Top 30 Typewriter Mechanic Interview Questions and Answers [Updated 2025]
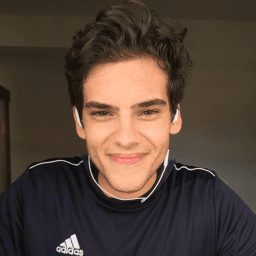
Andre Mendes
•
March 30, 2025
Are you aspiring to become a Typewriter Mechanic or looking to sharpen your interview skills? This blog post is your ultimate guide, featuring the most common interview questions for this unique role. Dive in to discover example answers and expert tips to help you respond effectively, ensuring you leave a lasting impression. Prepare yourself thoroughly and boost your confidence for the big day!
Download Typewriter Mechanic Interview Questions in PDF
To make your preparation even more convenient, we've compiled all these top Typewriter Mechanicinterview questions and answers into a handy PDF.
Click the button below to download the PDF and have easy access to these essential questions anytime, anywhere:
List of Typewriter Mechanic Interview Questions
Behavioral Interview Questions
Can you describe a time when you successfully diagnosed a complex issue with a typewriter?
How to Answer
- 1
Choose a specific incident where the issue was not obvious.
- 2
Explain the steps you took to diagnose the problem.
- 3
Focus on the tools and methods you used during diagnosis.
- 4
Highlight the outcome and any improvements made.
- 5
Mention any teamwork or collaboration if relevant.
Example Answers
I once had a client whose typewriter jammed frequently. I disassembled the machine and identified a misaligned carriage. I adjusted the alignment and tested it, which resolved the issue and improved performance.
Tell me about a situation where you had to explain a repair issue to a non-technical customer. How did you ensure they understood the problem?
How to Answer
- 1
Use simple language without technical jargon
- 2
Relate the issue to something the customer can understand
- 3
Check for understanding by asking if they have any questions
- 4
Use visual aids if possible, like diagrams or parts
- 5
Be patient and ready to explain things multiple times if needed
Example Answers
When a customer brought in their typewriter complaining it wouldn't type, I explained the issue by saying the ribbon was jammed. I compared it to a car's engine getting stuck. I then asked if they understood what I meant, and offered to show them how a new ribbon would work.
Don't Just Read Typewriter Mechanic Questions - Practice Answering Them!
Reading helps, but actual practice is what gets you hired. Our AI feedback system helps you improve your Typewriter Mechanic interview answers in real-time.
Personalized feedback
Unlimited practice
Used by hundreds of successful candidates
Describe a time when you worked in a team to repair a large batch of typewriters. What was your role, and how did you contribute to the team's success?
How to Answer
- 1
Identify a specific project where teamwork was crucial.
- 2
Explain your specific role and responsibilities in the project.
- 3
Highlight the skills you used that benefited the team.
- 4
Discuss a challenge the team faced and how you helped overcome it.
- 5
Conclude with the successful outcome and your contribution to it.
Example Answers
In my last job, I worked on a project to repair 100 vintage typewriters. I was responsible for disassembling and cleaning each unit. My attention to detail ensured that all components were functioning properly. When we encountered a shortage of parts, I suggested sourcing them locally, which helped us meet our deadline. The team completed the project ahead of schedule, and our clients were thrilled.
Tell me about a time when you had to learn a new repair technique quickly to fix a customer's typewriter. How did you manage the situation?
How to Answer
- 1
Identify the specific typewriter model and issue you faced.
- 2
Explain how you gathered information quickly, such as manuals or online resources.
- 3
Describe the steps you took to apply the new technique in practice.
- 4
Highlight the outcome and customer satisfaction after the repair.
- 5
Reflect on what you learned from the experience to improve future repairs.
Example Answers
I had a customer with a rare typewriter model that had a stuck carriage. I quickly researched the model online and found a video demonstrating the fix. I gathered tools and followed along with the video, successfully unjamming the carriage. The customer was thrilled to have their typewriter back in working condition.
Describe an instance where attention to detail prevented a significant error in your repair work.
How to Answer
- 1
Think of a specific repair incident where your focus made a difference.
- 2
Explain what details you noticed that others might have missed.
- 3
Describe the potential consequences if you had ignored those details.
- 4
Focus on your thought process during the repair.
- 5
Highlight the outcome thanks to your attention to detail.
Example Answers
During a typewriter repair, I noticed that one of the keys was slightly misaligned. I double-checked the alignment and found that a small spring was incorrectly placed. If I had ignored it, the key would have stuck, frustrating the user. By correcting it, the typewriter functioned flawlessly.
How do you stay up-to-date with new tools or techniques in typewriter repair?
How to Answer
- 1
Follow typewriter repair blogs or forums for the latest trends
- 2
Attend workshops or training sessions related to typewriter maintenance
- 3
Join online groups or communities focused on typewriter enthusiasts
- 4
Subscribe to newsletters from manufacturers of typewriter repair tools
- 5
Experiment with new techniques and share results with peers
Example Answers
I follow several typewriter repair blogs and participate in forums where experts discuss new tools and techniques. This helps me stay informed about the latest practices in the field.
Recall a time when you disagreed with a colleague about the best way to repair a typewriter. How did you resolve the conflict?
How to Answer
- 1
Describe the specific disagreement clearly and objectively.
- 2
Emphasize collaboration by seeking input from your colleague.
- 3
Highlight how you both considered each other's ideas.
- 4
Share the outcome, focusing on the resolution reached.
- 5
Reflect on any lessons learned from the experience.
Example Answers
During a repair on a vintage typewriter, my colleague wanted to replace the entire ribbon mechanism while I suggested a thorough cleaning. Instead of pushing my idea, I proposed we clean it first and see the results. We did so, and it worked perfectly, saving time and resources. We learned that trying simpler solutions first can often be effective.
Describe how you manage your time when juggling multiple repair jobs with varying levels of urgency.
How to Answer
- 1
Assess the urgency of each job and prioritize accordingly.
- 2
Create a schedule or to-do list for the day with time estimates.
- 3
Communicate with customers about expected timelines for each repair.
- 4
Use tools or techniques to minimize downtime between jobs.
- 5
Regularly review and adjust your plan based on changing priorities.
Example Answers
I start by assessing the urgency of each repair job, prioritizing those that are most critical. I then create a to-do list with estimated completion times, which helps me allocate the right amount of time for each job. I keep my customers informed about the timelines, which helps manage expectations.
Give an example of when you went beyond the standard repair to improve a typewriter's performance.
How to Answer
- 1
Think of a specific instance where you made an improvement.
- 2
Describe the problem you identified beyond normal repairs.
- 3
Explain the steps you took to enhance performance.
- 4
Share the outcome and how it benefited the user.
- 5
Keep your answer focused and concise.
Example Answers
In one case, a client had a typewriter that frequently jammed. I not only fixed the jams but also cleaned and lubricated the entire mechanism, ensuring smoother operation. This reduced jamming significantly and improved the typing experience for the client.
Don't Just Read Typewriter Mechanic Questions - Practice Answering Them!
Reading helps, but actual practice is what gets you hired. Our AI feedback system helps you improve your Typewriter Mechanic interview answers in real-time.
Personalized feedback
Unlimited practice
Used by hundreds of successful candidates
Describe a time when precision and careful handling of a typewriter were crucial in a repair job.
How to Answer
- 1
Think of a specific instance where you repaired a typewriter.
- 2
Focus on the delicate components you handled.
- 3
Explain the steps you took to ensure precision.
- 4
Mention any tools you used to assist in the repair.
- 5
Emphasize the positive result of your careful handling.
Example Answers
I once repaired a vintage typewriter where the carriage was misaligned. I carefully disassembled it using specialized screwdrivers to avoid stripping the screws. I measured the alignment with calipers to ensure precision before reassembling. As a result, the typewriter worked flawlessly and was preserved for future generations.
Technical Interview Questions
What are the main differences between servicing a mechanical typewriter and an electric typewriter?
How to Answer
- 1
Identify the key components that differ between mechanical and electric typewriters.
- 2
Discuss the basic maintenance tasks required for each type.
- 3
Mention the tools or techniques specific to servicing each type.
- 4
Highlight any common issues that occur uniquely in one type.
- 5
Emphasize your hands-on experience with both types if applicable.
Example Answers
Mechanical typewriters require manual adjustments and lubrication of moving parts, while electric typewriters may need electrical component checks and software recalibrations.
When faced with a typewriter that jams frequently, what are the steps you take to diagnose the problem?
How to Answer
- 1
Inspect the paper path for misalignment or obstructions
- 2
Check the ribbon for tension and proper installation
- 3
Examine the typebars for any physical blockages or damage
- 4
Clean the mechanisms to remove dirt or corrosion
- 5
Test the typewriter after each step to identify the specific issue
Example Answers
I start by inspecting the paper path for any obstructions or misalignment, as those often cause jams. Next, I check the ribbon to make sure it is properly tensioned and installed. I also look at the typebars to see if any are blocked or damaged. Finally, I'll clean the interior to remove dirt buildup and test the typewriter after each step.
Don't Just Read Typewriter Mechanic Questions - Practice Answering Them!
Reading helps, but actual practice is what gets you hired. Our AI feedback system helps you improve your Typewriter Mechanic interview answers in real-time.
Personalized feedback
Unlimited practice
Used by hundreds of successful candidates
Explain the process of replacing a typewriter's ribbon and ensuring it advances correctly.
How to Answer
- 1
Gather necessary tools including a new ribbon and scissors.
- 2
Carefully remove the old ribbon from the spools and typewriter carriage.
- 3
Install the new ribbon on the spools ensuring correct direction of travel.
- 4
Thread the ribbon through any guides or rollers according to the typewriter model.
- 5
Test the ribbon by typing a few characters to check for proper advancement.
Example Answers
To replace a typewriter's ribbon, I first gather a new ribbon and scissors. I remove the old ribbon, paying attention to the spool orientation. After installing the new ribbon, I ensure it follows the intended path through the guides and test it by typing a few letters.
What tools are essential for a typewriter mechanic, and how do you use them effectively?
How to Answer
- 1
Identify key tools such as screwdrivers, wrenches, and cleaning brushes.
- 2
Explain how each tool is specifically used in typewriter repair.
- 3
Mention the importance of having a good set of replacement parts.
- 4
Discuss maintenance tools like oil for lubrication and cleaning supplies.
- 5
Emphasize the necessity of precision tools for adjustments and repairs.
Example Answers
As a typewriter mechanic, I find that screwdrivers and wrenches are essential for disassembling and reassembling typewriters. I use a variety of sizes to fit different screws and bolts. Additionally, I use cleaning brushes to maintain the internal components, ensuring that they function smoothly. I've also found having a selection of replacement ribbons and rollers vital for repairs.
Can you explain the key mechanical components in a manual typewriter and their functions?
How to Answer
- 1
Identify the main components such as the keys, type bars, and ribbon.
- 2
Explain the function of each component clearly without jargon.
- 3
Provide a brief overview of how these components interact during typing.
- 4
Use examples from your experience with typewriters if applicable.
- 5
Keep your explanation structured to ensure clarity and flow.
Example Answers
The key components of a manual typewriter include the keys, type bars, and ribbon mechanism. When you press a key, it activates a type bar that strikes the ribbon, transferring ink onto the paper to print each character.
What is your approach to routine maintenance to ensure typewriters remain in optimal condition?
How to Answer
- 1
Perform regular cleaning of the typewriter to remove dust and debris.
- 2
Check and replace worn ribbons to maintain print quality.
- 3
Lubricate moving parts according to the manufacturer's recommendations.
- 4
Inspect and adjust the alignment of the typebar mechanics regularly.
- 5
Test the machine after maintenance to ensure everything operates smoothly.
Example Answers
I start by cleaning the typewriter to get rid of any dust, and I always check the ribbon to see if it needs replacing. I use a small amount of lubrication on moving parts and perform regular inspections to adjust the typebar alignment if necessary. Finally, I always test the typewriter after maintenance to confirm it works well.
How do you handle troubleshooting electronic components in electric typewriters?
How to Answer
- 1
Start by identifying the specific issue with the typewriter.
- 2
Use schematic diagrams to locate the electronic components.
- 3
Test components systematically with a multimeter to check for faults.
- 4
Replace any faulty components following proper safety protocols.
- 5
Document the troubleshooting process for future reference.
Example Answers
I first identify the specific issue, such as a key not typing. Then, I refer to the schematic diagrams to locate the relevant electronic components. I use a multimeter to test suspect components and replace any that are faulty, ensuring I follow safety protocols.
How do you approach repairing vintage typewriters with components that are no longer manufactured?
How to Answer
- 1
Evaluate the specific issue and identify the part needed for repair.
- 2
Research alternative parts that may be interchangeable or can be modified.
- 3
Utilize creative solutions such as 3D printing for non-manufactured components.
- 4
Network with other mechanics for advice or potential part sources.
- 5
Document repairs to build a reference for future repairs.
Example Answers
When repairing vintage typewriters, I first assess the problem to understand which part is needed. If the part is obsolete, I research online for alternative components that might work or can be modified.
Explain how you align and calibrate the type guide to ensure consistent typing quality.
How to Answer
- 1
Identify the specific type guide components that need alignment.
- 2
Use measuring tools like calipers or rulers for precision.
- 3
Adjust the type guide screws carefully to avoid over-tightening.
- 4
Test the alignment with a sample print to check consistency.
- 5
Make incremental adjustments and retest until optimal quality is achieved.
Example Answers
To align the type guide, I first check the positioning against the type face using calipers to ensure proper spacing. I then adjust the screws of the type guide gently, making sure not to over-tighten. After alignment, I run a sample print to test quality and make any necessary adjustments based on the printout.
What are the most common issues found with typewriter platens, and how do you address them?
How to Answer
- 1
Identify the common issues such as hardening, cracking, and wear.
- 2
Explain how to inspect the platen for these issues visually.
- 3
Describe specific methods for cleaning and conditioning the platen.
- 4
Mention the replacement options if the platen is beyond repair.
- 5
Discuss how to properly install a new platen if needed.
Example Answers
Common issues with typewriter platens include hardening due to age, cracks, and surface wear. I inspect the platen visually for signs of these problems. For hardening, I apply a suitable platen conditioner. If there are cracks, I recommend replacing the platen entirely. When installing a new platen, I ensure that it aligns correctly with the machine's mechanisms.
Don't Just Read Typewriter Mechanic Questions - Practice Answering Them!
Reading helps, but actual practice is what gets you hired. Our AI feedback system helps you improve your Typewriter Mechanic interview answers in real-time.
Personalized feedback
Unlimited practice
Used by hundreds of successful candidates
Situational Interview Questions
A customer claims their newly repaired typewriter is still malfunctioning. How would you address their concerns?
How to Answer
- 1
Listen carefully to the customer's complaints.
- 2
Ask specific questions about the malfunction they are experiencing.
- 3
Apologize for the inconvenience they are facing.
- 4
Explain the next steps you will take to resolve the issue.
- 5
Ensure the customer feels valued and reassured throughout the process.
Example Answers
I would first listen to the customer’s description of the problem to fully understand their concerns. Then, I would ask them specific questions to identify the exact malfunction. I would apologize for any inconvenience and reassure them that I will investigate the issue further to fix it promptly.
If you receive multiple service requests at once, how do you determine which typewriter to repair first?
How to Answer
- 1
Assess the urgency of each request based on customer need
- 2
Consider the severity of the typewriter's issues
- 3
Prioritize based on the order of requests received
- 4
Evaluate the typewriter model and familiarity
- 5
Communicate with customers to manage expectations
Example Answers
I would prioritize repairs based on urgency, addressing those that are critical for business needs first. If one typewriter is needed for a customer event that day, that would take precedence.
Don't Just Read Typewriter Mechanic Questions - Practice Answering Them!
Reading helps, but actual practice is what gets you hired. Our AI feedback system helps you improve your Typewriter Mechanic interview answers in real-time.
Personalized feedback
Unlimited practice
Used by hundreds of successful candidates
During a repair, you discover that a part you need is no longer available. What steps do you take to find a solution?
How to Answer
- 1
Check with the manufacturer for any available substitute parts.
- 2
Search online marketplaces and auction sites for used parts.
- 3
Consult with other mechanics or forums for advice on alternatives.
- 4
Consider modifying or fabricating a part in-house if feasible.
- 5
Document the issue and the steps taken for future reference.
Example Answers
First, I would contact the manufacturer to see if they offer any compatible substitute parts. If not, I would search reputable online marketplaces for used parts. Additionally, I would ask my fellow mechanics or check forums for advice on workable alternatives. If needed, I would also consider fabricating a part if I had the capability. Finally, I would document the whole process for record-keeping.
How would you handle a situation where a typewriter repair takes longer than expected, affecting your ability to meet deadlines?
How to Answer
- 1
Communicate proactively with customers about delays.
- 2
Assess the reason for the delay and prioritize tasks.
- 3
Explore options for temporary solutions if possible.
- 4
Maintain a positive attitude and focus on quality work.
- 5
Consider adjusting future estimates based on this experience.
Example Answers
I would immediately inform the customer about the delay and explain the reason. I would prioritize the tasks, focusing on what I can do quickly while still ensuring quality.
A customer requests a modification to their typewriter to suit a unique need. How would you approach this task?
How to Answer
- 1
Listen carefully to the customer's requirements to understand their specific needs
- 2
Assess the typewriter's current functionality and limitations
- 3
Use your technical knowledge to suggest feasible modifications
- 4
Explain the modification process clearly to the customer
- 5
Ensure to check if the modification will affect the warranty or function negatively
Example Answers
I would first hear the customer out to fully grasp what modifications they need, then evaluate if the typewriter can accommodate these changes. I would provide clear options and any potential issues they might face afterward.
If a customer is dissatisfied with your previous repairs, what steps would you take to rectify the situation and restore their trust?
How to Answer
- 1
Listen carefully to the customer's concerns without interruption.
- 2
Apologize sincerely and acknowledge their dissatisfaction.
- 3
Offer to inspect the typewriter again to identify the issue.
- 4
Provide a timeline for rectifying the repairs and keep them informed.
- 5
Follow up after the repair to ensure their satisfaction and trust.
Example Answers
I would first listen to the customer's concerns to understand their dissatisfaction. Then, I would apologize for any inconvenience and offer to take a look at their typewriter again. I would ensure I communicate clearly about the expected outcome and follow up after the repairs to check if they are satisfied.
You've repaired a typewriter, but during the final test, a new problem occurs. How do you handle this situation?
How to Answer
- 1
Stay calm and assess the new problem carefully.
- 2
Recheck your previous repairs to ensure they are intact.
- 3
Document the new issue as it may provide insight into the root cause.
- 4
Use a systematic approach to troubleshoot the new problem.
- 5
Communicate with the client about the situation and next steps.
Example Answers
First, I would stay calm and carefully observe the new issue to understand what is happening. I would then recheck my previous repairs to ensure everything is still functioning as intended.
How do you ensure the quality of your repair work before returning a typewriter to a customer?
How to Answer
- 1
Perform a thorough test of all mechanical functions after repairs.
- 2
Check alignment of the typebars and ribbon to ensure proper printing.
- 3
Ensure all screws and components are securely fastened.
- 4
Clean the typewriter to remove dust and debris before returning it.
- 5
Provide a detailed summary of the repairs and any maintenance done.
Example Answers
I test all mechanical functions extensively, including typing speed and alignment, after completing the repairs to ensure everything operates smoothly.
What would you do if a customer's typewriter requires a part not widely available?
How to Answer
- 1
Assess the specific part needed and its impact on functionality
- 2
Explore alternative sources for the part, such as online marketplaces or specialty suppliers
- 3
Consider fabricating the part if possible or finding a workaround
- 4
Inform the customer about the situation and discuss their options
- 5
Ensure follow-up communication to keep the customer updated on progress
Example Answers
First, I would identify the exact part that is missing and determine how essential it is for the typewriter's operation. Then, I'd look online or contact specialty suppliers to see if the part is available anywhere. If it's impossible to find, I would discuss other viable options with the customer.
Typewriter Mechanic Position Details
Related Positions
- Machine Repairman
- Printer Technician
- Mechanic
- Computer Mechanic
- Copier Technician
- Electronics Mechanic
- Computer Technician
- Computer Repairer
- Repair Technician
- Linotypist
Similar positions you might be interested in.
Ace Your Next Interview!
Practice with AI feedback & get hired faster
Personalized feedback
Used by hundreds of successful candidates
Ace Your Next Interview!
Practice with AI feedback & get hired faster
Personalized feedback
Used by hundreds of successful candidates