Top 27 Tractor Mechanic Interview Questions and Answers [Updated 2025]
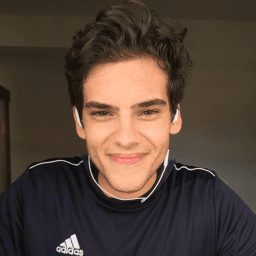
Andre Mendes
•
March 30, 2025
Embarking on a career as a tractor mechanic? This blog post equips you with the most common interview questions tailored for this specialized role. Dive into expertly crafted example answers and insightful tips designed to help you respond effectively and confidently. Whether you're a seasoned pro or just starting out, this guide is your roadmap to acing your next tractor mechanic interview.
Download Tractor Mechanic Interview Questions in PDF
To make your preparation even more convenient, we've compiled all these top Tractor Mechanicinterview questions and answers into a handy PDF.
Click the button below to download the PDF and have easy access to these essential questions anytime, anywhere:
List of Tractor Mechanic Interview Questions
Behavioral Interview Questions
Can you describe a time when you diagnosed a complex issue with a tractor? What steps did you take to resolve it?
How to Answer
- 1
Start with a specific example of a complex issue.
- 2
Explain how you identified the problem using systematic methods.
- 3
Detail the steps you took to troubleshoot and fix the issue.
- 4
Mention any tools or techniques that were particularly helpful.
- 5
Reflect on the outcome and what you learned from the experience.
Example Answers
I once dealt with a tractor that wouldn't start. I systematically checked the battery, ignition system, and fuel supply. Using a multimeter, I identified a faulty ignition coil. I replaced the coil and tested the system which resolved the issue, and I learned more about the ignition circuitry.
Tell me about a time you worked in a team to complete a major repair project on a tractor. What role did you play?
How to Answer
- 1
Choose a specific project that highlights teamwork.
- 2
Describe your role and responsibilities clearly.
- 3
Focus on communication and collaboration with team members.
- 4
Mention any challenges faced and how the team overcame them.
- 5
Highlight the positive outcome and what you learned from the experience.
Example Answers
In a recent project, our team worked on overhauling an old tractor. I was the lead mechanic responsible for engine repair. We divided tasks, and I coordinated with others to ensure we stayed on schedule. We faced a delay due to missing parts, but I communicated with suppliers to expedite the order. We completed the project on time, and the tractor ran better than expected.
Don't Just Read Tractor Mechanic Questions - Practice Answering Them!
Reading helps, but actual practice is what gets you hired. Our AI feedback system helps you improve your Tractor Mechanic interview answers in real-time.
Personalized feedback
Unlimited practice
Used by hundreds of successful candidates
Describe an instance when you had to explain a technical issue to a non-technical customer. How did you ensure they understood?
How to Answer
- 1
Use simple language and avoid jargon
- 2
Relate the issue to a real-world analogy
- 3
Be patient and encourage questions
- 4
Check for understanding by summarizing key points
- 5
Offer a follow-up resource if available
Example Answers
I explained a broken hydraulic system to a farmer by comparing it to a garden hose. I showed him how clogs in the hose can stop water flow, just like blockages can affect the hydraulic system. I encouraged him to ask questions and verified his understanding by asking him to summarize the issue back to me.
Give an example of how you prioritized multiple tractor repair jobs. What factors influenced your decisions?
How to Answer
- 1
Assess the urgency of each job based on customer needs or deadlines
- 2
Consider the complexity of each repair and required parts availability
- 3
Evaluate the potential impact on the overall operation or farm productivity
- 4
Communicate with team members about workload and deadlines
- 5
Use a systematic approach, like a prioritization matrix, if necessary
Example Answers
In a recent situation, I had three tractors needing repair: one had a hydraulic issue affecting a customer's harvest, another was scheduled for preventive maintenance, and the third needed a minor engine tune-up. I prioritized the hydraulic issue first due to its immediate impact on productivity, then scheduled the preventive maintenance next to prevent future breakdowns, leaving the minor tune-up for later.
Can you provide an example of a disagreement you had with a team member on how to fix a tractor? How did you resolve it?
How to Answer
- 1
Identify the disagreement clearly and state each viewpoint.
- 2
Explain the reasoning behind your position and listen to the other person's arguments.
- 3
Suggest a compromise or a collaborative solution that takes both opinions into account.
- 4
Highlight the importance of teamwork and communication in resolving the conflict.
- 5
Conclude with the outcome and what you learned from the experience.
Example Answers
I had a disagreement with a colleague about whether to replace the tractor battery or just recharge it. I believed replacing it was necessary due to its age. We discussed both options, weighing cost and efficiency. Together, we decided to test the battery first before replacing it. This approach saved resources and improved our decision-making process.
What has been your most satisfying repair project on a tractor, and why did it resonate with you?
How to Answer
- 1
Select a specific repair project with a positive outcome
- 2
Explain the challenges faced during the repair
- 3
Highlight your problem-solving skills and techniques used
- 4
Discuss the impact of the repair on the equipment's performance
- 5
Share how the experience affected your growth as a mechanic
Example Answers
One satisfying project was when I overhauled a tractor engine that was losing power. The challenge was diagnosing a faulty fuel pump, which took time. After I replaced it, the tractor ran like new, improving efficiency for the farmer. This experience boosted my confidence in tackling complex mechanical issues.
Describe a time when you made a mistake while working on a tractor. How did you handle it and what did you learn?
How to Answer
- 1
Be honest about the mistake you made
- 2
Explain the steps you took to correct it
- 3
Highlight what you learned from the experience
- 4
Keep it focused on the tractor work
- 5
Show how it improved your skills or processes
Example Answers
Once, I accidentally misdiagnosed a fuel issue on a tractor, thinking it was an electrical problem. I noticed the engine still wouldn't start after replacing the battery. I double-checked the fuel lines and discovered a clogged filter. I learned the importance of systematic troubleshooting and now always follow a specific diagnostic checklist first.
Technical Interview Questions
What are the common signs of engine failure in tractors, and how would you diagnose the issue?
How to Answer
- 1
Identify key symptoms like unusual noises, smoke, and loss of power.
- 2
Check for fluid leaks and overheating.
- 3
Use diagnostic tools to read error codes if available.
- 4
Inspect fuel, air, and oil filters for clogs.
- 5
Conduct tests on compression and ignition systems.
Example Answers
Common signs of engine failure include strange noises, excessive smoke, and the engine losing power. To diagnose, I would first check for fluid leaks, then listen for abnormal sounds while inspecting the cooling system for overheating.
Can you explain how a tractor's hydraulic system works and how you would troubleshoot a malfunctioning hydraulic component?
How to Answer
- 1
Start by briefly defining the hydraulic system and its main components.
- 2
Explain the basic working principle of hydraulics using fluid power.
- 3
Describe common issues that can occur in hydraulic systems.
- 4
Outline a step-by-step troubleshooting process, focusing on diagnostics.
- 5
Mention safety measures when working with hydraulic systems.
Example Answers
The hydraulic system uses fluid to transfer power through hoses and cylinders, helping operate implements. If I notice slow or no movement in a hydraulic cylinder, I'd first check fluid levels and inspect for leaks before testing the system pressure.
Don't Just Read Tractor Mechanic Questions - Practice Answering Them!
Reading helps, but actual practice is what gets you hired. Our AI feedback system helps you improve your Tractor Mechanic interview answers in real-time.
Personalized feedback
Unlimited practice
Used by hundreds of successful candidates
What steps would you take to diagnose an electrical problem in a tractor, such as failure of the starter motor?
How to Answer
- 1
Check the battery condition and connections for corrosion or looseness
- 2
Test the starter solenoid to see if it engages when you turn the ignition
- 3
Inspect the wiring for any signs of damage or breaks
- 4
Use a multimeter to measure voltage at the starter and battery
- 5
Look for any blown fuses or circuit issues that may affect starting
Example Answers
First, I would check the battery and its connections for corrosion. Then, I would test the starter solenoid to ensure it's functioning. Next, I would inspect the wiring for damage and measure voltage using a multimeter.
What routine maintenance tasks do you believe are essential for keeping tractors in optimal working condition?
How to Answer
- 1
Highlight the importance of regular oil changes and fluid checks
- 2
Include checking tire pressure and tread for safety and efficiency
- 3
Mention the need to inspect and clean filters regularly
- 4
Discuss the importance of greasing moving parts to reduce wear
- 5
Talk about checking and maintaining battery health
Example Answers
I believe regular oil changes and checking fluids are crucial for engine longevity. Also, ensuring the tires are properly inflated and have good tread can improve fuel efficiency and safety.
What safety precautions do you follow while performing repairs on tractors, especially regarding heavy machinery?
How to Answer
- 1
Always wear appropriate personal protective equipment like gloves, goggles, and steel-toed boots.
- 2
Ensure the tractor is turned off and properly secured before starting any repairs.
- 3
Use jack stands to support the tractor when working underneath or lifting any heavy components.
- 4
Keep the work area clean and free of clutter to avoid accidents.
- 5
Be aware of the hydraulic systems and relieve pressure before working on those components.
Example Answers
I always wear gloves, goggles, and steel-toed boots to protect myself. I make sure the tractor is off and secured, using jack stands when needed. I keep the area tidy to prevent tripping hazards.
What specific tools do you consider essential for a tractor mechanic, and how do you select the right tool for a job?
How to Answer
- 1
Identify key tools specific to tractor mechanics, such as wrenches and diagnostic equipment.
- 2
Explain how you assess the job's requirements before tool selection.
- 3
Mention the importance of tool maintenance and readiness.
- 4
Discuss the benefits of having a diverse toolset for various tasks.
- 5
Highlight any personal experiences where your tool choice made a difference.
Example Answers
I consider hand wrenches, socket sets, and diagnostic scanners essential. For each job, I review the task requirements, ensuring I select the most effective tool while also keeping my equipment well-maintained to avoid delays.
What are the key components of a tractor's powertrain, and how do you assure they function properly during inspections?
How to Answer
- 1
Identify key powertrain components like the engine, transmission, drive shafts, and differential.
- 2
Discuss specific inspection techniques for each component, such as checking fluid levels and looking for leaks.
- 3
Mention the importance of listening for unusual noises during operation.
- 4
Highlight the role of regular maintenance in ensuring reliability.
- 5
Emphasize documenting findings for future reference and repairs.
Example Answers
The main components of a tractor's powertrain include the engine, transmission, drive shafts, and differential. During inspections, I check fluid levels, look for leaks, and listen for unusual noises. Regular maintenance is also critical to catch issues early.
What process do you follow for diagnosing and repairing issues with tractor tires?
How to Answer
- 1
Start with a visual inspection of the tire for damage or wear.
- 2
Check tire pressure and ensure it meets the manufacturer's specifications.
- 3
Look for uneven wear patterns to identify alignment or mechanical issues.
- 4
Perform a tread depth measurement to assess tire health.
- 5
Document findings and suggest appropriate repairs or replacements.
Example Answers
I begin with a visual inspection for cuts or cracks, then check the tire pressure and adjust it as needed. I look for uneven wear patterns to diagnose potential alignment issues, and I always measure tread depth to determine if a replacement is necessary.
How would you troubleshoot a cooling system problem in a tractor that's overheating?
How to Answer
- 1
Check the coolant level and top off if necessary
- 2
Inspect for leaks in hoses or radiator
- 3
Test the thermostat functionality and replace if stuck
- 4
Examine the water pump for proper operation
- 5
Look for blockages in the radiator or cooling fins
Example Answers
First, I would check the coolant level and add more if it's low. Next, I'd inspect all hoses for any leaks. If that checks out, I would test the thermostat to ensure it's functioning correctly. After that, I would look at the water pump to make sure it's not faulty, and finally, I would clear any blockages in the radiator.
How do you approach warranty repairs on tractors, ensuring compliance with manufacturer guidelines?
How to Answer
- 1
Review the warranty documentation carefully to understand coverage and limitations
- 2
Follow manufacturer repair protocols step-by-step to ensure compliance
- 3
Document all repair processes and parts used for accountability
- 4
Communicate any issues or deviations from guidelines to management promptly
- 5
Stay updated on any changes to warranty policies from manufacturers
Example Answers
I begin by thoroughly reviewing the warranty documentation to know what's covered. Then, I follow the manufacturer's repair procedures closely to ensure compliance. I document everything meticulously to keep a record and discuss any issues with my supervisor.
Don't Just Read Tractor Mechanic Questions - Practice Answering Them!
Reading helps, but actual practice is what gets you hired. Our AI feedback system helps you improve your Tractor Mechanic interview answers in real-time.
Personalized feedback
Unlimited practice
Used by hundreds of successful candidates
What diagnostic tools do you use regularly, and how do they aid in the repair processes for tractors?
How to Answer
- 1
List specific diagnostic tools you use, such as multimeters or software.
- 2
Explain how each tool helps identify issues accurately.
- 3
Mention your experience with troubleshooting using these tools.
- 4
Share an example of a successful repair aided by a specific tool.
- 5
Emphasize the importance of staying updated with new diagnostic technologies.
Example Answers
I regularly use a multimeter for electrical diagnostics which helps identify issues like shorts or faulty connections quickly. Additionally, I utilize diagnostic software to read error codes directly from the tractor's computer system, allowing for precise troubleshooting.
Situational Interview Questions
If you were faced with a situation where multiple tractors needed repairs but limited resources were available, how would you prioritize which repairs to handle first?
How to Answer
- 1
Assess which tractors are most critical for immediate operations
- 2
Evaluate the severity of each problem affecting the tractors
- 3
Consider the potential impact of each repair on productivity
- 4
Communicate with team members to gather insights about usage needs
- 5
Take into account any deadlines or external factors affecting repairs
Example Answers
I would start by identifying which tractors are essential for daily tasks and prioritize those. Then, I would assess the severity of each issue, focusing first on problems that prevent operation altogether. Lastly, I'd consult with the team to ensure we're aligned on what machinery is most urgently needed.
Imagine a customer is unhappy with the speed of service for their tractor repairs. How would you address their concerns?
How to Answer
- 1
Listen actively to the customer's concerns without interrupting.
- 2
Acknowledge their frustration and empathize with their situation.
- 3
Provide clear information on the reasons for any delays in service.
- 4
Outline the steps you are taking to remedy the situation.
- 5
Follow up with the customer after resolving their issue to ensure satisfaction.
Example Answers
I would first listen to the customer and let them express their frustrations without interruptions. Then, I would acknowledge their feelings and explain the reasons for the delay. Finally, I'd outline how I will expedite their service and follow up in a few days to ensure they are satisfied.
Don't Just Read Tractor Mechanic Questions - Practice Answering Them!
Reading helps, but actual practice is what gets you hired. Our AI feedback system helps you improve your Tractor Mechanic interview answers in real-time.
Personalized feedback
Unlimited practice
Used by hundreds of successful candidates
How would you handle a situation where you have a looming deadline for repairs, but you discover a critical fault that requires more time than anticipated to fix?
How to Answer
- 1
Assess the critical fault and its impact on safety and functionality.
- 2
Communicate the issue promptly to your supervisor or team.
- 3
Prioritize tasks to manage the deadline while addressing the fault.
- 4
Consider temporary solutions or workarounds if applicable.
- 5
Document the issue and the steps taken for future reference.
Example Answers
If I find a critical fault, I first analyze its seriousness. I would inform my supervisor immediately and outline the implications. Then, I would prioritize fixing this fault, potentially leading to a discussion on deadlines or temporary fixes to ensure safety.
If you were tasked with repairing a tractor that has a unique or uncommon problem, how would you approach finding a solution?
How to Answer
- 1
Gather as much information as possible about the problem.
- 2
Review the tractor's service manual for troubleshooting tips.
- 3
Utilize diagnostic tools to identify specific issues.
- 4
Consult with colleagues or online forums for insights.
- 5
Test your solution on similar systems or components.
Example Answers
I would start by documenting the symptoms and gathering the tractor’s service manual to look for relevant troubleshooting steps.
Imagine you are assigned to a repair project with a team where members have different opinions on the method of repair. How would you facilitate a consensus?
How to Answer
- 1
Listen to each team member's point of view without interruption
- 2
Encourage open dialogue by asking clarifying questions
- 3
Identify common goals and priorities among team members
- 4
Propose a compromise that incorporates elements from different suggestions
- 5
Summarize the agreed-upon method to ensure mutual understanding
Example Answers
I would start by listening to each team member's perspective to understand their reasoning. Then I would encourage a discussion by asking questions. We could identify our common goals, like efficiency and safety, and propose a compromise solution that combines the best ideas.
Suppose you discover a more efficient method for conducting regular maintenance on tractors. How would you propose this change to your supervisor?
How to Answer
- 1
Identify key benefits of the new method, such as time savings and cost reduction.
- 2
Prepare a clear presentation or document outlining the current method and your proposed changes.
- 3
Anticipate potential questions or concerns your supervisor may have.
- 4
Suggest a pilot test of the new method to demonstrate its effectiveness.
- 5
Express openness to feedback and collaboration in refining the approach.
Example Answers
I would prepare a document that highlights how my new maintenance method reduces downtime and improves overall efficiency. I’d suggest we implement a pilot phase to test its effectiveness while remaining open to adjustments based on feedback.
If you encountered a parts shortage while performing a repair, what alternative solutions or workarounds might you consider?
How to Answer
- 1
Assess the specific part's function and necessity in the repair.
- 2
Consider using compatible parts from other equipment as temporary solutions.
- 3
Evaluate the possibility of repairing the existing part instead of replacing it.
- 4
Explore local suppliers or online resources for quick part acquisition.
- 5
Document the situation for future reference and ensure alignment with safety standards.
Example Answers
I would first assess if the part is critical for the operation. If it’s not essential, I’d look for compatible parts available from other machines on-site as a temporary fix.
How would you handle constructive feedback from a senior mechanic regarding your repair techniques?
How to Answer
- 1
Acknowledge the feedback respectfully and express gratitude for the input
- 2
Ask clarifying questions to fully understand the suggestions
- 3
Reflect on the feedback and identify areas for improvement
- 4
Implement the feedback in future repairs to show growth
- 5
Follow up later to discuss changes and seek additional advice
Example Answers
I would thank the senior mechanic for the feedback, ask any questions I have to better understand their perspective, and then take their advice to improve my techniques on my next repair.
Tractor Mechanic Position Details
Recommended Job Boards
ZipRecruiter
www.ziprecruiter.com/Jobs/Tractor-MechanicThese job boards are ranked by relevance for this position.
Related Positions
- Truck Mechanic
- Locomotive Mechanic
- Diesel Mechanic
- Maintenance Mechanic
- Transit Mechanic
- Fleet Mechanic
- Bus Mechanic
- Boat Mechanic
- Agriculture Mechanic
- Agricultural Mechanic
Similar positions you might be interested in.
Ace Your Next Interview!
Practice with AI feedback & get hired faster
Personalized feedback
Used by hundreds of successful candidates
Ace Your Next Interview!
Practice with AI feedback & get hired faster
Personalized feedback
Used by hundreds of successful candidates