance.
- 4
Test the functionality of tools periodically with a performance check or calibration if needed.
- 5
Document any findings and repairs in a maintenance log for future reference.
Example Answers
I conduct maintenance on tools by establishing a weekly schedule where I visually inspect them for wear and tear, cleaning them after each use to keep them in top condition.
Don't Just Read Tool Changer Questions - Practice Answering Them!
Reading helps, but actual practice is what gets you hired. Our AI feedback system helps you improve your Tool Changer interview answers in real-time.
Personalized feedback
Unlimited practice
Used by hundreds of successful candidates
What safety protocols do you follow when changing tools on a machine?
How to Answer
- 1
Ensure machine is powered down before starting tool change.
- 2
Use appropriate personal protective equipment (PPE) like gloves and goggles.
- 3
Follow the manufacturer's instructions for tool replacement.
- 4
Inspect the tool and machine for wear or damage before changing.
- 5
Keep the work area clean and free of hazards during the process.
Example Answers
I always start by powering down the machine and ensuring it's locked out. Then, I put on my gloves and goggles. I follow the manufacturer's guide for safely replacing the tool and inspect both the tool and the machine for any wear. Lastly, I make sure my workspace is organized and clear of any obstacles.
What is your process for calibrating tools to meet production requirements?
How to Answer
- 1
Identify the specifications for the tools needed in production
- 2
Use precise measuring instruments to assess tool performance
- 3
Adjust the tools based on initial measurements and specifications
- 4
Document the calibration process and results for future reference
- 5
Regularly verify tools against production standards
Example Answers
First, I review the production requirements to determine the necessary tool specifications. Then, I use calipers and gauges to measure the tools' dimensions and performance. Based on these measurements, I make necessary adjustments to the tools. After calibration, I keep a record of all adjustments made for quality assurance.
How familiar are you with software used to track tooling and production metrics?
How to Answer
- 1
Mention specific software you've used related to tooling and metrics.
- 2
Discuss how you utilized the software to improve production efficiency.
- 3
Share any experiences of data analysis and reporting using these tools.
- 4
Highlight any certifications or training in relevant software.
- 5
Emphasize your willingness to learn new software quickly if needed.
Example Answers
I have used software like SAP and Oracle for tracking tooling and production metrics. In my previous role, I implemented a new reporting tool that reduced downtime by 15% by analyzing equipment performance data.
Can you discuss how different materials affect the choice of tools?
How to Answer
- 1
Identify key materials and their properties like hardness and abrasiveness
- 2
Explain how these properties influence tool wear and selection
- 3
Mention specific tool types suitable for different materials
- 4
Discuss the importance of matching tool coatings to material types
- 5
Illustrate with examples from personal experience or industry standards
Example Answers
Different materials have unique properties like hardness and friction. For instance, when working with steel, I would choose high-speed steel tools for durability, while for softer materials like plastic, I would opt for carbide-tipped tools to reduce wear. Coatings also play a role; titanium nitride coating is great for abrasive materials.
How do you measure the performance of a tool after a change?
How to Answer
- 1
Establish clear performance metrics before the change.
- 2
Compare the tool's output to baseline data.
- 3
Monitor key indicators like speed, accuracy, and reliability.
- 4
Gather feedback from users after the change implementation.
- 5
Document any improvements or regressions in performance.
Example Answers
I measure performance by setting specific metrics like speed and accuracy prior to changes, then I compare post-change data against these baselines to see any improvements.
Explain your experience with modifying tools for specific applications.
How to Answer
- 1
Mention specific tools you have modified and the application context.
- 2
Describe the steps you took to modify the tools.
- 3
Highlight any challenges faced during the modification process.
- 4
Discuss the impact of your modifications on performance or efficiency.
- 5
Use quantifiable results if possible to demonstrate success.
Example Answers
In my previous position, I modified a robotic arm tool changer by adjusting the gripping strength for precise handling of sensitive components. This involved recalibrating the sensors based on weight tests, and as a result, we improved our production yield by 15%.
What standard practices do you follow for tool handling and maintenance?
How to Answer
- 1
Always inspect tools for damage before use.
- 2
Keep tools clean and stored properly after each use.
- 3
Use the correct tool for the specific job to prevent wear.
- 4
Regularly calibrate and service tools according to manufacturer guidelines.
- 5
Document tool usage and maintenance to track history and performance.
Example Answers
I inspect each tool for any wear or damage before using it, and I always clean and store them properly right after each job.
Don't Just Read Tool Changer Questions - Practice Answering Them!
Reading helps, but actual practice is what gets you hired. Our AI feedback system helps you improve your Tool Changer interview answers in real-time.
Personalized feedback
Unlimited practice
Used by hundreds of successful candidates
Situational Interview Questions
If resources for tool changes are limited, how would you maximize productivity?
How to Answer
- 1
Prioritize tool changes based on production demand.
- 2
Implement a schedule for tool maintenance and changes to reduce downtime.
- 3
Utilize quick-change tooling systems to minimize time spent on changes.
- 4
Streamline the number of tools to only essential ones to simplify the process.
- 5
Train staff thoroughly on efficient tool handling and changeover techniques.
Example Answers
I would prioritize tool changes based on the production schedule, ensuring we always have the necessary tools for the most critical tasks. Additionally, I would implement regular maintenance checks to avoid unexpected breakdowns and use quick-change systems for efficiency.
If you had multiple tools that needed changing at the same time, how would you prioritize your work?
How to Answer
- 1
Assess the urgency and importance of each tool task
- 2
Identify which tools impact production or safety the most
- 3
Consider the time required for each tool change
- 4
Communicate with team members to ensure coordination
- 5
Plan to change the tools that offer the biggest efficiency boost first
Example Answers
I would first evaluate which tool changes are critical for ongoing operations and prioritize those. I'd also take into account how quickly I can change each tool to minimize downtime.
Don't Just Read Tool Changer Questions - Practice Answering Them!
Reading helps, but actual practice is what gets you hired. Our AI feedback system helps you improve your Tool Changer interview answers in real-time.
Personalized feedback
Unlimited practice
Used by hundreds of successful candidates
If you disagreed with a team member about the best tool for a specific job, how would you handle it?
How to Answer
- 1
Listen to your team member's reasoning and show respect for their opinion.
- 2
Present your own perspective clearly and back it with data or experience.
- 3
Suggest a trial run with both tools to see which performs better.
- 4
Encourage a collaborative decision by involving the whole team.
- 5
Focus on the goal of achieving the best outcome for the job.
Example Answers
I would first listen to my teammate's reasoning for their tool choice, making sure to understand their perspective. Then, I would share my insights and experiences with the alternative tool I suggest, showing any relevant data. If we still disagree, I would propose a trial run with both tools to evaluate which one works better.
You have a tight deadline but a critical tool is malfunctioning. What steps would you take?
How to Answer
- 1
Assess the tool to identify the specific malfunction.
- 2
Determine if a temporary workaround can help meet the deadline.
- 3
Communicate with your team about the issue and potential impacts.
- 4
Prioritize tasks that can be completed while resolving the tool issue.
- 5
Seek immediate assistance from a technician if necessary.
Example Answers
First, I would examine the tool to pinpoint the malfunction. Then, I would check if there's a simple workaround to use while fixing it. I'll inform my team about the situation and adjust our priorities to focus on tasks we can complete without the tool.
If a tool change delays production, how would you communicate this to stakeholders?
How to Answer
- 1
Be clear and concise when stating the reason for the delay.
- 2
Use data to explain the impact on production timelines.
- 3
Provide potential solutions or next steps to mitigate the delay.
- 4
Communicate promptly to maintain transparency.
- 5
Offer to update stakeholders regularly on progress.
Example Answers
I would inform stakeholders immediately about the tool change and explain that it caused a delay due to its necessity in ensuring quality. I would provide updated timelines and suggest reallocating resources to minimize the impact.
A newer team member is struggling with tool changes. How would you assist them?
How to Answer
- 1
Offer to demonstrate the tool change process step by step.
- 2
Provide a clear and easy-to-follow checklist or guide.
- 3
Encourage questions and create a supportive environment.
- 4
Suggest they practice the tool change with your supervision.
- 5
Follow up after a few attempts to see how they are progressing.
Example Answers
I would first demonstrate the tool change process while explaining each step to ensure they understand. Then, I would provide them with a checklist to follow along.
What would you do in an emergency situation where an important tool breaks unexpectedly?
How to Answer
- 1
Stay calm and assess the situation quickly
- 2
Identify the tool's importance and impact on operations
- 3
Communicate with your team about the issue immediately
- 4
Look for any available backup tools or alternatives
- 5
Follow up with a plan to repair or replace the broken tool
Example Answers
If a crucial tool broke, I would first remain calm to assess the situation. I would inform my team immediately about the breakdown and determine if we have similar tools available to continue our work. Meanwhile, I would document the issue for future reference and work on arranging repairs as quickly as possible.
How would you handle a situation where a tool change affects product quality?
How to Answer
- 1
Identify the specific quality issues caused by the tool change
- 2
Communicate with the team about the impact of the tool change
- 3
Implement a quality control process to monitor the changes
- 4
Suggest adjustments to the tool or process to mitigate quality loss
- 5
Document the findings and create a plan for future tool changes
Example Answers
First, I would pinpoint the exact quality issues, then discuss them with the team to understand everyone's perspective. I would implement a quality monitoring system to catch any deviations early and suggest modifications to either the tool or the process to fix these problems promptly. Finally, I would document everything to ensure we learn from this situation.
If a tool change went wrong, what kind of report would you produce?
How to Answer
- 1
Identify the specifics of the tool change issue.
- 2
Include details such as time and date of the failure.
- 3
Document the impact on production and any delays caused.
- 4
Suggest corrective actions based on your analysis.
- 5
Keep the report factual and objective.
Example Answers
I would produce a report that details the tool change error, including the date and time of the incident, the specific tools involved, and the impact on production schedules. I would include recommendations for improving the tool change process.
If faced with budget cuts, how would you manage tool-related costs?
How to Answer
- 1
Evaluate current tool usage to identify underutilized tools
- 2
Negotiate with suppliers for better pricing or bulk discounts
- 3
Implement a preventative maintenance program to reduce tool failures
- 4
Train staff on best practices to prolong tool life
- 5
Consider renting tools instead of purchasing for short-term needs
Example Answers
I would start by assessing our current tools to see if any are underutilized and could be eliminated. Additionally, I would reach out to suppliers to negotiate better prices or consider bulk purchasing to cut costs.
Don't Just Read Tool Changer Questions - Practice Answering Them!
Reading helps, but actual practice is what gets you hired. Our AI feedback system helps you improve your Tool Changer interview answers in real-time.
Personalized feedback
Unlimited practice
Used by hundreds of successful candidates
Tool Changer Position Details
Recommended Job Boards
CareerBuilder
www.careerbuilder.com/jobs-tool-changerZipRecruiter
www.ziprecruiter.com/Jobs/Tool-Changer/These job boards are ranked by relevance for this position.
Related Positions
- Cell Changer
- Tool Master
- Tool Technician
- Transformer Mechanic
- Battery Mechanic
- Tool Inspector
- Battery Repairer
- Battery Inspector
- Motor Rebuilder
- Saw Repairer
Similar positions you might be interested in.
Ace Your Next Interview!
Practice with AI feedback & get hired faster
Personalized feedback
Used by hundreds of successful candidates
Ace Your Next Interview!
Practice with AI feedback & get hired faster
Personalized feedback
Used by hundreds of successful candidates